- お役立ち記事
- Basic knowledge of manufacturing cost evaluation that purchasing personnel should know
月間76,176名の
製造業ご担当者様が閲覧しています*
*2025年3月31日現在のGoogle Analyticsのデータより
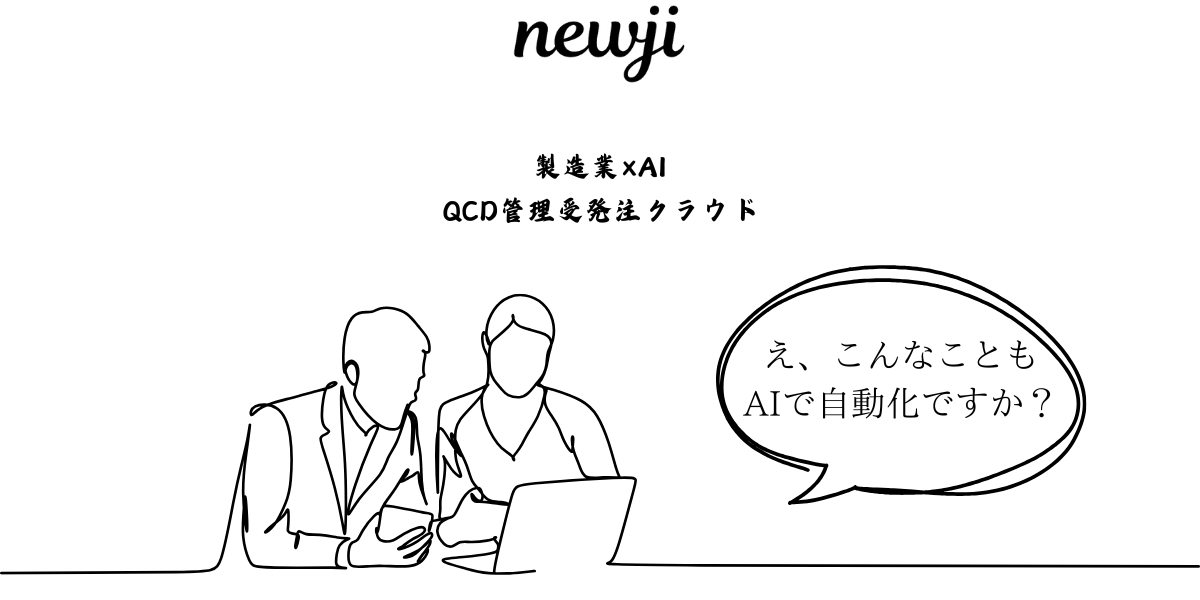
Basic knowledge of manufacturing cost evaluation that purchasing personnel should know
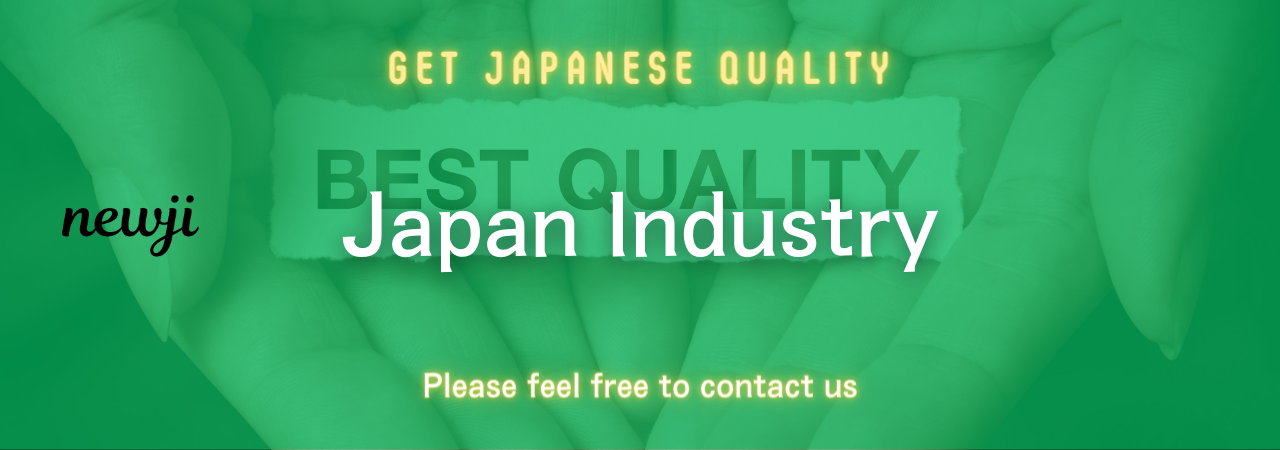
目次
Understanding Manufacturing Costs
To effectively manage purchasing in any manufacturing business, it’s crucial to have a solid grasp of manufacturing costs.
Knowing how these costs are structured helps you make informed decisions that can lead to significant cost savings and contribute to your company’s bottom line.
Manufacturing costs are generally categorized into three main components: direct materials, direct labor, and manufacturing overhead.
Let’s delve deeper into each of these categories.
Direct Materials
Direct materials are the raw inputs that become a part of the final product.
For example, the metal used in making a car or the fabric used in a shirt are considered direct materials.
These materials can be traced back directly to the finished product.
Purchasing personnel need to maintain relationships with reliable suppliers to ensure the quality and timely delivery of these materials.
Understanding the cost structure of direct materials involves knowing the price, the quantity required, and any additional costs such as shipping or import duties.
It’s essential for purchasing managers to negotiate effectively with suppliers to obtain the best prices and terms.
Direct Labor
Direct labor refers to the wages paid to workers who are directly involved in the production process, such as assembly line workers or machinists.
These costs are variable, meaning they can change based on the number of units produced.
Understanding direct labor costs is critical as they can significantly impact the manufacturing cost per unit.
To evaluate labor costs, it’s necessary to analyze wage rates, employee productivity, and the hours required to complete the production process.
Investing in employee training and efficient production processes can lead to a reduction in direct labor costs over time.
Manufacturing Overhead
Manufacturing overhead includes all the costs that aren’t direct materials or direct labor but are necessary for the production process.
This includes costs like factory utilities, equipment depreciation, and salaries of indirect labor such as maintenance staff.
Unlike direct costs, manufacturing overhead is often fixed and does not fluctuate with production levels.
Purchasing personnel should understand how overhead costs are allocated to products to accurately assess the total manufacturing cost.
Improving equipment efficiency and reducing unnecessary expenses can help manage these overhead costs.
Cost Accounting Methods
Different cost accounting methods are used to evaluate manufacturing cost, including absorption costing, variable costing, and activity-based costing.
Absorption Costing
Absorption costing, also known as full costing, is a method where all manufacturing costs, including fixed and variable overhead, are allocated to the product.
This approach ensures that the product reflects the full cost associated with its production.
For purchasing personnel, understanding absorption costing is crucial as it impacts inventory valuation and financial reporting.
Variable Costing
Variable costing includes only variable production costs, such as direct materials and direct labor, in the product cost.
Fixed overhead is expensed in the period incurred.
This method helps in decision-making as it provides a clearer picture of the contribution margin and helps in pricing strategies.
Understanding both absorption and variable costing enables purchasing managers to strategize better and make informed decisions regarding inventory levels and pricing.
Activity-Based Costing (ABC)
Activity-based costing assigns costs to products based on the activities required to produce them.
It offers a more accurate reflection of costs by identifying what drives costs in a particular process.
For purchasing managers, ABC provides insights into which areas are consuming resources and where cost optimization can occur.
This approach can lead to better supplier selection and process improvements.
Analyzing and Reducing Manufacturing Costs
To keep manufacturing costs in check, purchasing personnel should engage in cost analysis and implement strategies for cost reduction.
Supplier Negotiations
One of the most effective ways to reduce direct material costs is through strategic supplier negotiations.
Purchasing managers must be skilled in securing favorable terms and exploring discounts for bulk purchases or long-term agreements.
Inventory Management
Efficient inventory management can prevent excess stock, reducing storage costs and minimizing waste.
Using just-in-time (JIT) inventory systems or other inventory management techniques helps maintain optimal stock levels.
Process Efficiency
Identifying areas of inefficiency within the production process can lead to significant savings.
Implementing lean manufacturing processes and investing in modern technology can improve productivity and reduce labor and overhead costs.
The Importance of Cost Evaluation
Regularly evaluating manufacturing costs is crucial for purchasing personnel as it provides insights into profitability and competitive pricing.
By understanding cost components and deploying effective cost management strategies, purchasing managers can contribute substantially to the organization’s financial health.
Staying informed about industry trends, technological advancements, and economic factors can also influence cost structures.
Purchasing personnel who proactively manage and evaluate manufacturing costs are invaluable assets to their organizations, helping to drive success and sustainability in a competitive market.
資料ダウンロード
QCD管理受発注クラウド「newji」は、受発注部門で必要なQCD管理全てを備えた、現場特化型兼クラウド型の今世紀最高の受発注管理システムとなります。
ユーザー登録
受発注業務の効率化だけでなく、システムを導入することで、コスト削減や製品・資材のステータス可視化のほか、属人化していた受発注情報の共有化による内部不正防止や統制にも役立ちます。
NEWJI DX
製造業に特化したデジタルトランスフォーメーション(DX)の実現を目指す請負開発型のコンサルティングサービスです。AI、iPaaS、および先端の技術を駆使して、製造プロセスの効率化、業務効率化、チームワーク強化、コスト削減、品質向上を実現します。このサービスは、製造業の課題を深く理解し、それに対する最適なデジタルソリューションを提供することで、企業が持続的な成長とイノベーションを達成できるようサポートします。
製造業ニュース解説
製造業、主に購買・調達部門にお勤めの方々に向けた情報を配信しております。
新任の方やベテランの方、管理職を対象とした幅広いコンテンツをご用意しております。
お問い合わせ
コストダウンが利益に直結する術だと理解していても、なかなか前に進めることができない状況。そんな時は、newjiのコストダウン自動化機能で大きく利益貢献しよう!
(β版非公開)