- お役立ち記事
- Applying FMEA (Failure Mode and Effects Analysis) to Prevent Quality Issues in Manufacturing
月間76,176名の
製造業ご担当者様が閲覧しています*
*2025年3月31日現在のGoogle Analyticsのデータより
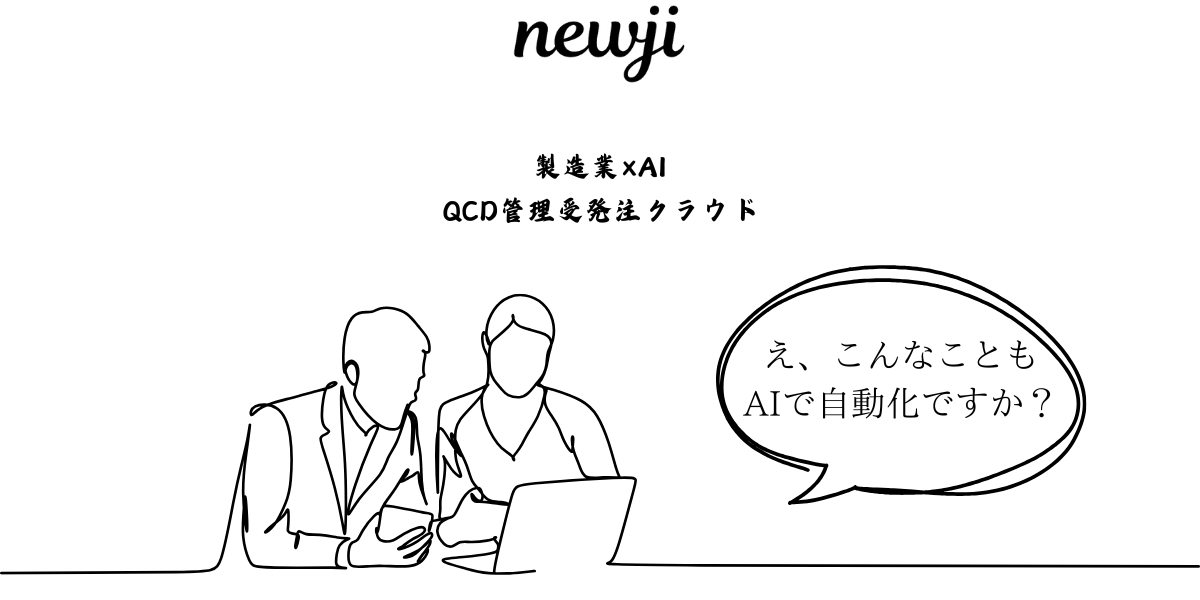
Applying FMEA (Failure Mode and Effects Analysis) to Prevent Quality Issues in Manufacturing
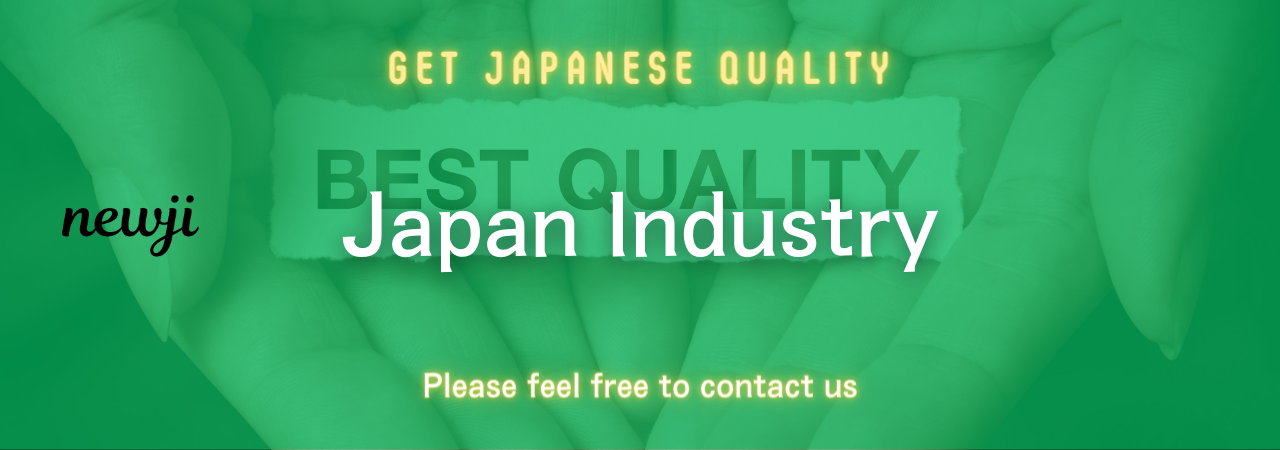
In the dynamic world of manufacturing, ensuring product quality is paramount. A single defect can lead to a ripple effect of issues, harming brand reputation and financial health. One effective tool to prevent these quality issues is FMEA, or Failure Mode and Effects Analysis. This blog post explores how to apply FMEA to safeguard the integrity of manufacturing processes.
目次
What is FMEA?
Failure Mode and Effects Analysis, or FMEA, is a systematic method used to identify potential failures within a process or product. The primary goal of FMEA is to pinpoint which failures are most likely to occur and what their impacts would be. Understanding these can guide strict preventive measures.
Types of FMEA
There are two main types of FMEA:
1. **Design FMEA (DFMEA):** Focuses on identifying and mitigating potential failures in product design.
2. **Process FMEA (PFMEA):** Concentrates on failures that may arise during the manufacturing process.
The Steps in FMEA
Let’s break down the FMEA process into manageable steps to understand its application better.
1. Define the Scope
The first crucial step in an FMEA process is to define the boundaries.
Identify the system, subsystem, or component for which the analysis will be conducted.
Clearly outline what parts of the manufacturing process will be scrutinized.
2. Assemble the Team
FMEA isn’t a solo task.
It requires a cross-functional team composed of individuals from different departments such as design, manufacturing, and quality control.
A diverse team ensures that multiple perspectives are considered, which enriches the analysis.
3. Identify Potential Failure Modes
Brainstorm all possible ways a component or process could fail.
Use historical data, design reviews, and team expertise to identify these potential failure modes.
Document them meticulously to ensure nothing is overlooked.
4. Determine the Effects of Each Failure Mode
Once potential failures are identified, the next step is to understand their effects.
What happens when a failure occurs?
Does it cause minor inconvenience, or does it lead to catastrophic failure?
Assessing this helps prioritize which failures need the most urgent attention.
5. Assign Severity, Occurrence, and Detection Ratings
For each potential failure, assign:
– **Severity (S):** How serious is the effect of the failure?
– **Occurrence (O):** How likely is the failure to happen?
– **Detection (D):** How likely is it that the failure will be detected before it causes harm?
Ratings typically range from 1 to 10, with higher numbers indicating greater severity, higher occurrence probability, or a less likely chance of detection.
6. Calculate the Risk Priority Number (RPN)
The RPN helps prioritize failures based on their ratings. Calculate it by multiplying Severity, Occurrence, and Detection (RPN = S x O x D).
The higher the RPN, the greater the risk that needs to be addressed.
7. Develop Action Plans
For failures with high RPNs, develop action plans to mitigate these risks.
This could involve redesigning the product, changing materials, modifying the manufacturing process, or enhancing quality checks.
Assign responsibility for these actions to team members and set deadlines for completion.
8. Implement and Review
Finally, implement the action plans and review their effectiveness.
Monitor the process to ensure that the risks have indeed been mitigated as planned.
Regular updates and periodic reviews of the FMEA are essential to adapt to any new risks that may arise.
The Benefits of Applying FMEA
Leveraging FMEA in manufacturing processes offers numerous benefits:
Improved Product Quality
By identifying potential issues before they occur, manufacturers can take preventive measures to ensure the final product meets quality standards.
This proactive approach reduces the likelihood of defects and rework, leading to higher customer satisfaction.
Enhanced Safety
Focusing on failure modes helps identify weak points that could compromise safety.
Addressing these issues ensures a safer work environment and reduces the risk of accidents.
Cost Savings
Proactively identifying and addressing potential failures can save significant costs related to rework, scrap, and warranty claims.
Preventive measures are generally less costly than corrective actions taken after failures occur.
Common Challenges in Implementing FMEA
Despite its benefits, implementing FMEA can come with challenges.
Time-Consuming
Conducting a thorough FMEA can be time-consuming, especially for complex systems or processes.
However, the initial time investment is usually justified by the long-term benefits.
Requires Expertise
FMEA requires a detailed understanding of both the product and the manufacturing process.
Assembling a knowledgeable team is crucial but can sometimes be difficult if expertise is limited.
Conclusion
Implementing FMEA in manufacturing processes is a proactive approach to ensuring product quality and reliability.
By following a structured methodology, manufacturers can identify potential failure modes, understand their impacts, and take appropriate actions to prevent them.
The benefits of improved product quality, enhanced safety, and cost savings far outweigh the challenges of implementation.
In the end, FMEA serves as a critical tool for manufacturers dedicated to delivering high-quality products and maintaining a competitive edge in the market.
資料ダウンロード
QCD管理受発注クラウド「newji」は、受発注部門で必要なQCD管理全てを備えた、現場特化型兼クラウド型の今世紀最高の受発注管理システムとなります。
ユーザー登録
受発注業務の効率化だけでなく、システムを導入することで、コスト削減や製品・資材のステータス可視化のほか、属人化していた受発注情報の共有化による内部不正防止や統制にも役立ちます。
NEWJI DX
製造業に特化したデジタルトランスフォーメーション(DX)の実現を目指す請負開発型のコンサルティングサービスです。AI、iPaaS、および先端の技術を駆使して、製造プロセスの効率化、業務効率化、チームワーク強化、コスト削減、品質向上を実現します。このサービスは、製造業の課題を深く理解し、それに対する最適なデジタルソリューションを提供することで、企業が持続的な成長とイノベーションを達成できるようサポートします。
製造業ニュース解説
製造業、主に購買・調達部門にお勤めの方々に向けた情報を配信しております。
新任の方やベテランの方、管理職を対象とした幅広いコンテンツをご用意しております。
お問い合わせ
コストダウンが利益に直結する術だと理解していても、なかなか前に進めることができない状況。そんな時は、newjiのコストダウン自動化機能で大きく利益貢献しよう!
(β版非公開)