- お役立ち記事
- Basic knowledge of raw material cost analysis that should be kept in mind during procurement
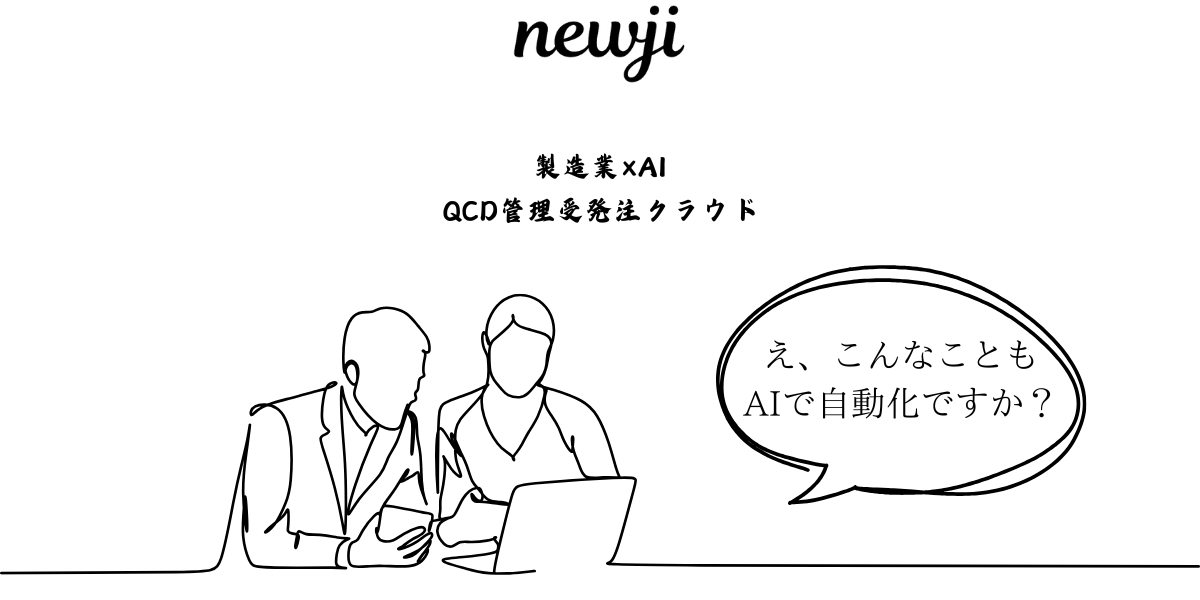
Basic knowledge of raw material cost analysis that should be kept in mind during procurement
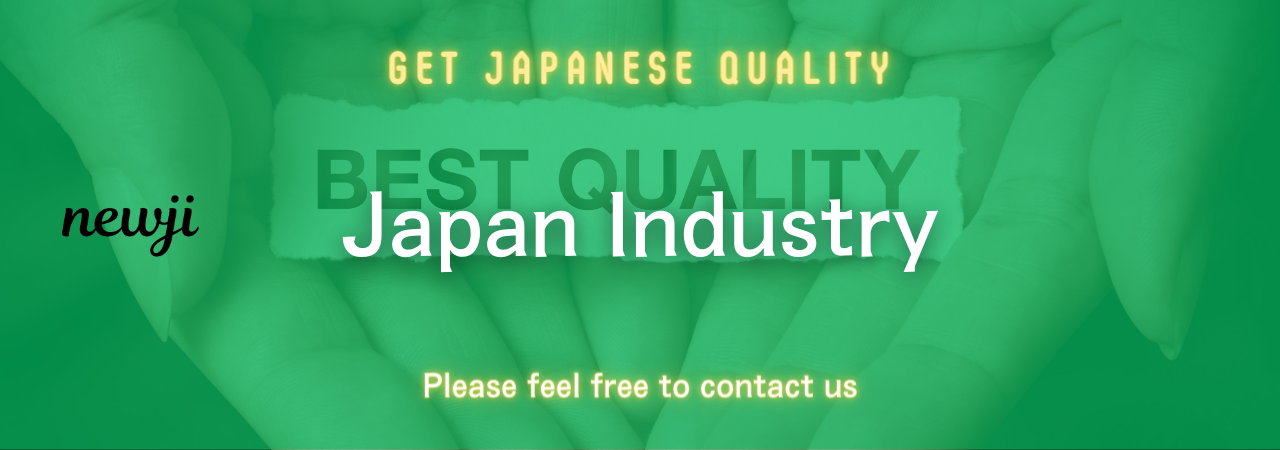
目次
Understanding Raw Material Cost Analysis
Raw material cost analysis is an essential aspect of procurement, helping businesses manage expenses and optimize their budgets effectively.
By understanding the factors that influence raw material costs, companies can make informed purchasing decisions, maintain profitability, and stay competitive in their respective industries.
In this article, we will explore the basic concepts of raw material cost analysis and provide a clear guide to help procurement professionals navigate this critical area.
Factors Influencing Raw Material Costs
1. Supply and Demand
The fundamental economic principle of supply and demand significantly impacts raw material costs.
When demand for a specific material exceeds its supply, prices tend to rise.
Conversely, when supply surpasses demand, prices usually fall.
Understanding these market dynamics is crucial for procurement professionals to predict price trends and plan purchases accordingly.
2. Market Conditions
Market conditions, including geopolitical events, currency fluctuations, and economic stability, can heavily influence raw material prices.
For instance, political instability in a key producing region can lead to supply disruptions, causing prices to spike.
Similarly, currency exchange rates play a critical role, as global trade often requires the conversion of currencies, affecting the cost of imports and exports.
3. Production Costs
The cost of producing raw materials, such as extraction or farming, can directly impact their prices.
Factors such as labor costs, energy prices, and technological advancements can alter production costs and subsequently affect raw material prices.
Staying informed about these aspects can help procurement professionals anticipate changes in material costs.
4. Transportation Costs
The logistics involved in transporting raw materials from suppliers to manufacturers are a significant component of raw material costs.
Fuel prices, transportation infrastructure, and distance all play a role in determining these costs.
Procurement professionals need to consider these factors when analyzing raw material expenses.
5. Environmental Regulations
Environmental regulations and sustainability practices can influence the cost of raw materials.
Compliance with environmental standards may require additional investments in technology or changes in production processes, potentially impacting material costs.
Procurement teams should stay abreast of relevant regulations and assess their potential effects on supply and costs.
Steps for Effective Raw Material Cost Analysis
1. Data Collection and Management
The first step in raw material cost analysis is collecting and managing relevant data.
This includes historical price data, supplier information, and any market intelligence that can provide insights into price trends.
Efficient data management systems help procurement professionals access the necessary information to make informed decisions.
2. Identifying Key Cost Drivers
Identifying the key factors driving costs is crucial for effective analysis.
Procurement professionals should evaluate the elements discussed earlier, such as supply and demand, market conditions, and production costs, to determine their impact on material prices.
3. Conducting Cost Forecasting
Cost forecasting involves predicting future raw material prices based on current data and market trends.
This process requires analytical skills, market insight, and sometimes the use of forecasting software.
Accurate forecasts enable procurement professionals to strategize and plan purchases at optimal times.
4. Supplier Assessment and Negotiation
Assessing supplier capabilities and negotiating favorable terms are vital components in managing raw material costs.
Evaluating supplier reliability, quality, and pricing allows procurement teams to make informed decisions and negotiate deals that benefit both parties.
5. Continuous Monitoring and Adjustment
Market conditions and raw material costs are constantly evolving.
Regular monitoring of price trends and market developments enables procurement professionals to adjust their strategies as needed.
Flexibility and adaptability are key in responding to changes and maintaining cost efficiencies.
Benefits of Raw Material Cost Analysis
Cost Savings
By analyzing raw material costs effectively, companies can identify opportunities for cost savings.
Proactive procurement strategies and informed decision-making lead to reduced expenses and improved profit margins.
Improved Negotiation Power
Armed with a thorough understanding of cost drivers and market conditions, procurement professionals have stronger negotiation positions when dealing with suppliers.
This can result in better pricing and terms, further enhancing an organization’s cost-efficiency.
Risk Mitigation
Raw material cost analysis helps identify potential risks associated with price fluctuations, supply disruptions, or regulatory changes.
By recognizing these risks early, companies can implement contingency plans and minimize negative impacts on operations.
Strategic Sourcing
With a clear understanding of raw material costs, procurement professionals can develop strategic sourcing plans that align with business goals.
This includes identifying alternative suppliers, exploring new materials, and fostering long-term supplier relationships.
Conclusion
Raw material cost analysis is a vital component of the procurement process, allowing companies to optimize their purchasing strategies and maintain competitiveness.
By considering the various factors influencing material costs and implementing effective analysis steps, procurement teams can achieve cost savings, improve their negotiation power, mitigate risks, and execute strategic sourcing initiatives.
By keeping these fundamentals in mind, businesses can ensure they are well-prepared to navigate the complexities of raw material procurement and make decisions that positively impact their bottom line.
資料ダウンロード
QCD調達購買管理クラウド「newji」は、調達購買部門で必要なQCD管理全てを備えた、現場特化型兼クラウド型の今世紀最高の購買管理システムとなります。
ユーザー登録
調達購買業務の効率化だけでなく、システムを導入することで、コスト削減や製品・資材のステータス可視化のほか、属人化していた購買情報の共有化による内部不正防止や統制にも役立ちます。
NEWJI DX
製造業に特化したデジタルトランスフォーメーション(DX)の実現を目指す請負開発型のコンサルティングサービスです。AI、iPaaS、および先端の技術を駆使して、製造プロセスの効率化、業務効率化、チームワーク強化、コスト削減、品質向上を実現します。このサービスは、製造業の課題を深く理解し、それに対する最適なデジタルソリューションを提供することで、企業が持続的な成長とイノベーションを達成できるようサポートします。
オンライン講座
製造業、主に購買・調達部門にお勤めの方々に向けた情報を配信しております。
新任の方やベテランの方、管理職を対象とした幅広いコンテンツをご用意しております。
お問い合わせ
コストダウンが利益に直結する術だと理解していても、なかなか前に進めることができない状況。そんな時は、newjiのコストダウン自動化機能で大きく利益貢献しよう!
(Β版非公開)