- お役立ち記事
- Applications and Future of Digital Twin Technology in Production Machinery
月間76,176名の
製造業ご担当者様が閲覧しています*
*2025年3月31日現在のGoogle Analyticsのデータより
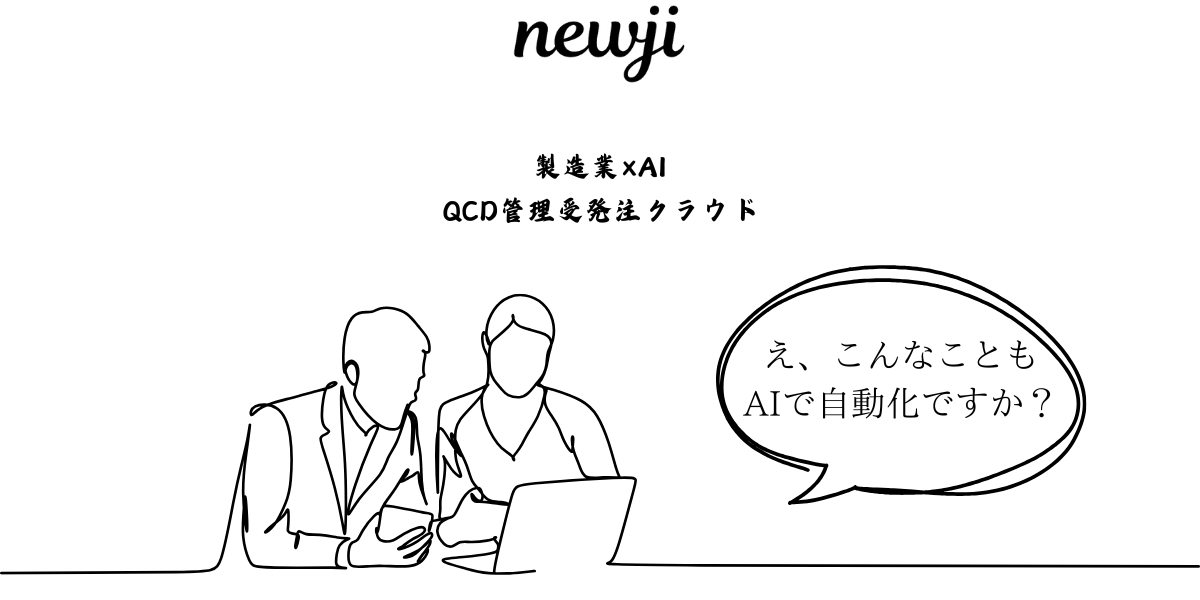
Applications and Future of Digital Twin Technology in Production Machinery
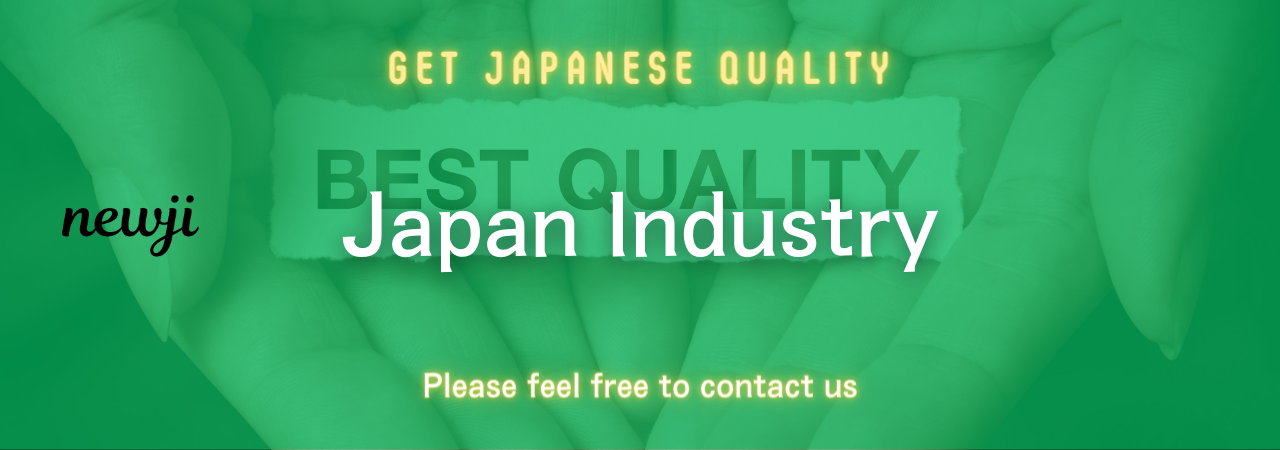
目次
Understanding Digital Twin Technology
Digital twin technology is an innovative concept that creates a virtual model of a physical object, system, or process.
In the realm of production machinery, this technology offers unprecedented opportunities for efficiency and innovation.
A digital twin is essentially a digital replica that reflects every aspect of a real-world asset, enabling manufacturers to monitor, analyze, and optimize machinery performance in real-time.
This technology provides valuable insights by utilizing data from IoT sensors, advanced software, and machine learning.
It allows manufacturers to not only simulate and predict potential issues but also make informed decisions to enhance operation and productivity.
Applications in Production Machinery
Digital twin technology has a multitude of applications in the world of production machinery.
The use of this advanced technology can transform traditional manufacturing processes by driving improvements in several key areas.
Predictive Maintenance
One of the most significant applications of digital twin technology is predictive maintenance.
By creating a digital replica of machinery, manufacturers can monitor the health and condition of equipment in real-time.
This approach allows for early detection of potential issues, minimizing downtime, and reducing maintenance costs.
Predictive maintenance using digital twins involves analyzing data from sensors to predict when a component might fail or require servicing.
This preemptive strategy means production lines can continue running smoothly without unexpected interruptions.
Performance Optimization
Digital twins provide insights into the performance of machinery, enabling manufacturers to identify bottlenecks and optimize processes.
By simulating different scenarios, they can experiment with ways to improve efficiency, reduce energy consumption, and increase throughput.
This iterative approach ensures that machinery is operating at its optimal capacity, supporting higher productivity and cost savings.
Product Design and Development
Incorporating digital twin technology into the product design and development phase can significantly reduce time and costs associated with bringing a new product to market.
By simulating real-world conditions virtually, designers can test and refine prototypes without the need for physical trials.
This not only expedites the design process but also reduces the risk of errors and enhances the final product quality.
Quality Control and Assurance
Digital twins can enhance quality control processes by providing manufacturers with real-time data on production environments.
They can track and analyze parameters such as temperature, humidity, and other environmental factors that affect product quality.
This data-driven approach ensures that products meet the highest standards before reaching the market, thereby boosting customer satisfaction and brand loyalty.
Future Prospects of Digital Twin Technology
The future of digital twin technology in production machinery is promising, with developments continuously emerging in this fast-evolving field.
Here are some potential trends and advancements that could shape the future landscape.
Integration with Artificial Intelligence and Machine Learning
As AI and machine learning technologies progress, they are expected to play a crucial role in enhancing digital twin capabilities.
Integrating AI can provide more accurate predictions and insights, automating decision-making processes and further optimizing machinery performance.
Increased Interconnectivity with Industry 4.0
Digital twins are a cornerstone of Industry 4.0, facilitating smarter and more interconnected manufacturing ecosystems.
The ability to connect various components of the production environment allows for seamless communication and more efficient operations.
Advanced data analytics and interconnected machinery will lead to better supply chain management and resource allocation.
Expanding IoT Development
The growth of IoT will significantly impact digital twin technology, enabling even more complex and detailed simulations of production machinery.
With more connected devices, manufacturers can gather richer datasets, resulting in more precise analyses and improvements in production processes.
Sustainability and Environmental Impact
Adopting digital twin technology can contribute to more sustainable manufacturing practices.
By optimizing machinery operations and reducing waste, manufacturers can lessen their environmental footprint.
This aligns with global efforts to drive sustainable industrialization and promote responsible consumption and production.
Challenges and Considerations
While digital twin technology offers immense potential, there are still challenges that need to be addressed to unlock its full capabilities.
Data Security and Privacy
The implementation of digital twin technology necessitates robust cybersecurity measures to protect valuable data from breaches.
Ensuring data privacy is crucial, especially as more sensitive information is collected and analyzed.
Skilled Workforce
The successful integration of digital twin technology requires a workforce adept in digital skills, data analysis, and machine learning.
Investing in employee training and development is essential to leverage this technology effectively.
High Initial Investment
The cost of implementing digital twin technology can be high, which might deter some manufacturers from adopting it.
However, the long-term benefits in efficiency and productivity can outweigh the initial expenditure, making it a worthwhile investment.
Conclusion
Digital twin technology is revolutionizing production machinery, offering innovative solutions for optimization, maintenance, and quality assurance.
As this technology continues to advance, it holds transformative potential for the manufacturing industry and beyond.
With its integration into Industry 4.0 and advancements in AI and IoT, the possibilities are vast and exciting.
Embracing these changes can lead to more efficient, sustainable, and competitive manufacturing processes.
資料ダウンロード
QCD管理受発注クラウド「newji」は、受発注部門で必要なQCD管理全てを備えた、現場特化型兼クラウド型の今世紀最高の受発注管理システムとなります。
ユーザー登録
受発注業務の効率化だけでなく、システムを導入することで、コスト削減や製品・資材のステータス可視化のほか、属人化していた受発注情報の共有化による内部不正防止や統制にも役立ちます。
NEWJI DX
製造業に特化したデジタルトランスフォーメーション(DX)の実現を目指す請負開発型のコンサルティングサービスです。AI、iPaaS、および先端の技術を駆使して、製造プロセスの効率化、業務効率化、チームワーク強化、コスト削減、品質向上を実現します。このサービスは、製造業の課題を深く理解し、それに対する最適なデジタルソリューションを提供することで、企業が持続的な成長とイノベーションを達成できるようサポートします。
製造業ニュース解説
製造業、主に購買・調達部門にお勤めの方々に向けた情報を配信しております。
新任の方やベテランの方、管理職を対象とした幅広いコンテンツをご用意しております。
お問い合わせ
コストダウンが利益に直結する術だと理解していても、なかなか前に進めることができない状況。そんな時は、newjiのコストダウン自動化機能で大きく利益貢献しよう!
(β版非公開)