- お役立ち記事
- Basics and applications of quality function development (QFD) that new employees in the research and development department of the cosmetics manufacturing industry should know.
Basics and applications of quality function development (QFD) that new employees in the research and development department of the cosmetics manufacturing industry should know.
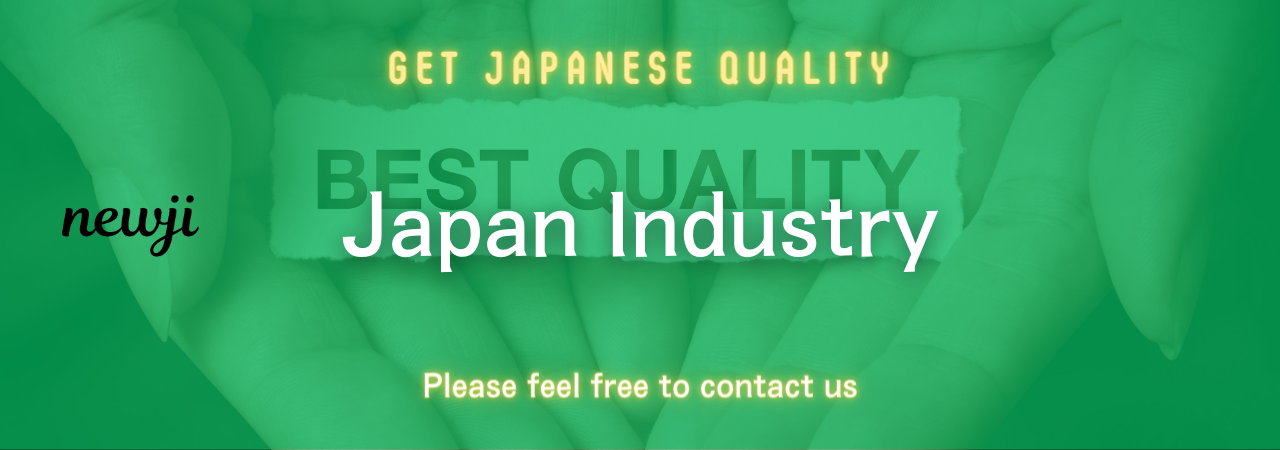
目次
Understanding Quality Function Deployment (QFD)
Quality Function Deployment (QFD) is a systematic process used by many industries, including the cosmetics manufacturing industry, to transform customer needs into engineering characteristics for a product.
It helps in identifying and prioritizing customer requirements, translating these into specific plans to produce products that meet those needs.
New employees in the research and development department play a pivotal role in understanding and applying QFD to ensure that the final product delivers the desired quality and satisfaction to the customers.
Quality Function Deployment is implemented through various tools and techniques, the most popular being the House of Quality.
It serves as a visual model of customer desires and technical descriptors.
By utilizing QFD, organizations streamline the design process and make sure that the customer is at the heart of every decision, leading to enhanced customer satisfaction and improved product quality.
The Five Phases of QFD
To effectively implement QFD, it’s essential to understand its five primary phases.
1. Product Planning
This initiates with collecting customer requirements, often referred to as the “Voice of the Customer” (VOC).
It includes understanding customer needs, expectations, and preferences.
In the cosmetics industry, this might involve identifying trends, customer feedback, and competitive product analysis.
Gathering this information helps in mapping out the critical customer requirements, which are then ranked in terms of importance.
These requirements form the foundation of your QFD analysis.
2. Product Design
The next step in QFD is converting the voice of the customer into specific product design attributes.
For a cosmetics manufacturer, this might involve choosing materials that are skin-friendly, sustainable, and align with customer demand for cruelty-free products.
In this phase, cross-functional teams collaborate to ensure that these design attributes are feasible and align with customer expectations.
Potential challenges are identified, and solutions are brainstormed to ensure a balance between customer desires and technical feasibility.
3. Process Planning
Once the product design attributes are established, the focus shifts to process planning.
Here, the objective is to determine how the product will be produced, highlighting the critical processes necessary to achieve the desired product attributes.
For new research and development employees, understanding how different processes affect the final product’s quality is crucial.
This includes selecting appropriate technologies, methodologies, and process parameters that maintain the product’s integrity and effectiveness.
4. Process Control
During this phase, controls are put in place to ensure that the manufacturing processes consistently produce products that meet design specifications.
Monitoring processes through statistical methods is common to ensure quality is maintained.
In the cosmetics industry, particular attention is paid to maintaining the quality of formulations, shelf life, and safety standards.
Process control ensures that any variations in product quality are minimized and promptly addressed.
5. Continuous Improvement
QFD is not a one-time process but a continuous cycle of improvement.
Even after a product is launched, customer feedback, market trends, and technological advancements necessitate ongoing enhancements.
New employees must stay informed about emerging trends, such as the increasing demand for organic and sustainable products, to adapt product offerings and processes accordingly.
Continuous improvement involves revisiting earlier phases of QFD to incorporate these changes, ensuring ongoing alignment with customer expectations.
Applications of QFD in the Cosmetics Industry
In the cosmetics manufacturing industry, QFD plays a critical role in both product innovation and existing product refinement.
New Product Development
Using QFD in new product development ensures that new cosmetics like creams, lotions, or makeup products meet consumer demands from conception to launch.
By focusing on what consumers value most, companies can better tailor their offerings to match those expectations effectively.
Enhancing Existing Products
QFD provides a structured approach to gathering data on existing products and identifying areas of enhancement, such as improving formula efficacy or packaging design.
This process aids in product differentiation in a competitive market, ensuring that existing products remain desirable to consumers.
Boosting Customer Satisfaction
By placing the customer’s voice at the core of the development process, QFD enhances customer satisfaction.
As a result, cosmetics companies can deliver products that aren’t just innovative but closely aligned with customer needs, building strong brand loyalty.
Challenges and Solutions in Implementing QFD
While QFD offers numerous benefits, its implementation also comes with challenges.
One challenge is accurately capturing the Voice of the Customer, especially when preferences are diverse and constantly changing.
Solution: Effective Communication Channels
Developing effective communication channels with customers can facilitate gathering more precise data.
Using surveys, focus groups, and social media analytics can provide actionable insights.
Another challenge is integrating QFD into existing processes without disrupting workflow.
Solution: Incremental Implementation
Implement QFD incrementally to allow for smooth adoption into existing processes.
Start by applying QFD to a smaller project before scaling up across larger endeavors.
Conclusion
For new employees in a cosmetics manufacturing research and development department, understanding and utilizing Quality Function Deployment is vital.
It ensures that the products developed resonate with customer demands and stand out in the competitive market.
By systematically translating customer needs into every phase of product development, QFD helps maintain high-quality standards, boosts customer satisfaction, and supports continuous product innovation and improvement.
Embracing QFD not only hones skills in product development but also contributes significantly to the overall success of the organization in delivering products that fulfill the needs and expectations of their valued customers.
資料ダウンロード
QCD調達購買管理クラウド「newji」は、調達購買部門で必要なQCD管理全てを備えた、現場特化型兼クラウド型の今世紀最高の購買管理システムとなります。
ユーザー登録
調達購買業務の効率化だけでなく、システムを導入することで、コスト削減や製品・資材のステータス可視化のほか、属人化していた購買情報の共有化による内部不正防止や統制にも役立ちます。
NEWJI DX
製造業に特化したデジタルトランスフォーメーション(DX)の実現を目指す請負開発型のコンサルティングサービスです。AI、iPaaS、および先端の技術を駆使して、製造プロセスの効率化、業務効率化、チームワーク強化、コスト削減、品質向上を実現します。このサービスは、製造業の課題を深く理解し、それに対する最適なデジタルソリューションを提供することで、企業が持続的な成長とイノベーションを達成できるようサポートします。
オンライン講座
製造業、主に購買・調達部門にお勤めの方々に向けた情報を配信しております。
新任の方やベテランの方、管理職を対象とした幅広いコンテンツをご用意しております。
お問い合わせ
コストダウンが利益に直結する術だと理解していても、なかなか前に進めることができない状況。そんな時は、newjiのコストダウン自動化機能で大きく利益貢献しよう!
(Β版非公開)