- お役立ち記事
- Basic notes on transportation risks and quality control for new employees in the purchasing department
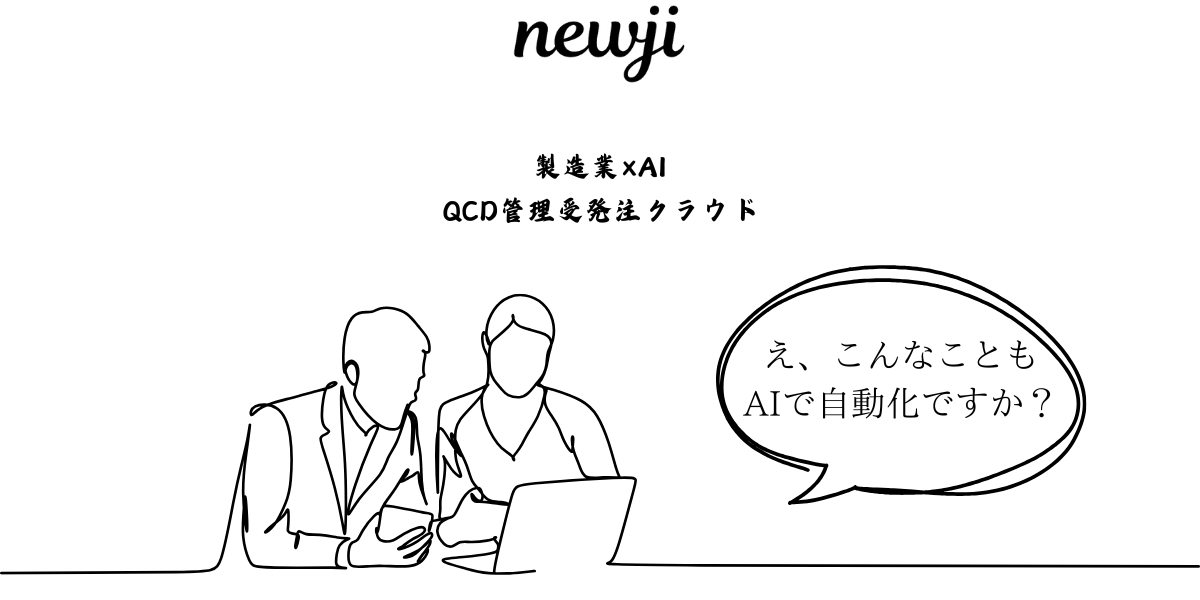
Basic notes on transportation risks and quality control for new employees in the purchasing department
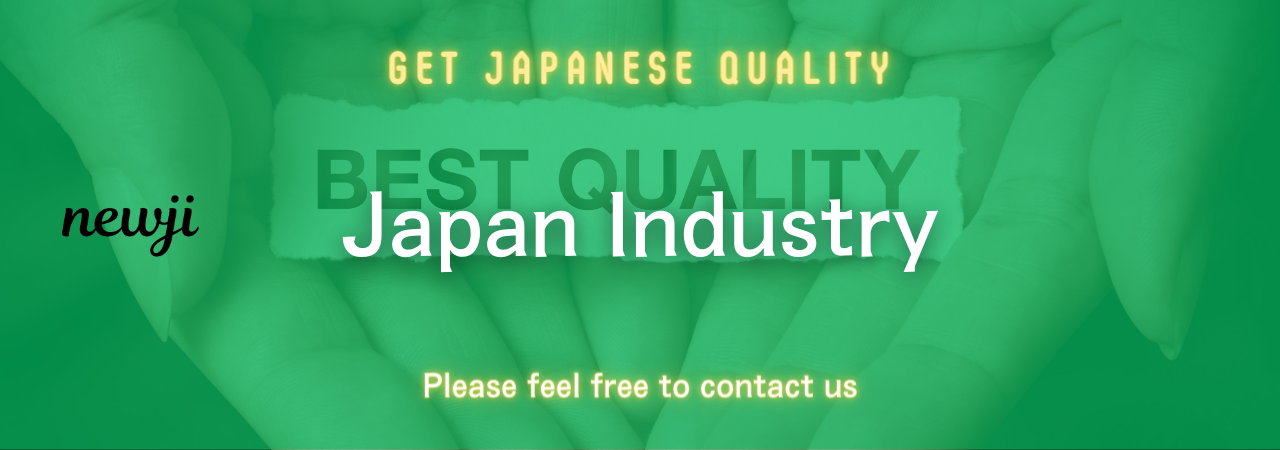
目次
Understanding Transportation Risks
When new employees join the purchasing department, gaining a solid understanding of transportation risks is crucial.
Transportation is a vital component of supply chain management, but it also comes with its own set of challenges and risks.
These risks can directly impact the quality of the products and ultimately affect customer satisfaction.
Therefore, recognizing and mitigating these risks from the outset is essential for maintaining the company’s reputation and efficiency.
Identifying Common Transportation Risks
One of the most common transportation risks is damage to goods during transit.
Goods can be subjected to rough handling, accidents, or exposure to unfavorable weather conditions, which can compromise their quality.
Another prevalent risk is the delay in delivery.
This can be caused by various factors such as traffic congestion, inclement weather, or issues at customs.
Delays can lead to stockouts, disappointing customers, and potential loss of sales.
The risk of theft or pilferage during transportation is another concern.
Valuable goods are attractive targets, and theft can lead to significant financial losses.
Additionally, compliance and regulatory issues pose a risk, as non-compliance with legal requirements can result in penalties and damage to the company’s reputation.
Strategies to Mitigate Transportation Risks
To address these risks, several strategies can be implemented.
Firstly, selecting reliable carriers and establishing strong partnerships with them can greatly reduce the likelihood of damaged goods.
Ensure that you work with carriers who have a proven track record and strong safety protocols in place.
Implementing robust packaging standards can further protect products during transit.
This involves using appropriate materials and techniques to cushion and secure items, ensuring they arrive in perfect condition.
For minimizing delays, real-time tracking and communication with logistics providers are essential.
By having access to live updates on the shipment’s status, you can promptly address any issues that might arise.
Also, have contingency plans in place for alternative routes or modes of transport to minimize disruption.
When it comes to theft prevention, sealing products with tamper-evident packaging and limiting access to trusted personnel is critical.
Using tracking technology can also help monitor for suspicious activity along the transportation route.
Lastly, always stay informed about legal and regulatory requirements.
Ensure that all documentation is accurate and complete, and adhere to local and international laws governing the transport of goods.
The Importance of Quality Control
Quality control is integral to purchasing, especially in the context of transportation.
Even with the best transportation practices, without rigorous quality control, the risk of receiving substandard products increases.
Implementing Effective Quality Control Measures
Start by establishing clear quality standards for all purchased goods.
These standards should outline the expected specifications, tolerances, and inspection procedures.
Communicate these standards effectively to suppliers to ensure mutual understanding.
Regular audits and inspections of incoming goods are vital components of quality control.
Conducting these checks upon delivery helps identify any defects or damages early, allowing for prompt action.
Implementing technology like barcode scanning or RFID can enhance the accuracy and efficiency of these inspections.
Supplier performance monitoring is another key aspect.
Track supplier performance over time, using key metrics such as defect rates, delivery punctuality, and responsiveness.
This data will help identify potential risks and allow the purchasing department to take corrective actions when necessary.
Training and educating employees within the purchasing department are also crucial.
Make sure they understand the importance of quality control and know how to conduct inspections effectively.
Encouraging a mindset of continuous improvement can lead to improved processes and better outcomes.
Building Strong Supplier Relationships
Developing strong partnerships with suppliers can greatly enhance quality control efforts.
Open and honest communication fosters trust and collaboration, leading to better quality outcomes.
Working closely with suppliers can also help in improving their processes and ensuring they align with your quality expectations.
Consider engaging in joint quality improvement initiatives with suppliers.
By working together towards common goals, both parties can benefit from improved product quality and reduced risks.
Conclusion
For new employees in the purchasing department, understanding transportation risks and the importance of quality control is essential for success.
By recognizing the common risks involved in transportation and implementing effective quality control measures, they can ensure the integrity of the supply chain.
This approach not only safeguards the company’s interests but also enhances customer satisfaction, contributing to overall business success.
Through continuous learning and strengthening supplier relationships, the purchasing department can effectively manage and mitigate transportation and quality risks.
資料ダウンロード
QCD調達購買管理クラウド「newji」は、調達購買部門で必要なQCD管理全てを備えた、現場特化型兼クラウド型の今世紀最高の購買管理システムとなります。
ユーザー登録
調達購買業務の効率化だけでなく、システムを導入することで、コスト削減や製品・資材のステータス可視化のほか、属人化していた購買情報の共有化による内部不正防止や統制にも役立ちます。
NEWJI DX
製造業に特化したデジタルトランスフォーメーション(DX)の実現を目指す請負開発型のコンサルティングサービスです。AI、iPaaS、および先端の技術を駆使して、製造プロセスの効率化、業務効率化、チームワーク強化、コスト削減、品質向上を実現します。このサービスは、製造業の課題を深く理解し、それに対する最適なデジタルソリューションを提供することで、企業が持続的な成長とイノベーションを達成できるようサポートします。
オンライン講座
製造業、主に購買・調達部門にお勤めの方々に向けた情報を配信しております。
新任の方やベテランの方、管理職を対象とした幅広いコンテンツをご用意しております。
お問い合わせ
コストダウンが利益に直結する術だと理解していても、なかなか前に進めることができない状況。そんな時は、newjiのコストダウン自動化機能で大きく利益貢献しよう!
(Β版非公開)