- お役立ち記事
- Basic procedures for overseas procurement and countermeasures and management points for quality, delivery dates, and transportation issues to avoid problems
Basic procedures for overseas procurement and countermeasures and management points for quality, delivery dates, and transportation issues to avoid problems
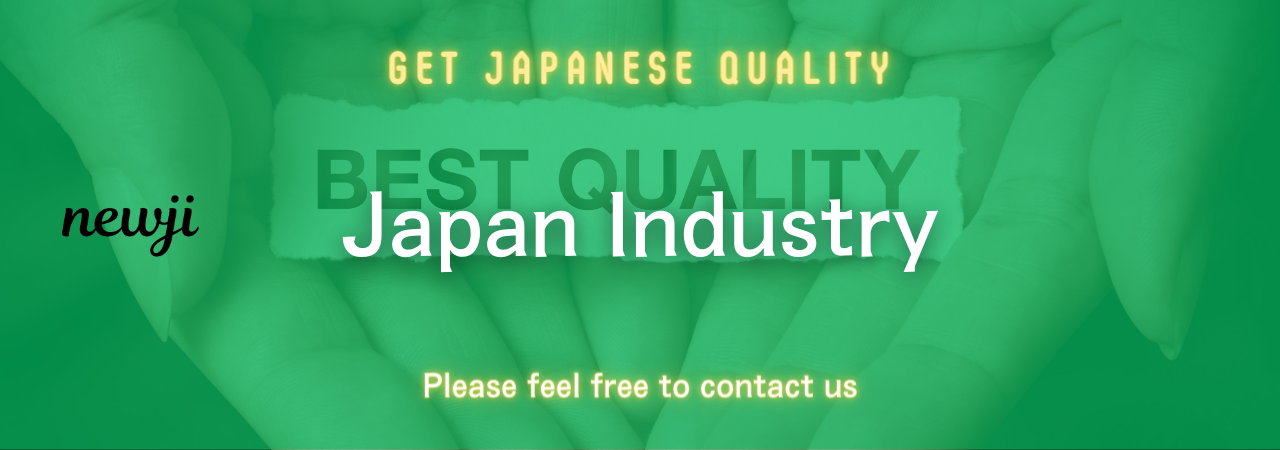
目次
Understanding Overseas Procurement
When businesses decide to expand their operations by sourcing materials or products from overseas, they step into a complex arena filled with opportunities and challenges.
Overseas procurement can offer competitive pricing, access to unique products, and a broader supply base.
However, it also carries potential risks related to quality, delivery timelines, and transportation issues.
To succeed in international sourcing, companies must balance these factors effectively.
Identifying Suitable Suppliers
Finding the right supplier is one of the most crucial steps in overseas procurement.
Companies should start by identifying potential suppliers that have a good reputation in the market.
Research can be conducted via industry directories, trade shows, and online platforms.
Additionally, companies should evaluate suppliers based on their financial stability, production capacity, and compliance with international standards.
Building relationships with local agents can also facilitate better communication and understanding of the supplier’s capabilities.
Developing a Supply Chain Strategy
A well-thought-out supply chain strategy is essential for ensuring the smooth flow of goods from overseas suppliers to the company’s warehouse.
Businesses should consider factors like shipping routes, customs regulations, and potential geopolitical risks.
Employing a mix of air and sea freight options, along with establishing a reliable logistics network, helps in optimizing the procurement process.
Companies may also work with logistics partners who have expertise in international shipping.
Managing Quality
Setting Clear Quality Expectations
Quality assurance in overseas procurement starts with setting clear quality expectations with suppliers.
Providing detailed product specifications, standards, and quality benchmarks is crucial.
Using technology, businesses can share clear digital mock-ups or prototypes to ensure mutual understanding.
Quality Control Mechanisms
Implementing robust quality control mechanisms throughout the production process is vital.
One effective approach is to conduct factory audits and regular inspections.
These efforts ensure that products meet the required standards before they leave the production facility.
Engaging third-party quality inspection services can provide an unbiased assessment of the product’s quality and confirm adherence to specifications.
Ensuring Timely Delivery
Setting Realistic Delivery Timelines
Understanding and setting realistic delivery timelines help in managing expectations and reducing disappointments.
Companies should factor in the production lead time, shipping duration, and possible customs delays.
Establishing milestones or checkpoints in the timeline can help track progress and identify potential delays early on.
Building Strong Communication Channels
Effective communication plays a pivotal role in ensuring timely deliveries.
Maintaining regular communication with suppliers keeps everyone updated on the progress of production.
Using project management tools and regular video conferencing can bridge the gap between different time zones and cultural perspectives.
Tackling Transportation Issues
Choosing the Right Transportation Mode
Selecting the appropriate mode of transportation is crucial for efficient overseas procurement.
Businesses should evaluate different transportation modes like sea freight, air freight, or intermodal transport, based on timing, cost, and product nature.
For instance, perishable goods require faster modes like air freight, while bulky goods can be shipped economically via sea freight.
Logistics Partner Collaboration
Collaborating with experienced logistics partners can help in overcoming transportation challenges.
These partners can offer insights into route optimization, customs procedures, and more.
Having a dedicated logistics partner ensures smoother operations and helps mitigate the risks associated with global supply chains.
Risk Management and Contingency Planning
Identifying Potential Risks
Every procurement strategy should include risk assessment.
Understanding potential risks like political instability, natural disasters, and currency fluctuations is crucial.
Once identified, businesses can develop strategies to mitigate these risks and ensure continuity in supply.
Developing Contingency Plans
Preparation is key to handling unforeseen disruptions.
Developing contingency plans, such as alternative supplier arrangements or additional inventories, can provide a buffer against supply chain disruptions.
Regularly updating these plans ensures they remain relevant in the face of changing global scenarios.
Conclusion
Overseas procurement can be a powerful tool for businesses seeking competitive advantage and operational efficiency.
By thoroughly understanding and managing the various aspects of quality, delivery, and transportation, companies can mitigate risks and enhance their procurement strategies.
Implementing clear quality controls, maintaining open lines of communication, and collaborating with reliable partners will lead to a successful overseas procurement operation.
With careful planning and strategic execution, businesses can harness the benefits of global sourcing while minimizing potential downsides.
資料ダウンロード
QCD調達購買管理クラウド「newji」は、調達購買部門で必要なQCD管理全てを備えた、現場特化型兼クラウド型の今世紀最高の購買管理システムとなります。
ユーザー登録
調達購買業務の効率化だけでなく、システムを導入することで、コスト削減や製品・資材のステータス可視化のほか、属人化していた購買情報の共有化による内部不正防止や統制にも役立ちます。
NEWJI DX
製造業に特化したデジタルトランスフォーメーション(DX)の実現を目指す請負開発型のコンサルティングサービスです。AI、iPaaS、および先端の技術を駆使して、製造プロセスの効率化、業務効率化、チームワーク強化、コスト削減、品質向上を実現します。このサービスは、製造業の課題を深く理解し、それに対する最適なデジタルソリューションを提供することで、企業が持続的な成長とイノベーションを達成できるようサポートします。
オンライン講座
製造業、主に購買・調達部門にお勤めの方々に向けた情報を配信しております。
新任の方やベテランの方、管理職を対象とした幅広いコンテンツをご用意しております。
お問い合わせ
コストダウンが利益に直結する術だと理解していても、なかなか前に進めることができない状況。そんな時は、newjiのコストダウン自動化機能で大きく利益貢献しよう!
(Β版非公開)