- お役立ち記事
- Basic Knowledge of Roll Casting Technology in Non-Ferrous Metals
Basic Knowledge of Roll Casting Technology in Non-Ferrous Metals
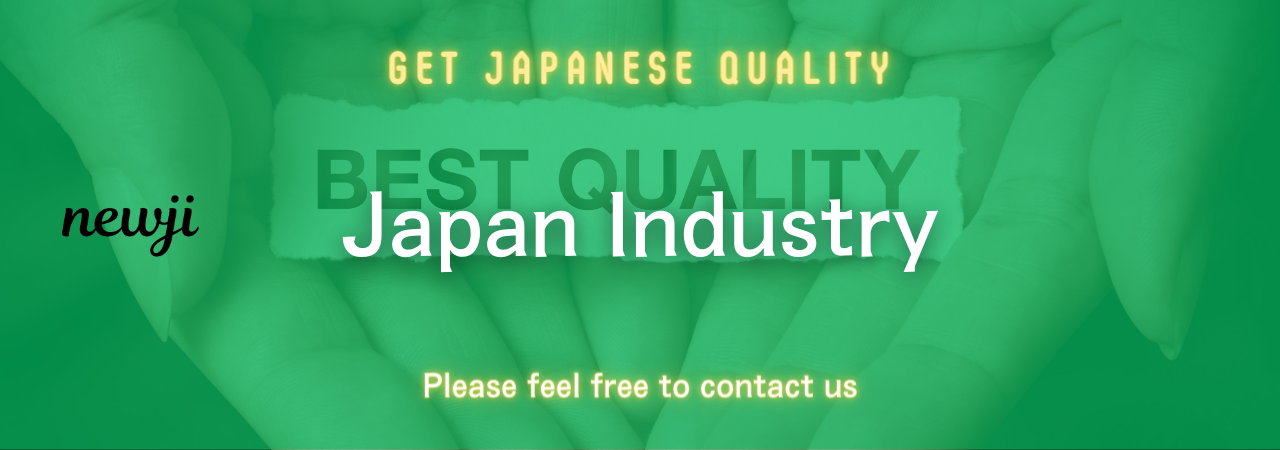
目次
Introduction to Roll Casting Technology
Roll casting is a specialized manufacturing process widely used in the production of non-ferrous metals.
It is a continuous process that combines the melting and solidification of metal into thin sheets or strips.
This technology is crucial in various industries, including automotive, electronics, and construction, due to its efficiency and cost-effectiveness.
The process minimizes waste and produces high-quality metal products that meet industry standards.
What is Roll Casting?
Roll casting involves pouring molten metal between two closely spaced, rotating rolls.
As the metal cools and solidifies, it is cast into a desired thickness, and the continuous process allows for high production rates and minimal waste.
The rolls’ speed, temperature, and the cooling mechanism are meticulously controlled to ensure the metal’s properties meet precise specifications.
The Importance of Non-Ferrous Metals
Non-ferrous metals, such as aluminum, copper, and magnesium, are remarkable for their resistance to corrosion and excellent conductivity.
These metals are distinguished from ferrous metals by the absence of iron, making them highly sought after in industries that require durable, lightweight, and conductive materials.
Roll casting is particularly advantageous for non-ferrous metals as it offers a consistent, efficient way to produce large quantities at a lower cost.
Advantages of Roll Casting Technology
Roll casting technology presents numerous benefits, especially when working with non-ferrous metals.
Efficiency and Cost-Effectiveness
One of the main advantages of roll casting is its high efficiency.
The continuous nature of the process reduces labor and material costs, as automation plays a significant role.
This efficiency translates to reduced production times and significant cost savings, making it an attractive option for manufacturers.
Product Consistency and Quality
Roll casting produces a uniform thickness across the entire strip of metal, ensuring consistent product quality.
This uniformity is crucial for applications that demand precision, such as electronic components and automotive parts.
The technology’s ability to maintain close dimensional tolerances means less material waste and improved product performance.
Environmental Considerations
The roll casting process is also environmentally friendly, as it reduces the need for extensive post-processing.
Since the process minimizes waste, it lessens the environmental impact associated with metal manufacturing.
Lower energy consumption compared to traditional methods further supports sustainable production practices.
Key Components of Roll Casting Equipment
Understanding the components of roll casting equipment is vital for optimizing the process and ensuring high-quality outcomes.
Furnace
The furnace is where the metal is melted before being cast.
It is crucial to maintain precise temperature control to ensure the metal’s properties are not compromised.
This component must be designed to handle the specific alloy being processed.
Rolls
The rolls are a critical part of the roll casting equipment.
They need to be made of robust materials capable of withstanding high temperatures and pressures.
Roll surfaces must be smooth to produce a flawless metal finish, and they require precise calibration to achieve the desired metal thickness.
Cooling System
Effective cooling is essential in the roll casting process.
The cooling system must quickly and evenly solidify the metal as it exits the rolls.
This system often involves water or forced air cooling, with the capability to adjust cooling rates to achieve specific mechanical properties in the final product.
Applications of Roll Cast Non-Ferrous Metals
Roll casting technology opens up numerous applications due to its ability to produce uniform and high-quality metal products.
Automotive Industry
In the automotive industry, roll-cast aluminum and magnesium alloys are highly valued for their lightweight properties.
These metals contribute to fuel efficiency and reduce the overall weight of vehicles.
Parts such as door panels, hoods, and structural components frequently utilize roll-cast metals.
Electronics Industry
Non-ferrous metals like copper and aluminum are integral to the electronics industry.
Roll casting produces the thin sheets required for electrical components, such as circuit boards and connectors, known for their excellent thermal and electrical conductivities.
Construction Sector
In construction, roll-cast metals provide durable and corrosion-resistant materials for roofing, siding, and structural components.
Aluminum, in particular, is favored for its strength-to-weight ratio and resistance to environmental degradation, making it ideal for exterior applications.
Challenges in Roll Casting Technology
While roll casting offers numerous benefits, it also presents specific challenges that must be addressed to optimize the process.
Control of Casting Parameters
Achieving consistent product quality requires careful control of casting parameters.
This includes maintaining accurate temperatures, roll speeds, and cooling rates.
Deviations in these parameters can lead to defects such as surface irregularities or internal stresses.
Alloy Composition
The composition of the alloy can significantly impact the roll casting process.
Different metals and alloys may require adjustments in temperature settings and cooling techniques.
Ensuring the correct composition is vital for achieving the desired mechanical properties in the final product.
Equipment Maintenance
Regular maintenance of roll casting equipment is crucial to minimize downtime and ensure consistent production quality.
Wear and tear on rolls, cooling systems, and furnaces can affect the process, necessitating ongoing inspection and repair schedules.
Conclusion
Roll casting technology plays a pivotal role in the manufacturing of non-ferrous metals, offering significant advantages in terms of efficiency, cost, and product quality.
With applications across various industries, its ability to produce lightweight, durable, and conductive metals continues to drive its adoption.
By understanding the process, components, and challenges involved, manufacturers can harness roll casting technology to produce high-quality non-ferrous metal products that meet the diverse demands of modern industries.
資料ダウンロード
QCD調達購買管理クラウド「newji」は、調達購買部門で必要なQCD管理全てを備えた、現場特化型兼クラウド型の今世紀最高の購買管理システムとなります。
ユーザー登録
調達購買業務の効率化だけでなく、システムを導入することで、コスト削減や製品・資材のステータス可視化のほか、属人化していた購買情報の共有化による内部不正防止や統制にも役立ちます。
NEWJI DX
製造業に特化したデジタルトランスフォーメーション(DX)の実現を目指す請負開発型のコンサルティングサービスです。AI、iPaaS、および先端の技術を駆使して、製造プロセスの効率化、業務効率化、チームワーク強化、コスト削減、品質向上を実現します。このサービスは、製造業の課題を深く理解し、それに対する最適なデジタルソリューションを提供することで、企業が持続的な成長とイノベーションを達成できるようサポートします。
オンライン講座
製造業、主に購買・調達部門にお勤めの方々に向けた情報を配信しております。
新任の方やベテランの方、管理職を対象とした幅広いコンテンツをご用意しております。
お問い合わせ
コストダウンが利益に直結する術だと理解していても、なかなか前に進めることができない状況。そんな時は、newjiのコストダウン自動化機能で大きく利益貢献しよう!
(Β版非公開)