- お役立ち記事
- Anti-Rebound and Quality Improvement in Manufacturing
Anti-Rebound and Quality Improvement in Manufacturing
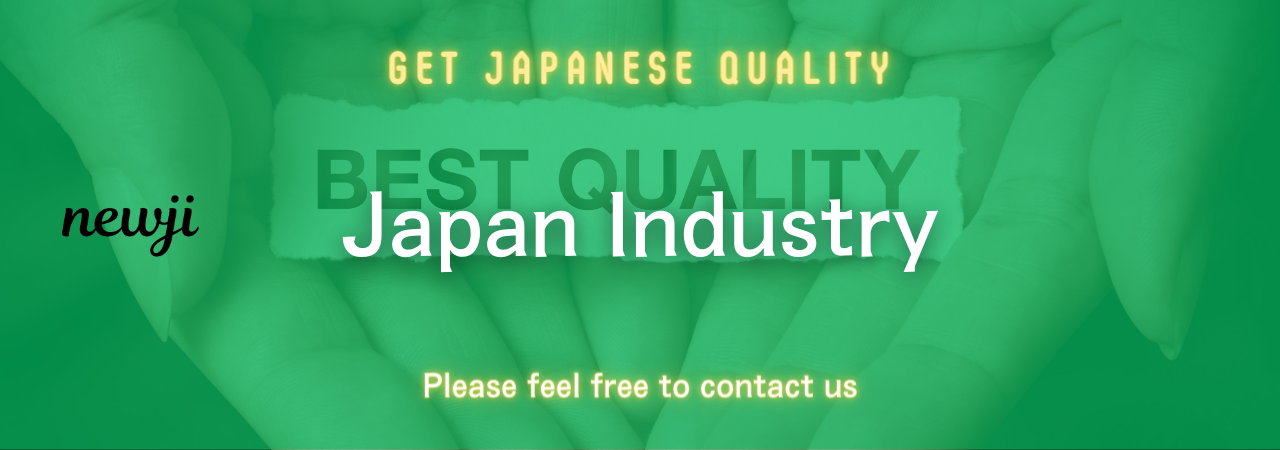
In the world of manufacturing, achieving high quality while minimizing waste is vital for success.
One of the key issues that industries face is the problem of rebounding, which can lead to defects and inefficiencies.
Understanding how to control this rebound effect and implementing strategies to continuously improve quality are essential for any successful manufacturing operation.
目次
What is Rebounding in Manufacturing?
Rebounding refers to the tendency of materials or products to return to their original shape or state after being worked on or processed.
This can happen during various stages of manufacturing, such as molding, welding, or pressing.
For instance, a metal part that has been bent might try to return to its original shape, leading to inaccuracies and defects.
Rebounding can compromise the integrity and functionality of the product, prompting costly rework and reducing overall efficiency.
Causes of Rebound in Manufacturing
Several factors contribute to the rebound effect in manufacturing processes.
These include the type of material being used, the method of processing, and the amount of force applied.
Materials like metals and plastics have inherent properties that make them prone to rebounding when subjected to stress.
Additionally, improper handling or incorrect processing parameters can exacerbate the issue.
Understanding these causes is the first step towards addressing the problem effectively.
Strategies to Minimize Rebounding Effects
Manufacturers can adopt various strategies to control and minimize the rebound effect.
Here are some effective approaches:
1. Selecting the Right Material
Choosing appropriate materials that exhibit minimal rebound tendencies is crucial.
Advanced composite materials or specially treated metals can offer better stability and less susceptibility to rebounding.
Collaborating with material scientists to understand the properties of potential materials can significantly benefit the manufacturing process.
2. Precise Processing Techniques
Adopting accurate and consistent processing techniques is essential.
For instance, companies can use advanced computer numerical control (CNC) machines that precisely control force and heat application.
Such precision helps in maintaining the desired shape and reduces the likelihood of rebound.
3. Proper Tooling and Equipment
Using the right tools and equipment specifically designed for the material and process can make a significant difference.
Tools that distribute force evenly and minimize stress concentration can help in reducing rebound.
Regular maintenance and calibration of machinery also ensure optimal performance and minimize defects.
Continuous Quality Improvement in Manufacturing
Quality improvement is a continuous journey, not a one-time achievement.
It involves regularly assessing and refining processes to enhance product quality and operational efficiency.
Here are some key practices for continuous quality improvement in manufacturing:
1. Implementing Total Quality Management (TQM)
Total Quality Management (TQM) is a holistic approach that emphasizes customer satisfaction, employee involvement, and continuous improvement.
By fostering a culture of quality at all levels, manufacturers can consistently meet or exceed customer expectations.
TQM involves regular training, process audits, and employee feedback mechanisms to identify and rectify issues promptly.
2. Using Six Sigma Methodology
Six Sigma is a data-driven approach that focuses on reducing defects and variability in processes.
It utilizes statistical tools and techniques to identify causes of defects and implement corrective actions.
Adopting Six Sigma principles helps in achieving higher precision and quality, leading to customer satisfaction and cost reduction.
3. Lean Manufacturing Principles
Lean manufacturing aims to minimize waste and maximize value by streamlining processes.
Identifying and eliminating non-value-added activities help in improving efficiency and product quality.
Techniques like just-in-time (JIT) production, 5S workplace organization, and kaizen (continuous improvement) are integral parts of lean manufacturing.
4. Investing in Advanced Technologies
Leveraging advanced technologies such as automation, artificial intelligence (AI), and the Internet of Things (IoT) can significantly enhance quality control.
Automated systems can perform repetitive tasks with high precision and consistency, reducing the margin for errors.
AI and IoT enable real-time monitoring and predictive maintenance, ensuring optimal performance and minimal downtime.
The Role of Employee Training and Involvement
Employees play a critical role in achieving and maintaining high quality in manufacturing.
Providing regular training and encouraging active involvement are essential components of a quality-driven culture.
1. Regular Training Programs
Conducting training sessions to update employees on the latest techniques, tools, and quality standards ensures that everyone is on the same page.
Training programs should be tailored to different roles, enhancing specific skills and knowledge required for each position.
2. Encouraging Employee Feedback
Creating an environment where employees feel comfortable sharing their insights and suggestions can lead to valuable improvements.
Regular feedback mechanisms, like suggestion boxes or team meetings, allow employees to voice their concerns and propose solutions.
3. Recognizing and Rewarding Excellence
Acknowledging and rewarding employees for their contributions to quality improvement fosters a sense of ownership and motivation.
Recognition programs can include awards, bonuses, or other incentives that highlight the importance of quality in the workplace.
Conclusion
Reducing rebound effects and improving quality in manufacturing are intertwined goals that require a strategic and comprehensive approach.
By understanding the causes of rebound, adopting precise processing techniques, and continuously refining processes, manufacturers can achieve higher quality and efficiency.
Moreover, fostering a culture of quality through employee involvement and the adoption of advanced technologies plays a crucial role in sustaining improvements over time.
Through these combined efforts, manufacturing operations can not only meet but exceed industry standards, leading to greater customer satisfaction and business success.
資料ダウンロード
QCD調達購買管理クラウド「newji」は、調達購買部門で必要なQCD管理全てを備えた、現場特化型兼クラウド型の今世紀最高の購買管理システムとなります。
ユーザー登録
調達購買業務の効率化だけでなく、システムを導入することで、コスト削減や製品・資材のステータス可視化のほか、属人化していた購買情報の共有化による内部不正防止や統制にも役立ちます。
NEWJI DX
製造業に特化したデジタルトランスフォーメーション(DX)の実現を目指す請負開発型のコンサルティングサービスです。AI、iPaaS、および先端の技術を駆使して、製造プロセスの効率化、業務効率化、チームワーク強化、コスト削減、品質向上を実現します。このサービスは、製造業の課題を深く理解し、それに対する最適なデジタルソリューションを提供することで、企業が持続的な成長とイノベーションを達成できるようサポートします。
オンライン講座
製造業、主に購買・調達部門にお勤めの方々に向けた情報を配信しております。
新任の方やベテランの方、管理職を対象とした幅広いコンテンツをご用意しております。
お問い合わせ
コストダウンが利益に直結する術だと理解していても、なかなか前に進めることができない状況。そんな時は、newjiのコストダウン自動化機能で大きく利益貢献しよう!
(Β版非公開)