- お役立ち記事
- Basics and applications of ultrasonic flaw detection technology that new employees in the quality control department of the aircraft parts manufacturing industry should learn
月間76,176名の
製造業ご担当者様が閲覧しています*
*2025年3月31日現在のGoogle Analyticsのデータより
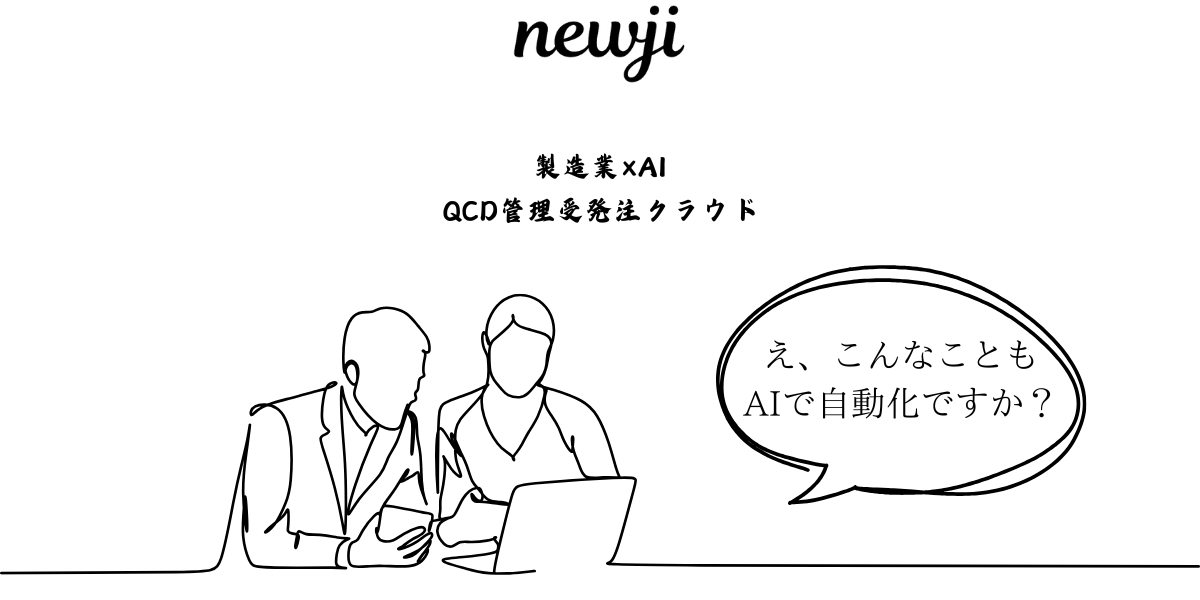
Basics and applications of ultrasonic flaw detection technology that new employees in the quality control department of the aircraft parts manufacturing industry should learn
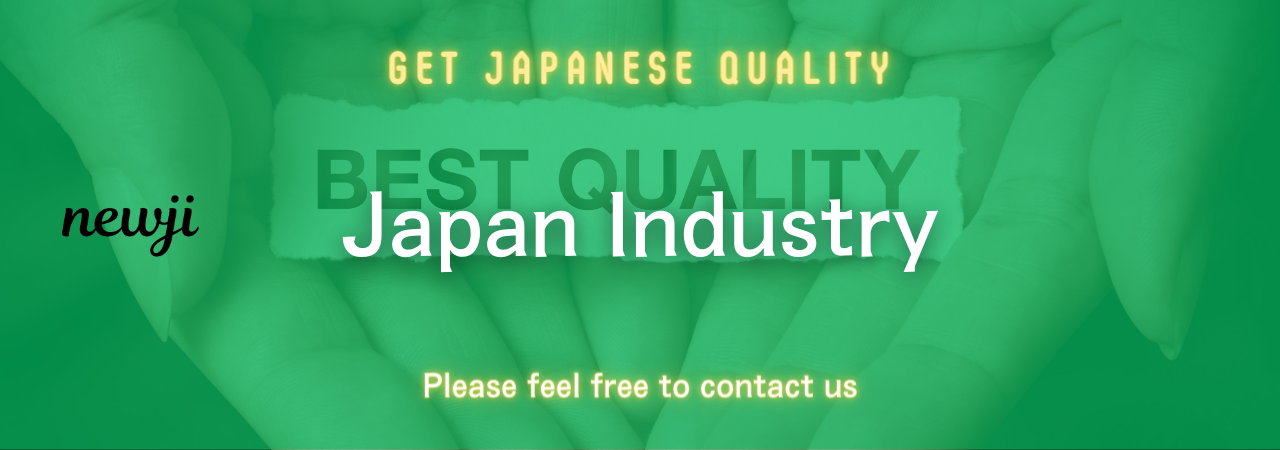
目次
Understanding Ultrasonic Flaw Detection
Ultrasonic flaw detection is an essential technology in the quality control department, especially for industries like aircraft parts manufacturing.
It involves using high-frequency sound waves to detect imperfections or discontinuities in materials.
This non-destructive testing (NDT) method is crucial as it ensures the safety and reliability of aircraft components, which must adhere to stringent quality standards.
How Ultrasonic Flaw Detection Works
At its core, ultrasonic flaw detection relies on sound waves that are beyond the range of human hearing.
These sound waves, typically with frequencies ranging from 500 kHz to 10 MHz, penetrate solid materials and are reflected back if they encounter any flaws.
A device called a transducer emits these sound waves and receives the echoes that bounce back.
The time it takes for the echoes to return, along with the amplitude, helps identify the size, location, and nature of any imperfections.
Components of Ultrasonic Flaw Detection Equipment
The equipment used in ultrasonic flaw detection consists of several key components:
1. **Transducer**: This is the part of the equipment that generates and receives sound waves.
It’s specially designed to handle high-frequency waves.
2. **Pulser/Receiver**: The pulser generates electrical pulses that are converted into ultrasonic waves by the transducer.
The receiver amplifies the returned echoes for analysis.
3. **Display Unit**: Often an oscilloscope or digital screen, this unit displays the waveforms of the echoes.
Operators interpret these waveforms to identify potential flaws.
4. **Calibration Block**: This standard block with known dimensions and materials is used to calibrate the system.
It ensures the equipment is accurate before testing actual parts.
The Importance of Ultrasonic Flaw Detection
In the aircraft parts manufacturing industry, ensuring component integrity is paramount.
Ultrasonic flaw detection offers several benefits that bolster quality assurance:
Non-Destructive Testing
One of the primary advantages is that ultrasonic testing is non-destructive.
This means the parts remain undamaged and usable after inspection.
Non-destructive testing is especially valuable for expensive components where replacement costs would be significant.
Detecting Subsurface Flaws
Ultrasonic testing can detect subsurface and internal defects that other methods might miss.
This is crucial in the aircraft industry, where even minor flaws can lead to significant safety risks.
Versatility and Precision
Ultrasonic flaw detection can be used on a wide range of materials, including metals, plastics, and composites.
It provides precise measurements, which help in identifying even the smallest of defects.
Training and Skills for New Employees
For new employees in the quality control department, understanding the basics of ultrasonic flaw detection is vital.
Here’s how they can get started:
Technical Training
New employees should undergo comprehensive training sessions to understand the theory and application of ultrasonic flaw detection.
This includes learning about sound wave behavior, equipment handling, and data interpretation.
Hands-On Experience
Theory alone is not enough.
Practical experience with the equipment is essential.
Employees should practice on calibration blocks and gradually move to actual parts under supervision.
Understanding Standards and Protocols
Familiarity with industry standards and protocols is crucial.
New employees should be aware of the regulatory requirements for aircraft part inspections to ensure compliance.
Real-World Applications
Ultrasonic flaw detection is used in various ways within aircraft manufacturing:
Inspection of Welded Joints
Welded joints are critical points in aircraft structures.
Ultrasonic testing checks for any voids or imperfections in these joints, ensuring structural integrity.
Composite Material Evaluation
Modern aircraft use composite materials for weight reduction.
Ultrasonic testing is ideal for inspecting these materials for delaminations or other defects.
Thickness Measurements
Over time, aircraft components can thin due to corrosion or wear.
Ultrasonic flaw detection helps regularly measure and monitor the thickness of critical parts.
The Future of Ultrasonic Flaw Detection
As technology advances, ultrasonic flaw detection is also evolving.
Here are some trends to watch:
Automation
Automated ultrasonic testing systems can increase efficiency, reduce human error, and handle larger volumes of inspections.
Advanced Data Analysis
With the integration of AI and machine learning, data analysis from ultrasonic inspections will become more accurate and faster.
Portable Units
The development of smaller, portable units makes on-site inspections easier, allowing for more flexibility in testing locations.
Conclusion
Understanding ultrasonic flaw detection is crucial for new employees in the quality control departments of aircraft parts manufacturing.
This technology not only ensures the structural integrity of parts but also aligns with industry safety standards.
Emphasizing rigorous training and staying informed about advancements will prepare employees to effectively use this technology, enhancing both their career prospects and the safety of air travel.
資料ダウンロード
QCD管理受発注クラウド「newji」は、受発注部門で必要なQCD管理全てを備えた、現場特化型兼クラウド型の今世紀最高の受発注管理システムとなります。
ユーザー登録
受発注業務の効率化だけでなく、システムを導入することで、コスト削減や製品・資材のステータス可視化のほか、属人化していた受発注情報の共有化による内部不正防止や統制にも役立ちます。
NEWJI DX
製造業に特化したデジタルトランスフォーメーション(DX)の実現を目指す請負開発型のコンサルティングサービスです。AI、iPaaS、および先端の技術を駆使して、製造プロセスの効率化、業務効率化、チームワーク強化、コスト削減、品質向上を実現します。このサービスは、製造業の課題を深く理解し、それに対する最適なデジタルソリューションを提供することで、企業が持続的な成長とイノベーションを達成できるようサポートします。
製造業ニュース解説
製造業、主に購買・調達部門にお勤めの方々に向けた情報を配信しております。
新任の方やベテランの方、管理職を対象とした幅広いコンテンツをご用意しております。
お問い合わせ
コストダウンが利益に直結する術だと理解していても、なかなか前に進めることができない状況。そんな時は、newjiのコストダウン自動化機能で大きく利益貢献しよう!
(β版非公開)