- お役立ち記事
- Application of Taguchi method (quality engineering) to prevent market quality problems and reduce costs
月間76,176名の
製造業ご担当者様が閲覧しています*
*2025年3月31日現在のGoogle Analyticsのデータより
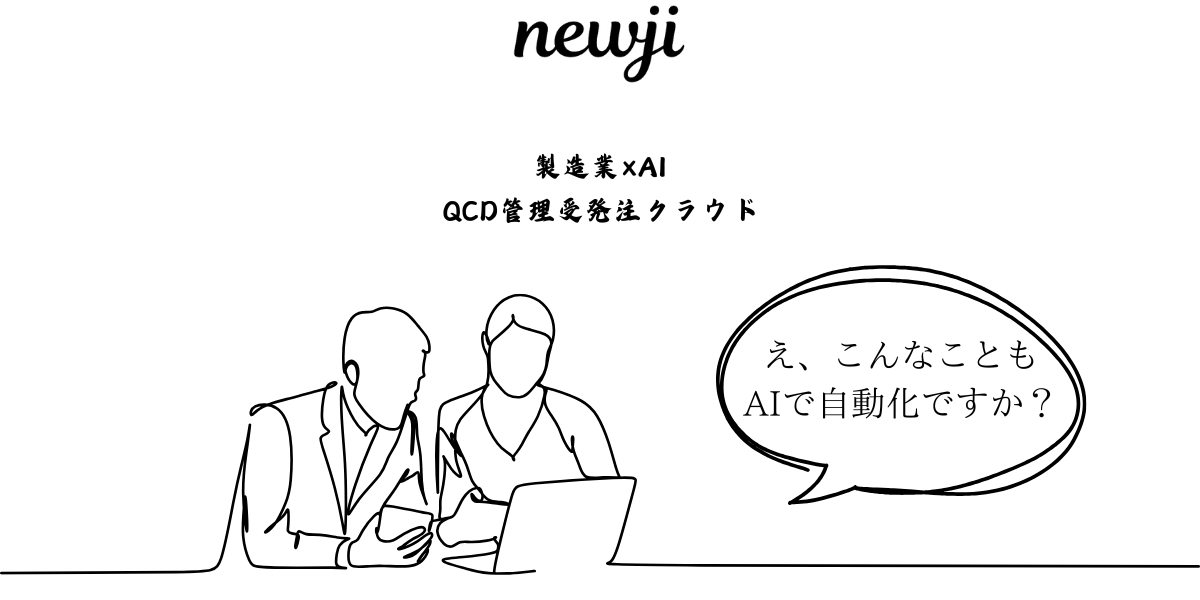
Application of Taguchi method (quality engineering) to prevent market quality problems and reduce costs
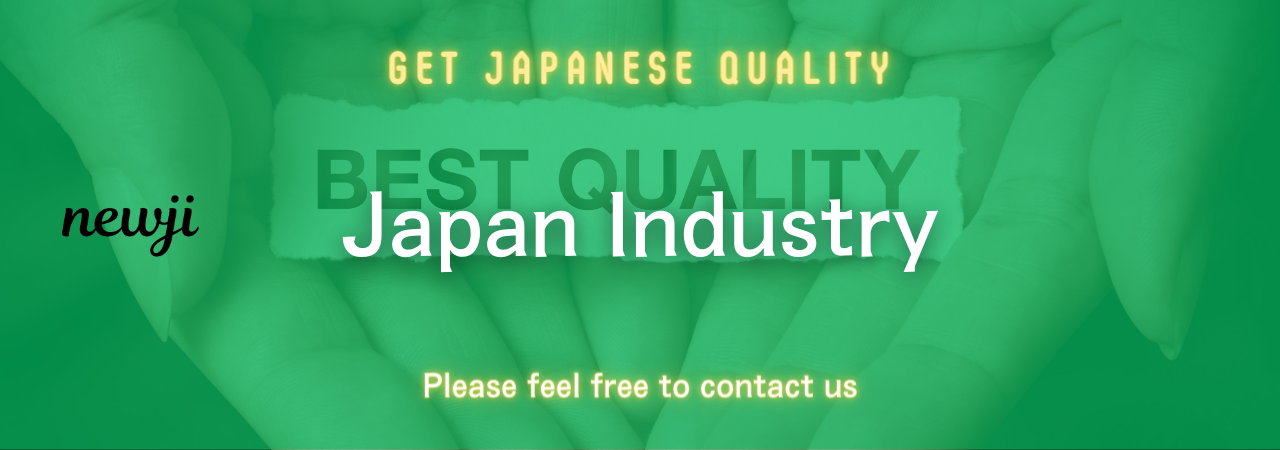
目次
Understanding the Taguchi Method
The Taguchi method, also known as quality engineering, is a cornerstone in manufacturing and production that seeks to enhance product quality and minimize costs.
Developed by Genichi Taguchi, this approach focuses on designing robust processes that remain consistent despite external and internal variations.
It emphasizes the importance of reducing variability in products rather than merely conducting quality tests post-production.
At its core, the Taguchi method utilizes statistical techniques to determine factors that have the most significant effect on a particular process or product.
This systematic approach allows manufacturers to identify and control the variables that could lead to defects or quality issues.
By proactively addressing these variables, companies can prevent market quality problems and achieve cost savings.
Benefits of Implementing the Taguchi Method
There are numerous benefits to applying the Taguchi method in manufacturing processes.
Firstly, it significantly reduces the cost of production by minimizing the risk of defects and rework.
By focusing on improving quality from the onset, businesses can save on expenses that would otherwise be incurred from fixing issues post-production.
Another significant benefit is improved customer satisfaction.
Products manufactured through the Taguchi method tend to be more reliable and of higher quality, which enhances the consumer’s experience and trust in the brand.
This reliability inevitably leads to reduced warranty claims and returns, further cutting down costs for the producer.
Additionally, the Taguchi method encourages innovation and continuous improvement.
By constantly analyzing processes and experimenting with different variables, companies foster a culture of learning and improvement.
This proactive approach not only improves current processes but can also lead to the discovery of novel production techniques or product improvements.
Key Principles of the Taguchi Method
The Taguchi method is grounded in several key principles that guide its application in quality engineering.
1. Robust Design
The first principle is robust design, which aims to create products and processes that are minimally affected by variability.
This involves understanding the variations that can impact the performance and quality of the product and designing processes that remain stable under these conditions.
Robust design also considers the end-user environment to ensure that products perform consistently in real-world scenarios.
2. Orthogonal Arrays
The use of orthogonal arrays is another critical component.
These arrays are a statistical method used to study a large number of variables with a minimal number of experiments.
They help in efficiently assessing the impact of different factors on the production process, saving time and resources.
3. Loss Function
Taguchi introduced the concept of the loss function to quantify the cost of deviating from the target value.
This function helps manufacturers evaluate how deviations from the desired product quality impact both the producer and the consumer.
The objective is to minimize this loss through process improvements and quality enhancements.
Applying the Taguchi Method in Industry
The application of the Taguchi method spans various industries, from automotive to electronics and everything in between.
To successfully implement this approach, companies generally follow a series of steps:
Step 1: Define the Problem
The first step is to clearly identify the quality problem or the process that needs improvement.
This involves setting specific goals for what is considered an acceptable level of performance or quality.
Step 2: Identify Variables
Next, identify the variables or factors that could potentially influence the process or product quality.
This step often involves brainstorming sessions and consultations with experts from different areas of the production line.
Step 3: Conduct Experiments
Using orthogonal arrays, conduct controlled experiments to test different combinations of variables.
These experiments will reveal which factors have the most substantial impact on quality.
Step 4: Analyze Results
Analyze the data collected from the experiments and use the insights to make decisions about process modifications.
This step often involves statistical analysis to determine the optimal settings for the factors tested.
Step 5: Implement Changes
After determining the best configuration, implement these changes in the production process.
It’s crucial to ensure all team members are trained and informed about the new processes.
Step 6: Monitor Performance
Finally, continuously monitor the performance of the process to ensure it remains stable over time.
This ongoing review helps in quickly identifying any new sources of variation and addressing them before they lead to quality problems.
Conclusion
The Taguchi method is a powerful tool for improving product quality and reducing manufacturing costs.
By focusing on robust design and minimizing variability, companies can prevent quality issues from reaching the consumer market.
The systematic approach of using orthogonal arrays and loss functions guides manufacturers in optimizing their processes for consistent and high-quality production.
As industries continue to face competition and the need for efficient resource utilization, the adoption of the Taguchi method could provide a competitive edge in quality management and cost reduction.
Implementing this method requires a commitment to detail and a culture focused on continuous improvement, but the long-term benefits to both businesses and consumers make it an investment well worth considering.
資料ダウンロード
QCD管理受発注クラウド「newji」は、受発注部門で必要なQCD管理全てを備えた、現場特化型兼クラウド型の今世紀最高の受発注管理システムとなります。
ユーザー登録
受発注業務の効率化だけでなく、システムを導入することで、コスト削減や製品・資材のステータス可視化のほか、属人化していた受発注情報の共有化による内部不正防止や統制にも役立ちます。
NEWJI DX
製造業に特化したデジタルトランスフォーメーション(DX)の実現を目指す請負開発型のコンサルティングサービスです。AI、iPaaS、および先端の技術を駆使して、製造プロセスの効率化、業務効率化、チームワーク強化、コスト削減、品質向上を実現します。このサービスは、製造業の課題を深く理解し、それに対する最適なデジタルソリューションを提供することで、企業が持続的な成長とイノベーションを達成できるようサポートします。
製造業ニュース解説
製造業、主に購買・調達部門にお勤めの方々に向けた情報を配信しております。
新任の方やベテランの方、管理職を対象とした幅広いコンテンツをご用意しております。
お問い合わせ
コストダウンが利益に直結する術だと理解していても、なかなか前に進めることができない状況。そんな時は、newjiのコストダウン自動化機能で大きく利益貢献しよう!
(β版非公開)