- お役立ち記事
- Basics and applications of MRP (Material Requirements Planning) that new leaders of production management departments should know
ユーザー企業増加中
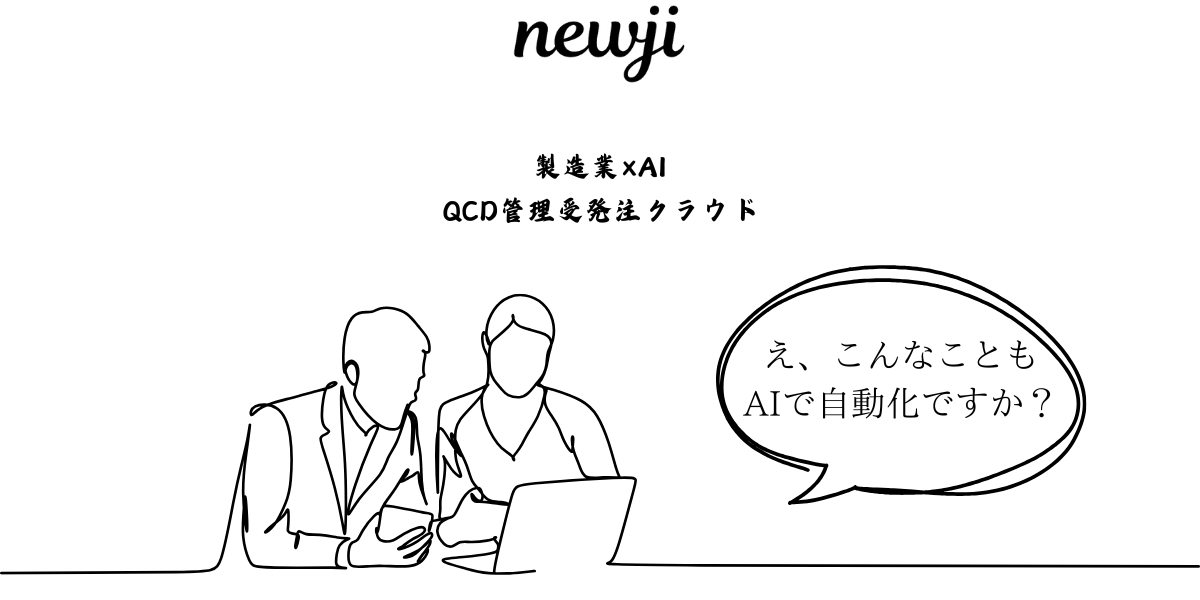
Basics and applications of MRP (Material Requirements Planning) that new leaders of production management departments should know
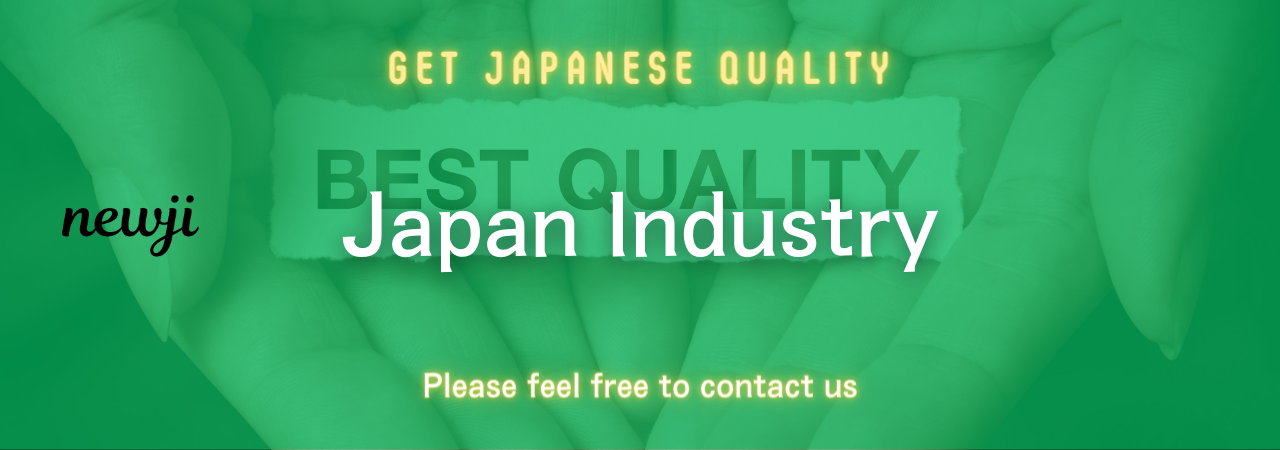
Understanding Material Requirements Planning (MRP)
Material Requirements Planning, or MRP, is an essential system used in the manufacturing industry to manage inventory levels, production scheduling, and planning.
It helps organizations streamline operations, reduce waste, and ensure that the right materials are available at the right time.
Understanding the fundamentals of MRP is crucial for new leaders in production management departments to optimize processes and improve efficiency.
The Basics of MRP
MRP is a computer-based inventory management system that aids production managers in planning and controlling the manufacturing process.
It focuses on three main objectives: ensuring materials and products are available for production and delivery, maintaining the lowest possible material and product levels in stock, and planning manufacturing activities, delivery schedules, and purchasing activities.
The process begins with determining the demand for finished products.
This information is typically derived from forecasts or actual customer orders.
Once the demand is known, the MRP system calculates the materials required to meet that demand by exploding the bill of materials (BOM).
The BOM is a detailed list of all raw materials, components, and assemblies needed to produce a product.
Key Components of MRP
Several critical components form the backbone of MRP:
1. **Master Production Schedule (MPS)**: This is a plan for individual commodities to be produced in each time period, such as production, staffing, inventory, etc.
2. **Bill of Materials (BOM)**: It is a comprehensive list of raw materials, components, and assemblies required to build a product. The BOM acts as a recipe for manufacturing that guides the MRP system in inventory planning.
3. **Inventory Status File**: This component keeps a record of the stock level of each material. It informs the MRP system of the current inventory status, including what is on hand, what has been ordered, and what is arriving.
4. **Lead Time**: This is the time required to procure or produce an item. The MRP system uses lead times to schedule production and purchase orders.
The Importance of Accurate Data
Accuracy in data is paramount for the effectiveness of an MRP system.
Any erroneous information regarding inventory levels, BOM accuracy, or forecast demand can lead to inefficiencies such as stockouts, excess inventory, or delayed production.
Therefore, maintaining up-to-date and accurate data is crucial for MRP to function properly.
The Role of MRP in Production Management
MRP plays a pivotal role in production management by offering several benefits:
– **Improved Inventory Control**: MRP helps in maintaining the right balance of stock levels. By calculating the exact needs based on demand forecasts and BOM explosions, it reduces the chances of overstocking or stockouts.
– **Reduced Lead Times**: With organized scheduling and planning, the production process becomes more streamlined, reducing the time it takes from the start of manufacturing to product delivery.
– **Cost Savings**: By optimizing inventory levels and production schedules, MRP can significantly reduce waste and unnecessary costs associated with storing excess inventory.
– **Enhanced Customer Satisfaction**: Meeting the exact demand without delays and fulfilling orders promptly enhances customer satisfaction and fosters stronger business relationships.
Implementing MRP in the Production Management Department
For new leaders in production management, implementing an MRP system involves several steps:
1. **Assess Current Processes**: Evaluate the existing production processes, inventory systems, and supply chain to identify areas for improvement.
2. **Select the Right MRP Software**: Choose a software that integrates well with your current systems and meets your specific production needs.
3. **Data Collection and Input**: Gather accurate and comprehensive data related to inventory, demand forecasts, and BOM.
4. **Staff Training**: Train employees on how to utilize the MRP system effectively. Proper training ensures that everyone understands their role in the process.
5. **Regular Monitoring and Updates**: Continuously monitor the system’s performance and update the data regularly to reflect changes in demand or production processes.
Applications of MRP Beyond Production
While MRP is primarily used in manufacturing, its principles can be applied in various other areas:
– **Supply Chain Management**: MRP helps in coordinating with suppliers and managing the procurement of materials, thus improving the entire supply chain process.
– **Project Management**: The systematic planning and scheduling approach of MRP can be applied to project management to ensure that projects are completed on time and within budget.
– **Service Industry**: MRP can help companies that maintain a significant inventory of parts for maintenance operations in services such as health care, IT, and telecommunication.
Challenges and Considerations
Despite its benefits, new leaders should be aware of certain challenges associated with MRP implementation:
– **Complexity**: MRP systems can be complex, requiring thorough understanding and management to ensure they function optimally.
– **Initial Costs**: The initial cost of implementing an MRP system can be high, but the long-term savings and efficiency gains often outweigh these costs.
– **System Integration**: Ensuring that the MRP system integrates seamlessly with other systems within the organization can be challenging.
Conclusion
For new leaders stepping into production management roles, understanding the basics and applications of Material Requirements Planning is vital.
An effective MRP system not only streamlines production processes but also enhances inventory management, reduces costs, and improves customer satisfaction.
By focusing on accurate data input, regular system monitoring, and continuous improvement, MRP can become an invaluable tool in achieving operational excellence within any manufacturing organization.
資料ダウンロード
QCD調達購買管理クラウド「newji」は、調達購買部門で必要なQCD管理全てを備えた、現場特化型兼クラウド型の今世紀最高の購買管理システムとなります。
ユーザー登録
調達購買業務の効率化だけでなく、システムを導入することで、コスト削減や製品・資材のステータス可視化のほか、属人化していた購買情報の共有化による内部不正防止や統制にも役立ちます。
NEWJI DX
製造業に特化したデジタルトランスフォーメーション(DX)の実現を目指す請負開発型のコンサルティングサービスです。AI、iPaaS、および先端の技術を駆使して、製造プロセスの効率化、業務効率化、チームワーク強化、コスト削減、品質向上を実現します。このサービスは、製造業の課題を深く理解し、それに対する最適なデジタルソリューションを提供することで、企業が持続的な成長とイノベーションを達成できるようサポートします。
オンライン講座
製造業、主に購買・調達部門にお勤めの方々に向けた情報を配信しております。
新任の方やベテランの方、管理職を対象とした幅広いコンテンツをご用意しております。
お問い合わせ
コストダウンが利益に直結する術だと理解していても、なかなか前に進めることができない状況。そんな時は、newjiのコストダウン自動化機能で大きく利益貢献しよう!
(Β版非公開)