- お役立ち記事
- Analysis simulation technology and application examples in powder processes
月間76,176名の
製造業ご担当者様が閲覧しています*
*2025年3月31日現在のGoogle Analyticsのデータより
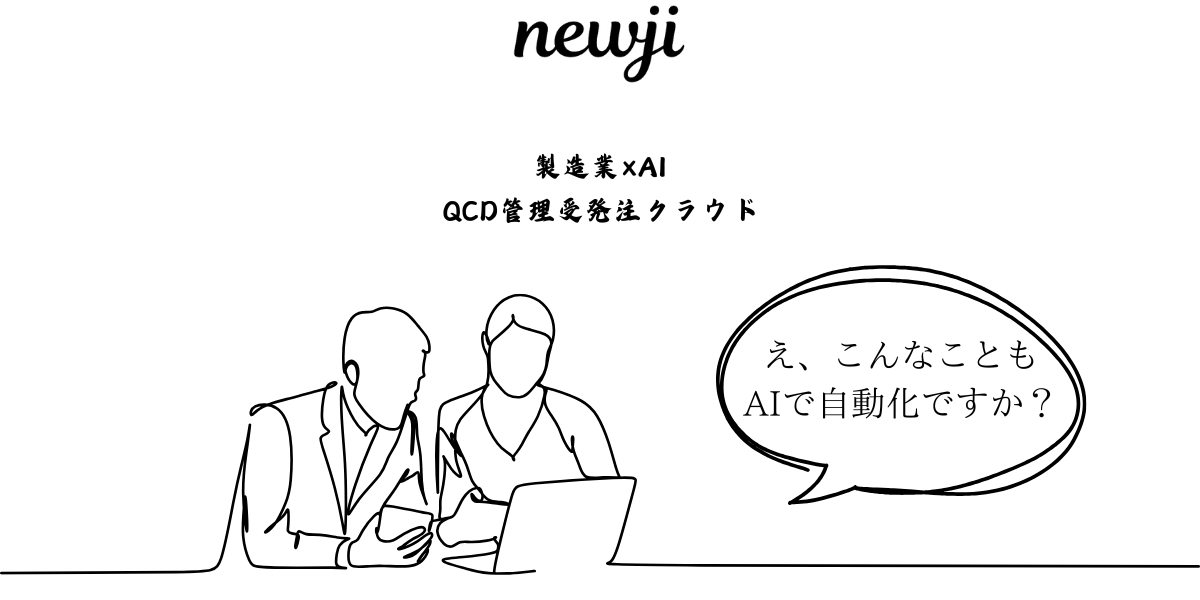
Analysis simulation technology and application examples in powder processes
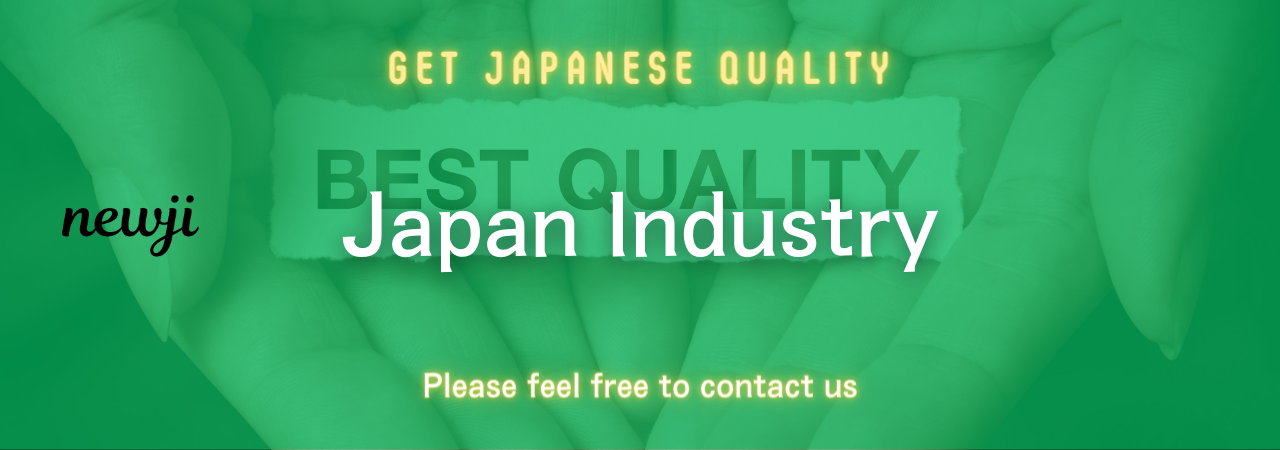
目次
Introduction to Analysis Simulation Technology
In recent years, analysis simulation technology has revolutionized various industrial sectors, including the powder processing industry.
This innovative technology allows scientists and engineers to model and simulate complex processes, enabling them to predict outcomes more accurately and efficiently.
By utilizing computer-based tools, manufacturers can optimize processes, enhance product quality, and minimize waste, thereby increasing profitability and sustainability.
Understanding Powder Processes
Powder processing involves various activities, from grinding and mixing to compaction and sintering.
These processes are crucial in industries such as pharmaceuticals, food, metallurgy, and ceramics.
The goal is to convert raw powdered materials into finished products with desired properties.
Each step of the powder process requires precise control to ensure that the end product meets specific quality standards.
The Role of Simulation in Powder Processes
Simulation technology plays a pivotal role in powder processes by enabling engineers to model the behavior of particles under different conditions.
Using computational models, simulations can predict how powders will flow, mix, or densify, facilitating more effective process design.
By simulating various scenarios, engineers can anticipate challenges and develop strategies to overcome them without wasting resources on trial-and-error approaches.
Types of Simulation Tools in Powder Processes
There are several key simulation tools used in powder processes, each serving specific purposes:
Discrete Element Method (DEM)
DEM is one of the most popular simulation techniques in powder processes.
It models the behavior of individual particles, accounting for interactions such as collisions and friction.
By analyzing these interactions, DEM provides valuable insights into powder flow, segregation, and mixing.
Computational Fluid Dynamics (CFD)
CFD is used to simulate fluid flows, which is especially important in processes involving powders suspended in liquids or gases.
By understanding fluid-particle interactions, CFD helps optimize processes like spray drying, fluidized bed drying, and pneumatic conveying.
Finite Element Analysis (FEA)
FEA is applied to study the mechanical properties of bulk powder materials under stress.
It helps in designing equipment and structures that are subject to the forces generated during powder compaction and handling.
Applications of Simulation in Powder Processes
Simulation technology has a wide range of applications in powder processes, each contributing to enhanced efficiency and product quality.
Optimizing Mixing Processes
In industries like pharmaceuticals, achieving a uniform mix of active ingredients is crucial.
Simulation tools can optimize mixing times, speeds, and equipment settings to ensure homogeneity, reducing the risk of ineffective or inconsistent products.
Improving Powder Flow
Poor powder flow can lead to blockages, uneven filling, and other production issues.
By simulating powder flow dynamics, engineers can design equipment and processes that minimize these problems, ensuring smooth and consistent operations.
Enhancing Compaction Techniques
During compaction, powders are pressed into solid forms, such as tablets or pellets.
Simulation helps predict how powders will behave under different pressures and die configurations, aiding in the development of compaction techniques that produce stronger and more uniform products.
Optimizing Drying Processes
Drying processes are critical in the food and chemical industries.
Simulations can model how moisture evaporates from powders, identifying optimal temperature and airflow conditions that enhance drying efficiency and product quality.
Minimizing Segregation
Segregation occurs when particles separate based on size or density, leading to inconsistent product quality.
Through simulation, processes can be designed to minimize segregation, ensuring that the final product has the intended composition.
Benefits of Using Simulation Technology
There are numerous benefits to integrating simulation technology into powder processes:
Cost Reduction
By predicting and preventing issues before they occur, simulation helps reduce material waste, energy consumption, and equipment wear, resulting in significant cost savings.
Enhanced Product Quality
Simulations provide insights that lead to more precise process control, ensuring products meet stringent quality standards and regulatory requirements.
Faster Development Times
With simulation tools, new processes and products can be developed and tested virtually, reducing the time and resources required for physical experimentation and shortening the time to market.
Flexibility and Innovation
Simulation allows for the exploration of innovative process designs and conditions, fostering creativity and the development of new techniques that can be tailored to specific industrial needs.
Challenges in Implementing Simulation Technology
Despite its benefits, implementing simulation technology in powder processes does come with challenges:
Complexity of Models
Accurate simulations require detailed models that account for various factors, which can be complex and time-consuming to develop.
Data Requirements
Reliable simulations depend on high-quality data, which may not always be available or easy to obtain.
Integration with Existing Systems
Successfully integrating simulation tools with existing equipment and processes can be technically challenging and may necessitate additional training and resources.
Conclusion
Analysis simulation technology is transforming the powder processing industry by providing accurate and efficient ways to optimize processes and improve product quality.
As technology evolves, its applications in powder processes are expected to expand, leading to more innovative solutions and greater industrial advancements.
By overcoming current challenges and continuing to develop comprehensive models, the potential for simulation technology to enhance powder processes is immense.
資料ダウンロード
QCD管理受発注クラウド「newji」は、受発注部門で必要なQCD管理全てを備えた、現場特化型兼クラウド型の今世紀最高の受発注管理システムとなります。
ユーザー登録
受発注業務の効率化だけでなく、システムを導入することで、コスト削減や製品・資材のステータス可視化のほか、属人化していた受発注情報の共有化による内部不正防止や統制にも役立ちます。
NEWJI DX
製造業に特化したデジタルトランスフォーメーション(DX)の実現を目指す請負開発型のコンサルティングサービスです。AI、iPaaS、および先端の技術を駆使して、製造プロセスの効率化、業務効率化、チームワーク強化、コスト削減、品質向上を実現します。このサービスは、製造業の課題を深く理解し、それに対する最適なデジタルソリューションを提供することで、企業が持続的な成長とイノベーションを達成できるようサポートします。
製造業ニュース解説
製造業、主に購買・調達部門にお勤めの方々に向けた情報を配信しております。
新任の方やベテランの方、管理職を対象とした幅広いコンテンツをご用意しております。
お問い合わせ
コストダウンが利益に直結する術だと理解していても、なかなか前に進めることができない状況。そんな時は、newjiのコストダウン自動化機能で大きく利益貢献しよう!
(β版非公開)