- お役立ち記事
- Application of plastic fracture mechanism, life prediction, fracture surface analysis, and damage prevention measures
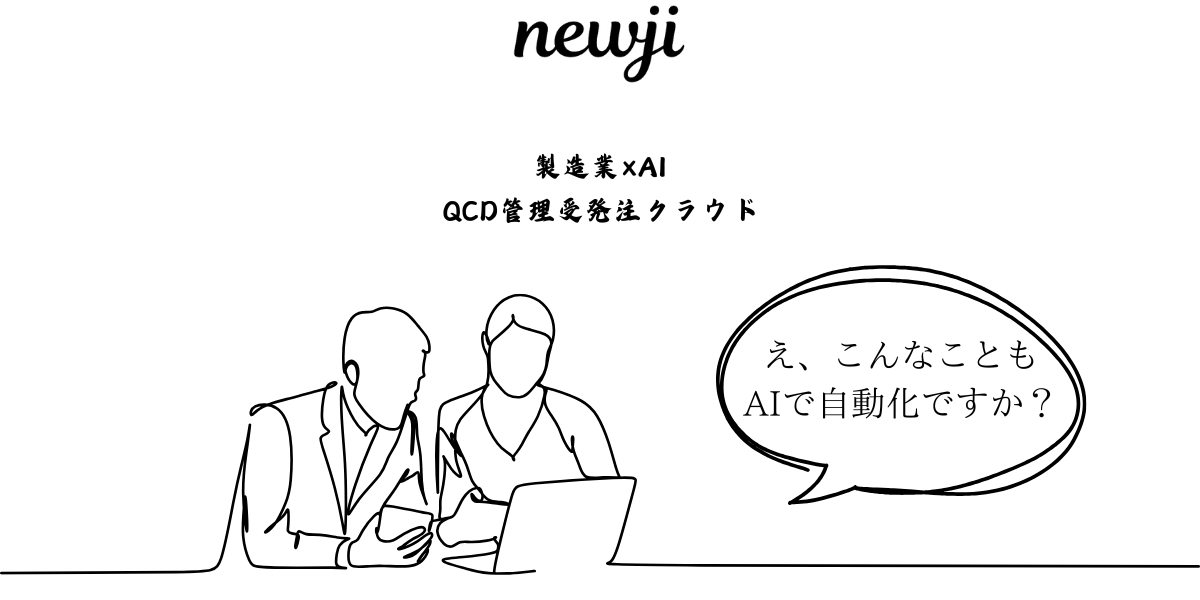
Application of plastic fracture mechanism, life prediction, fracture surface analysis, and damage prevention measures
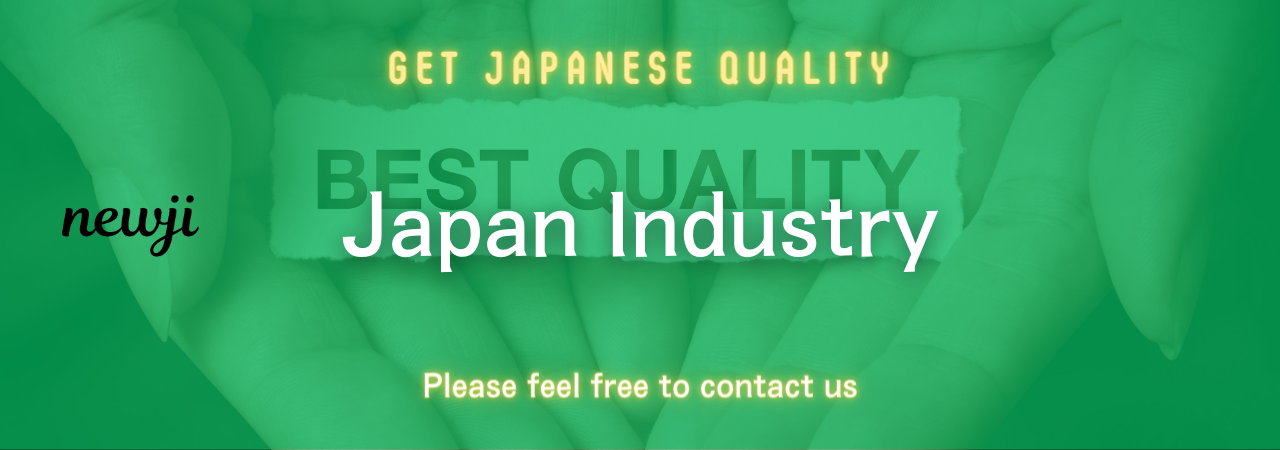
目次
Understanding Plastic Fracture Mechanism
The plastic fracture mechanism is a fundamental concept that explains how materials deform and eventually break under stress.
In simple terms, when a force is applied to an object, it can either return to its original shape (elastic deformation) or become permanently deformed (plastic deformation).
Once a material has undergone plastic deformation, it is more prone to fracturing.
Understanding this mechanism is crucial for engineers and scientists who work with materials that require both strength and durability.
Materials such as plastics, metals, and ceramics can exhibit different fracture behaviors under varying conditions.
The Process of Plastic Fracture
The process of plastic fracture begins with the nucleation of small micro-cracks within the material.
These cracks typically form at sites of stress concentration, such as impurities, voids, or grain boundaries.
As stress continues to be applied, these micro-cracks grow and connect with each other, leading to the formation of a larger crack.
Eventually, the crack reaches a critical size and propagates rapidly, resulting in the material’s complete fracture.
Predicting Material Life through Fracture Mechanics
Fracture mechanics provides a framework for predicting the life of a material by studying the behavior of cracks.
By understanding how cracks initiate and grow, engineers can estimate when a material might fail and take preventative steps.
Fatigue Life Prediction
One key aspect of fracture mechanics is the prediction of fatigue life.
Fatigue refers to the weakening of a material when subjected to repeated loading and unloading cycles.
Even if the applied stress is below the material’s yield strength, fatigue can cause cracks to form over time.
The S-N curve, which plots stress (S) against the number of cycles to failure (N), is a valuable tool in predicting fatigue life.
Another important concept is fracture toughness, which measures a material’s ability to resist crack propagation.
Materials with higher fracture toughness are more resistant to cracking and have longer fatigue lives.
Using Computer Simulations
With the advancement of computational tools, engineers now use sophisticated simulations to predict material behavior.
Finite element analysis (FEA) is widely used to simulate how materials will react under different loading conditions.
Such simulations provide insights into potential failure points and allow scientists to design more robust materials.
Analyzing Fracture Surfaces
Fracture surface analysis is a forensic technique used to investigate the cause of material failures.
By examining the surface of a fracture, experts can gather information about the failure mode and potentially identify contributing factors.
Macroscopic Examination
The initial examination of a fracture surface usually involves a macroscopic analysis.
This includes visual inspection and photography to capture the overall fracture pattern.
Information such as the fracture’s texture, color, and direction of crack propagation can provide valuable clues.
Microscopic Examination
For a more detailed analysis, a microscopic examination is conducted using tools such as scanning electron microscopes (SEM).
Microscopic examination can reveal features such as striations, dimples, and ridges, which are indicative of different types of fracture modes like ductile or brittle fracture.
Preventing Fracture through Damage Prevention Measures
Implementing damage prevention measures is critical to extending the life of materials and preventing catastrophic failures.
Material Selection
Selecting the right materials for specific applications is crucial.
Materials with higher fracture toughness and resistance to environmental conditions should be chosen for applications involving high stress or extreme conditions.
Quality Control and Inspections
Regular quality control and inspections are necessary to ensure that materials are free of defects that could act as stress concentrators.
Non-destructive testing methods, like X-ray or ultrasonic testing, can help identify these issues before they lead to a failure.
Design Improvements
Often, rethinking design can help prevent fractures.
Introducing features such as fillets or rounded corners can help redistribute stress and minimize stress concentration.
Moreover, load path continuity is an essential principle of design engineering to avoid abrupt changes in cross-sectional areas of a structure.
Environmental Considerations
Materials can deteriorate due to environmental factors like temperature, humidity, and exposure to chemicals.
Protective coatings and proper sealing can mitigate these effects and extend material life.
Conclusion
The application of the plastic fracture mechanism, life prediction, fracture surface analysis, and damage prevention measures plays a vital role in engineering.
By understanding the detailed processes of how materials fracture, and how to predict and prevent these fractures, we can ensure the structural integrity of components used in a wide array of industries.
Adopting these best practices not only enhances safety but also leads to cost savings and efficiency improvements.
As technology continues to advance, so too will our methods of managing and preventing material fractures.
資料ダウンロード
QCD調達購買管理クラウド「newji」は、調達購買部門で必要なQCD管理全てを備えた、現場特化型兼クラウド型の今世紀最高の購買管理システムとなります。
ユーザー登録
調達購買業務の効率化だけでなく、システムを導入することで、コスト削減や製品・資材のステータス可視化のほか、属人化していた購買情報の共有化による内部不正防止や統制にも役立ちます。
NEWJI DX
製造業に特化したデジタルトランスフォーメーション(DX)の実現を目指す請負開発型のコンサルティングサービスです。AI、iPaaS、および先端の技術を駆使して、製造プロセスの効率化、業務効率化、チームワーク強化、コスト削減、品質向上を実現します。このサービスは、製造業の課題を深く理解し、それに対する最適なデジタルソリューションを提供することで、企業が持続的な成長とイノベーションを達成できるようサポートします。
オンライン講座
製造業、主に購買・調達部門にお勤めの方々に向けた情報を配信しております。
新任の方やベテランの方、管理職を対象とした幅広いコンテンツをご用意しております。
お問い合わせ
コストダウンが利益に直結する術だと理解していても、なかなか前に進めることができない状況。そんな時は、newjiのコストダウン自動化機能で大きく利益貢献しよう!
(Β版非公開)