- お役立ち記事
- Basic concept of MRP
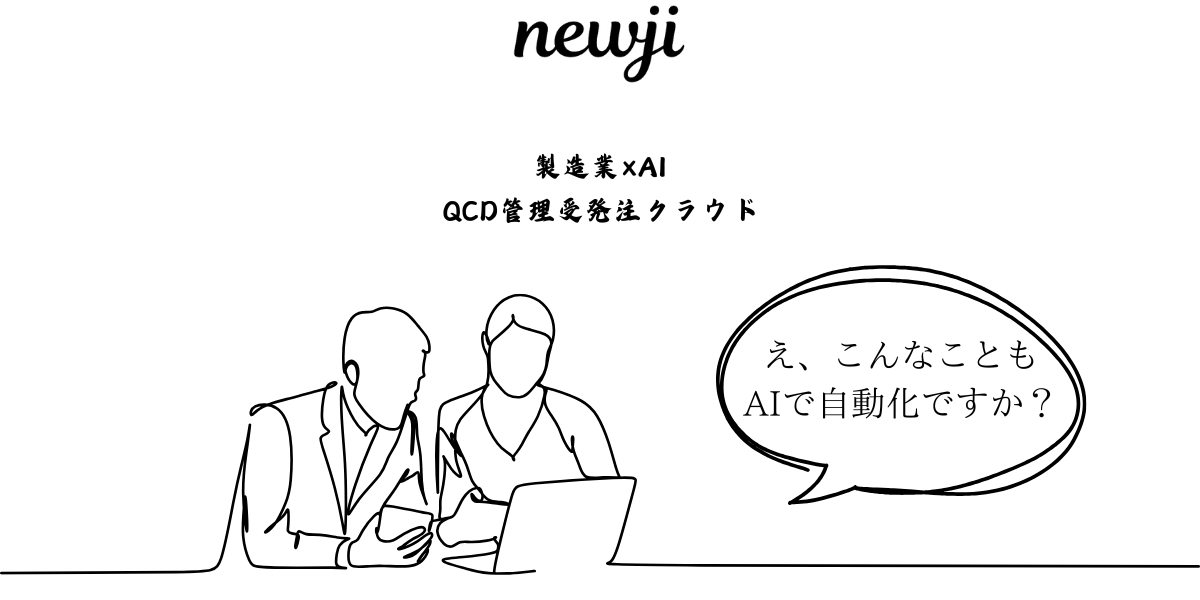
Basic concept of MRP
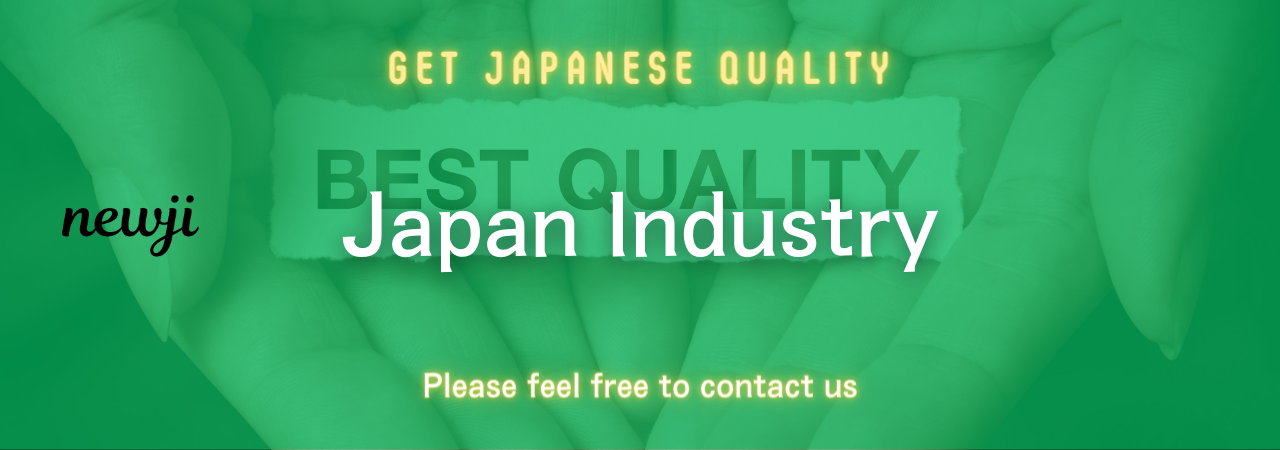
目次
Introduction to MRP
Material Requirements Planning, commonly known as MRP, is a fundamental concept in the world of manufacturing and production planning.
It’s an essential tool that companies use to manage inventory levels, streamline production schedules, and ensure that the necessary materials are available when needed.
In this article, we’ll explore the core principles of MRP, its components, and how it helps businesses optimize their operations.
What is MRP?
Material Requirements Planning is a systematic approach to calculating the materials and components required to manufacture a product.
MRP is designed to answer three key questions:
– What is needed?
– How much is needed?
– When is it needed?
By answering these questions, MRP helps businesses avoid overproduction, minimize waste, and improve the efficiency of the production process.
It provides a clear framework for managing inventories, scheduling production runs, and coordinating with suppliers.
The Components of MRP
To fully understand MRP, we need to explore its critical components or inputs.
These include:
1. Bill of Materials (BOM)
The Bill of Materials (BOM) is essentially a comprehensive list of all the raw materials, components, and assemblies needed to manufacture a product.
Think of it as the recipe for the product.
The BOM provides detailed information about each component, its quantity, and its relationship to the finished product.
It serves as a blueprint that guides the production process.
2. Master Production Schedule (MPS)
The Master Production Schedule (MPS) outlines the quantities of each product that need to be produced and when.
It includes the planned production of finished goods and takes into account customer orders, sales forecasts, and inventory levels.
The MPS helps ensure that production aligns with demand, preventing stockouts and excess inventory.
3. Inventory Records
Inventory records are used to track the current levels of raw materials and components.
They provide a snapshot of what is available, what is already allocated for existing orders, and what needs to be replenished.
Accurate inventory records are crucial for MRP to function effectively because they help determine when and how much to reorder.
How MRP Works
MRP operates by using the information from the BOM, MPS, and inventory records to create a detailed production and procurement plan.
Here’s a step-by-step breakdown of how MRP works:
Step 1: Gross Requirements Calculation
The process begins by assessing the gross requirements for each component based on the MPS.
The gross requirement indicates the total quantity needed without considering existing inventory.
Step 2: Net Requirements Calculation
Net requirements are determined by subtracting the available inventory and scheduled receipts from the gross requirements.
This step calculates the actual quantity that needs to be ordered or produced.
Step 3: Planned Orders
Based on the net requirements, MRP generates planned orders for the purchase of materials or the production of components.
These orders specify the quantity needed and the timing of delivery.
Step 4: Production Scheduling
MRP creates a detailed production schedule, outlining when each component or product should be manufactured.
This scheduling ensures that production aligns with demand and that materials are available when needed.
Step 5: Order Release
Finally, planned orders are converted into actual purchase orders or work orders.
These orders are then released to the appropriate departments or suppliers to initiate the production or procurement process.
Benefits of MRP
Implementing MRP can bring several significant benefits to businesses:
1. Improved Inventory Management
One of the primary advantages of MRP is its ability to optimize inventory levels.
By accurately forecasting demand and calculating requirements, companies can avoid excess inventory, reducing carrying costs and minimizing waste.
2. Enhanced Production Planning
MRP streamlines production planning by providing clear schedules and guidelines for manufacturing processes.
This leads to more efficient use of resources, reduced lead times, and on-time delivery of products.
3. Reduced Lead Times
With MRP, companies can better coordinate their production and procurement activities, resulting in shorter lead times.
This agility is crucial in today’s fast-paced markets where customer expectations for quick delivery are high.
4. Improved Customer Satisfaction
By ensuring that products are available when customers need them, MRP contributes to higher levels of customer satisfaction.
Meeting delivery deadlines and avoiding stockouts can enhance a company’s reputation and loyalty among its clients.
Challenges and Limitations
While MRP offers numerous benefits, it is not without its challenges and limitations:
1. Data Accuracy
MRP relies heavily on accurate data from BOMs, inventory records, and MPS.
Any discrepancies or errors in this data can lead to flawed planning and decision-making.
2. Complexity
Implementing and managing an MRP system can be complex, especially for large organizations with diverse product lines.
It requires a well-integrated software solution and skilled personnel to operate effectively.
3. Changing Demand
MRP is designed to work with stable demand patterns.
Sudden shifts in demand or unexpected changes can disrupt the planning process and lead to inefficiencies.
Conclusion
In conclusion, Material Requirements Planning (MRP) is a fundamental tool for modern manufacturing and production management.
By providing a structured approach to inventory management and production scheduling, MRP helps businesses optimize their operations, reduce costs, and improve customer satisfaction.
While it comes with its share of challenges, the benefits it offers make it an indispensable asset for companies striving for efficiency in today’s competitive markets.
資料ダウンロード
QCD調達購買管理クラウド「newji」は、調達購買部門で必要なQCD管理全てを備えた、現場特化型兼クラウド型の今世紀最高の購買管理システムとなります。
ユーザー登録
調達購買業務の効率化だけでなく、システムを導入することで、コスト削減や製品・資材のステータス可視化のほか、属人化していた購買情報の共有化による内部不正防止や統制にも役立ちます。
NEWJI DX
製造業に特化したデジタルトランスフォーメーション(DX)の実現を目指す請負開発型のコンサルティングサービスです。AI、iPaaS、および先端の技術を駆使して、製造プロセスの効率化、業務効率化、チームワーク強化、コスト削減、品質向上を実現します。このサービスは、製造業の課題を深く理解し、それに対する最適なデジタルソリューションを提供することで、企業が持続的な成長とイノベーションを達成できるようサポートします。
オンライン講座
製造業、主に購買・調達部門にお勤めの方々に向けた情報を配信しております。
新任の方やベテランの方、管理職を対象とした幅広いコンテンツをご用意しております。
お問い合わせ
コストダウンが利益に直結する術だと理解していても、なかなか前に進めることができない状況。そんな時は、newjiのコストダウン自動化機能で大きく利益貢献しよう!
(Β版非公開)