- お役立ち記事
- An integrated strategy for procurement processes and quality control that purchasing departments should pay attention to
月間76,176名の
製造業ご担当者様が閲覧しています*
*2025年3月31日現在のGoogle Analyticsのデータより
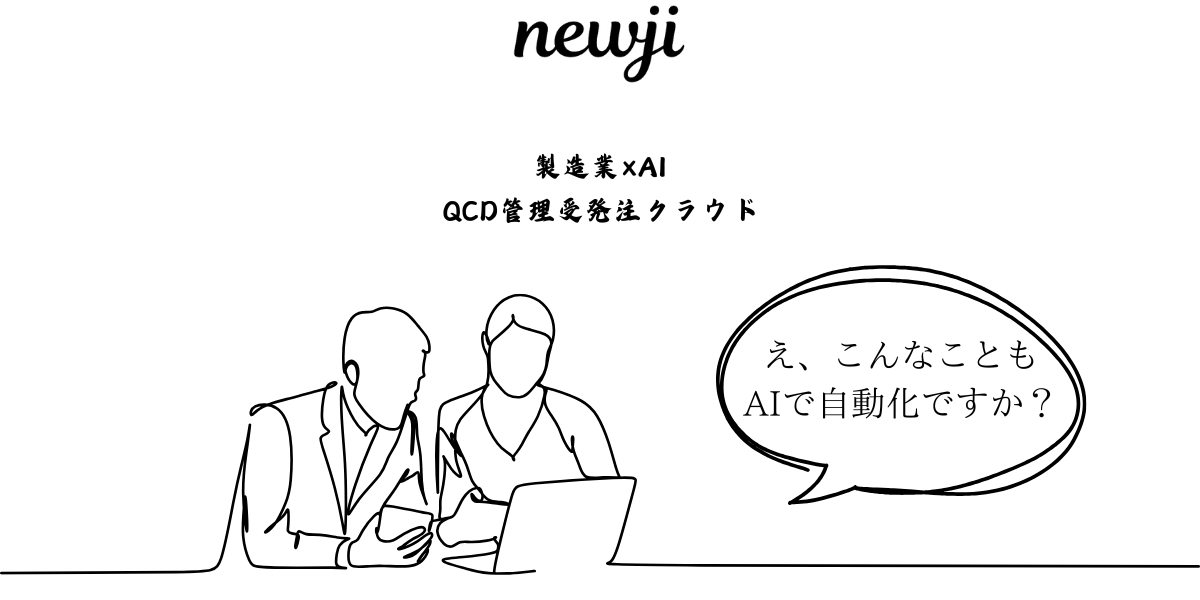
An integrated strategy for procurement processes and quality control that purchasing departments should pay attention to
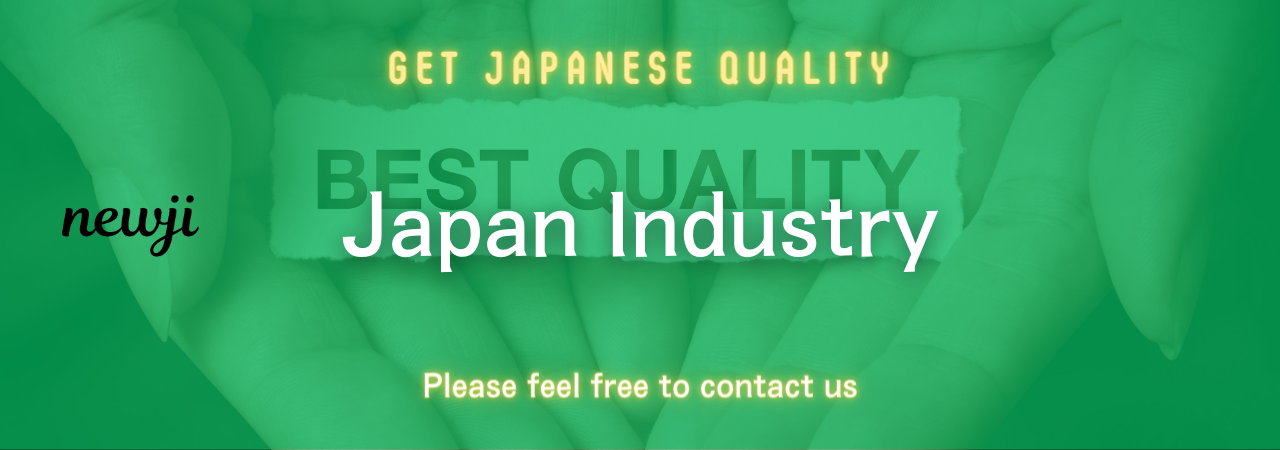
目次
Introduction to Procurement Processes and Quality Control
Procurement processes and quality control are crucial parts of any organization’s operational structure.
Purchasing departments need to focus on these areas to ensure that they not only acquire the best products or services but also maintain high quality standards.
An integrated strategy that combines procurement processes with quality control can lead to significant improvements in efficiency and effectiveness.
Understanding Procurement Processes
The procurement process is the series of steps an organization takes to purchase goods or services.
It involves identifying needs, selecting suppliers, negotiating terms, and ultimately making the purchase.
The first step in an effective procurement process is recognizing what products or services are needed by the organization to function efficiently.
After identifying needs, the purchasing department evaluates potential suppliers.
Supplier evaluation is crucial because it determines the quality of goods or services the company will receive.
Factors considered during this evaluation include the supplier’s reputation, financial stability, and ability to meet delivery timelines.
Negotiating Terms and Prices
Once suitable suppliers are shortlisted, negotiations begin.
The purchasing department must negotiate favorable terms that align with the organization’s budget and quality requirements.
This may involve discussing prices, payment terms, delivery schedules, and warranty conditions.
A successful negotiation results in a contract that guarantees product or service performance and price stability over the term of the agreement.
Purchase Order and Contract Management
With terms agreed upon, the purchasing department issues a purchase order to the supplier.
This document outlines the agreed terms and ensures both parties understand their responsibilities.
Effective contract management during this phase ensures that suppliers adhere to contractual obligations regarding quality and delivery.
The Role of Quality Control in Procurement
Quality control is an integral part of procurement processes.
It ensures that the products or services acquired meet the organization’s standards and are fit for purpose.
Incorporating quality control measures helps prevent substandard goods and reduces the risk of customer dissatisfaction.
Setting Quality Standards
Before beginning the procurement process, organizations must establish clear quality standards.
These standards act as benchmarks against which supplier performance can be measured.
They should be communicated to suppliers to ensure they understand the expectations and can deliver accordingly.
Inspection and Testing
Upon receiving goods or services, inspection, and testing are crucial quality control steps.
This process involves checking products to confirm they meet the predetermined standards.
Materials that do not pass inspection may be rejected or returned to the supplier for replacement or repair.
In some cases, organizations may employ third-party inspectors for added assurance.
This additional verification step can help uncover issues that internal inspections might miss, ensuring only high-quality products make it to the end-user.
Benefits of an Integrated Strategy
Integrating procurement processes with quality control offers several advantages.
It ensures seamless operations, meeting organizational goals effectively.
Enhanced Supplier Relationships
When procurement and quality control work together, it fosters better relationships with suppliers.
Clear communication of expectations and consistent quality assessments help build trust.
This can lead to long-term partnerships with suppliers, resulting in better pricing and exclusive access to high-quality products.
Cost Efficiency
An integrated strategy promotes cost efficiency by reducing waste and preventing rework.
Quality issues discovered early in the procurement process save time and resources.
Additionally, negotiating with preferred suppliers can lead to discounts and other financial incentives.
Improved Risk Management
Combining procurement and quality control helps manage risks effectively.
By anticipating potential quality issues and addressing them promptly, organizations minimize operational disruptions.
This proactive approach protects the business from potential liabilities associated with substandard products.
Boosted Competitive Advantage
Organizations that consistently deliver high-quality products gain a competitive edge.
An integrated strategy allows companies to enhance their brand reputation and increase customer loyalty.
Satisfied customers are more likely to return and recommend the organization to others.
Implementing an Integrated Strategy
To successfully integrate procurement and quality control, organizations need to establish a flexible framework.
This involves defining processes, utilizing technology, and providing training for staff.
Process Definition and Documentation
Clearly defining and documenting processes ensures everyone involved understands their roles and responsibilities.
This reduces errors and inefficiencies, allowing smooth operation between departments handling procurement and quality control.
Leveraging Technology
Technology plays a significant role in the integration of procurement and quality control.
Software solutions can automate processes, track supplier performance, and analyze quality data.
Utilizing such tools provides real-time insights, facilitating better decision-making.
Training and Development
Continuous training for procurement and quality control teams is essential.
Training programs should focus on the latest industry practices and technologies.
Well-informed staff contributes to the success of an integrated strategy through improved efficiency and effectiveness.
Conclusion
In conclusion, an integrated strategy for procurement processes and quality control is vital for any organization aiming to enhance its operations.
By paying attention to both areas, purchasing departments can ensure they acquire high-quality products and services while managing costs effectively.
With an established framework, clear communication, and technology integration, organizations can achieve their goals and gain a competitive advantage in the marketplace.
資料ダウンロード
QCD管理受発注クラウド「newji」は、受発注部門で必要なQCD管理全てを備えた、現場特化型兼クラウド型の今世紀最高の受発注管理システムとなります。
ユーザー登録
受発注業務の効率化だけでなく、システムを導入することで、コスト削減や製品・資材のステータス可視化のほか、属人化していた受発注情報の共有化による内部不正防止や統制にも役立ちます。
NEWJI DX
製造業に特化したデジタルトランスフォーメーション(DX)の実現を目指す請負開発型のコンサルティングサービスです。AI、iPaaS、および先端の技術を駆使して、製造プロセスの効率化、業務効率化、チームワーク強化、コスト削減、品質向上を実現します。このサービスは、製造業の課題を深く理解し、それに対する最適なデジタルソリューションを提供することで、企業が持続的な成長とイノベーションを達成できるようサポートします。
製造業ニュース解説
製造業、主に購買・調達部門にお勤めの方々に向けた情報を配信しております。
新任の方やベテランの方、管理職を対象とした幅広いコンテンツをご用意しております。
お問い合わせ
コストダウンが利益に直結する術だと理解していても、なかなか前に進めることができない状況。そんな時は、newjiのコストダウン自動化機能で大きく利益貢献しよう!
(β版非公開)