- お役立ち記事
- Analysis of fracture surfaces of plastic products, identification of fracture modes, prediction of deterioration lifespan, and countermeasures against defects
月間76,176名の
製造業ご担当者様が閲覧しています*
*2025年3月31日現在のGoogle Analyticsのデータより
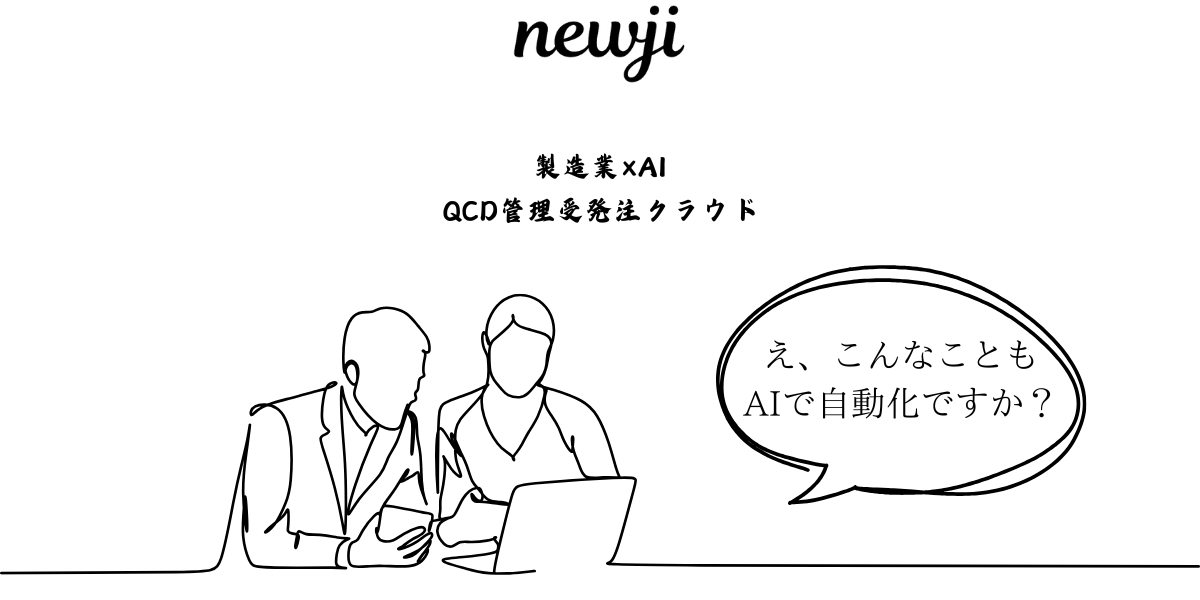
Analysis of fracture surfaces of plastic products, identification of fracture modes, prediction of deterioration lifespan, and countermeasures against defects
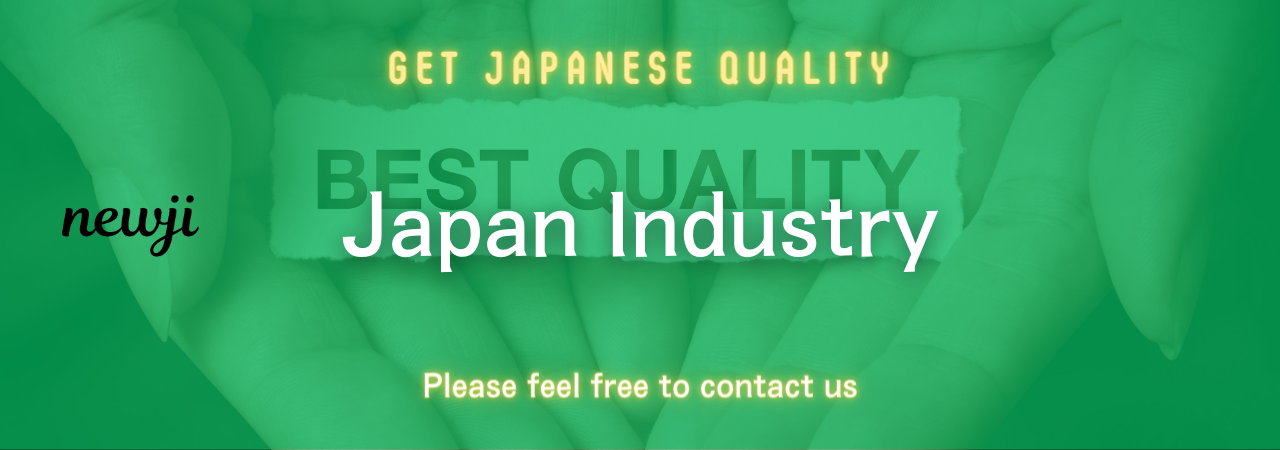
目次
Understanding Fracture Surfaces of Plastic Products
When it comes to analyzing the durability and lifespan of plastic products, studying the fracture surfaces plays a crucial role.
Fracture surfaces offer critical insights into the failure mechanisms that affect plastic materials.
By examining these surfaces, experts can identify the fracture modes that occur, predict potential deterioration over time, and develop strategies to prevent defects.
This exploration is crucial for industries that rely heavily on plastic components, ensuring products meet safety and quality standards.
Identifying Fracture Modes in Plastic Materials
Fracture modes refer to the different ways in which a material can fail under stress.
In the context of plastic products, several fracture modes can be identified, each with its unique characteristics and contributing factors.
One common fracture mode is brittle fracture, where the material breaks with little to no plastic deformation.
This type of failure often occurs in high-stress areas and is characterized by a smooth, shiny fracture surface.
Brittle fractures can be sudden and catastrophic, necessitating a thorough understanding for prevention.
Another fracture mode is ductile fracture, which involves significant plastic deformation before failure.
The surface of a ductile fracture typically appears rough and fibrous, differentiating it from brittle fractures.
Understanding the transition from ductile to brittle behavior in plastics is vital for predicting product performance under various conditions.
Fatigue fracture is another critical mode, occurring due to repeated cyclic stresses over time.
This type of fracture is identified by the presence of beach marks or striations on the fracture surface, which indicate the progressive nature of the failure.
Recognizing fatigue fractures allows manufacturers to enhance product endurance through design modifications or material improvements.
Predicting Deterioration Lifespan of Plastics
Predicting the lifespan of plastic products involves understanding how they deteriorate under different environmental and operational conditions.
Several factors contribute to the deterioration process, including UV radiation, temperature fluctuations, chemical exposure, and mechanical stress.
Polymer degradation is a significant concern, as it can lead to reduced material properties and ultimately, failure.
By studying fracture surfaces and the modes of failure, experts can make informed predictions about the product’s lifespan.
For instance, exposure to UV radiation can cause photo-oxidation, leading to the material’s embrittlement and fracture.
Fracture surfaces in such cases might display discoloration and surface cracking, indicating UV-induced degradation.
Predicting this deterioration allows for the inclusion of UV stabilizers in the material formulation to extend the product’s longevity.
Temperature variations also play a crucial role in the lifespan of plastic products.
Repeated exposure to high and low temperatures can result in thermal fatigue, weakening the material over time.
Analyzing fracture surfaces can reveal signs of thermal stress, like crazing or micro-cracking, enabling preventive strategies.
Chemically aggressive environments can lead to stress-corrosion cracking in plastics, where fractures initiate at points of chemical attack.
Experts can predict the product’s lifespan by identifying corrosion signs on fracture surfaces, suggesting material changes or protective coatings to counteract such effects.
Countermeasures Against Defects in Plastic Products
Preventing defects in plastic products is as essential as understanding their failure mechanisms.
With insights gained from analyzing fracture surfaces and identifying deterioration causes, manufacturers can implement effective countermeasures to enhance product quality.
One approach is material selection and design optimization.
Choosing plastics with higher toughness or fatigue resistance can reduce the risk of brittle and fatigue fractures.
Designing products with stress-relief features or thicker sections in high-stress areas also prevents premature failure.
Manufacturing processes greatly influence the defect levels in plastic components.
Ensuring proper mold design, controlling the processing temperatures, and maintaining uniform cooling rates can significantly impact the occurrence of defects.
Incorporating these procedures reduces residual stresses and potential weak points, enhancing product reliability.
Introducing additives to the plastic formulation is another countermeasure.
Antioxidants, UV stabilizers, and impact modifiers help improve the material’s resistance to environmental degradation and mechanical stresses.
These additives are tailored to address specific failure modes, prolonging the product’s effective life.
Lastly, regular quality control and testing are pivotal for defect prevention.
Implementing rigorous testing methods, such as tensile testing, impact testing, and fatigue testing, helps identify potential weaknesses before products reach the market.
Analyzing test data provides valuable feedback for adjusting design and manufacturing processes, ensuring consistent quality standards.
Conclusion
Understanding the intricacies of fracture surfaces in plastic products is a fundamental aspect of product reliability and quality assurance.
By identifying fracture modes, predicting deterioration lifespans, and implementing countermeasures, manufacturers can develop robust plastic components that withstand various operational and environmental challenges.
This proactive approach not only extends the lifespan of plastic products but also enhances consumer trust and industry reputation.
Through meticulous analysis and strategic interventions, the potential for defects is minimized, driving innovation and sustainability in the realm of plastic manufacturing.
資料ダウンロード
QCD管理受発注クラウド「newji」は、受発注部門で必要なQCD管理全てを備えた、現場特化型兼クラウド型の今世紀最高の受発注管理システムとなります。
ユーザー登録
受発注業務の効率化だけでなく、システムを導入することで、コスト削減や製品・資材のステータス可視化のほか、属人化していた受発注情報の共有化による内部不正防止や統制にも役立ちます。
NEWJI DX
製造業に特化したデジタルトランスフォーメーション(DX)の実現を目指す請負開発型のコンサルティングサービスです。AI、iPaaS、および先端の技術を駆使して、製造プロセスの効率化、業務効率化、チームワーク強化、コスト削減、品質向上を実現します。このサービスは、製造業の課題を深く理解し、それに対する最適なデジタルソリューションを提供することで、企業が持続的な成長とイノベーションを達成できるようサポートします。
製造業ニュース解説
製造業、主に購買・調達部門にお勤めの方々に向けた情報を配信しております。
新任の方やベテランの方、管理職を対象とした幅広いコンテンツをご用意しております。
お問い合わせ
コストダウンが利益に直結する術だと理解していても、なかなか前に進めることができない状況。そんな時は、newjiのコストダウン自動化機能で大きく利益貢献しよう!
(β版非公開)