- お役立ち記事
- Basics and Effective Utilization of FMEA and DRBFM
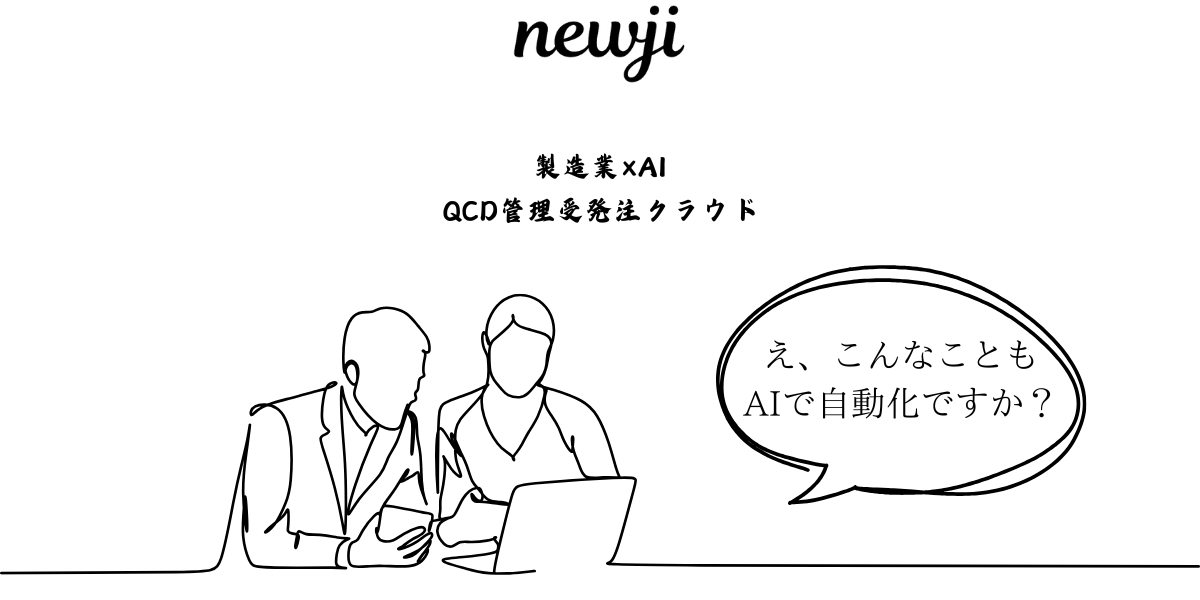
Basics and Effective Utilization of FMEA and DRBFM
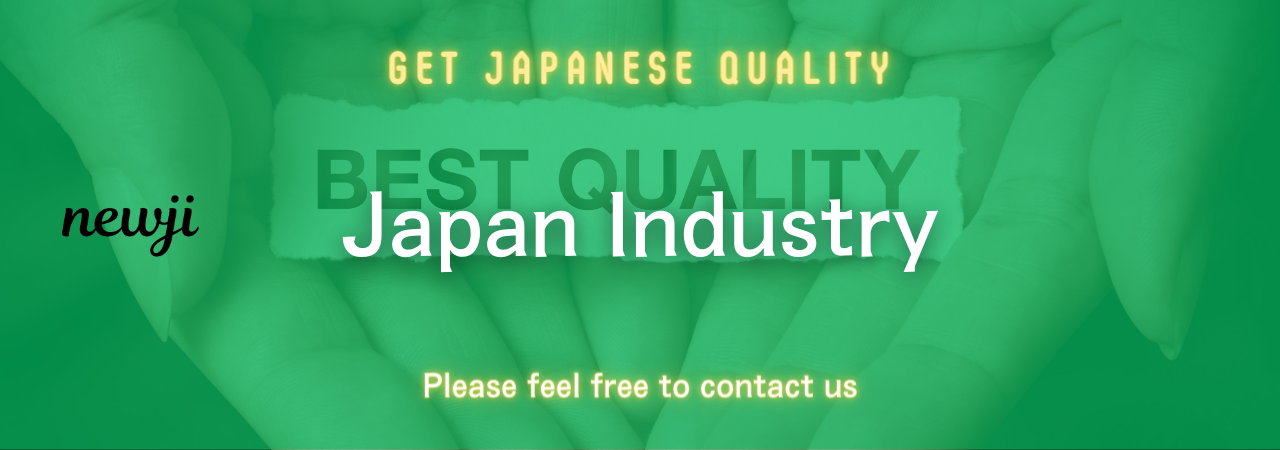
目次
Understanding FMEA
Failure Modes and Effects Analysis (FMEA) is a systematic method for evaluating processes to identify where and how they might fail and assessing the relative impact of different failures.
The objective of FMEA is to anticipate potential problems early in the development process, before they become actual issues.
By identifying the various ways a product or process can fail, organizations can prioritize which parts need improvement and take corrective or preventive actions accordingly.
FMEA is widely used across various industries, including automotive, aerospace, healthcare, and manufacturing, due to its effectiveness in mitigating risks associated with product and process failures.
Types of FMEA
There are mainly two types of FMEA: Design FMEA (DFMEA) and Process FMEA (PFMEA).
DFMEA focuses on potential failures in the design phase and aims to identify design shortcomings before they are released for production.
Its goal is to enhance product reliability and safety.
PFMEA, on the other hand, evaluates failures in the manufacturing and assembly process, aiming to reduce process-related defects.
Both DFMEA and PFMEA follow similar steps, though their focus varies depending on the point of application.
Steps to Conduct FMEA
Conducting FMEA involves several steps:
1. **Identify the process or product**: Begin by selecting the process or system you will analyze.
2. **List possible failure modes**: For each process step, brainstorm potential failure modes.
3. **Assess the effects of each failure**: Determine the impact of each failure on the overall system or product.
4. **Prioritize failures**: Use a risk priority number (RPN) or similar metric to prioritize failures based on their severity, occurrence, and detectability.
5. **Recommend corrective actions**: Develop measures to reduce the risk of high-priority failures.
6. **Implement and review**: Apply corrective actions and monitor their effectiveness over time.
Exploring DRBFM
Design Review Based on Failure Mode (DRBFM) is an advanced process that has its roots in FMEA, with a focus on intensive analysis of changes.
Created in the automotive industry by Toyota, DRBFM emphasizes rigorous examination of even the smallest change in a design.
Its core objective is to ensure that all potential issues resulting from these changes are thoroughly reviewed and rectified.
DRBFM is particularly useful when updating existing products or processes, where changes can introduce new risks.
DRBFM vs. FMEA
While FMEA focuses broadly on identifying and mitigating risks in design and processes, DRBFM narrows the focus to changes within a system, analyzing potential risks these alterations might introduce.
DRBFM is proactive in nature, often implemented as a detailed follow-up to FMEA findings, contributing to an enhanced approach to process improvement.
Whereas FMEA offers a holistic risk assessment, DRBFM drills down into specific issues, facilitating targeted problem-solving.
Steps to Perform DRBFM
Like FMEA, DRBFM follows a structured approach:
1. **Change Point Identification**: Identify specific points within a design or process where changes have been made or are proposed.
2. **Engineering Analysis**: Evaluate these changes to understand their impact, identifying new potential failure modes.
3. **Brainstorming Sessions**: Collaborate with cross-functional teams to discuss and analyze potential failures introduced by the changes.
4. **D-Ring Evaluation**: Use a DRBFM worksheet or “D-Ring” to prioritize and document potential risks, similar to the RPN concept in FMEA.
5. **Review and Validate**: Review proposed solutions, ensure they address potential failures comprehensively, and validate their effectiveness.
The Synergy Between FMEA and DRBFM
While FMEA and DRBFM serve distinct functions, they are most effective when used in combination.
FMEA provides the groundwork by thoroughly analyzing and identifying risks within a design or process.
DRBFM takes this analysis deeper, especially when changes are imminent, ensuring that modifications do not introduce unanticipated issues.
Utilizing both methodologies ensures robust quality control and risk management in the product lifecycle.
Through the integration of FMEA and DRBFM, organizations can achieve higher levels of safety, reliability, and efficiency.
Effective Utilization in Industries
Many industries have seen significant improvements by effectively utilizing FMEA and DRBFM in tandem.
In the automotive sector, for instance, these tools are crucial for safety-critical components, ensuring all potential failures are addressed before vehicles reach the market.
The aerospace industry benefits from these methodologies to meet stringent safety regulations and minimize the risk of in-flight failures.
Healthcare companies also adopt FMEA and DRBFM to improve the reliability and safety of medical devices, ultimately enhancing patient care.
Best Practices for Implementing FMEA and DRBFM
1. **Cross-functional Involvement**: Engage diverse teams from various departments to ensure all angles of potential failures are considered.
2. **Continuous Training**: Provide regular training to your teams to keep them updated on the latest tools and techniques in risk analysis.
3. **Documentation**: Maintain thorough documentation of both FMEA and DRBFM findings to support continuous improvement efforts.
4. **Regular Reviews**: Reassess FMEA and DRBFM at regular intervals, especially after significant process or design changes, to ensure ongoing effectiveness.
5. **Integrate Feedback Loops**: Use feedback loops to capture lessons learned and refine both methodologies over time.
By following these best practices, organizations can harness the full potential of FMEA and DRBFM.
These methodologies not only help in identifying potential risks early but also provide a structured way to manage and mitigate them effectively, leading to enhanced product quality and customer satisfaction.
資料ダウンロード
QCD調達購買管理クラウド「newji」は、調達購買部門で必要なQCD管理全てを備えた、現場特化型兼クラウド型の今世紀最高の購買管理システムとなります。
ユーザー登録
調達購買業務の効率化だけでなく、システムを導入することで、コスト削減や製品・資材のステータス可視化のほか、属人化していた購買情報の共有化による内部不正防止や統制にも役立ちます。
NEWJI DX
製造業に特化したデジタルトランスフォーメーション(DX)の実現を目指す請負開発型のコンサルティングサービスです。AI、iPaaS、および先端の技術を駆使して、製造プロセスの効率化、業務効率化、チームワーク強化、コスト削減、品質向上を実現します。このサービスは、製造業の課題を深く理解し、それに対する最適なデジタルソリューションを提供することで、企業が持続的な成長とイノベーションを達成できるようサポートします。
オンライン講座
製造業、主に購買・調達部門にお勤めの方々に向けた情報を配信しております。
新任の方やベテランの方、管理職を対象とした幅広いコンテンツをご用意しております。
お問い合わせ
コストダウンが利益に直結する術だと理解していても、なかなか前に進めることができない状況。そんな時は、newjiのコストダウン自動化機能で大きく利益貢献しよう!
(Β版非公開)