- お役立ち記事
- Approach to reduce design trial and error of prototype parts
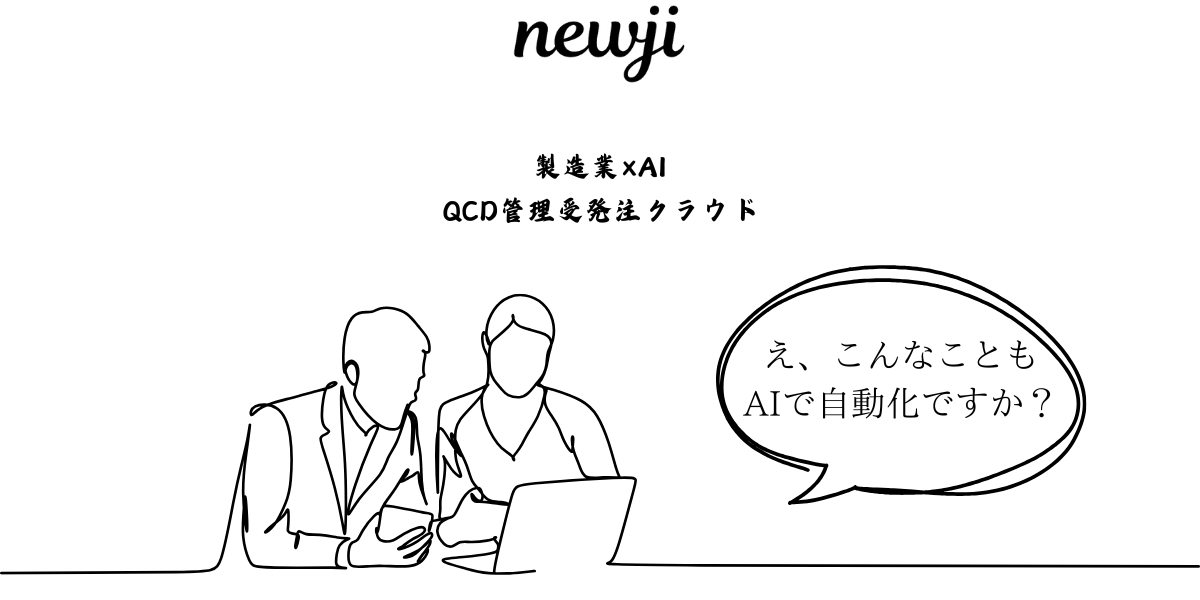
Approach to reduce design trial and error of prototype parts
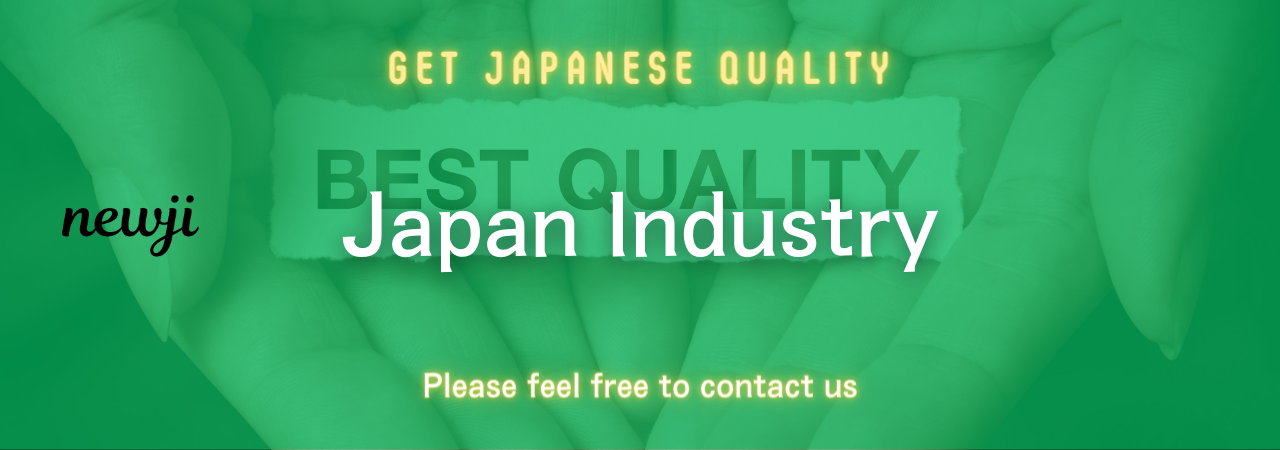
目次
Understanding Prototype Design
Designing prototype parts is a vital stage in product development.
Prototypes serve as preliminary versions of a product that allow designers and engineers to test and refine their ideas.
While this is an indispensable process, it often involves significant trial and error, which can be both time-consuming and costly.
Understanding how to reduce unnecessary trial and error in prototype design is crucial for the efficiency and success of any project.
Initial Research and Planning
One of the most effective ways to minimize trial and error in prototype design is by conducting thorough research and planning upfront.
Before diving into the actual design process, it is important to gather relevant data about the market, target audience, and existing solutions.
This research provides valuable insights into potential pitfalls and helps in making informed decisions.
Effective planning involves setting clear objectives and defining the scope of the prototype.
By identifying the specific functions and requirements of the product early on, designers can focus on the most critical aspects and avoid unnecessary iterations.
Collaboration and Teamwork
Collaborative efforts can significantly reduce the trial-and-error phase in prototype design.
Involving a diverse team of experts from various fields brings different perspectives and expertise to the table.
Engineers, designers, and marketers working together can address potential issues from multiple angles, thereby minimizing mistakes.
Regular team meetings and brainstorming sessions create an environment of open communication and idea exchange.
It encourages team members to share feedback and suggestions, which can lead to innovative solutions and a smoother design process.
Utilizing Advanced Design Tools
The adoption of advanced design software and tools is another effective method to reduce trial and error in prototype development.
Modern CAD (Computer-Aided Design) tools allow designers to create detailed 3D models and simulations of their prototypes.
These digital mockups help in visualizing the final product and identifying design flaws at an early stage.
Simulation tools also enable designers to test various aspects of the prototype, such as its structural integrity, thermal performance, and material properties.
By running virtual tests, many potential issues can be addressed before physical prototypes are ever created, saving both time and resources.
Agile Prototyping Techniques
Incorporating agile principles into the prototyping process can lead to more efficient design iterations.
Agile prototyping encourages rapid development cycles with continuous feedback and iteration.
This approach allows designers to make incremental changes based on real-time feedback rather than waiting until the final design to assess performance.
Using an incremental build-and-test methodology not only speeds up the prototyping process but also fosters innovation.
Designers can experiment with different approaches and learn from small failures, reducing the risk of major setbacks.
Creating Functional and Low-Fidelity Prototypes
Before moving into high-fidelity prototypes, starting with functional or low-fidelity prototypes can be beneficial.
These early-stage models focus on testing core functionalities rather than final aesthetics.
Functional prototypes can be made from simple materials and allow designers to understand the basic functionality of their designs before committing to more expensive versions.
Low-fidelity prototypes can quickly reveal design weaknesses and functionality issues, helping teams to make necessary adjustments.
Refining these versions as they progress reduces the need for major changes later in the design process.
Learning from Past Projects
Taking the time to reflect on past projects and prototypes can provide valuable lessons.
Analyzing previous design processes to identify where the most trial and error occurred helps in developing more efficient strategies in the future.
Design teams should document the trials encountered and their solutions as part of a learning process.
This documentation becomes a reference point for future projects, enabling better risk management and decision-making.
User Feedback and Testing
Gathering user feedback early in the prototype design process can provide critical insights into how the product will be received.
Real users can pinpoint usability issues and offer suggestions that might not be evident to the design team.
This feedback loop encourages iterative improvements based on actual user experiences rather than assumptions.
Testing prototypes with real-world users ensures that design decisions are user-centered, ultimately improving product functionality and reducing unnecessary changes later in the development cycle.
Streamlining the Evaluation Process
Developing a systematic evaluation process for prototypes can prevent excessive trial and error.
This involves setting clear criteria for evaluating each version of the prototype, along with predefined metrics to measure success.
With specific evaluation criteria in place, teams can objectively assess designs and determine whether they meet initial project goals.
Consistent evaluations not only streamline the design process but also provide clear direction for necessary modifications, keeping the project on schedule.
Conclusion
Reducing trial and error during the design of prototype parts is achievable through a combination of strategic planning, collaboration, and the use of modern tools and techniques.
By understanding the underlying principles of effective prototype design and leveraging the advantages offered by technology and teamwork, design teams can drastically improve efficiency and outcomes.
As projects move forward, applying these strategies will help in navigating the complexities of product development with more ease and success.
資料ダウンロード
QCD調達購買管理クラウド「newji」は、調達購買部門で必要なQCD管理全てを備えた、現場特化型兼クラウド型の今世紀最高の購買管理システムとなります。
ユーザー登録
調達購買業務の効率化だけでなく、システムを導入することで、コスト削減や製品・資材のステータス可視化のほか、属人化していた購買情報の共有化による内部不正防止や統制にも役立ちます。
NEWJI DX
製造業に特化したデジタルトランスフォーメーション(DX)の実現を目指す請負開発型のコンサルティングサービスです。AI、iPaaS、および先端の技術を駆使して、製造プロセスの効率化、業務効率化、チームワーク強化、コスト削減、品質向上を実現します。このサービスは、製造業の課題を深く理解し、それに対する最適なデジタルソリューションを提供することで、企業が持続的な成長とイノベーションを達成できるようサポートします。
オンライン講座
製造業、主に購買・調達部門にお勤めの方々に向けた情報を配信しております。
新任の方やベテランの方、管理職を対象とした幅広いコンテンツをご用意しております。
お問い合わせ
コストダウンが利益に直結する術だと理解していても、なかなか前に進めることができない状況。そんな時は、newjiのコストダウン自動化機能で大きく利益貢献しよう!
(Β版非公開)