- お役立ち記事
- Application to reliability prediction and life estimation of electronic devices and its key points
月間77,185名の
製造業ご担当者様が閲覧しています*
*2025年2月28日現在のGoogle Analyticsのデータより
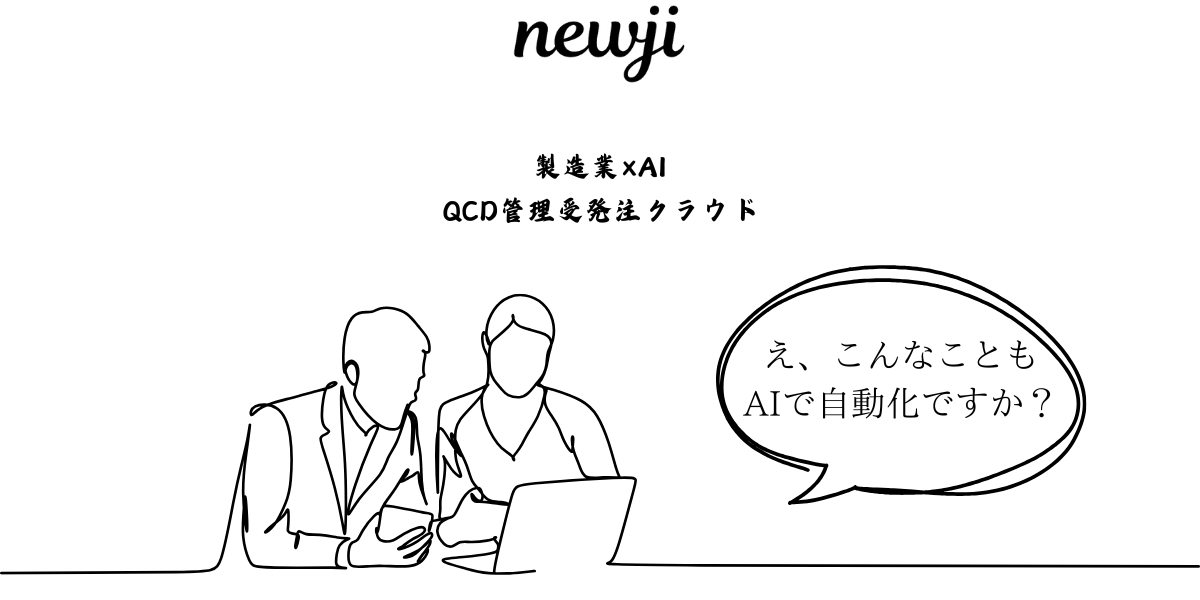
Application to reliability prediction and life estimation of electronic devices and its key points
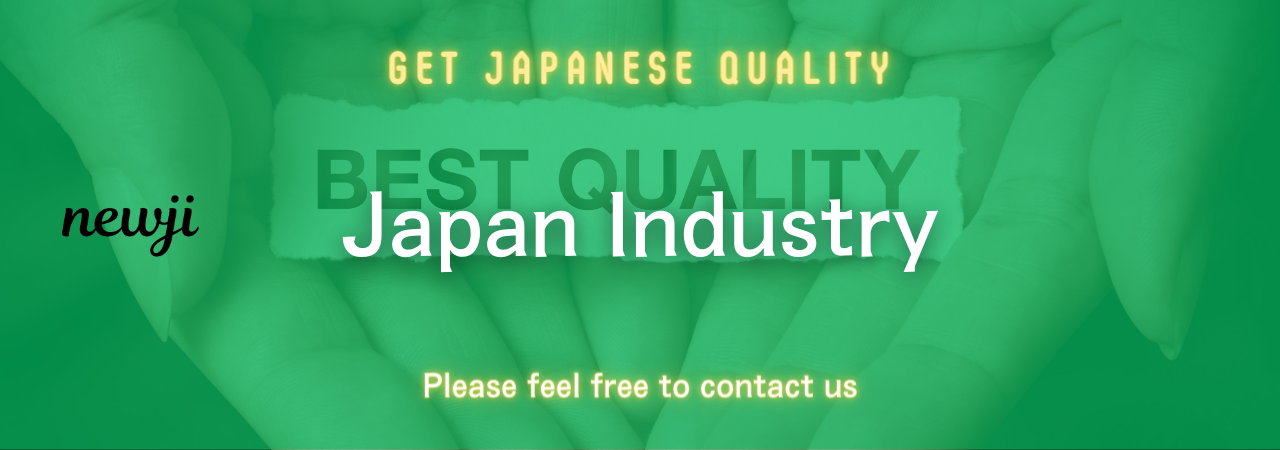
目次
Understanding the Importance of Reliability Prediction in Electronics
In today’s world, electronic devices are a crucial part of our everyday lives.
From smartphones to televisions, and even kitchen appliances, electronics have made life more convenient and efficient.
However, with their increasing use comes the responsibility of ensuring these devices are reliable and have a predictable lifespan.
Reliability prediction and life estimation of electronic devices are critical for manufacturers and consumers alike.
Manufacturers need to ensure their products meet quality standards and possess durability that satisfies consumer expectations.
Consumers, on the other hand, need reliable products that justify their investment and serve their needs effectively over time.
Key Concepts in Reliability Prediction
Reliability prediction involves scientific assessments and statistical analysis used to determine how long an electronic device is expected to function under normal conditions.
Several factors influence this prediction, including material quality, manufacturing processes, and environmental conditions.
By understanding these factors, manufacturers can anticipate potential faults and design products that minimize failures.
The life estimation process uses historical data and testing to forecast the service life of a product.
It involves rigorous testing under various conditions to simulate real-world usage and anticipate wear and tear.
These tests provide vital data that helps manufacturers improve design and manufacturing processes to enhance the reliability of their devices.
Methods of Reliability Prediction
Reliability prediction methods vary based on the complexity of the devices and the resources available.
Some of the most common techniques include:
1. Empirical Methods
These methods rely on historical data and observed failure rates to predict the lifespan of new devices.
By studying past performance, manufacturers can infer patterns and apply this knowledge to new models.
While empirical methods are straightforward, their accuracy heavily relies on the quality and volume of available data.
2. Physics of Failure (PoF)
The PoF approach examines the physical processes that might lead to device failures.
By understanding the underlying causes, such as thermal stress or material fatigue, engineers can identify the weakest links in a device’s design.
This method provides detailed insights but requires a deep understanding of material science and engineering principles.
3. Statistical Models
Statistical models, such as Weibull analysis or Monte Carlo simulations, utilize mathematical computations to predict device reliability.
These models can handle complex data sets and provide probabilities of failure and expected lifespan.
While powerful, they require expertise in statistical analysis to interpret the results accurately.
Life Estimation and Testing
To ensure reliability predictions are accurate, life estimation tests are essential.
These tests can be divided into several categories:
1. Accelerated Life Testing (ALT)
This method subjects devices to stress conditions beyond normal use to hasten the wear and failure process.
By pushing a device to its limits, manufacturers can gather data on how it performs under extremes and use this to predict its behavior over time.
2. Environmental Testing
Devices are tested under various environmental conditions such as temperature fluctuations, humidity, and vibration.
These factors are critical as they reflect the real-world scenarios that a device might encounter.
Testing under these conditions ensures the product’s durability in diverse environments.
3. Burn-In Testing
Here, devices are used continuously for a set period to expose early-life failures.
This process identifies defects that might not be visible initially but could emerge during normal usage over time.
Burn-in testing helps weed out unreliable units before they reach consumers.
Key Points for Applying Reliability Predictions
When applying reliability prediction and life estimation in electronics, certain key points need consideration:
1. Comprehensive Data Collection
Reliable predictions heavily depend on data quality.
Ensure robust data collection during design, production, and testing phases to build a comprehensive database that strengthens future predictions.
2. Continuous Monitoring and Feedback
Monitor products after they are released into the market.
Collect feedback from real-world usage to refine predictive models and improve future designs.
This ongoing process helps manufacturers adapt to emerging patterns and technological advancements.
3. Collaboration Across Teams
Predictive reliability strategies require input from various teams, including design, engineering, quality assurance, and logistics.
Effective collaboration ensures all perspectives are considered, leading to more accurate and useful predictions.
4. Incorporation of Advanced Technologies
Utilize advanced technologies like AI and machine learning to enhance prediction accuracy.
These technologies can process vast amounts of data, identify underlying patterns, and provide more precise forecasts than traditional methods.
Conclusion
Reliability prediction and life estimation are vital components in the design and manufacturing of electronic devices.
By applying robust prediction methods and conducting thorough life tests, manufacturers can ensure their products are durable and meet consumer expectations.
Consumers benefit through access to reliable and long-lasting electronics.
Adapting to technological advancements and continuously refining predictive models will further enhance the reliability of electronic devices, ultimately leading to better products and satisfied customers.
資料ダウンロード
QCD管理受発注クラウド「newji」は、受発注部門で必要なQCD管理全てを備えた、現場特化型兼クラウド型の今世紀最高の受発注管理システムとなります。
ユーザー登録
受発注業務の効率化だけでなく、システムを導入することで、コスト削減や製品・資材のステータス可視化のほか、属人化していた受発注情報の共有化による内部不正防止や統制にも役立ちます。
NEWJI DX
製造業に特化したデジタルトランスフォーメーション(DX)の実現を目指す請負開発型のコンサルティングサービスです。AI、iPaaS、および先端の技術を駆使して、製造プロセスの効率化、業務効率化、チームワーク強化、コスト削減、品質向上を実現します。このサービスは、製造業の課題を深く理解し、それに対する最適なデジタルソリューションを提供することで、企業が持続的な成長とイノベーションを達成できるようサポートします。
製造業ニュース解説
製造業、主に購買・調達部門にお勤めの方々に向けた情報を配信しております。
新任の方やベテランの方、管理職を対象とした幅広いコンテンツをご用意しております。
お問い合わせ
コストダウンが利益に直結する術だと理解していても、なかなか前に進めることができない状況。そんな時は、newjiのコストダウン自動化機能で大きく利益貢献しよう!
(β版非公開)