- お役立ち記事
- Application of fatigue damage detection/monitoring technology, life prediction, and data processing technology for mechanical systems
月間76,176名の
製造業ご担当者様が閲覧しています*
*2025年3月31日現在のGoogle Analyticsのデータより
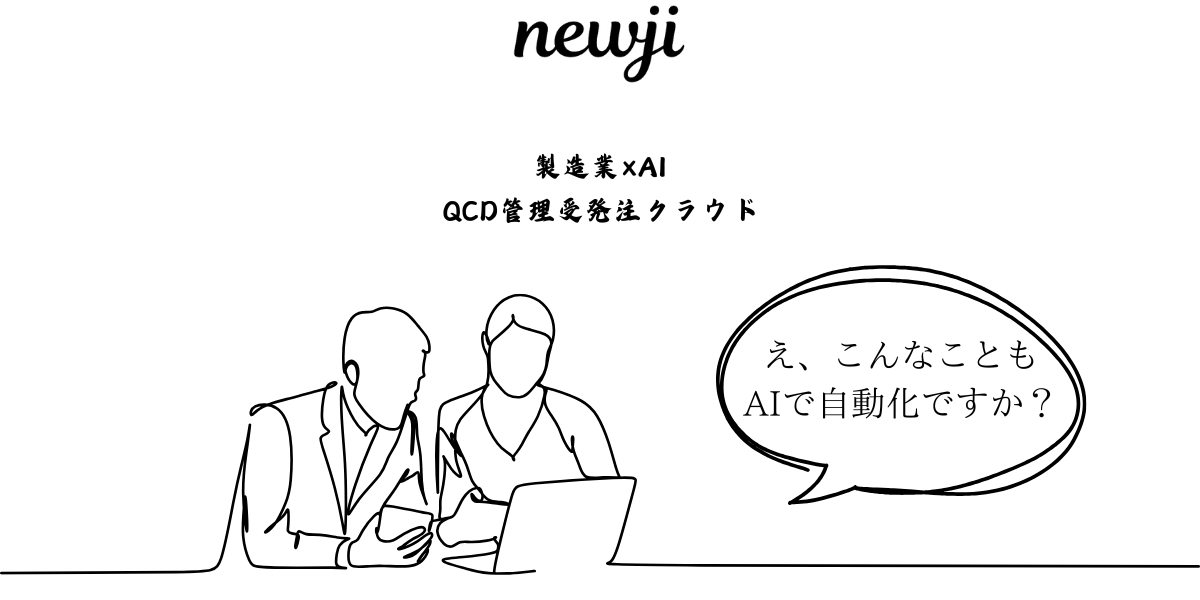
Application of fatigue damage detection/monitoring technology, life prediction, and data processing technology for mechanical systems
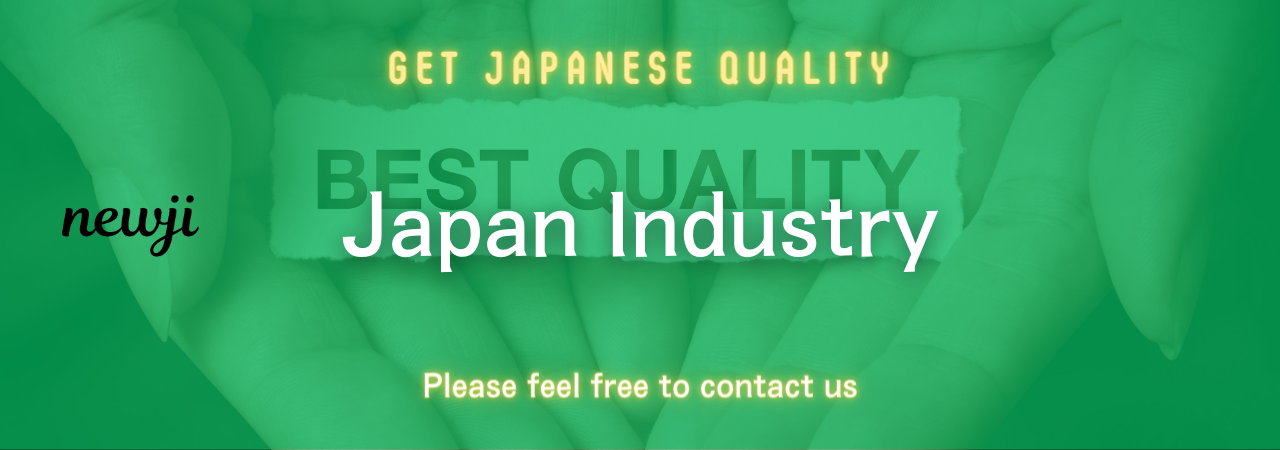
目次
Understanding Fatigue Damage in Mechanical Systems
Fatigue damage in mechanical systems is a critical issue that affects the longevity and efficiency of machinery.
When machines undergo repeated stress cycles, the materials can weaken over time.
This can lead to unexpected failures, which in turn cause downtime or even severe accidents.
Understanding fatigue damage is the first step toward creating effective monitoring and prediction strategies to counteract these failures.
Importance of Fatigue Damage Detection
Detecting fatigue damage early is essential for maintaining mechanical systems.
By identifying signs of wear and tear before they become serious, maintenance can be scheduled efficiently.
This proactive approach not only saves time but also reduces the cost of repairs and extends the machinery’s lifespan.
Modern technology has made it possible to employ sophisticated fatigue damage detection methods.
Techniques like acoustic emission, vibration analysis, and thermography are commonly used to detect early signs of fatigue.
These methods help in identifying areas where the material is beginning to fail, alerting maintenance teams before significant damage occurs.
Monitoring Technologies for Fatigue Damage
Monitoring technologies are integral to the ongoing health of mechanical systems.
They provide continuous feedback on the state of the machinery, allowing for real-time analysis and immediate action.
These technologies include strain gauges, which measure deformation, and ultrasonic testing, which identifies subsurface defects.
The use of sensors and IoT (Internet of Things) technology has revolutionized fatigue damage monitoring.
These systems can collect vast amounts of data from various parts of a machine, providing a comprehensive overview of its condition.
This data is then used to predict future failures, allowing for timely maintenance and preventing potential downtime.
Advancements in Life Prediction of Mechanical Systems
Predicting the life span of mechanical systems is critical for planning and resource allocation.
Life prediction technology uses complex algorithms and data analysis to estimate when a machine might fail.
These predictions are based on historical performance data and the current condition of the machinery.
With advancements in AI and machine learning, life prediction models have become more accurate.
These technologies analyze patterns and trends in data that might not be evident to human observers.
By anticipating failures, companies can make informed decisions about equipment replacement and maintenance scheduling.
Data Processing Technologies in Mechanical Systems
Data processing technologies play a vital role in the effective management of mechanical systems.
With the abundance of data generated by modern machines, processing this information efficiently is crucial.
Data processing technologies gather, analyze, and interpret this data to provide actionable insights.
Big data analytics is one of the most significant advancements in this field.
It allows for the analysis of large data sets to identify trends and patterns.
Another critical technology is cloud computing, which provides the computational power necessary to process and store vast amounts of data.
This enables companies to access real-time data and analytics from anywhere in the world.
Integrating Technologies for Optimal Performance
The integration of fatigue damage detection, life prediction, and data processing technologies results in optimal performance of mechanical systems.
When these technologies work together seamlessly, they create a comprehensive monitoring and maintenance strategy.
For example, data collected from fatigue detection technologies can feed into life prediction models, providing more accurate forecasts.
In turn, these predictions can help optimize maintenance schedules and extend the life of machinery.
Data processing technologies support this integration by ensuring that all information is current, accurate, and accessible.
The Future of Mechanical System Management
The future of mechanical system management lies in the continuous advancement of technology.
As new technologies emerge, they will offer even more precise detection, monitoring, and prediction capabilities.
The integration of these technologies with advanced analytics will allow for unprecedented insights into machinery health.
One area of potential growth is the development of self-healing materials, which can repair themselves after sustaining damage.
Such innovations could revolutionize how mechanical systems operate, making machinery more resilient to fatigue.
Conclusion
The application of fatigue damage detection, monitoring technology, life prediction, and data processing is transforming how mechanical systems are managed.
These technologies allow for proactive maintenance strategies, reducing downtime, and extending the life of machinery.
By staying abreast of technological advancements, companies can ensure the reliability and efficiency of their systems, ultimately leading to greater productivity and reduced costs.
資料ダウンロード
QCD管理受発注クラウド「newji」は、受発注部門で必要なQCD管理全てを備えた、現場特化型兼クラウド型の今世紀最高の受発注管理システムとなります。
ユーザー登録
受発注業務の効率化だけでなく、システムを導入することで、コスト削減や製品・資材のステータス可視化のほか、属人化していた受発注情報の共有化による内部不正防止や統制にも役立ちます。
NEWJI DX
製造業に特化したデジタルトランスフォーメーション(DX)の実現を目指す請負開発型のコンサルティングサービスです。AI、iPaaS、および先端の技術を駆使して、製造プロセスの効率化、業務効率化、チームワーク強化、コスト削減、品質向上を実現します。このサービスは、製造業の課題を深く理解し、それに対する最適なデジタルソリューションを提供することで、企業が持続的な成長とイノベーションを達成できるようサポートします。
製造業ニュース解説
製造業、主に購買・調達部門にお勤めの方々に向けた情報を配信しております。
新任の方やベテランの方、管理職を対象とした幅広いコンテンツをご用意しております。
お問い合わせ
コストダウンが利益に直結する術だと理解していても、なかなか前に進めることができない状況。そんな時は、newjiのコストダウン自動化機能で大きく利益貢献しよう!
(β版非公開)