- お役立ち記事
- Application of IH reflow technology and SDGs compliance
Application of IH reflow technology and SDGs compliance
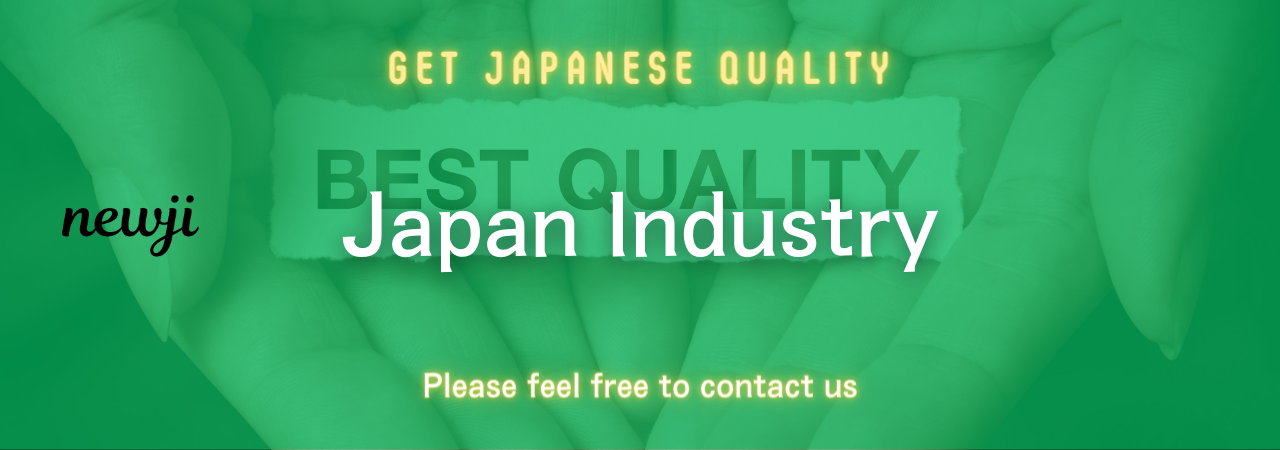
目次
Understanding IH Reflow Technology
Induction Heating (IH) reflow technology is a modern innovation in the field of electronics manufacturing.
This technique is primarily used for soldering electronic components onto circuit boards, a critical step in assembling various electronic devices.
Unlike traditional reflow methods, IH reflow uses electromagnetic induction to heat components, making it more efficient and precise.
One of the key advantages of IH reflow technology is its ability to provide uniform heating.
This is achieved by generating heat directly within the component through induction, which minimizes the risk of overheating or damaging sensitive parts.
The precision of IH reflow technology ensures high-quality solder joints, which are essential for the reliability and longevity of electronic devices.
Furthermore, IH reflow systems often feature rapid heating and cooling cycles, which improve production throughput and reduce energy consumption.
This efficiency aligns perfectly with the growing demands for sustainable manufacturing practices.
In this regard, IH reflow technology offers a promising alternative to traditional convection or infrared-based reflow systems.
The Role of IH Reflow Technology in Sustainable Development
In recent years, industries worldwide have increasingly focused on integrating sustainability into their operations.
This shift is driven by the United Nations Sustainable Development Goals (SDGs), which aim to address global challenges such as climate change, resource depletion, and environmental degradation.
IH reflow technology plays a significant role in advancing these goals by promoting more sustainable manufacturing processes.
One of the primary ways IH reflow technology contributes to sustainability is through energy efficiency.
Traditional reflow methods can be energy-intensive due to the need for prolonged heating periods and multiple temperature adjustments.
However, IH reflow systems can minimize energy consumption by quickly reaching the desired temperature and efficiently maintaining it.
This reduction in energy usage not only lowers operational costs but also decreases the carbon footprint of the manufacturing process, aligning with SDG 7, which promotes affordable and clean energy.
Moreover, IH reflow technology supports SDG 12, responsible consumption and production, by reducing waste.
The precise control offered by induction heating minimizes the occurrence of defects and reworking, resulting in less material wastage and fewer discarded components.
This leads to a more efficient use of resources, which is critical for sustainable development.
Implementing IH Reflow Technology for SDG Compliance
For companies aiming to align with the SDGs, implementing IH reflow technology can be a strategic move.
The transition to this innovative approach involves several key steps, beginning with the assessment of current manufacturing processes.
Firstly, organizations should conduct a comprehensive analysis of their existing reflow systems.
This involves evaluating energy consumption, production efficiency, and quality metrics to identify areas of improvement.
Such an analysis helps determine the potential benefits of switching to IH reflow technology.
Next, companies need to invest in IH reflow equipment and train their workforce to operate the new systems.
Although the initial investment may be significant, the long-term savings in energy costs and increased production efficiency can offset these expenses.
Additionally, training programs help ensure that employees are proficient in managing and maintaining IH reflow technology, maximizing its potential benefits.
It’s also essential for organizations to monitor and evaluate the impact of IH reflow technology on their sustainability objectives.
This involves tracking key performance indicators related to energy consumption, production waste, and product quality.
By maintaining a clear overview of these metrics, companies can make informed decisions to optimize their processes further.
Advantages of IH Reflow Technology in the Electronics Industry
The electronics industry is one of the primary beneficiaries of IH reflow technology.
This advanced soldering method offers several advantages, making it an appealing choice for manufacturers looking to enhance their production capabilities while adhering to sustainable practices.
One of the main advantages of IH reflow technology is its ability to handle complex and densely populated circuit boards.
With the increasing demand for compact and multifunctional electronic devices, manufacturers are faced with the challenge of soldering numerous components within a limited space.
IH reflow technology, with its precise heat control, allows for the effective soldering of densely packed components without risking thermal damage, leading to higher product reliability.
Another benefit is the environmental impact of IH reflow technology.
By reducing energy consumption and minimizing waste, this technology contributes to a more sustainable manufacturing ecosystem.
In a world where consumers and regulatory bodies are increasingly scrutinizing environmental practices, adopting IH reflow technology can enhance a company’s reputation and competitive edge.
Furthermore, IH reflow technology offers flexibility in production.
With programmable heating profiles and rapid temperature adjustments, manufacturers can easily customize their processes to accommodate different types of components and materials.
This adaptability is crucial for meeting the diverse and ever-changing demands of the electronics market.
Future Prospects of IH Reflow Technology
As the electronics industry continues to evolve, IH reflow technology is poised to play a significant role in shaping its future.
Ongoing advancements in induction heating techniques and equipment design promise even greater efficiency and precision in production processes.
One potential area of development is the integration of artificial intelligence and machine learning with IH reflow systems.
These technologies can enhance process optimization, enabling real-time adjustments based on data analytics and predictive modeling.
Such advancements can further improve production efficiency, reduce waste, and ensure the consistent quality of solder joints.
Additionally, as environmental concerns become more pronounced, IH reflow technology may expand its applications beyond the electronics industry.
Sectors such as automotive, aerospace, and medical devices, which require reliable and high-performance components, may increasingly adopt induction heating due to its sustainable and precise soldering capabilities.
In conclusion, IH reflow technology is a powerful tool for achieving SDG compliance while advancing manufacturing efficiency and quality.
By understanding its benefits and implementing best practices, organizations can pave the way for a more sustainable and prosperous future.
資料ダウンロード
QCD調達購買管理クラウド「newji」は、調達購買部門で必要なQCD管理全てを備えた、現場特化型兼クラウド型の今世紀最高の購買管理システムとなります。
ユーザー登録
調達購買業務の効率化だけでなく、システムを導入することで、コスト削減や製品・資材のステータス可視化のほか、属人化していた購買情報の共有化による内部不正防止や統制にも役立ちます。
NEWJI DX
製造業に特化したデジタルトランスフォーメーション(DX)の実現を目指す請負開発型のコンサルティングサービスです。AI、iPaaS、および先端の技術を駆使して、製造プロセスの効率化、業務効率化、チームワーク強化、コスト削減、品質向上を実現します。このサービスは、製造業の課題を深く理解し、それに対する最適なデジタルソリューションを提供することで、企業が持続的な成長とイノベーションを達成できるようサポートします。
オンライン講座
製造業、主に購買・調達部門にお勤めの方々に向けた情報を配信しております。
新任の方やベテランの方、管理職を対象とした幅広いコンテンツをご用意しております。
お問い合わせ
コストダウンが利益に直結する術だと理解していても、なかなか前に進めることができない状況。そんな時は、newjiのコストダウン自動化機能で大きく利益貢献しよう!
(Β版非公開)