- お役立ち記事
- Application and Effectiveness of the Taguchi Method in Quality Control in Manufacturing
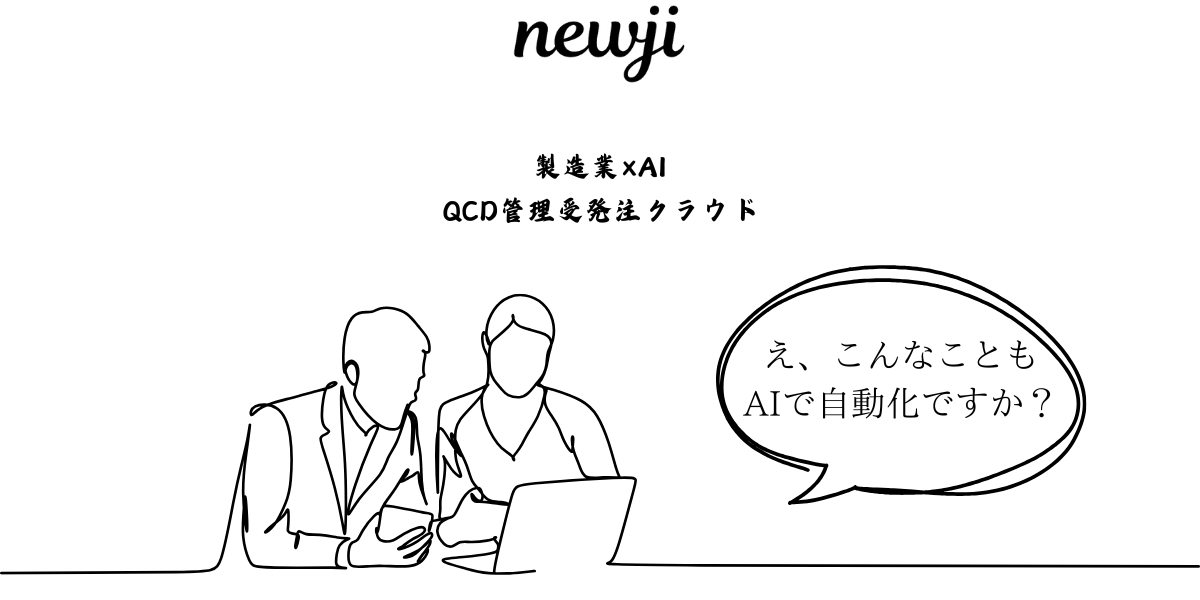
Application and Effectiveness of the Taguchi Method in Quality Control in Manufacturing
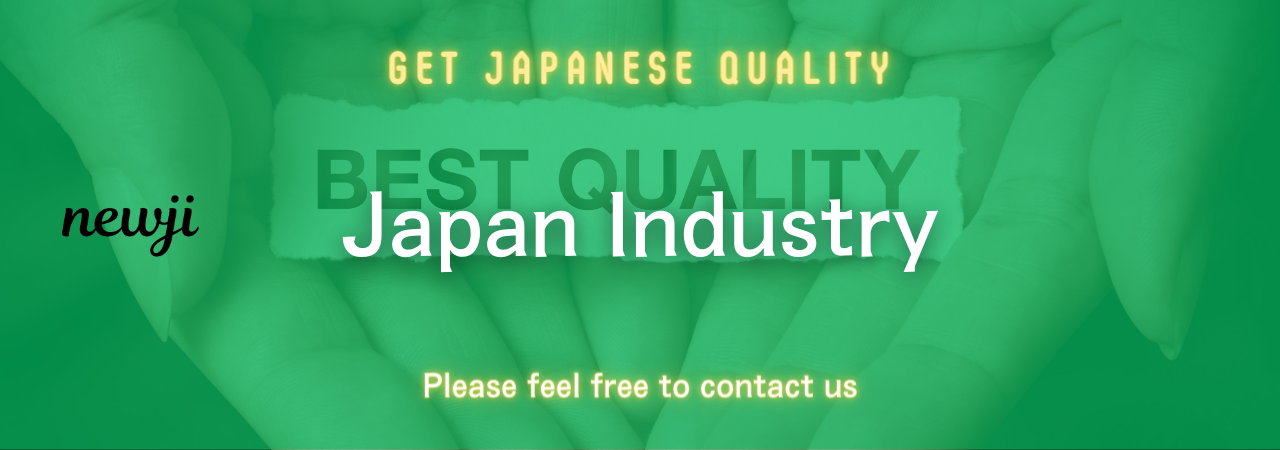
目次
Introduction to the Taguchi Method
In the world of manufacturing, maintaining high quality is essential.
One of the most effective techniques for quality control is the Taguchi Method.
Developed by Dr. Genichi Taguchi, this method focuses on improving product quality by minimizing variations and optimizing the production process.
But what exactly is the Taguchi Method, and why is it so effective?
Understanding the Taguchi Method
Basic Principles
The Taguchi Method is mainly based on two principles: robust design and process optimization.
Robust design aims to develop products that perform consistently under various conditions.
Process optimization, on the other hand, focuses on finding the best manufacturing parameters to achieve high-quality results.
Design of Experiments (DOE)
A key element of the Taguchi Method is the Design of Experiments (DOE).
DOE involves planning, conducting, and analyzing controlled tests to understand the factors that affect product quality.
By using a systematic approach, manufacturers can identify the optimal settings for their production processes.
Signal-to-Noise Ratio
Another important concept in the Taguchi Method is the Signal-to-Noise ratio (S/N ratio).
The S/N ratio measures the robustness of a system by comparing the signal (desired performance) to the noise (variability).
A higher S/N ratio indicates a more robust design, which means the product is less affected by variations in the production process.
Application of the Taguchi Method in Manufacturing
Employing the Taguchi Method in manufacturing can lead to significant improvements in product quality and process efficiency.
Let’s take a closer look at some of the most common applications.
Product Development
The Taguchi Method is widely used in product development to ensure new products meet high-quality standards.
By applying DOE, manufacturers can identify the best material combinations and design parameters.
This results in products that perform consistently and reliably in different circumstances.
Process Optimization
Optimizing the manufacturing process is crucial for reducing costs and increasing efficiency.
The Taguchi Method helps identify the optimal settings for various process parameters, such as temperature, pressure, and speed.
This leads to a more efficient production process with fewer defects and less waste.
Quality Improvement
Quality improvement is a continuous goal for manufacturers.
The Taguchi Method provides a structured approach to identify and eliminate the root causes of quality issues.
By focusing on reducing variability, manufacturers can improve the overall quality of their products and maintain customer satisfaction.
Benefits of the Taguchi Method
The Taguchi Method offers several advantages that make it a popular choice for quality control in manufacturing.
Cost Reduction
One of the primary benefits of the Taguchi Method is cost reduction.
By optimizing the production process and reducing defects, manufacturers can lower their production costs.
This leads to higher profit margins and more competitive pricing.
Enhanced Product Quality
Improving product quality is a key goal for any manufacturer.
The Taguchi Method helps achieve this by minimizing variability and ensuring consistent performance.
This results in higher customer satisfaction and a stronger market reputation.
Time Savings
Implementing the Taguchi Method can significantly reduce the time required to develop new products and optimize processes.
By using a systematic approach, manufacturers can quickly identify the best settings for their production parameters.
This accelerates the development cycle and allows for faster time-to-market.
Environmental Benefits
Reducing waste and improving process efficiency can have positive environmental impacts.
The Taguchi Method helps manufacturers minimize material usage and energy consumption, leading to a more sustainable production process.
Steps to Implement the Taguchi Method
Implementing the Taguchi Method in a manufacturing setting involves several key steps.
Let’s explore the process in more detail.
Identify the Problem
The first step is to clearly identify the problem or objective.
This involves understanding the specific quality issues or process inefficiencies that need to be addressed.
Select Factors and Levels
Next, identify the factors that could influence the outcome and determine the levels at which these factors will be tested.
This step is crucial for designing effective experiments.
Design the Experiment
Design the experiments using the DOE approach.
This involves planning a series of tests to systematically vary the factors and observe the results.
Conduct the Experiments
Carry out the experiments according to the plan.
Ensure that the tests are conducted in a controlled and consistent manner to obtain reliable data.
Analyze the Results
Analyze the data collected from the experiments to identify the optimal settings for the factors.
This analysis often involves calculating the S/N ratio to assess robustness.
Implement the Improvements
Finally, implement the identified improvements in the production process.
Monitor the impact of these changes to ensure they lead to the desired quality improvements.
Challenges and Considerations
While the Taguchi Method offers numerous benefits, there are also some challenges to consider.
Understanding these challenges can help manufacturers make the most of this powerful technique.
Complexity
The Taguchi Method can be complex and may require specialized knowledge for effective implementation.
Manufacturers may need to invest in training or hire experts to fully leverage this technique.
Initial Costs
There may be initial costs associated with conducting experiments and implementing changes.
However, these costs are often offset by the long-term benefits of improved quality and efficiency.
Data Quality
The accuracy of the Taguchi Method depends on the quality of the data collected during experiments.
Accurate and reliable data is essential for identifying the optimal settings for production parameters.
Conclusion
The Taguchi Method is a powerful technique for improving quality control in manufacturing.
By focusing on robust design and process optimization, it helps manufacturers reduce variability, lower costs, and enhance product quality.
While there may be some challenges, the benefits of implementing the Taguchi Method far outweigh the drawbacks.
With a systematic and thoughtful approach, manufacturers can achieve significant improvements in their production processes and maintain a competitive edge in the market.
資料ダウンロード
QCD調達購買管理クラウド「newji」は、調達購買部門で必要なQCD管理全てを備えた、現場特化型兼クラウド型の今世紀最高の購買管理システムとなります。
ユーザー登録
調達購買業務の効率化だけでなく、システムを導入することで、コスト削減や製品・資材のステータス可視化のほか、属人化していた購買情報の共有化による内部不正防止や統制にも役立ちます。
NEWJI DX
製造業に特化したデジタルトランスフォーメーション(DX)の実現を目指す請負開発型のコンサルティングサービスです。AI、iPaaS、および先端の技術を駆使して、製造プロセスの効率化、業務効率化、チームワーク強化、コスト削減、品質向上を実現します。このサービスは、製造業の課題を深く理解し、それに対する最適なデジタルソリューションを提供することで、企業が持続的な成長とイノベーションを達成できるようサポートします。
オンライン講座
製造業、主に購買・調達部門にお勤めの方々に向けた情報を配信しております。
新任の方やベテランの方、管理職を対象とした幅広いコンテンツをご用意しております。
お問い合わせ
コストダウンが利益に直結する術だと理解していても、なかなか前に進めることができない状況。そんな時は、newjiのコストダウン自動化機能で大きく利益貢献しよう!
(Β版非公開)