- お役立ち記事
- Balance between quality assurance and cost reduction from the purchasing department’s perspective
月間76,176名の
製造業ご担当者様が閲覧しています*
*2025年3月31日現在のGoogle Analyticsのデータより
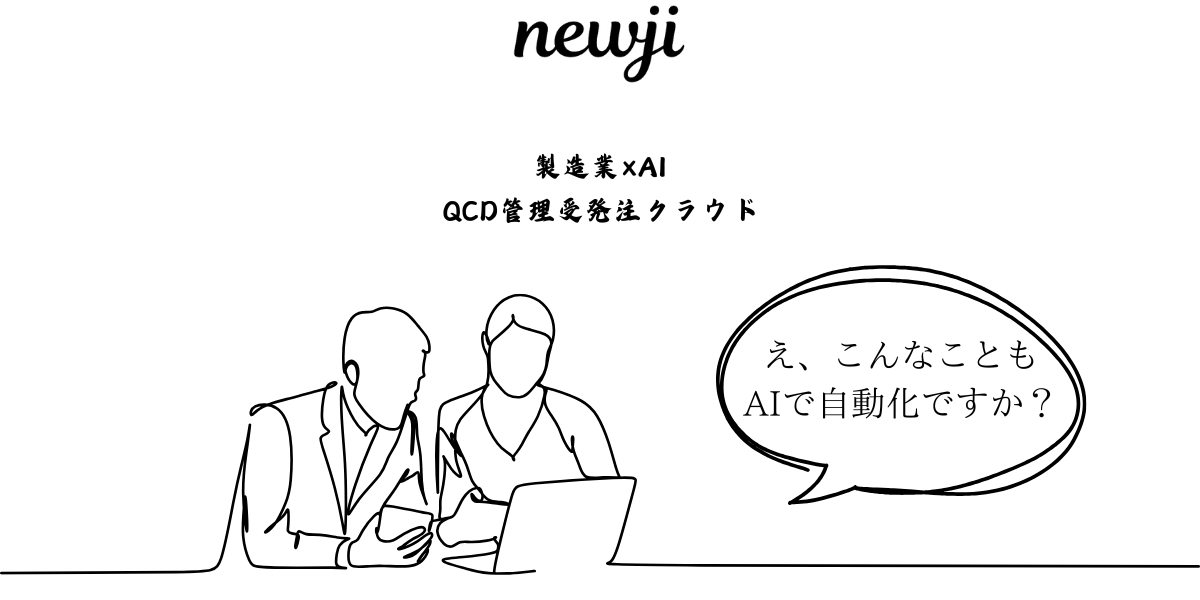
Balance between quality assurance and cost reduction from the purchasing department’s perspective
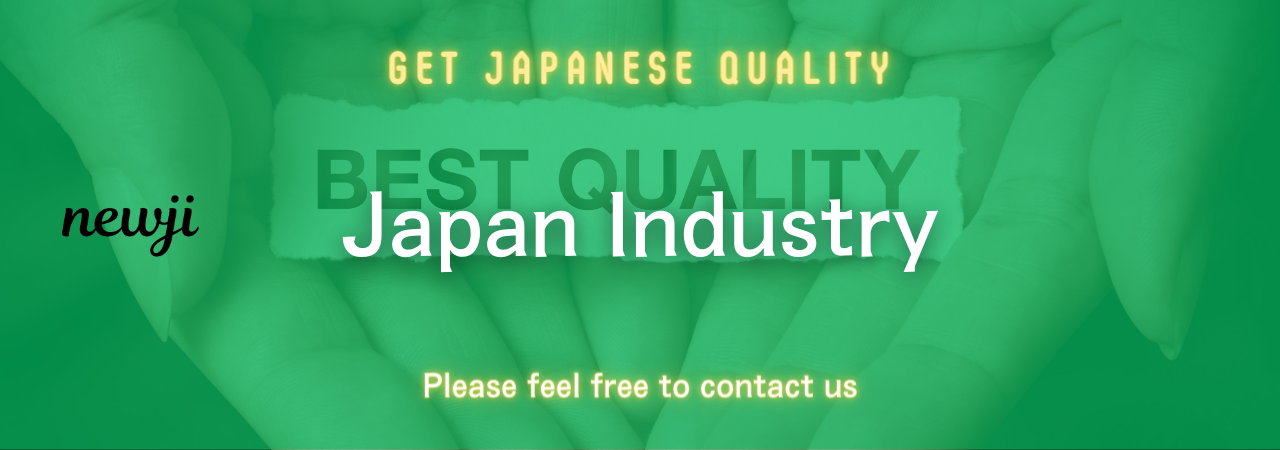
目次
Introduction
In the realm of business operations, the purchasing department plays a pivotal role in ensuring quality assurance while managing costs effectively.
Achieving the right balance between quality and cost is crucial for a company’s success.
When a purchasing department identifies the needs of the organization, it faces the challenge of meeting quality standards without exceeding budget constraints.
This delicate balance is essential to maintaining competitiveness and ensuring customer satisfaction.
The Role of the Purchasing Department
The purchasing department is responsible for obtaining the materials, goods, or services that a company requires to conduct its operations.
Its primary functions include supplier selection, price negotiation, and ensuring the timely delivery of products.
Effective purchasing involves evaluating suppliers to ensure they can meet both the quality standards and cost limitations of the company.
Balancing these aspects requires a strategic approach and thorough understanding of both market trends and internal company needs.
Quality Assurance: Why It Matters
Quality assurance in purchasing is about ensuring that the products or services acquired meet the required standards and specifications.
Consistent quality assurance is vital because it directly impacts the company’s overall performance and customer satisfaction.
If a product fails to meet quality standards, it can lead to increased returns, warranty claims, and customer dissatisfaction.
In the long term, poor quality can damage the company’s reputation and lead to financial losses.
Cost Reduction: A Necessity in Purchasing
Cost reduction is equally important to ensure the financial health and competitiveness of a company.
By minimizing expenses, a company can increase its profit margins and invest in other critical areas such as research and development or marketing.
The purchasing department must negotiate favorable terms with suppliers and seek cost-effective alternatives without compromising quality.
Effective cost management strategies help a company remain agile and responsive to market changes.
Strategies for Balancing Quality and Cost
Achieving a balance between quality assurance and cost reduction involves the implementation of strategic methods in the purchasing process.
Supplier Relationship Management
Developing robust relationships with suppliers is critical.
Suppliers who understand a company’s quality expectations and budget constraints are more likely to collaborate effectively.
By establishing long-term partnerships, companies can negotiate better terms and receive superior services.
Additionally, having a reliable supplier network allows purchasing departments to ensure a consistent supply of required materials.
Conducting Regular Audits and Evaluations
Regular audits and evaluations of suppliers help maintain standards and improve quality control.
This practice enables the purchasing department to identify any potential quality issues early and address them before they escalate.
By keeping suppliers accountable, companies can ensure adherence to quality specifications without incurring additional costs.
Embracing Technology and Automation
Leveraging technology, such as procurement software and systems, can streamline purchasing activities and enhance efficiency.
Automation reduces manual errors and allows for better data management, aiding in decision-making processes.
Through technology, purchasing departments can monitor trends, analyze spend data, and optimize order quantities, helping achieve cost savings while maintaining quality standards.
Utilizing Total Cost of Ownership (TCO)
Evaluating the total cost of ownership rather than just the initial purchase price helps in making informed decisions.
TCO considers all the associated costs over the product’s lifecycle, such as maintenance, operation, and disposal costs.
A lower purchase price may lead to higher expenses in the long term, affecting overall quality and profitability.
Thus, balancing these factors is crucial for optimizing procurement processes.
Challenges in Balancing Quality and Cost
Despite the best efforts, achieving the perfect balance between quality and cost is often fraught with challenges.
Supplier Variability
Supplier variability can influence both quality and cost unpredictably.
Factors such as changes in supplier management, economic fluctuations, or material shortages can disrupt planned purchasing strategies.
Adaptability and contingency plans are necessary to navigate these uncertainties.
Market Volatility
The fluctuating nature of global markets and economic conditions can lead to unexpected changes in costs.
Inflation, currency changes, and economic crises can affect supplier pricing and availability, impacting purchasing decisions.
Continuous market analysis and agility are required to mitigate these impacts effectively.
Balancing Innovation with Cost
Incorporating new technologies and innovations can lead to improved quality but also higher costs.
Determining when and how much to invest in innovative solutions is a critical decision for purchasing departments.
A strategic approach is necessary to encourage innovation without jeopardizing financial stability.
Conclusion
The purchasing department plays a vital role in achieving the balance between quality assurance and cost reduction.
By implementing strategic methodologies, such as supplier relationship management, regular supplier audits, technological integration, and a focus on total cost of ownership, companies can optimize their purchasing processes.
Despite the challenges that may arise, maintaining this equilibrium is essential for ensuring a company’s long-term success and sustaining competitive advantage in the marketplace.
資料ダウンロード
QCD管理受発注クラウド「newji」は、受発注部門で必要なQCD管理全てを備えた、現場特化型兼クラウド型の今世紀最高の受発注管理システムとなります。
ユーザー登録
受発注業務の効率化だけでなく、システムを導入することで、コスト削減や製品・資材のステータス可視化のほか、属人化していた受発注情報の共有化による内部不正防止や統制にも役立ちます。
NEWJI DX
製造業に特化したデジタルトランスフォーメーション(DX)の実現を目指す請負開発型のコンサルティングサービスです。AI、iPaaS、および先端の技術を駆使して、製造プロセスの効率化、業務効率化、チームワーク強化、コスト削減、品質向上を実現します。このサービスは、製造業の課題を深く理解し、それに対する最適なデジタルソリューションを提供することで、企業が持続的な成長とイノベーションを達成できるようサポートします。
製造業ニュース解説
製造業、主に購買・調達部門にお勤めの方々に向けた情報を配信しております。
新任の方やベテランの方、管理職を対象とした幅広いコンテンツをご用意しております。
お問い合わせ
コストダウンが利益に直結する術だと理解していても、なかなか前に進めることができない状況。そんな時は、newjiのコストダウン自動化機能で大きく利益貢献しよう!
(β版非公開)