- お役立ち記事
- Applying Six Sigma in Quality Assurance for Manufacturing: Implementation and Results
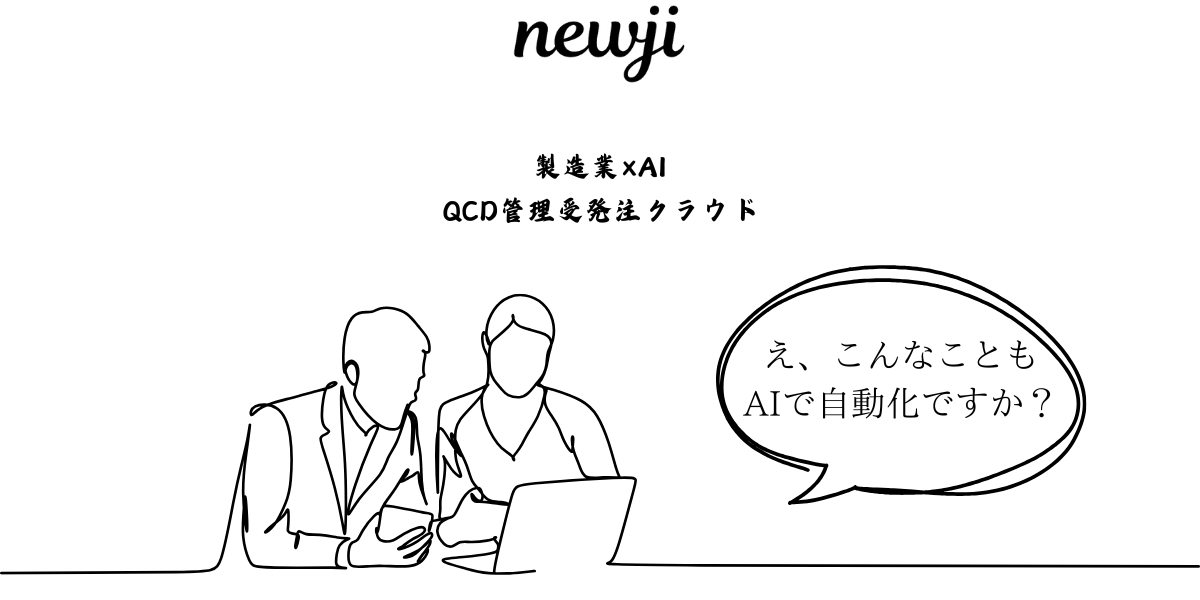
Applying Six Sigma in Quality Assurance for Manufacturing: Implementation and Results
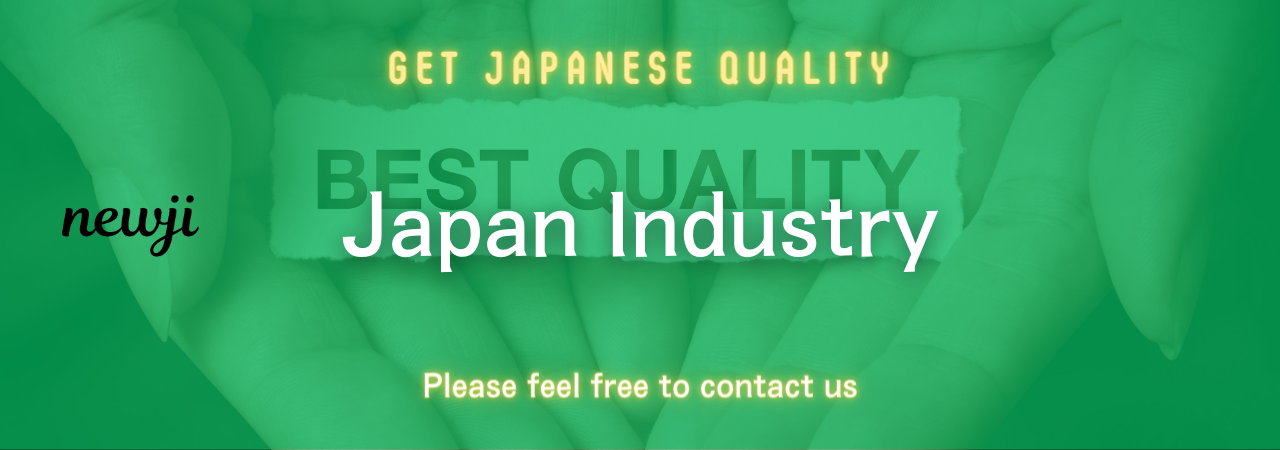
Six Sigma is a methodology used by businesses to improve process efficiency and quality.
When applied to manufacturing, it helps companies reduce defects and maximize product quality.
In this article, we will explore how Six Sigma can be implemented in quality assurance for manufacturing and examine the results of such implementation.
目次
Introduction to Six Sigma in Manufacturing
Six Sigma is a set of techniques and tools designed to improve processes by identifying and removing the causes of defects and minimizing variability in manufacturing and business processes.
It uses statistical methods to identify where and how errors are made and then takes steps to improve the process.
The name “Six Sigma” comes from the statistical concept of standard deviation, with six sigma indicating a process that is nearly free of defects.
In manufacturing, this translates to fewer defective products and more consistent quality.
Key Principles of Six Sigma
Several principles form the foundation of Six Sigma.
Customer Focus
At the core of Six Sigma is the principle of putting the customer first.
Understanding customer needs and expectations is essential.
Once these are identified, processes can be tailored to meet or exceed those expectations, leading to higher satisfaction and loyalty.
Data-Driven Decision Making
Six Sigma relies heavily on data.
By collecting and analyzing data, businesses can make informed decisions about process improvements.
Data provides insights into where problems are occurring and how they can be fixed.
Process Improvement
The aim of Six Sigma is continuous process improvement.
This involves constantly monitoring processes and making incremental changes to enhance quality and efficiency.
Steps for Implementing Six Sigma in Manufacturing
Embedding Six Sigma into a manufacturing process involves a structured approach.
This usually follows the DMAIC cycle: Define, Measure, Analyze, Improve, and Control.
Define
The first step is to define the problem clearly.
A project charter is created to outline the scope, goals, and participants.
Understanding the problem helps to focus efforts and resources effectively.
Measure
Accurate measurement is crucial in Six Sigma.
Data is collected on current processes to establish a baseline.
This data helps in understanding the extent of the problem and sets a benchmark against which improvements will be measured.
Analyze
Once data is collected, it’s analyzed to identify the root causes of defects.
Various tools such as cause-and-effect diagrams, Pareto charts, and histograms can be used for this analysis.
Improve
After identifying the root causes, solutions are developed and implemented.
These solutions aim to eliminate the root causes of defects.
Pilot testing the solutions on a small scale before full implementation is a good practice to ensure they work as intended.
Control
To maintain improvements, control mechanisms are put in place.
This could include regular monitoring, standard operating procedures, and training programs for employees.
Consistent control ensures that the process remains optimized and any deviations are quickly addressed.
Benefits of Six Sigma in Manufacturing
Implementing Six Sigma in manufacturing can lead to significant benefits.
Reduced Defects
By identifying and eliminating the root causes of defects, companies can reduce the number of defective products.
This leads to higher-quality products and fewer customer complaints.
Increased Efficiency
Six Sigma focuses on improving processes, which can result in increased efficiency.
Streamlined processes often mean faster production times and lower costs.
Cost Savings
With fewer defects, less waste is produced.
This not only saves money on materials but also reduces costs related to rework and repairs.
Improved Customer Satisfaction
Higher quality products and more reliable delivery times lead to greater customer satisfaction.
Happier customers are more likely to return and recommend the company to others.
Real-World Examples of Six Sigma in Manufacturing
Let’s look at how some companies have successfully implemented Six Sigma in their manufacturing processes.
General Electric
General Electric (GE) is one of the most notable examples of a company that has successfully used Six Sigma.
By applying Six Sigma, GE was able to save billions of dollars.
They used the DMAIC process to reduce defects and improve efficiency across multiple divisions.
Motorola
Motorola developed Six Sigma in the 1980s to reduce defects in its manufacturing processes.
By implementing Six Sigma, Motorola was able to significantly improve product quality and reduce costs.
Their success with Six Sigma has served as a model for other companies to follow.
Honeywell
Honeywell adopted Six Sigma to improve its manufacturing processes and enhance product quality.
The company focused on reducing variation and eliminating waste, resulting in improved efficiency and substantial cost savings.
Challenges and Considerations
While the benefits of Six Sigma are substantial, there are challenges to consider.
Training and Commitment
Successful implementation requires extensive training and a strong commitment from all levels of the organization.
Employees need to understand Six Sigma principles and how to apply them effectively.
Initial Costs
There are initial costs associated with implementing Six Sigma, including training and possibly hiring consultants.
However, these costs are often outweighed by the long-term savings and improvements.
Resistance to Change
Change can be difficult for any organization.
There may be resistance from employees who are accustomed to the old ways of doing things.
Effective communication and involving employees in the process can help mitigate this resistance.
Conclusion
Applying Six Sigma in quality assurance for manufacturing can lead to remarkable improvements in process efficiency and product quality.
By following the DMAIC cycle and focusing on data-driven decision-making and continuous improvement, companies can reduce defects, increase efficiency, and enhance customer satisfaction.
Although there may be challenges, the long-term benefits of Six Sigma make it a worthy investment for any manufacturing company seeking to achieve excellence in quality assurance.
資料ダウンロード
QCD調達購買管理クラウド「newji」は、調達購買部門で必要なQCD管理全てを備えた、現場特化型兼クラウド型の今世紀最高の購買管理システムとなります。
ユーザー登録
調達購買業務の効率化だけでなく、システムを導入することで、コスト削減や製品・資材のステータス可視化のほか、属人化していた購買情報の共有化による内部不正防止や統制にも役立ちます。
NEWJI DX
製造業に特化したデジタルトランスフォーメーション(DX)の実現を目指す請負開発型のコンサルティングサービスです。AI、iPaaS、および先端の技術を駆使して、製造プロセスの効率化、業務効率化、チームワーク強化、コスト削減、品質向上を実現します。このサービスは、製造業の課題を深く理解し、それに対する最適なデジタルソリューションを提供することで、企業が持続的な成長とイノベーションを達成できるようサポートします。
オンライン講座
製造業、主に購買・調達部門にお勤めの方々に向けた情報を配信しております。
新任の方やベテランの方、管理職を対象とした幅広いコンテンツをご用意しております。
お問い合わせ
コストダウンが利益に直結する術だと理解していても、なかなか前に進めることができない状況。そんな時は、newjiのコストダウン自動化機能で大きく利益貢献しよう!
(Β版非公開)