- お役立ち記事
- Application and Effectiveness of Quality Function Deployment (QFD) in Manufacturing Quality Management
Application and Effectiveness of Quality Function Deployment (QFD) in Manufacturing Quality Management
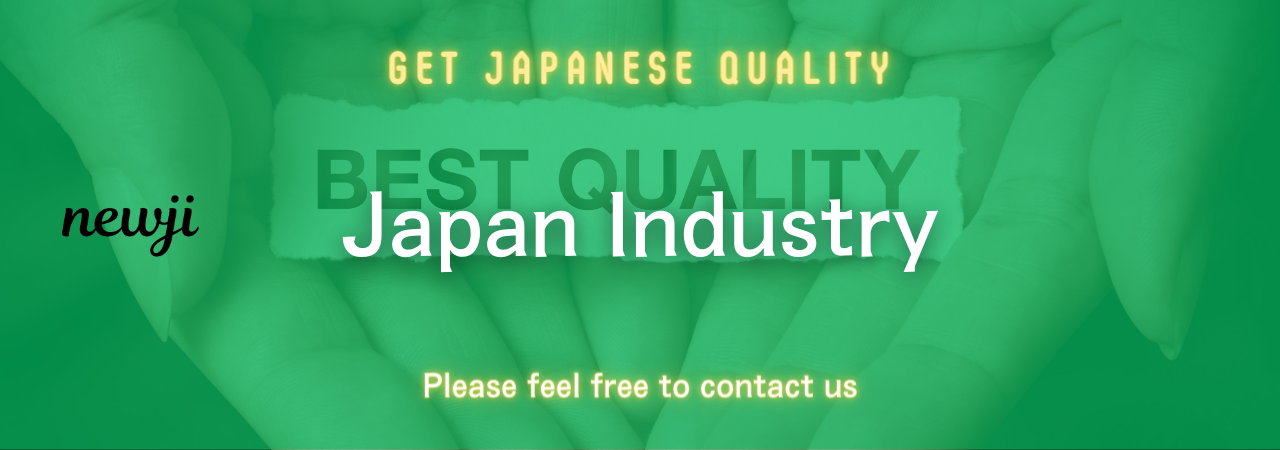
Quality Function Deployment (QFD) is an essential tool in the realm of manufacturing quality management.
It supports companies in understanding their customers’ needs and translating them into specific plans to produce high-quality products.
By prioritizing customer requirements and systematically addressing them throughout the production cycle, QFD helps in enhancing overall product performance and customer satisfaction.
目次
What is Quality Function Deployment (QFD)?
QFD is a structured process that helps organizations translate customer requirements into technical specifications.
Developed in Japan in the late 1960s, it has since become a widely adopted methodology in quality management.
QFD involves a series of matrices that identify and prioritize customer needs and link them to the production process.
The House of Quality
Central to QFD is the “House of Quality,” a metaphor that represents customer requirements visually.
The House of Quality is a matrix that relates customer desires (“Whats”) to how the company plans to meet these desires (“Hows”).
This matrix serves as a first step in the QFD process and lays the foundation for subsequent actions.
How QFD Enhances Manufacturing Quality
Implementing QFD in manufacturing quality management brings numerous benefits.
These include better alignment with customer expectations, reduced time to market, and improved team collaboration.
Aligning Products with Customer Expectations
The primary goal of QFD is to ensure that the final product aligns closely with what customers desire.
By focusing on customer requirements from the outset, manufacturers can avoid the pitfalls of designing products that miss the mark.
This alignment enhances customer satisfaction and builds brand loyalty.
Reducing Time to Market
QFD helps in streamlining the product development process by clearly defining specifications early on.
With a clear understanding of customer needs, the design and development teams can work more efficiently, avoiding unnecessary revisions.
This leads to faster completion times and quicker product launches.
Improving Team Collaboration
The QFD process involves cross-functional teams, including marketing, engineering, and production.
By bringing diverse perspectives together, QFD fosters better communication and collaboration.
Teams work collectively towards common goals, resulting in cohesive and well-rounded product development.
Steps Involved in the QFD Process
Implementing QFD involves several structured steps.
Each step builds on the previous one and ensures a comprehensive approach to meeting customer needs.
1. Identifying Customer Requirements
The first step is to gather and understand customer requirements.
This can be done through surveys, focus groups, or direct customer feedback.
Understanding what customers truly want is crucial for the next steps in the QFD process.
2. Prioritizing Customer Needs
Not all customer requirements are equally important.
QFD involves prioritizing these needs based on factors such as importance to the customer and potential impact on the business.
This step ensures that the most critical requirements receive the most attention.
3. Translating Requirements into Specifications
Once customer needs are prioritized, the next step is to translate these needs into technical specifications.
This involves determining how each requirement can be met within the production process.
4. Developing the House of Quality
The House of Quality matrix is created by linking customer requirements to the technical specifications.
This visual representation helps teams to understand the relationships and dependencies between various factors.
5. Finalizing and Implementing the Production Plan
Based on the House of Quality, a detailed production plan is developed.
This plan outlines the specific steps and resources required to meet the customer requirements.
Once the plan is finalized, it is implemented in the production process.
Case Studies: Successful QFD Implementation
Many companies have successfully implemented QFD to improve their manufacturing quality.
Here, we explore a few examples.
Toyota
Toyota is one of the pioneers in using QFD.
By focusing intensely on customer requirements, Toyota has maintained its reputation for high-quality vehicles.
QFD has helped Toyota to prioritize features and deliver cars that exceed customer expectations.
Boeing
Boeing uses QFD to design and manufacture aircraft that meet stringent customer and regulatory requirements.
By systematically addressing customer needs, Boeing ensures that its planes are safe, reliable, and comfortable.
Samsung
Samsung employs QFD in developing its electronic products.
This has enabled the company to stay ahead of the competition by innovating products that resonate well with customers.
Challenges in Implementing QFD
While QFD offers numerous benefits, its implementation can be challenging.
It requires significant effort in terms of time and resources.
Resource Intensive
QFD involves extensive data collection and analysis, which can be resource-intensive.
Companies need to invest in skilled personnel and tools to carry out the QFD process effectively.
Requires Cross-Functional Collaboration
Successful QFD implementation requires collaboration across various departments.
Achieving this level of coordination can be challenging, particularly in large organizations with siloed structures.
Maintaining Customer Focus
Keeping the focus on customer requirements throughout the product development cycle is crucial.
There is always a risk of deviation as technical and production challenges arise.
Conclusion
Quality Function Deployment (QFD) is a powerful methodology for aligning manufacturing processes with customer needs.
By following a structured approach, companies can develop high-quality products that meet or exceed customer expectations.
While implementing QFD can be challenging, the benefits in terms of improved product quality, enhanced customer satisfaction, and faster time to market make it a worthwhile investment.
For manufacturers aiming to stay competitive in today’s market, QFD offers a robust framework for achieving excellence in quality.
資料ダウンロード
QCD調達購買管理クラウド「newji」は、調達購買部門で必要なQCD管理全てを備えた、現場特化型兼クラウド型の今世紀最高の購買管理システムとなります。
ユーザー登録
調達購買業務の効率化だけでなく、システムを導入することで、コスト削減や製品・資材のステータス可視化のほか、属人化していた購買情報の共有化による内部不正防止や統制にも役立ちます。
NEWJI DX
製造業に特化したデジタルトランスフォーメーション(DX)の実現を目指す請負開発型のコンサルティングサービスです。AI、iPaaS、および先端の技術を駆使して、製造プロセスの効率化、業務効率化、チームワーク強化、コスト削減、品質向上を実現します。このサービスは、製造業の課題を深く理解し、それに対する最適なデジタルソリューションを提供することで、企業が持続的な成長とイノベーションを達成できるようサポートします。
オンライン講座
製造業、主に購買・調達部門にお勤めの方々に向けた情報を配信しております。
新任の方やベテランの方、管理職を対象とした幅広いコンテンツをご用意しております。
お問い合わせ
コストダウンが利益に直結する術だと理解していても、なかなか前に進めることができない状況。そんな時は、newjiのコストダウン自動化機能で大きく利益貢献しよう!
(Β版非公開)