- お役立ち記事
- Application and Results of Six Sigma in Manufacturing Quality Assurance
Application and Results of Six Sigma in Manufacturing Quality Assurance
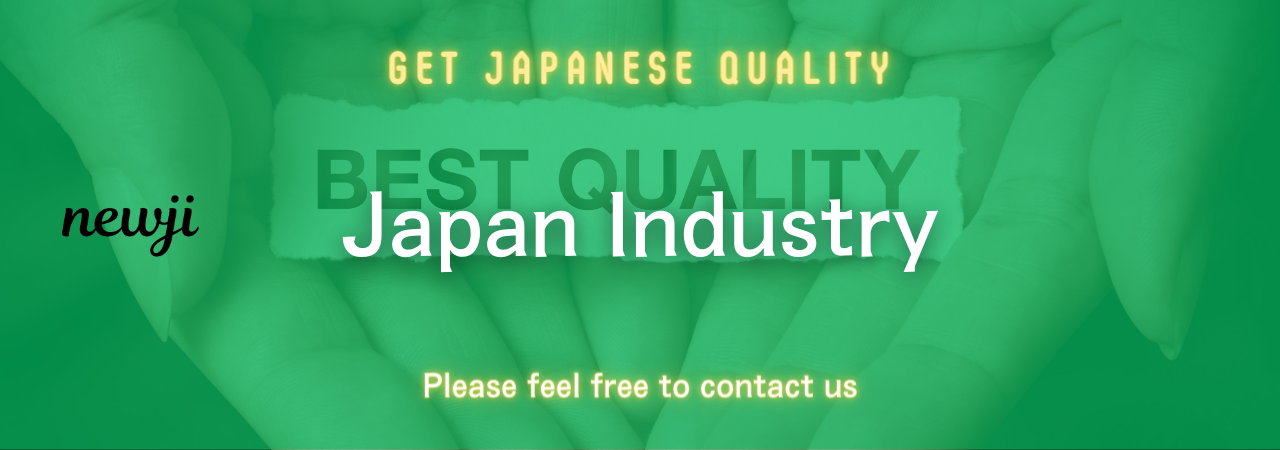
Six Sigma is a powerful methodology used across various industries to improve processes and ensure quality.
In the world of manufacturing, where precision and quality are paramount, Six Sigma stands out as an effective tool for maintaining and enhancing production standards.
This methodology helps companies minimize defects, reduce costs, and improve customer satisfaction. In this article, we’ll delve into the applications and results of Six Sigma in manufacturing quality assurance.
目次
Understanding Six Sigma
Six Sigma is a data-driven approach that aims to eliminate defects and improve processes by identifying and removing the causes of errors.
It utilizes statistical tools and techniques to achieve these goals. The term “Six Sigma” itself comes from the standard deviation used in statistics, symbolizing a process that is 99.99966% defect-free, or producing no more than 3.4 defects per million opportunities.
The Core Principles
At the heart of Six Sigma are five key principles, often summarized by the acronym DMAIC:
1. **Define**: Identifying the problem and the project goals.
2. **Measure**: Collecting data to understand current performance.
3. **Analyze**: Identifying root causes of defects.
4. **Improve**: Implementing solutions to address root causes.
5. **Control**: Monitoring changes to ensure ongoing success.
These steps guide teams through a structured problem-solving process, ensuring they reach effective and sustainable solutions.
Applications of Six Sigma in Manufacturing
Reducing Defects and Variability
One of the primary applications of Six Sigma in manufacturing is reducing defects and variability in production processes.
By analyzing data and understanding the sources of variation, manufacturers can make necessary adjustments to ensure consistent quality.
For example, a car manufacturer might use Six Sigma to identify and rectify issues in their assembly line that cause defects in engine parts.
Optimizing Supply Chain Management
Six Sigma methodologies can also be applied to optimizing supply chain management.
Companies can utilize Six Sigma tools to streamline their supply chain operations, thereby reducing lead times and improving order accuracy.
This ensures a smoother production process and reduces the likelihood of disruptions, leading to better product quality and customer satisfaction.
Improving Equipment Efficiency
In manufacturing, equipment efficiency plays a crucial role in maintaining production quality.
Six Sigma can be used to analyze equipment performance, identify downtime causes, and implement preventative measures.
This leads to higher equipment uptime, more consistent production output, and ultimately, better product quality.
Enhancing Product Design
Six Sigma principles can also be applied during the product design phase.
By incorporating Six Sigma techniques early in the design process, manufacturers can foresee potential issues and address them before production begins.
This proactive approach not only saves time and resources but also ensures that the final product meets quality standards.
Results Achieved Through Six Sigma
Cost Reduction
One of the most significant outcomes of implementing Six Sigma in manufacturing is cost reduction.
By minimizing defects and optimizing processes, companies often experience a substantial decrease in waste and rework, leading to lower production costs.
For instance, GE, one of the pioneers in using Six Sigma, reported savings of over $10 billion in just five years by implementing Six Sigma methodologies.
Improved Product Quality
Implementing Six Sigma helps in achieving better quality control, which translates into higher quality products.
Reducing variability and defects ensures that products consistently meet customer expectations.
This not only enhances the brand’s reputation but also boosts customer loyalty and satisfaction.
Increased Efficiency
Another key result of Six Sigma is increased efficiency in manufacturing processes.
By identifying bottlenecks and eliminating inefficiencies, production lines can run more smoothly and at a higher capacity.
This leads to faster turnaround times, allowing companies to meet demand more effectively.
Better Customer Satisfaction
When a company produces high-quality products consistently, it naturally leads to higher customer satisfaction.
Six Sigma ensures that customer requirements are met or exceeded, fostering a positive relationship between the company and its customers.
This is particularly crucial in industries where competition is fierce, and customer loyalty is hard to come by.
Enhanced Employee Morale
Successful implementation of Six Sigma also results in improved employee morale.
When employees see tangible results from their efforts and are part of a thriving and efficient production environment, their job satisfaction increases.
This, in turn, leads to better performance and contributes to the overall success of the organization.
Conclusion
Six Sigma has proven to be an invaluable tool in the realm of manufacturing quality assurance.
Its structured approach to problem-solving and focus on data-driven decision-making makes it particularly effective in reducing defects, optimizing processes, and enhancing product quality.
The applications of Six Sigma in manufacturing are vast, from improving equipment efficiency to enhancing product design.
Moreover, the results—ranging from cost reduction and increased efficiency to better customer satisfaction and employee morale—underscore its importance in maintaining high standards in manufacturing.
Embracing Six Sigma not only helps manufacturers meet their quality goals but also positions them for long-term success in a competitive market.
資料ダウンロード
QCD調達購買管理クラウド「newji」は、調達購買部門で必要なQCD管理全てを備えた、現場特化型兼クラウド型の今世紀最高の購買管理システムとなります。
ユーザー登録
調達購買業務の効率化だけでなく、システムを導入することで、コスト削減や製品・資材のステータス可視化のほか、属人化していた購買情報の共有化による内部不正防止や統制にも役立ちます。
NEWJI DX
製造業に特化したデジタルトランスフォーメーション(DX)の実現を目指す請負開発型のコンサルティングサービスです。AI、iPaaS、および先端の技術を駆使して、製造プロセスの効率化、業務効率化、チームワーク強化、コスト削減、品質向上を実現します。このサービスは、製造業の課題を深く理解し、それに対する最適なデジタルソリューションを提供することで、企業が持続的な成長とイノベーションを達成できるようサポートします。
オンライン講座
製造業、主に購買・調達部門にお勤めの方々に向けた情報を配信しております。
新任の方やベテランの方、管理職を対象とした幅広いコンテンツをご用意しております。
お問い合わせ
コストダウンが利益に直結する術だと理解していても、なかなか前に進めることができない状況。そんな時は、newjiのコストダウン自動化機能で大きく利益貢献しよう!
(Β版非公開)