- お役立ち記事
- Basics and Implementation Methodology of Business Process Management (BPM) in Manufacturing
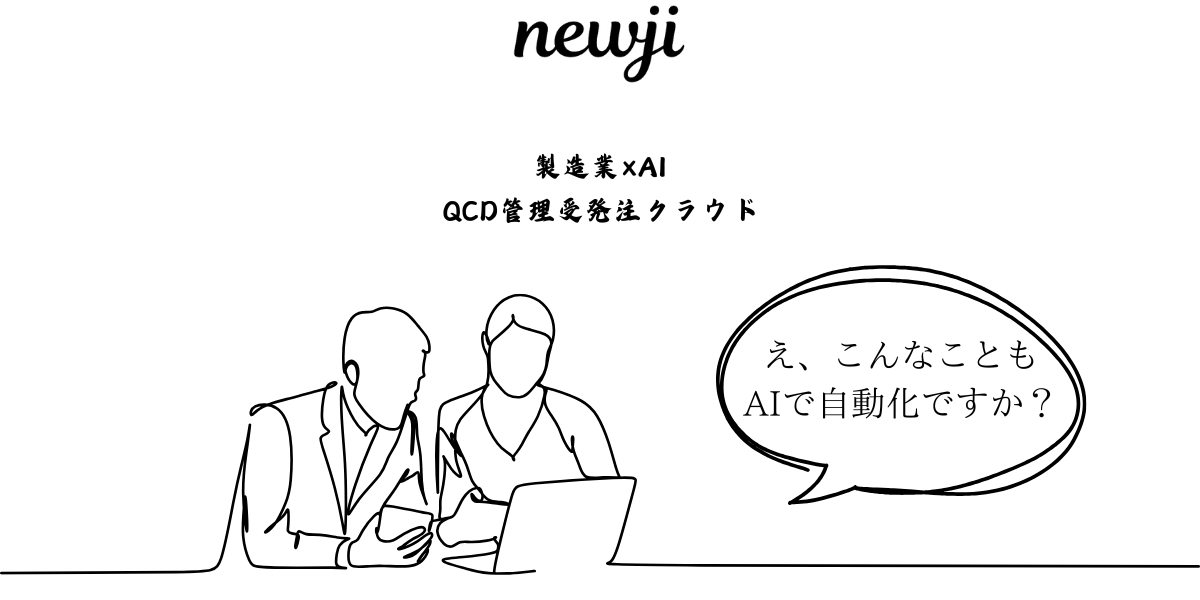
Basics and Implementation Methodology of Business Process Management (BPM) in Manufacturing
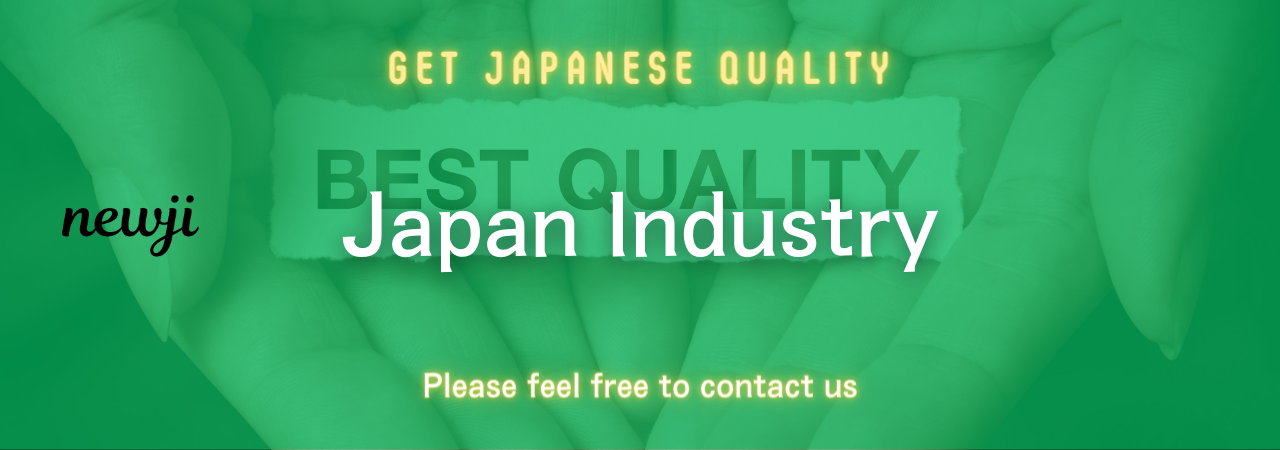
In the complex world of manufacturing, optimizing processes and improving efficiency are pivotal for success.
Business Process Management (BPM) stands as a crucial strategy to align resources, workflows, and technology in a way that enhances overall productivity and performance.
Let’s dive into the basics and implementation methodology of BPM in manufacturing.
目次
What is Business Process Management (BPM)?
Business Process Management refers to a systematic approach to making an organization’s processes more effective and efficient.
It involves analyzing existing processes, identifying areas for improvement, and implementing changes to achieve greater efficiency.
BPM is not a one-time initiative but an ongoing practice aimed at continuous improvement.
Core Components of BPM
To understand BPM fully, let’s break it down into its core components:
1. **Modeling:** This involves mapping out current processes to get a clear understanding of workflows and sub-processes.
2. **Analysis:** Identifying inefficiencies and root causes of bottlenecks in the supply chain.
3. **Design:** Crafting updated or new processes that eliminate these inefficiencies.
4. **Implementation:** Putting the new processes into action using tools like software or automation technologies.
5. **Monitoring:** Continuously tracking the performance of the implemented processes to ensure they are yielding the desired outcomes.
6. **Optimization:** Making continual adjustments based on performance metrics and feedback.
Importance of BPM in Manufacturing
Manufacturing involves numerous interconnected processes, from procurement to production to distribution.
BPM helps streamline these workflows, ensuring smoother transitions between different stages of production.
Enhanced Efficiency
By adopting BPM, manufacturers can eliminate unnecessary steps, reduce waste, and minimize production times.
This leads to a more straightforward and agile production line capable of responding swiftly to market demands.
Quality Assurance
Standardized processes ensure that products are manufactured consistently, adhering to quality standards set by the company or regulatory bodies.
This standardization helps in reducing defects and ensuring a high level of customer satisfaction.
Cost Reduction
Optimized processes mean less resource wastage, be it raw materials, energy, or labor.
This reduction in resource use directly translates to cost savings, thus improving the bottom line.
Implementation Methodology of BPM in Manufacturing
Successfully implementing BPM requires a structured approach.
Here’s a detailed, step-by-step methodology to guide you through the process.
Step 1: Define Objectives
Start by outlining the goals you want to achieve through BPM.
These could range from reducing production times to improving product quality or enhancing customer satisfaction.
Clear objectives will serve as a roadmap for your BPM journey.
Step 2: Process Mapping
Next, map out all current processes in the manufacturing lifecycle.
Use flowcharts or BPM software to create a detailed picture of existing workflows.
This step is crucial for identifying areas where improvements can be made.
Step 3: Identify Bottlenecks
Analyze the process maps to find inefficiencies and bottlenecks that hinder productivity.
Whether it’s a manual step that can be automated or a stage that continually causes delays, identifying these pain points is vital for subsequent improvements.
Step 4: Redesign Processes
Based on your analysis, design new processes that eliminate the identified inefficiencies.
Involve key stakeholders during this stage to ensure the redesigned processes are practical and effective.
Step 5: Select BPM Tools
Choose appropriate BPM tools and software that can help in automating and monitoring the new processes.
The right tools will depend on the complexity of the processes and the specific needs of your manufacturing setup.
Step 6: Implementation
Roll out the new processes gradually, starting with a pilot phase.
This allows you to test and refine the changes before a full-scale implementation.
Training employees on the new workflows is crucial to ensure smooth transition and adoption.
Step 7: Monitor Performance
Use key performance indicators (KPIs) to continuously monitor the effectiveness of the new processes.
This could include metrics like production time, defect rates, or customer satisfaction scores.
Monitoring helps in identifying if further tweaks are necessary.
Step 8: Continual Improvement
BPM is an ongoing effort, not a one-time project.
Use insights gained from performance monitoring to make continual adjustments and improvements.
This will help you maintain optimal efficiency and adapt to any changes in market conditions.
Challenges in BPM Implementation
While BPM offers numerous benefits, it also comes with its set of challenges.
Resistance to Change
Employees may resist changes to established workflows, fearing job displacement or increased complexity.
Addressing this requires effective change management strategies, including transparent communication and employee training.
Cost
Implementing BPM often requires investment in new software tools and training programs.
While the long-term benefits outweigh these costs, initial expenses can be a barrier for some organizations.
Complexity
Manufacturing processes can be highly complex, involving multiple stakeholders and phases.
This complexity can make BPM implementation a daunting task, requiring precise planning and execution.
Case Study: BPM in Action
Let’s consider a real-world example to see BPM in action.
A car manufacturing company was struggling with prolonged production cycles and high defect rates.
Objective
Their primary objective was to reduce production times by 20% and defect rates by 15%.
Process Mapping and Analysis
They started by mapping out their existing manufacturing processes.
The analysis revealed several bottlenecks, especially in the quality control phase and the supply chain management.
Redesigning and Implementing
New processes were designed, including automated quality checks and real-time inventory tracking using IoT devices.
These changes were implemented in phases, starting with pilot runs.
Outcome
Within six months, the company saw a 28% reduction in production times and a 20% decrease in defect rates.
Employee training sessions ensured smooth adoption of the new processes, contributing to overall success.
In summary, Business Process Management is indispensable for modern manufacturing.
By understanding its basics and following a structured implementation methodology, manufacturers can achieve significant improvements in efficiency, quality, and cost savings.
Though challenges exist, the long-term benefits of BPM make it a worthy investment for any manufacturing organization looking to stay competitive in today’s fast-paced industrial landscape.
資料ダウンロード
QCD調達購買管理クラウド「newji」は、調達購買部門で必要なQCD管理全てを備えた、現場特化型兼クラウド型の今世紀最高の購買管理システムとなります。
ユーザー登録
調達購買業務の効率化だけでなく、システムを導入することで、コスト削減や製品・資材のステータス可視化のほか、属人化していた購買情報の共有化による内部不正防止や統制にも役立ちます。
NEWJI DX
製造業に特化したデジタルトランスフォーメーション(DX)の実現を目指す請負開発型のコンサルティングサービスです。AI、iPaaS、および先端の技術を駆使して、製造プロセスの効率化、業務効率化、チームワーク強化、コスト削減、品質向上を実現します。このサービスは、製造業の課題を深く理解し、それに対する最適なデジタルソリューションを提供することで、企業が持続的な成長とイノベーションを達成できるようサポートします。
オンライン講座
製造業、主に購買・調達部門にお勤めの方々に向けた情報を配信しております。
新任の方やベテランの方、管理職を対象とした幅広いコンテンツをご用意しております。
お問い合わせ
コストダウンが利益に直結する術だと理解していても、なかなか前に進めることができない状況。そんな時は、newjiのコストダウン自動化機能で大きく利益貢献しよう!
(Β版非公開)