- お役立ち記事
- Basics and application examples of sintering technology
月間76,176名の
製造業ご担当者様が閲覧しています*
*2025年3月31日現在のGoogle Analyticsのデータより
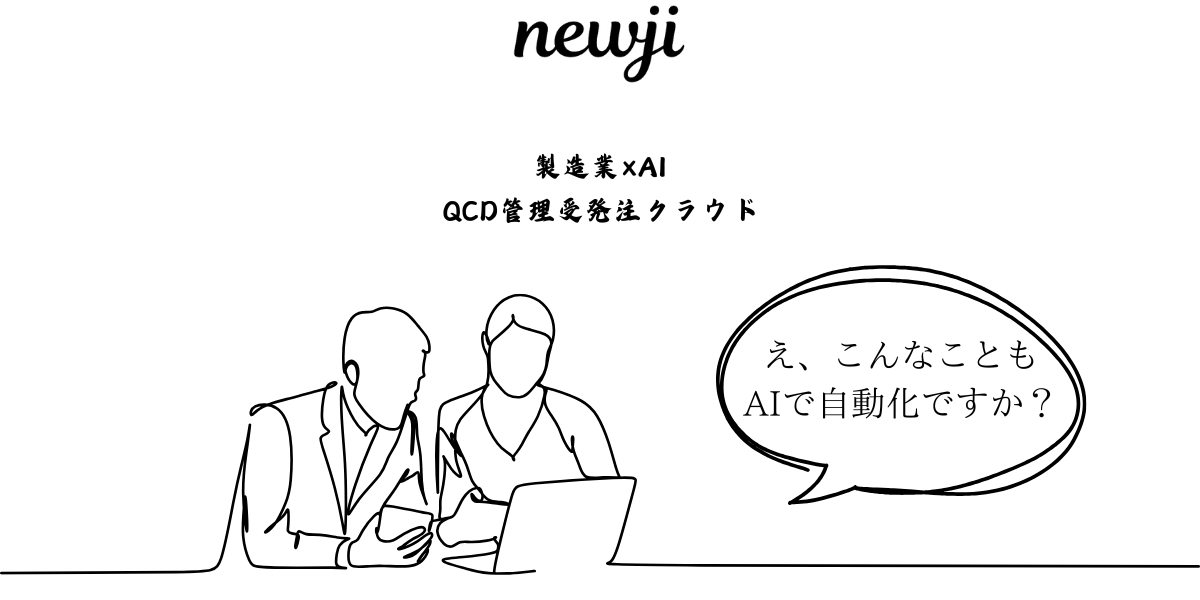
Basics and application examples of sintering technology
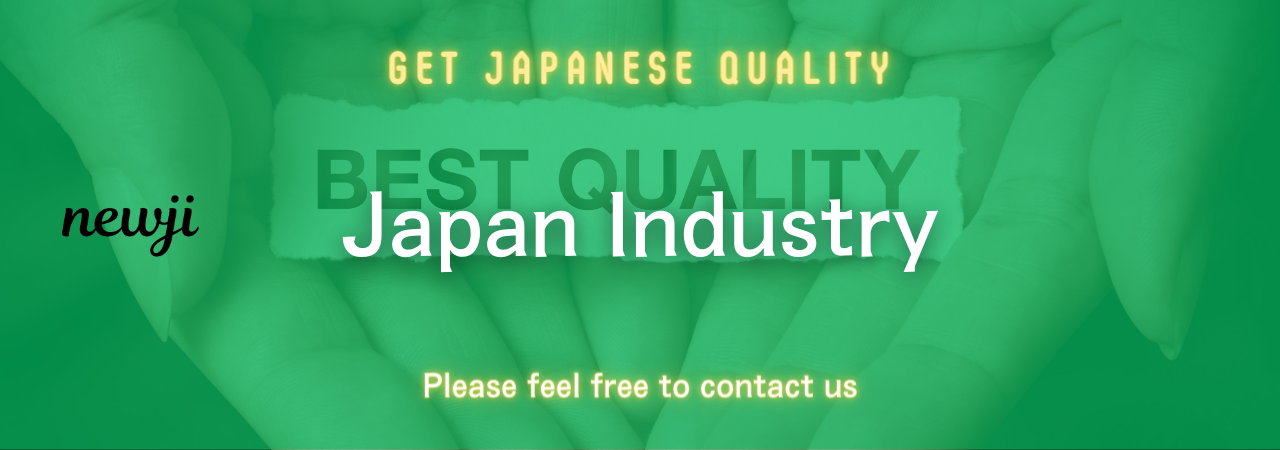
目次
What is Sintering?
Sintering is a fascinating process widely used in various industries to create solid structures from powder materials.
The technique involves heating powdered materials below their melting points until the particles adhere to one another, forming a solid piece.
This method is essential in producing complex shapes and structures that would be difficult or impossible to achieve through traditional melting processes.
The Science Behind Sintering
At its core, sintering is all about manipulating heat to enable particles to bond.
When the powder is heated, the temperature increases the kinetic energy of the particles.
This renewed energy allows them to move closer, occupying the gaps between each other.
As the process continues, particles begin to bond due to high temperature pressure, forming a denser and more robust structure.
The process typically involves three stages: initial bonding, intermediate, and final stage densification.
In the initial stage, particles touch and begin bonding at their contact points.
During the intermediate stage, the pores between the particles shrink as densification occurs.
Finally, in the culminating stage, a dense, solid material forms as most of the pores close.
Different Types of Sintering
Sintering can be done in several ways depending on the materials used and the desired outcome.
Some common types include:
Solid-State Sintering
This method involves compacting and heating a powder to just below its melting point.
Solid-state sintering is widely used for materials that do not have a liquid phase during heating.
Typically used for ceramic and metal powders, this method ensures particles fuse without becoming entirely liquid, resulting in a combined solid mass.
Liquid Phase Sintering
This technique incorporates a secondary material with a lower melting point than the powdered material.
During heating, this secondary material becomes liquid, filling gaps between solid particles and enhancing the overall bonding process.
Liquid phase sintering is crucial in producing tungsten carbide and other alloy materials.
Pressure-Assisted Sintering
For materials requiring additional bonding energy, pressure-assisted sintering combines high pressure with heat to enhance densification and reduce porosity.
This method allows for stronger and more durable materials, often used in fields requiring highly resilient components, such as aerospace and automotive industries.
Applications of Sintering Technology
Sintering is beneficial in many fields due to its ability to produce strong, complex structures.
Here are some of the key applications:
Metal Powder Production
One of the most common applications of sintering is in the production of metal powders.
Sintering enables the creation of precise and intricate metal parts for various industries, including aerospace, automotive, and electronics.
This technique affords superior control over the material’s properties and features, ensuring high-quality and reliable components.
Ceramics and Porous Materials
Sintering is crucial in the production of ceramics and materials with specific porosity levels.
This process allows for creating a wide variety of ceramic items, from simple plates and mugs to more advanced applications like thermal insulators and engine components.
Porous materials sintered this way can also be used for filtration systems, capable of trapping undesirable particles while allowing fluids to pass through.
Powder Metallurgy
Powder metallurgy, an umbrella term that covers a variety of metal-forming techniques, frequently utilizes sintering to manufacture intricate and high-performance metal components.
This practice is vital for producing gears, bearings, and other mechanical components that require precision and strength.
Advantages of Sintering
Sintering technology offers numerous advantages that make it an attractive option for creating complex structures:
Cost-Effectiveness
Sintering allows manufacturers to create complex shapes without the need for costly machining processes.
This results in significant savings on materials and labor, especially when producing high volumes of parts.
Material Efficiency
The sintering process minimizes waste, as the powders used can be recycled or repurposed.
Additionally, this method effectively utilizes materials known for brittleness or difficulty in processing, such as ceramics, without any loss of their unique properties.
Customization and Versatility
The sintering process can be adjusted to produce materials with specific properties and behaviors.
This customization enables the creation of products tailored to specific job requirements or applications.
Conclusion
Sintering technology provides an innovative and efficient way to create solid structures from powders.
With its cost-effectiveness, material efficiency, and ability to produce complex shapes, it is an invaluable tool across many industries.
As technology advances, we can expect further developments in sintering processes, leading to even more versatile and sustainable production methods.
資料ダウンロード
QCD管理受発注クラウド「newji」は、受発注部門で必要なQCD管理全てを備えた、現場特化型兼クラウド型の今世紀最高の受発注管理システムとなります。
ユーザー登録
受発注業務の効率化だけでなく、システムを導入することで、コスト削減や製品・資材のステータス可視化のほか、属人化していた受発注情報の共有化による内部不正防止や統制にも役立ちます。
NEWJI DX
製造業に特化したデジタルトランスフォーメーション(DX)の実現を目指す請負開発型のコンサルティングサービスです。AI、iPaaS、および先端の技術を駆使して、製造プロセスの効率化、業務効率化、チームワーク強化、コスト削減、品質向上を実現します。このサービスは、製造業の課題を深く理解し、それに対する最適なデジタルソリューションを提供することで、企業が持続的な成長とイノベーションを達成できるようサポートします。
製造業ニュース解説
製造業、主に購買・調達部門にお勤めの方々に向けた情報を配信しております。
新任の方やベテランの方、管理職を対象とした幅広いコンテンツをご用意しております。
お問い合わせ
コストダウンが利益に直結する術だと理解していても、なかなか前に進めることができない状況。そんな時は、newjiのコストダウン自動化機能で大きく利益貢献しよう!
(β版非公開)