- お役立ち記事
- Balancing Cost and Quality in CNC Machining OEM for Manufacturing
Balancing Cost and Quality in CNC Machining OEM for Manufacturing
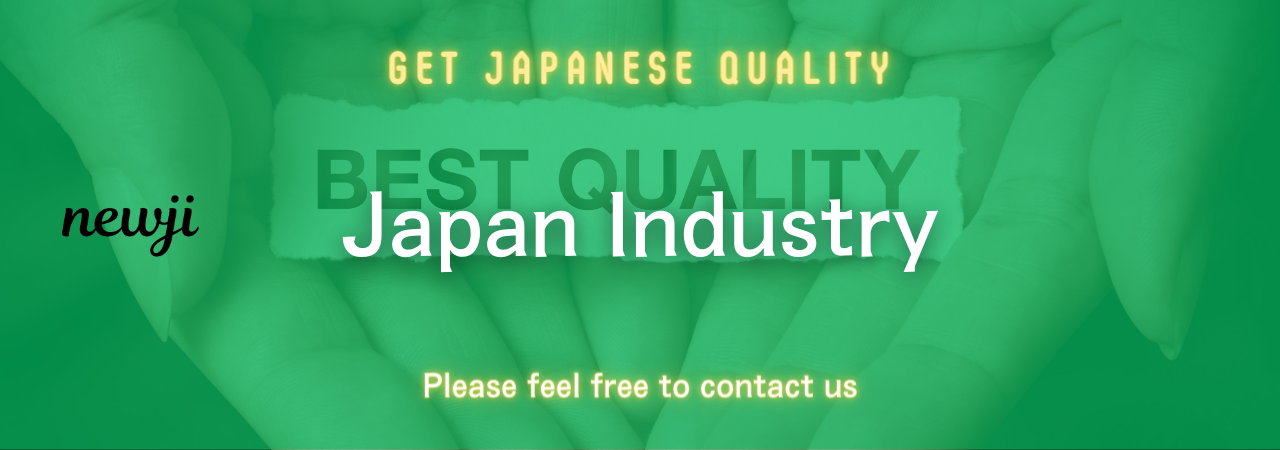
目次
Understanding CNC Machining OEM
CNC machining, or Computer Numerical Control machining, plays a vital role in modern manufacturing.
It involves the use of computers to control machine tools like lathes, mills, and grinders.
OEM stands for Original Equipment Manufacturer.
In a CNC machining OEM setting, the manufacturer produces parts or products that are used in another company’s end products.
The goal of a CNC machining OEM is to provide high-quality parts that meet precise specifications.
However, balancing cost and quality is a constant challenge for manufacturers.
Many factors come into play, such as material costs, labor, and machinery maintenance.
The Importance of Quality in Manufacturing
In the competitive world of manufacturing, quality cannot be overstated.
High-quality components ensure the final product performs well and has a long lifespan.
Poor quality, on the other hand, can lead to failures, recalls, and a tarnished brand reputation.
Quality in CNC machining involves precise measurements and fine-tuned processes.
Any deviation from the required specifications can render a part unusable.
Therefore, maintaining high standards is essential.
Factors Affecting Cost in CNC Machining OEM
Several elements influence the cost of CNC machining OEM services.
Material Costs
The type of material used in manufacturing is a significant cost factor.
Metals like aluminum and steel are common, but specialized alloys can be very expensive.
Choosing the right material involves balancing performance requirements with budget constraints.
Labor Costs
Labor is another major expense.
Skilled operators are necessary to oversee the CNC machines and ensure they run smoothly.
While automation reduces some labor costs, human oversight is still crucial.
Machinery and Maintenance
CNC machines themselves are costly investments.
They require regular maintenance to function at optimal levels.
Downtime for repairs not only incurs costs but also delays production schedules.
Overhead Costs
Other overhead costs include utilities, facility rent, and administrative expenses.
These all add up and impact the overall cost of production.
Strategies for Balancing Cost and Quality
Balancing cost and quality is a delicate act but can be achieved through several strategies.
Opt for Efficient Designs
Design efficiency can dramatically impact both cost and quality.
Simplifying a part’s design can reduce machining time and material usage.
This leads to lower costs without sacrificing quality.
Working with designers skilled in optimization can make a big difference.
Choose the Right Materials
Material selection should be based on both performance and cost-effectiveness.
Sometimes, a slightly more expensive material can reduce machining time or improve part longevity.
Conducting a cost-benefit analysis helps in making informed decisions.
Invest in Advanced Machinery
Modern CNC machines offer better efficiency, accuracy, and reliability.
While the upfront investment is high, the long-term benefits include reduced labor costs and higher quality output.
Advanced machinery also usually requires less maintenance, translating to lower downtime.
Implement Quality Control Measures
Use stringent quality control measures to catch issues early.
Techniques like Six Sigma and Total Quality Management help in maintaining high standards.
Quality control reduces waste and prevents costly errors, thereby optimizing both cost and quality.
Supplier Relationships
Good relationships with suppliers can also help manage costs.
Long-term partnerships can lead to better pricing and more reliable material supplies.
Consider suppliers as part of your team, working together towards the same goals.
The Role of Automation in Cost and Quality
Automation is increasingly important in CNC machining OEM.
Automated systems reduce human error, leading to higher quality parts.
They also speed up production, lowering labor costs.
Automated Quality Control
Automated quality control systems use sensors and cameras to inspect parts in real-time.
This immediate feedback catches errors early, reducing waste and rework.
Robotic Assistance
Robotic arms and automated material handling reduce the need for manual labor.
They also enhance precision, further ensuring high-quality output.
Case Studies: Successful Cost and Quality Balances
Many companies have successfully balanced cost and quality in CNC machining OEM.
Automotive Industry
In the automotive sector, components must meet exacting standards.
Companies use high-strength materials and invest in advanced machinery to ensure quality.
Simultaneously, they optimize designs to cut costs without compromising performance.
Aerospace Industry
The aerospace industry demands the highest quality due to safety concerns.
Here, cost-saving measures include using automated inspection systems and advanced materials.
While the initial costs are high, the long-term savings and performance benefits are substantial.
Future Trends in CNC Machining OEM
As technology advances, new trends will further help balance cost and quality.
These include:
3D Printing
3D printing offers new ways to produce parts with less material wastage.
It complements CNC machining by creating complex shapes that are hard to machine.
Internet of Things (IoT)
IoT-enabled machines can predict maintenance needs and optimize performance in real-time.
This reduces downtime and maintains high-quality production standards.
Artificial Intelligence (AI)
AI can analyze vast amounts of data to improve processes and predict quality issues.
Implementing AI can lead to smarter, cost-effective production.
In conclusion, balancing cost and quality in CNC machining OEM is a complex but achievable goal.
By focusing on design efficiency, material selection, advanced machinery, and stringent quality control, manufacturers can meet their objectives.
Automation and emerging technologies will further aid in this balance, ensuring both cost-effectiveness and superior quality in manufacturing.
資料ダウンロード
QCD調達購買管理クラウド「newji」は、調達購買部門で必要なQCD管理全てを備えた、現場特化型兼クラウド型の今世紀最高の購買管理システムとなります。
ユーザー登録
調達購買業務の効率化だけでなく、システムを導入することで、コスト削減や製品・資材のステータス可視化のほか、属人化していた購買情報の共有化による内部不正防止や統制にも役立ちます。
NEWJI DX
製造業に特化したデジタルトランスフォーメーション(DX)の実現を目指す請負開発型のコンサルティングサービスです。AI、iPaaS、および先端の技術を駆使して、製造プロセスの効率化、業務効率化、チームワーク強化、コスト削減、品質向上を実現します。このサービスは、製造業の課題を深く理解し、それに対する最適なデジタルソリューションを提供することで、企業が持続的な成長とイノベーションを達成できるようサポートします。
オンライン講座
製造業、主に購買・調達部門にお勤めの方々に向けた情報を配信しております。
新任の方やベテランの方、管理職を対象とした幅広いコンテンツをご用意しております。
お問い合わせ
コストダウンが利益に直結する術だと理解していても、なかなか前に進めることができない状況。そんな時は、newjiのコストダウン自動化機能で大きく利益貢献しよう!
(Β版非公開)