- お役立ち記事
- Application to reaction engineering
Application to reaction engineering
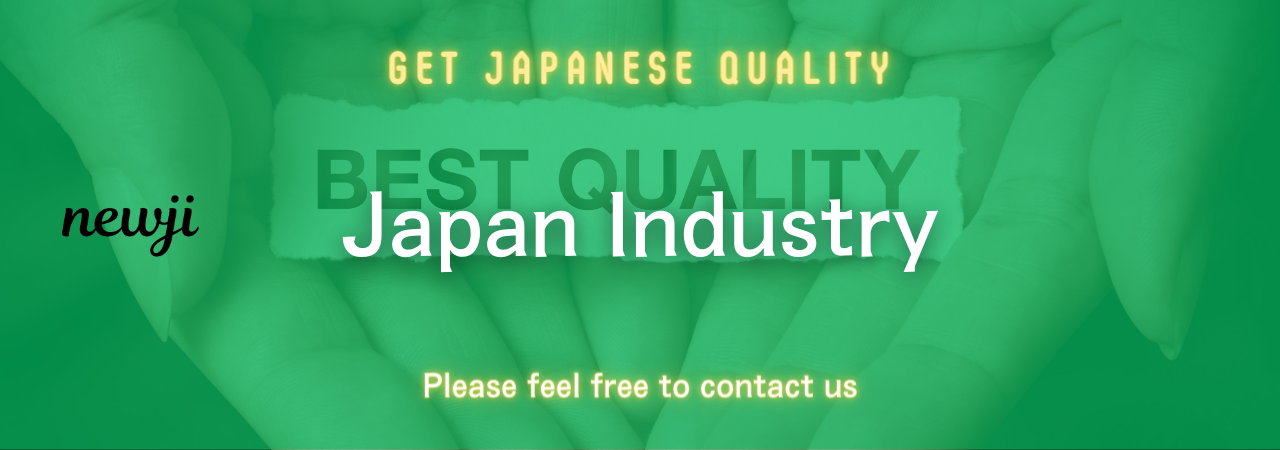
目次
Introduction to Reaction Engineering
Reaction engineering is a fascinating field of chemical engineering dedicated to understanding and designing processes where chemical reactions are critical.
It bridges the gap between the unique properties of individual chemicals and the many applications they enable in practical industry.
Understanding the fundamentals of reaction engineering is essential for anyone interested in pursuing a career in chemical engineering or related fields.
The Basics of Chemical Reactions
Chemical reactions are processes where substances, known as reactants, transform into different substances, called products.
These reactions are characterized by changes in the chemical composition, often accompanied by energy changes in the form of heat, light, or sound.
Understanding how and why these reactions occur is paramount for reaction engineers.
They must consider factors such as reaction kinetics, equilibrium, and thermodynamics to design efficient systems.
Reaction Kinetics
Reaction kinetics deals with understanding the speed or rate at which chemical reactions proceed.
The rate depends on various factors, including temperature, pressure, concentration of reactants, and the presence of catalysts.
In reaction engineering, being able to predict reaction rates is crucial for designing reactors that operate efficiently under specific conditions.
Reaction Equilibrium
Equilibrium in chemical reactions refers to the state where the rate of the forward reaction equals the rate of the reverse reaction, leading to no net change in the concentration of reactants and products.
This concept is crucial for understanding how reactions can be driven to completion or maintain particular product concentrations.
Reaction engineers use this knowledge to manipulate conditions to favor desired outcomes.
Types of Reactors and Their Applications
Different types of reactors are used in reaction engineering, each tailored for specific kinds of reactions and processes.
Knowing which reactor type to choose is an essential decision for engineers to ensure optimal performance and efficiency.
Batch Reactors
Batch reactors are commonly used for liquid-phase reactions.
In these reactors, reactants are loaded, the reaction proceeds for a certain time, and then the products are removed.
Batch reactors are particularly suitable for small-scale production, pharmaceutical industries, and processes requiring high levels of purity.
Continuous Stirred Tank Reactors (CSTR)
CSTRs are ideal for continuous processes where reactants are continuously added while products are continuously removed.
This type of reactor ensures a steady state, making it effective for reactions that need consistent conditions over time.
CSTRs are widely used in industries like chemicals and petrochemicals.
Plug Flow Reactors (PFR)
In PFRs, reactants flow through a cylindrical pipe, and the reaction takes place as they move.
This kind of reactor allows for a high conversion per unit volume and is preferred for exothermic reactions.
The plug flow design is common in industries that require large-scale production, such as oil refineries.
The Role of Reaction Catalysts
Catalysts play a pivotal role in reaction engineering by increasing the rate of reactions without being consumed.
They provide an alternative reaction pathway with a lower activation energy.
Understanding the role of catalysts allows engineers to enhance process efficiency and selectivity.
Homogeneous Catalysts
Homogeneous catalysts exist in the same phase as the reactants, usually in a liquid form.
They offer the advantage of easy mixing and uniformity, leading to higher reaction rates in certain processes.
However, separation of catalysts from the product can be challenging.
Heterogeneous Catalysts
Heterogeneous catalysts exist in a different phase than the reactants, often solid catalysts in liquid or gas reactions.
They are prevalent in industries due to their ease of separation and recyclability.
The surface properties of these catalysts are crucial for maximizing reaction efficiency.
Applications of Reaction Engineering
Reaction engineering underpins many crucial industrial processes, driving innovation and efficiency across various sectors.
Petrochemical Industry
In the petrochemical industry, reaction engineering facilitates the conversion of natural resources like crude oil and natural gas into valuable chemical products such as fuels, plastics, and fertilizers.
These processes often involve complex reaction pathways requiring precise control and optimization.
Pharmaceutical Manufacturing
The pharmaceutical sector heavily relies on reaction engineering to produce active pharmaceutical ingredients (APIs).
Precise control over reaction conditions ensures the purity and efficacy of drugs.
Batch reactors are often used to accommodate the stringent regulatory requirements in this industry.
Environmental Engineering
Reaction engineering is vital for environmental applications, including waste treatment and pollution control.
It helps in designing processes that convert pollutants into harmless or less harmful substances.
The development of catalytic converters in vehicles is a practical example of its application.
Food Processing
In the food industry, reaction engineering aids in developing processes like fermentation, pasteurization, and hydrogenation.
These reactions are pivotal for producing and preserving food products with desired characteristics and shelf life.
Conclusion
Reaction engineering is an integral part of chemical engineering, essential for the development and optimization of processes in various industries.
By understanding reaction kinetics, equilibrium, and the role of catalysts, engineers can design efficient systems to meet the growing demands of modern society.
Whether in energy production, pharmaceuticals, or environmental solutions, reaction engineering is a field that shapes the world we live in today.
資料ダウンロード
QCD調達購買管理クラウド「newji」は、調達購買部門で必要なQCD管理全てを備えた、現場特化型兼クラウド型の今世紀最高の購買管理システムとなります。
ユーザー登録
調達購買業務の効率化だけでなく、システムを導入することで、コスト削減や製品・資材のステータス可視化のほか、属人化していた購買情報の共有化による内部不正防止や統制にも役立ちます。
NEWJI DX
製造業に特化したデジタルトランスフォーメーション(DX)の実現を目指す請負開発型のコンサルティングサービスです。AI、iPaaS、および先端の技術を駆使して、製造プロセスの効率化、業務効率化、チームワーク強化、コスト削減、品質向上を実現します。このサービスは、製造業の課題を深く理解し、それに対する最適なデジタルソリューションを提供することで、企業が持続的な成長とイノベーションを達成できるようサポートします。
オンライン講座
製造業、主に購買・調達部門にお勤めの方々に向けた情報を配信しております。
新任の方やベテランの方、管理職を対象とした幅広いコンテンツをご用意しております。
お問い合わせ
コストダウンが利益に直結する術だと理解していても、なかなか前に進めることができない状況。そんな時は、newjiのコストダウン自動化機能で大きく利益貢献しよう!
(Β版非公開)