- お役立ち記事
- Application development of functional materials using graphite silica and how to proceed with product planning
月間77,185名の
製造業ご担当者様が閲覧しています*
*2025年2月28日現在のGoogle Analyticsのデータより
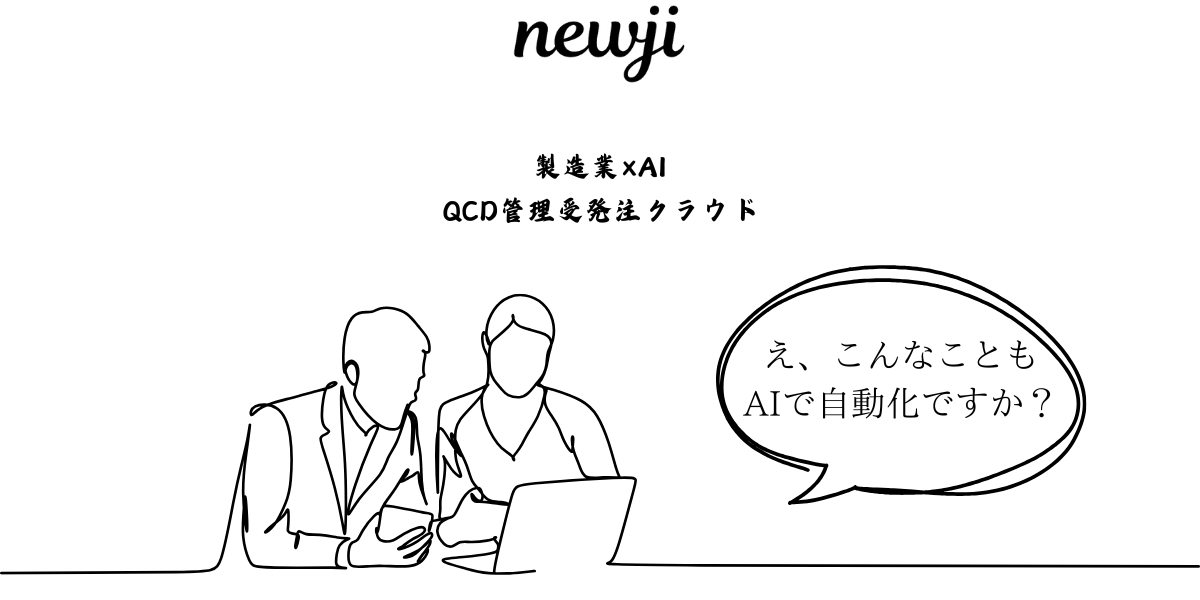
Application development of functional materials using graphite silica and how to proceed with product planning
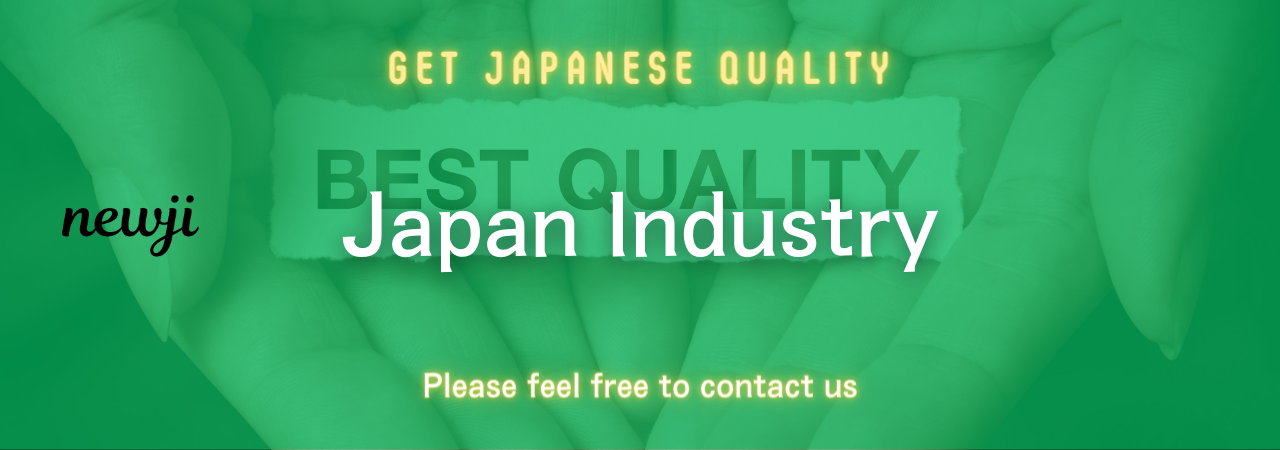
目次
Understanding Graphite Silica
Graphite silica is a fascinating fusion of two distinct materials – graphite and silica.
Graphite is well-known for its excellent electrical conductivity, while silica is recognized for its high thermal stability and insulating properties.
When combined, these materials create a composite that inherits beneficial properties from both parent materials.
This hybrid material is useful in various applications due to its distinct characteristics.
Graphite silica composites are often sought for their durability, thermal resistance, and ability to conduct electricity with minimal resistance.
Such attributes make them ideal candidates for use in diverse technological fields.
The Role of Graphite Silica in Functional Material Development
When developing functional materials, graphite silica is an exciting choice due to its versatility.
These composites can be tailored to meet the specific needs of different industries.
For instance, in electronics, graphite silica is used in the manufacture of components that require both electrical conductivity and thermal management.
In the energy sector, these materials play a pivotal role in improving the efficiency and longevity of devices such as batteries and solar cells.
Their hybrid nature allows them to support high energy densities while maintaining structural integrity under various conditions.
Moreover, graphite silica’s resistance to high temperatures makes it an excellent material for applications that involve combustion or extreme heat exposure.
This quality is particularly valuable in the automotive and aerospace industries, where materials must withstand harsh environments without degrading.
How to Develop Graphite Silica-Based Products
Creating products with graphite silica involves several methodical steps.
The development process is rooted in both scientific understanding and creative product design, ensuring that the final product meets desired specifications.
Step 1: Identifying the Need
The first step in product development involves identifying a clear need or problem that the new material can address.
This requires an extensive market analysis to understand both the challenges faced by potential users and how graphite silica can provide a solution.
Engaging with stakeholders from various sectors can provide insights into how this material can be applied effectively.
Additionally, analyzing market trends and advancements in technology helps in determining the product’s viability and potential success.
Step 2: Research and Development
Once a need is identified, the next focus should be on research and development (R&D).
This phase includes experimenting with different combinations of graphite and silica to hone in on the optimal composite ratios.
The R&D process focuses on enhancing the properties that best suit the end application, whether it’s maximizing thermal resistance, improving conductivity, or optimizing structural durability.
During this stage, collaboration with material scientists and engineers helps in evaluating prototypes and iterative testing to refine the material properties and design.
Step 3: Design and Testing
Next is the design phase, where the product’s specific application dictates the project scope and development timeline.
Computer-aided design (CAD) tools are often employed to simulate how the material will perform in real-world conditions.
This makes it possible to foresee design issues and make necessary adjustments before physical prototyping begins.
Testing is a crucial part of this phase, as it involves subjecting prototypes to rigorous conditions that replicate their intended use.
The aim is to identify any deficiencies and make improvements, ensuring the final product is reliable and functional.
Step 4: Production and Scale-Up
After successful testing, the focus shifts to production.
Developing a cost-effective production process that maintains the quality and consistency of graphite silica is paramount.
The process may involve traditional manufacturing methods or advanced techniques like additive manufacturing, depending on the product’s complexity and requirements.
Scaling up production while maintaining low costs is essential for commercial success, as it enables widespread application in the market.
This often requires investing in specialized equipment and training the workforce to adapt to new manufacturing processes.
Step 5: Marketing and Launch
Once the product is ready, creating a robust marketing strategy to promote its unique benefits is critical.
This involves identifying target audiences and the best channels to reach them.
Effective marketing strategies could range from digital campaigns to direct engagement with industries that can benefit from the product.
Launching the product requires careful planning to ensure that distribution channels are streamlined and that any initial customer feedback can be swiftly addressed.
Post-launch analysis is also crucial for continuous improvement and to adapt products to evolving market demands.
The Future of Graphite Silica in Material Science
With ongoing advancements in materials technology, the future of graphite silica looks promising.
As industries continue to seek more efficient and durable materials, the demand for innovative composites like graphite silica is expected to grow.
Researchers and companies alike are exploring new ways to refine its properties and expand its applications.
In addition to existing uses, potential future applications include developing advanced coatings, constructing lightweight yet robust structures, and creating components for next-gen electronic devices.
The continuous evolution of this material will likely drive innovation across multiple sectors, contributing significantly to leaps in technology and sustainability.
In summary, the application development of functional materials using graphite silica involves a thorough understanding of its properties and potential uses.
By following a detailed plan from need identification to production and launch, businesses can harness the advantages of this composite to create beneficial products in a variety of fields.
資料ダウンロード
QCD管理受発注クラウド「newji」は、受発注部門で必要なQCD管理全てを備えた、現場特化型兼クラウド型の今世紀最高の受発注管理システムとなります。
ユーザー登録
受発注業務の効率化だけでなく、システムを導入することで、コスト削減や製品・資材のステータス可視化のほか、属人化していた受発注情報の共有化による内部不正防止や統制にも役立ちます。
NEWJI DX
製造業に特化したデジタルトランスフォーメーション(DX)の実現を目指す請負開発型のコンサルティングサービスです。AI、iPaaS、および先端の技術を駆使して、製造プロセスの効率化、業務効率化、チームワーク強化、コスト削減、品質向上を実現します。このサービスは、製造業の課題を深く理解し、それに対する最適なデジタルソリューションを提供することで、企業が持続的な成長とイノベーションを達成できるようサポートします。
製造業ニュース解説
製造業、主に購買・調達部門にお勤めの方々に向けた情報を配信しております。
新任の方やベテランの方、管理職を対象とした幅広いコンテンツをご用意しております。
お問い合わせ
コストダウンが利益に直結する術だと理解していても、なかなか前に進めることができない状況。そんな時は、newjiのコストダウン自動化機能で大きく利益貢献しよう!
(β版非公開)