- お役立ち記事
- Automatic measurement of fatigue mechanism and crack growth in metal materials and application to fatigue design
月間77,185名の
製造業ご担当者様が閲覧しています*
*2025年2月28日現在のGoogle Analyticsのデータより
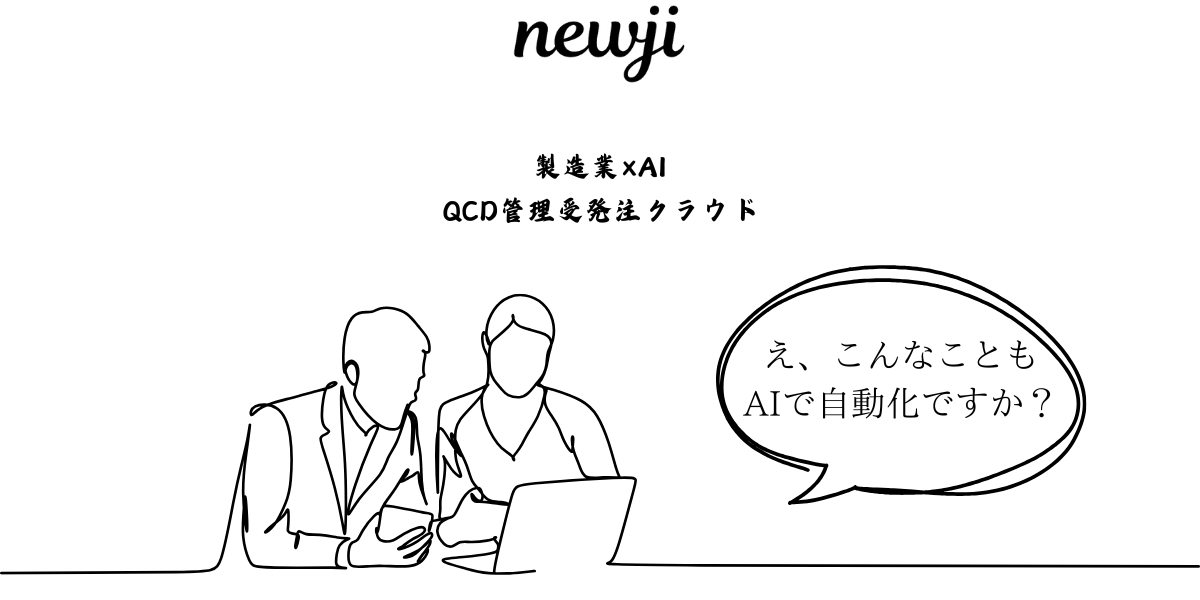
Automatic measurement of fatigue mechanism and crack growth in metal materials and application to fatigue design
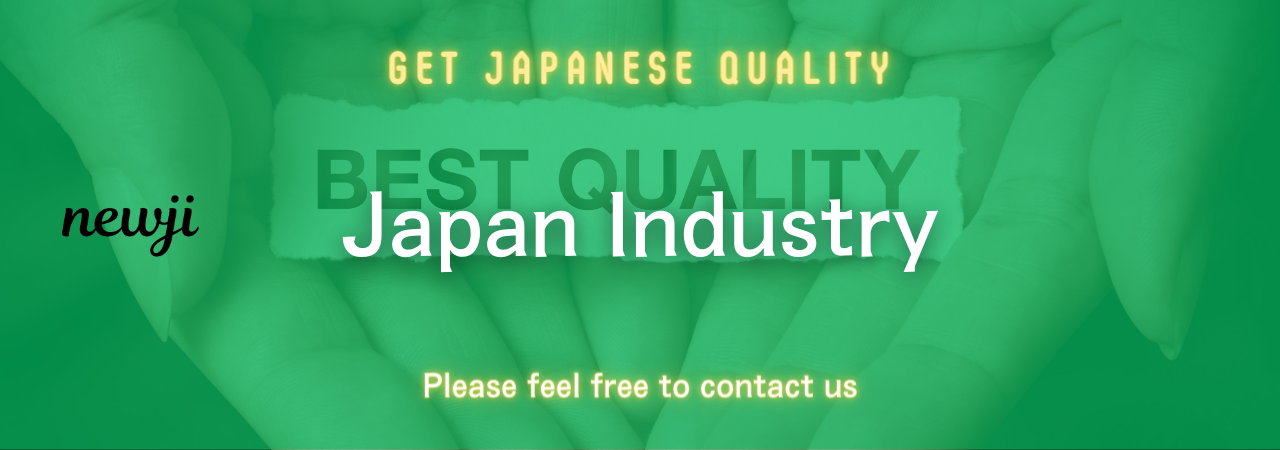
目次
Understanding Fatigue in Metal Materials
Metal materials are widely used in various industries because of their strength and durability.
However, like all materials, metals are subject to wear and fatigue over time.
Fatigue in metal involves the progressive and localized structural damage that occurs when a material is subjected to cyclic loading.
This phenomenon can eventually result in cracking and potentially catastrophic failures if not properly managed.
Understanding fatigue and the mechanisms driving it is vital, especially in applications where the safety and reliability of metal structures are critical.
The Process of Fatigue Mechanism
Fatigue mechanisms in metals are quite complex.
They begin with the initiation of small cracks within the material, often at sites of stress concentration such as surface notches, inclusions, or other imperfections.
These microscopic cracks gradually grow with each load cycle.
Their growth rate can be influenced by various factors such as the environment, temperature, and the material’s properties.
Typically, fatigue is characterized by three stages: crack initiation, crack growth, and final fracture.
The crack initiation phase might occupy most of the lifespan of the component.
Once a crack has been initiated, it can grow incrementally with each load cycle.
It’s in the crack growth phase that the most critical observations and measurements can be made to predict and prevent ultimate failure.
How Cracks Grow in Metal Materials
The propagation of cracks in metal materials is a major area of study within fatigue analysis.
The rate at which a crack propagates can provide crucial information about the remaining life of a component.
Crack growth is typically measured using various techniques, including fracture mechanics approaches.
One of the most commonly used methods for measuring crack growth is the use of a crack gauge or the direct observation technique with sophisticated microscopy.
Other advanced techniques, such as digital image correlation and X-ray tomography, are also employed to capture the complex behavior of cracks as they propagate through the material.
The rate of crack growth is influenced by the stress intensity at the crack tip, which is dependent on the geometrical configuration, material properties, and the applied load.
Understanding these factors allows engineers to predict crack growth accurately and design appropriately to avoid premature failure.
Advanced Techniques for Automatic Measurement
With advancements in technology, the measurement of fatigue and crack growth in metal materials has significantly improved.
Automatic measurement systems now allow for continuous monitoring of components under cyclic loading conditions.
These systems use sensors and software algorithms to detect the presence of cracks and measure their growth over time without the need for constant human intervention.
For instance, strain gauges and acoustic emission sensors can provide real-time data on the condition of a metal component.
Automated systems can assess fatigue life by analyzing the collected data, which is crucial for fatigue design and maintenance planning.
By implementing such systems, industries can greatly reduce the risk of unexpected failures, enhance safety, and optimize maintenance schedules.
Applications to Fatigue Design
The knowledge gained from understanding fatigue mechanisms and monitoring crack growth has significant applications in the fatigue design of metal components.
Fatigue design involves creating components that can withstand the required load cycles without experiencing significant cracking or failure within the intended lifespan.
Designers use data from fatigue studies to refine their designs, selecting appropriate materials and geometries that minimize stress concentrations and improve fatigue resistance.
Utilizing fracture mechanics principles, they can predict the growth of potential cracks and design components that can accommodate such growth without failing.
Additionally, fatigue design often incorporates safety factors based on the expected service conditions and the reliability of the materials used.
This proactive approach ensures structures can perform their intended function safely over their entire service life.
Benefits of Incorporating Automatic Measurement Systems
Incorporating automatic measurement systems in fatigue design offers numerous benefits.
Firstly, it enhances accuracy and reliability in monitoring metal components and predicting their lifespan.
It reduces the dependence on manual inspections, thus minimizing human error.
Secondly, it provides real-time insight into the condition of the material, allowing for timely interventions if necessary.
This capability can prevent catastrophic failures by enabling repairs or replacements before a crack grows to a critical size.
Lastly, automatic systems can lead to cost savings by optimizing maintenance schedules, preventing unnecessary downtimes, and extending the service life of components.
Future Prospects and Challenges
The future of automatic measurement in fatigue analysis looks promising with the continuous advancement of technology.
Development in areas such as AI and machine learning is expected to further enhance the ability to predict fatigue life and crack growth efficiently.
However, challenges remain, particularly in developing systems that are both highly accurate and cost-effective.
There is also an ongoing need to improve the capability of sensors to withstand harsh operational environments while providing reliable data.
Collaboration between research institutions, industries, and technology developers will be pivotal in overcoming these challenges.
As more sophisticated solutions are developed, they will open up new possibilities in fatigue design, enabling safer and more reliable use of metal materials across various sectors.
In conclusion, understanding the fatigue mechanism and monitoring crack growth are integral elements of engineering that serve to enhance the reliability and safety of metal components.
The application of automatic measurement systems represents a significant advancement in this field, offering both practical and economic benefits.
As technology continues to evolve, these systems will become increasingly vital in the design, maintenance, and operation of metal structures.
資料ダウンロード
QCD管理受発注クラウド「newji」は、受発注部門で必要なQCD管理全てを備えた、現場特化型兼クラウド型の今世紀最高の受発注管理システムとなります。
ユーザー登録
受発注業務の効率化だけでなく、システムを導入することで、コスト削減や製品・資材のステータス可視化のほか、属人化していた受発注情報の共有化による内部不正防止や統制にも役立ちます。
NEWJI DX
製造業に特化したデジタルトランスフォーメーション(DX)の実現を目指す請負開発型のコンサルティングサービスです。AI、iPaaS、および先端の技術を駆使して、製造プロセスの効率化、業務効率化、チームワーク強化、コスト削減、品質向上を実現します。このサービスは、製造業の課題を深く理解し、それに対する最適なデジタルソリューションを提供することで、企業が持続的な成長とイノベーションを達成できるようサポートします。
製造業ニュース解説
製造業、主に購買・調達部門にお勤めの方々に向けた情報を配信しております。
新任の方やベテランの方、管理職を対象とした幅広いコンテンツをご用意しております。
お問い合わせ
コストダウンが利益に直結する術だと理解していても、なかなか前に進めることができない状況。そんな時は、newjiのコストダウン自動化機能で大きく利益貢献しよう!
(β版非公開)