- お役立ち記事
- Basics and Applications of CIP Molding in Manufacturing
月間76,176名の
製造業ご担当者様が閲覧しています*
*2025年3月31日現在のGoogle Analyticsのデータより
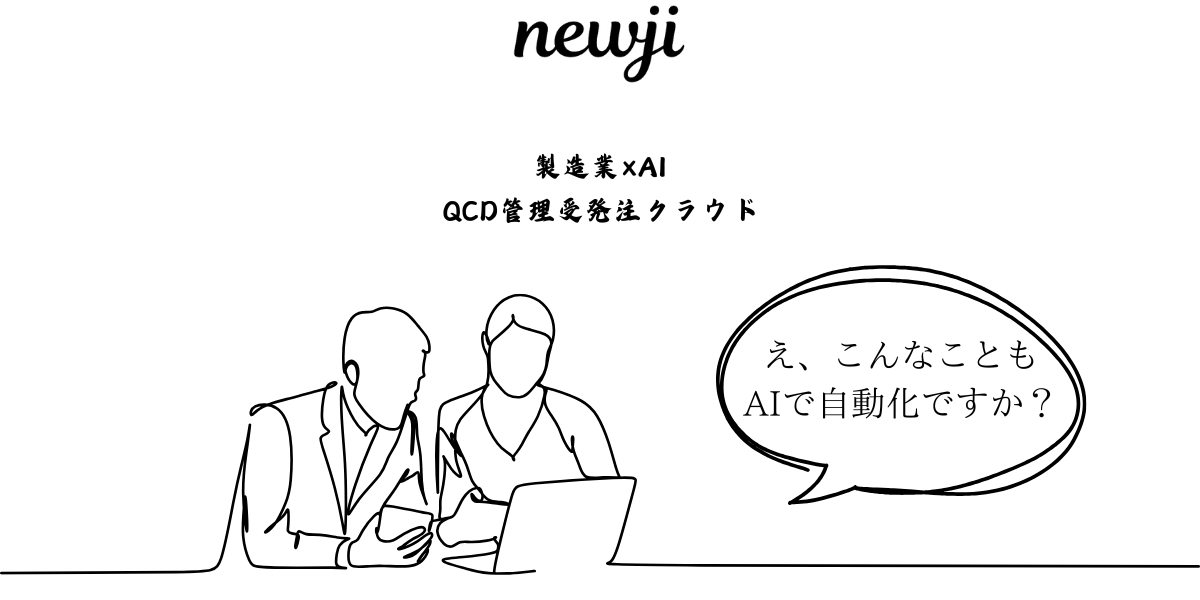
Basics and Applications of CIP Molding in Manufacturing
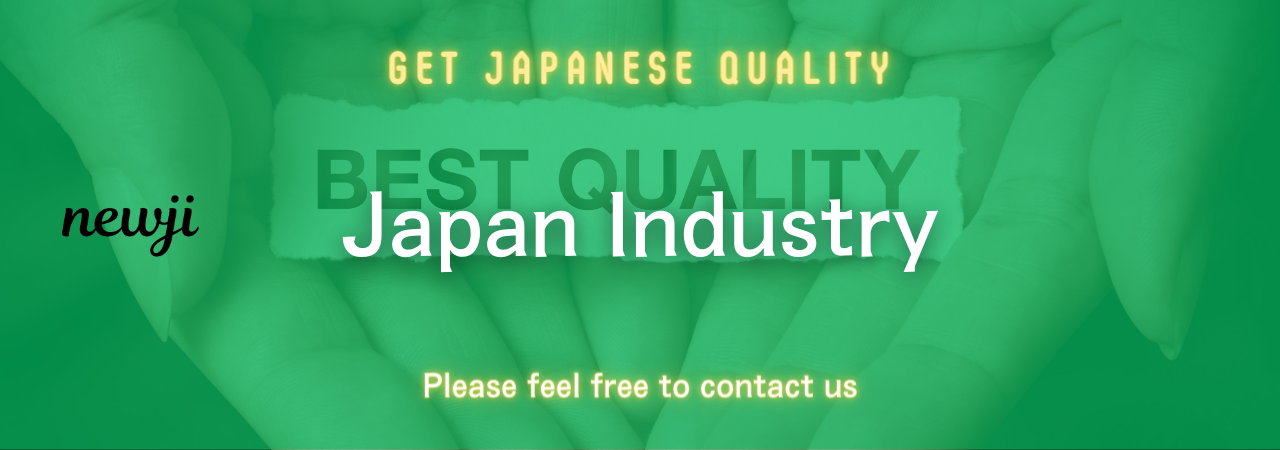
In the world of manufacturing, technology plays a crucial role in shaping how products are created, ensuring efficiency, and meeting the demands of various industries.
One such innovative technique is CIP molding.
Understanding the fundamentals and uses of CIP molding can illuminate why it’s gaining prominence in modern manufacturing.
目次
What is CIP Molding?
CIP, or Cold Isostatic Pressing, is a process used to compress materials into a desired shape at room temperature.
This method involves placing a material in a mold and then applying pressure uniformly in all directions using a fluid medium.
Unlike traditional methods that use heat, CIP mocouplesommonly relies on room or low temperatures to achieve the desired density and form.
This makes it suitable for materials that may degrade or change properties when exposed to high temperatures.
The Basics of CIP Molding
The CIP process generally involves a few crucial steps:
1. **Material Preparation**: The raw material (often in powder form) is prepared for molding.
2. **Mold Loading**: The material is placed into a flexible, often rubber, mold.
3. **Pressure Application**: The mold is then submerged in a fluid medium, usually water or oil, within a high-pressure vessel.
4. **Uniform Compression**: Pressure is applied uniformly from all directions, ensuring consistent density and homogeneity of the molded product.
5. **Demolding**: The applied pressure is released, and the molded part is taken out of the mold for finishing touches if necessary.
Materials Used in CIP Molding
One of the significant advantages of CIP molding is its adaptability to a wide range of materials.
Materials frequently used in CIP molding include ceramics, metals, and composites.
Ceramic powders benefit greatly from CIP molding because the process can produce dense, uniform ceramic parts without defects that might occur if traditional heating methods were used.
For metals, especially brittle or high-melting-point alloys, CIP molding offers a way to create intricate shapes without the risk of melting or distortion.
Additionally, composite materials, which combine different substances to leverage their best qualities, can be effectively molded using the CIP process to ensure they remain stable and robust.
Advantages of CIP Molding
The merits of CIP molding contribute to its increasing adoption in the manufacturing sector.
Here are some key advantages:
Uniformity and Consistency
By applying pressure uniformly, CIP molding ensures that the densification of the material is even throughout the part.
This consistency eliminates weak points and enhances the overall strength and integrity of the finished product.
Ability to Mold Complex Shapes
CIP molding allows for the creation of complex geometries that might be challenging to achieve through conventional methods.
This flexibility is especially valuable in industries requiring precise shapes and dimensions, such as aerospace and automotive sectors.
Enhanced Material Properties
Since the process does not rely on high temperatures, materials that might otherwise degrade or lose desirable properties can retain their optimal characteristics.
CIP molding can enhance properties like hardness, tensile strength, and resistance to wear and tear.
Energy Efficiency
Cold Isostatic Pressing uses room temperature or low temperatures during the molding process, making it more energy-efficient compared to processes that require significant heating.
This not only reduces energy consumption but also minimizes the environmental impact of production.
Applications of CIP Molding
Because of its numerous advantages, CIP molding finds applications across a broad spectrum of industries:
Aerospace
The aerospace industry demands materials with high strength, durability, and resistance to extreme conditions.
CIP molding is employed to produce components like turbine blades, engine parts, and ceramic matrix composites that meet these stringent requirements.
Automotive
In the automotive sector, performance and reliability are paramount.
CIP molding is used to create parts such as gears, bearings, and various other components that need to withstand high stress and wear.
Medical Field
Biocompatible materials and precise dimensions are crucial in medical device manufacturing.
CIP molding is used to produce implants, dental prosthetics, and various other medical tools that require stringent quality control and consistency.
Electronics
In electronics, miniaturization and precision are key.
CIP molding helps create specialized components like sensors, actuators, and insulators that demand high performance and reliability.
Future of CIP Molding in Manufacturing
As technologies advance and industries continue to push the boundaries of what is possible, CIP molding is poised to play an even more prominent role in manufacturing.
Research and development are ongoing to expand the materials and applications for this versatile technique.
Innovations such as the integration of automation and real-time monitoring during the CIP process are likely to enhance its capabilities further.
Automating the CIP Process
Automation could streamline the CIP molding process, increasing efficiency and consistency.
Automated systems can handle precise material measurements, mold loading, and pressure application, reducing human error and improving production speeds.
Smart Manufacturing Integration
Integrating CIP molding with smart manufacturing technologies, such as the Internet of Things (IoT) and data analytics, could offer real-time monitoring and optimization.
These advancements would allow for immediate adjustments to pressures, temperatures, and other variables to ensure optimal product outcomes.
In conclusion, CIP molding is a transformative technique with the potential to redefine manufacturing processes across various industries.
Its ability to produce uniform, high-quality components with complex shapes, while conserving energy and enhancing material properties, makes it an invaluable tool in modern manufacturing.
As the technology evolves, its applications and efficiencies are expected to grow, paving the way for more innovative and sustainable manufacturing practices.
資料ダウンロード
QCD管理受発注クラウド「newji」は、受発注部門で必要なQCD管理全てを備えた、現場特化型兼クラウド型の今世紀最高の受発注管理システムとなります。
ユーザー登録
受発注業務の効率化だけでなく、システムを導入することで、コスト削減や製品・資材のステータス可視化のほか、属人化していた受発注情報の共有化による内部不正防止や統制にも役立ちます。
NEWJI DX
製造業に特化したデジタルトランスフォーメーション(DX)の実現を目指す請負開発型のコンサルティングサービスです。AI、iPaaS、および先端の技術を駆使して、製造プロセスの効率化、業務効率化、チームワーク強化、コスト削減、品質向上を実現します。このサービスは、製造業の課題を深く理解し、それに対する最適なデジタルソリューションを提供することで、企業が持続的な成長とイノベーションを達成できるようサポートします。
製造業ニュース解説
製造業、主に購買・調達部門にお勤めの方々に向けた情報を配信しております。
新任の方やベテランの方、管理職を対象とした幅広いコンテンツをご用意しております。
お問い合わせ
コストダウンが利益に直結する術だと理解していても、なかなか前に進めることができない状況。そんな時は、newjiのコストダウン自動化機能で大きく利益貢献しよう!
(β版非公開)