- お役立ち記事
- APQP processes that product quality departments are focused on and their effective implementation methods
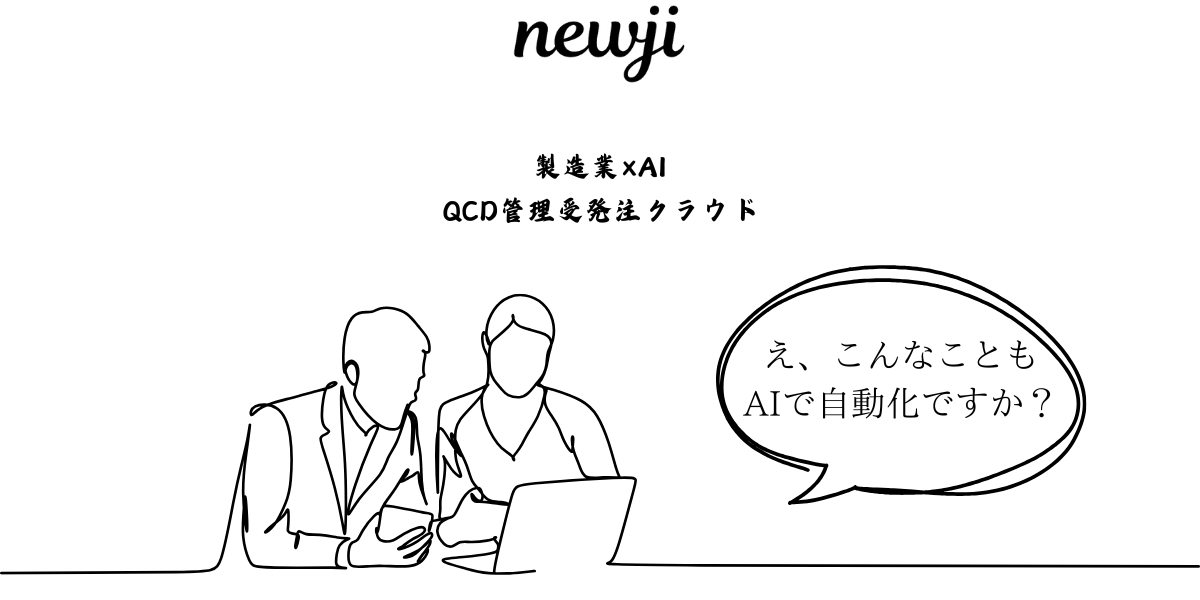
APQP processes that product quality departments are focused on and their effective implementation methods
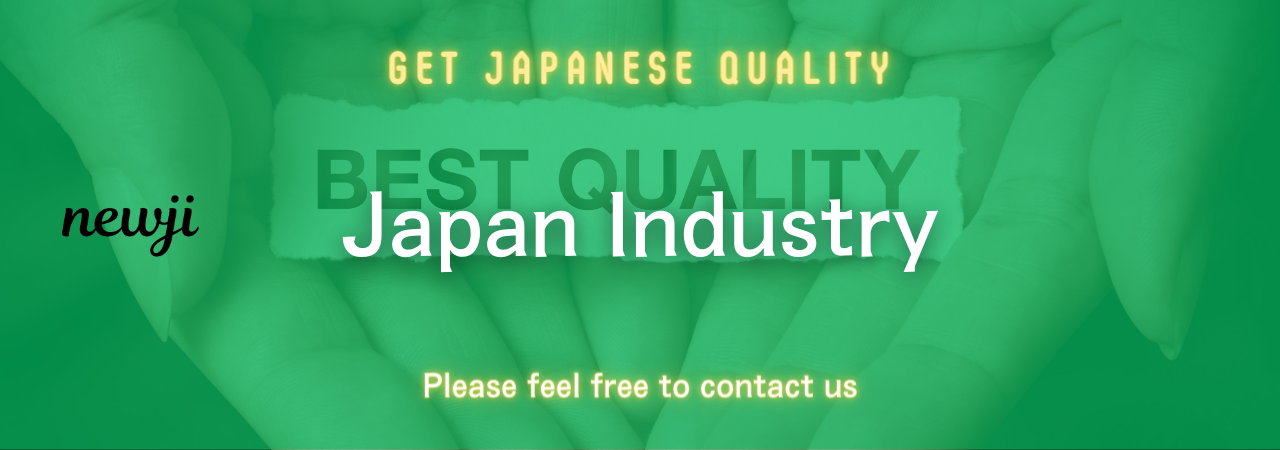
目次
Understanding APQP Processes
Advanced Product Quality Planning (APQP) is an important framework used predominantly within the automotive industry but applicable across various sectors for ensuring product quality.
It facilitates a structured approach to product development, ensuring that quality is prioritized from the initial conception to the final production stages.
Product quality departments focus on APQP processes to systematically improve product reliability and customer satisfaction.
These processes are grounded in three main principles: setting clear expectations, early involvement in design and manufacturing, and proactive prevention of potential issues.
The Phases of APQP
APQP is structured around five major phases that guide teams through planning and development:
1. **Plan and Define Program**: This is the initial phase where teams gather initial insights to understand customer needs and requirements.
This phase forms the foundation for the entire project, involving feasibility assessments and establishing goals.
2. **Product Design and Development**: In this phase, the focus shifts to developing detailed product designs.
It involves activities such as designing for manufacturability and conducting design reviews to ensure that designs meet quality standards and customer needs.
3. **Process Design and Development**: Here, teams concentrate on developing the necessary manufacturing processes.
This involves identifying necessary equipment, setting process parameters, and ensuring that processes can produce consistent quality.
4. **Product and Process Validation**: This critical phase involves testing both products and processes to ensure they can meet performance levels.
Prototyping, pilot production runs, and final product inspections are key activities to validate the design and processes.
5. **Feedback, Assessment, and Corrective Action**: The final phase focuses on monitoring output quality and implementing continuous improvements.
Feedback loops are created to address any discrepancies between planned and actual outcomes, leading to corrective actions.
Effective Implementation Methods
Implementing APQP processes effectively requires a comprehensive strategy incorporating cross-functional collaboration, diligent planning, and ongoing communication.
Cross-Functional Collaboration
The success of APQP processes greatly hinges on the collaborative efforts of multiple departments.
Cross-functional teams, involving stakeholders from engineering, quality control, manufacturing, and supply chain, bring diverse perspectives and expertise to the table.
This collaboration ensures that potential issues are identified early, allowing for timely interventions and enhancements.
Diligent Planning and Documentation
Diligent planning is paramount in the execution of APQP processes.
Meticulous documentation of every phase, including design specifications, process guidelines, and quality plans, provides a roadmap for team members to follow.
Detailed documentation aids in maintaining transparency and aligning team efforts with the project’s objectives.
Furthermore, it acts as a reference for future projects, enabling teams to replicate successful strategies and avoid past pitfalls.
Ongoing Communication
Communication is key to the successful implementation of APQP.
Regular meetings, updates, and feedback sessions ensure that all team members are informed about progress and any emerging challenges.
This open communication fosters a culture of transparency and allows for quick decision-making and problem-solving, which are crucial in maintaining project timelines and quality standards.
Additionally, maintaining open channels of communication with suppliers and customers ensures that expectations are clearly defined and met throughout the project lifecycle.
Overcoming Challenges in APQP Implementation
While APQP processes are highly effective, they do come with certain challenges that quality departments need to address proactively.
Managing Complexity
Projects often involve complex design and manufacturing requirements that can complicate APQP implementation.
Breaking down these complexities into manageable tasks and phases ensures a more focused approach.
Utilizing tools like project management software can help streamline tasks and keep teams organized.
Resource Allocation
Proper allocation of resources, including time, personnel, and financial investment, is crucial for effective APQP processes.
Ensuring that all necessary resources are available and utilized efficiently demands meticulous scheduling and budgeting.
Maintaining Quality Standards
Maintaining consistent quality standards throughout the project is a significant challenge.
Continuous monitoring and adherence to quality benchmarks are vital.
Implementing robust quality assurance processes at every stage ensures that final products meet or exceed customer expectations.
The Impact of APQP on Business Success
The successful implementation of APQP processes can lead to significant business benefits.
Companies can achieve higher customer satisfaction, as products are developed with the customer’s needs and quality as the core focus.
Reducing time-to-market is another advantage, as efficient processes prevent unnecessary delays.
This, in turn, results in competitive advantages within the marketplace.
Furthermore, APQP processes lead to cost savings through waste reduction and enhanced process efficiencies.
By focusing on quality from the onset, companies often experience fewer defects and rework, reducing production costs.
In conclusion, mastering APQP processes allows quality departments to seamlessly align product development and manufacturing efforts with business objectives.
Effective implementation methods like cross-functional collaboration, diligent planning, and ongoing communication, backed by overcoming challenges such as complexity and resource allocation, empower organizations to deliver superior products.
Through APQP, companies can enhance their competitive edge, ensuring that their products not only meet but exceed customer expectations.
資料ダウンロード
QCD調達購買管理クラウド「newji」は、調達購買部門で必要なQCD管理全てを備えた、現場特化型兼クラウド型の今世紀最高の購買管理システムとなります。
ユーザー登録
調達購買業務の効率化だけでなく、システムを導入することで、コスト削減や製品・資材のステータス可視化のほか、属人化していた購買情報の共有化による内部不正防止や統制にも役立ちます。
NEWJI DX
製造業に特化したデジタルトランスフォーメーション(DX)の実現を目指す請負開発型のコンサルティングサービスです。AI、iPaaS、および先端の技術を駆使して、製造プロセスの効率化、業務効率化、チームワーク強化、コスト削減、品質向上を実現します。このサービスは、製造業の課題を深く理解し、それに対する最適なデジタルソリューションを提供することで、企業が持続的な成長とイノベーションを達成できるようサポートします。
オンライン講座
製造業、主に購買・調達部門にお勤めの方々に向けた情報を配信しております。
新任の方やベテランの方、管理職を対象とした幅広いコンテンツをご用意しております。
お問い合わせ
コストダウンが利益に直結する術だと理解していても、なかなか前に進めることができない状況。そんな時は、newjiのコストダウン自動化機能で大きく利益貢献しよう!
(Β版非公開)