- お役立ち記事
- Basic Knowledge of Subtractive Manufacturing Techniques for Metal Products
月間76,176名の
製造業ご担当者様が閲覧しています*
*2025年3月31日現在のGoogle Analyticsのデータより
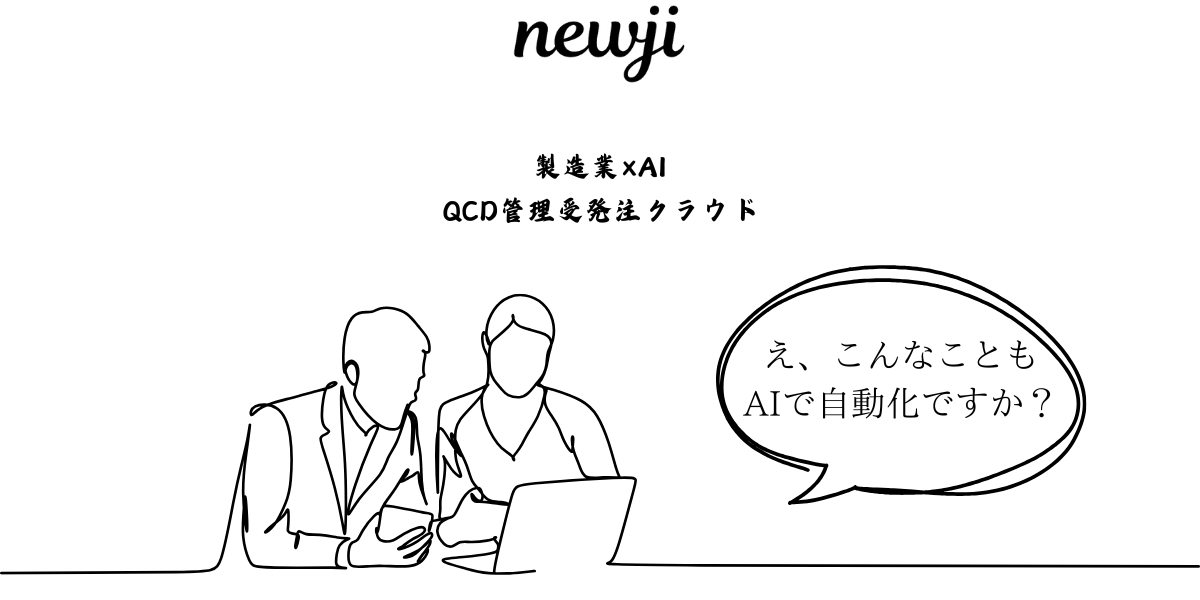
Basic Knowledge of Subtractive Manufacturing Techniques for Metal Products
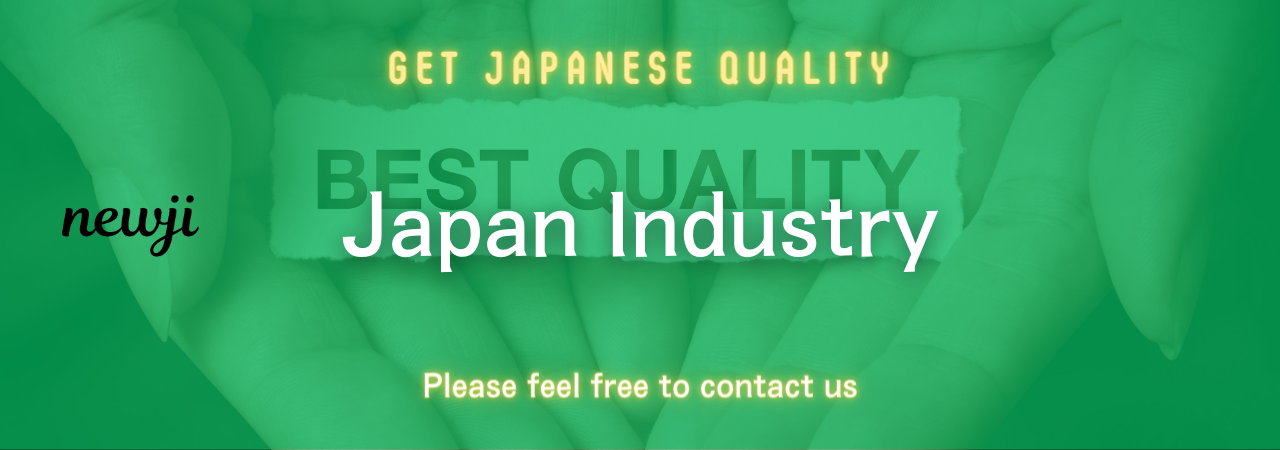
目次
Understanding Subtractive Manufacturing
Subtractive manufacturing is a process in which material is removed from a solid block or billet to create a desired shape and design in metal products.
This method contrasts with additive manufacturing, where materials are added layer by layer.
Subtractive manufacturing involves various techniques like milling, turning, drilling, and grinding that are used across industries to produce precision metal components.
From automotive parts to aerospace components, subtractive manufacturing plays a critical role in the creation of intricate metal products.
Key Techniques in Subtractive Manufacturing
Milling
Milling is one of the most common subtractive manufacturing techniques.
It involves the use of rotary cutters to remove material from a workpiece.
A milling machine can perform a variety of operations, including cutting, drilling, and routing.
This versatility makes milling a popular choice for creating complex parts with high precision.
There are two main types of milling processes: horizontal and vertical.
In horizontal milling, the cutting tool is mounted on a horizontal spindle, allowing for heavy-duty milling along the face of the workpiece.
Vertical milling, on the other hand, has the cutting tool mounted on a vertical spindle, allowing for more intricate and detailed work.
Turning
Turning is another fundamental subtractive manufacturing technique.
It involves rotating the workpiece around a fixed cutting tool to shape the metal.
This process is typically performed on a lathe, which holds the workpiece in place and allows it to spin at various speeds.
Turning is especially suited for producing cylindrical shapes and is commonly used for creating parts like shafts, rods, and pipes.
Precision in turning is achieved through careful control of the cutting tool’s movement, often guided by computer numerical control (CNC) systems.
Drilling
Drilling is the process of creating holes in a workpiece.
The technique employs a drill bit, a cutting tool attached to a drill press or machine.
As the drill bit rotates, it bores into the metal, creating precise holes for fasteners or other applications.
Among subtractive manufacturing techniques, drilling is essential for creating components that require fastening or assembly.
Modern CNC machines are capable of drilling multiple holes with high accuracy, ensuring consistent production of parts.
Grinding
Grinding is a finishing process used to achieve high surface quality and precise dimensions.
In grinding, an abrasive wheel removes small amounts of material from the metal workpiece.
This technique is often employed to achieve a smooth surface on parts that have been machined using other subtractive methods.
Grinding is especially important in industries where precision and smooth finishes are critical, such as in aerospace and medical equipment manufacturing.
With advances in abrasive technology, grinding can produce incredibly accurate and fine finishes.
Benefits of Subtractive Manufacturing
Subtractive manufacturing offers several advantages that make it a preferred choice for creating metal products.
First, this technique allows for high precision and tight tolerances which are essential for many engineering applications.
The ability to machine parts with exact specifications ensures that components fit perfectly within larger assemblies.
Another benefit is the wide range of materials that can be used in subtractive manufacturing.
From stainless steel to titanium, various metals can be processed using these techniques, providing flexibility for different applications.
Furthermore, subtractive manufacturing often results in superior surface finishes compared to additive methods.
This quality is crucial for parts exposed to wear or those that need to meet aesthetic or functional standards.
Challenges and Limitations
Despite its benefits, subtractive manufacturing does have some limitations.
One primary challenge is the amount of waste material generated during the machining process.
As material is removed, there can be significant excess, especially when machining complex shapes from large metal blocks.
The initial setup costs can be considerable, particularly for advanced CNC machines.
This investment can be a barrier to entry for smaller manufacturers or businesses working with smaller production volumes.
Additionally, the complexity of certain designs may limit the effectiveness of subtractive methods.
For parts with intricate internal features, alternative manufacturing techniques might be more suitable.
Future of Subtractive Manufacturing
The landscape of subtractive manufacturing is evolving with technological advancements.
The integration of CAD (computer-aided design) and CAM (computer-aided manufacturing) has streamlined the production process, enhancing precision and reducing lead times.
Moreover, hybrid manufacturing is on the rise, combining both subtractive and additive techniques.
This approach allows for the benefits of both methods, such as building strong structural components through additive methods and finishing them with subtractive processes for precision.
Automation and advancements in AI and machine learning are also playing a role in shaping the future of subtractive manufacturing.
These technologies provide manufacturers with the tools to optimize machining strategies, improve efficiency, and predict issues before they occur.
Conclusion
Subtractive manufacturing remains a cornerstone of metal product manufacturing, valued for its precision, versatility, and ability to work with a wide variety of materials.
While there are challenges to address, the ongoing advancements in technology promise to further enhance these processes, ensuring their relevance in the modern manufacturing landscape.
As industries continue to innovate, mastering the basics of subtractive manufacturing will be key to maintaining competitiveness in the production of high-quality metal components.
資料ダウンロード
QCD管理受発注クラウド「newji」は、受発注部門で必要なQCD管理全てを備えた、現場特化型兼クラウド型の今世紀最高の受発注管理システムとなります。
ユーザー登録
受発注業務の効率化だけでなく、システムを導入することで、コスト削減や製品・資材のステータス可視化のほか、属人化していた受発注情報の共有化による内部不正防止や統制にも役立ちます。
NEWJI DX
製造業に特化したデジタルトランスフォーメーション(DX)の実現を目指す請負開発型のコンサルティングサービスです。AI、iPaaS、および先端の技術を駆使して、製造プロセスの効率化、業務効率化、チームワーク強化、コスト削減、品質向上を実現します。このサービスは、製造業の課題を深く理解し、それに対する最適なデジタルソリューションを提供することで、企業が持続的な成長とイノベーションを達成できるようサポートします。
製造業ニュース解説
製造業、主に購買・調達部門にお勤めの方々に向けた情報を配信しております。
新任の方やベテランの方、管理職を対象とした幅広いコンテンツをご用意しております。
お問い合わせ
コストダウンが利益に直結する術だと理解していても、なかなか前に進めることができない状況。そんな時は、newjiのコストダウン自動化機能で大きく利益貢献しよう!
(β版非公開)