- お役立ち記事
- Basics and implementation of laser marking that new employees in the production technology department of the electronic parts manufacturing industry should learn
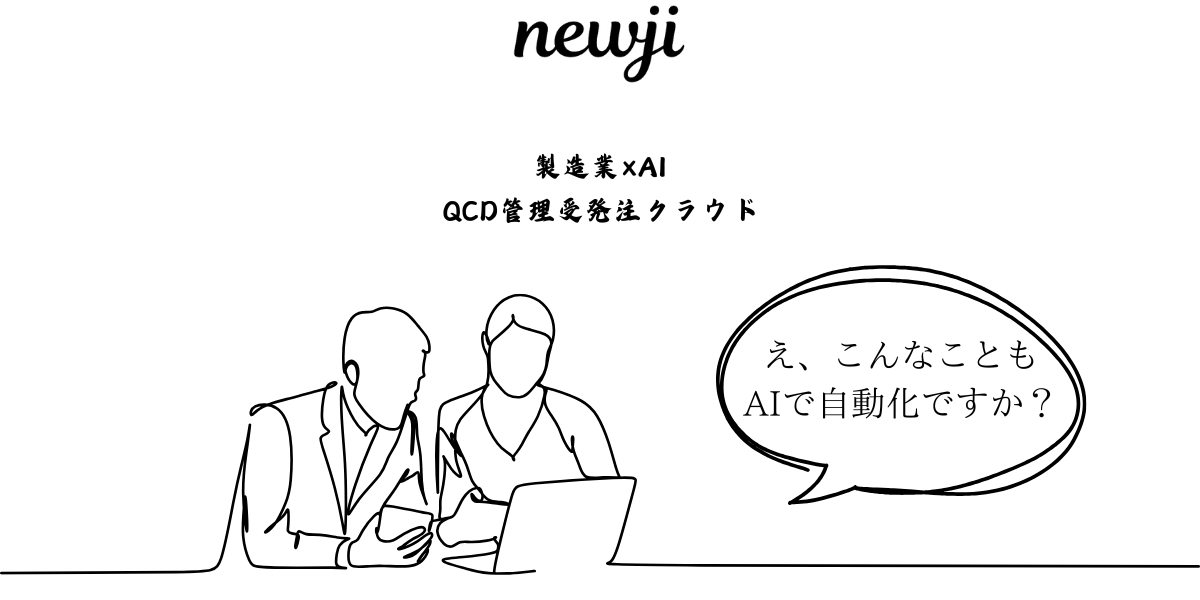
Basics and implementation of laser marking that new employees in the production technology department of the electronic parts manufacturing industry should learn
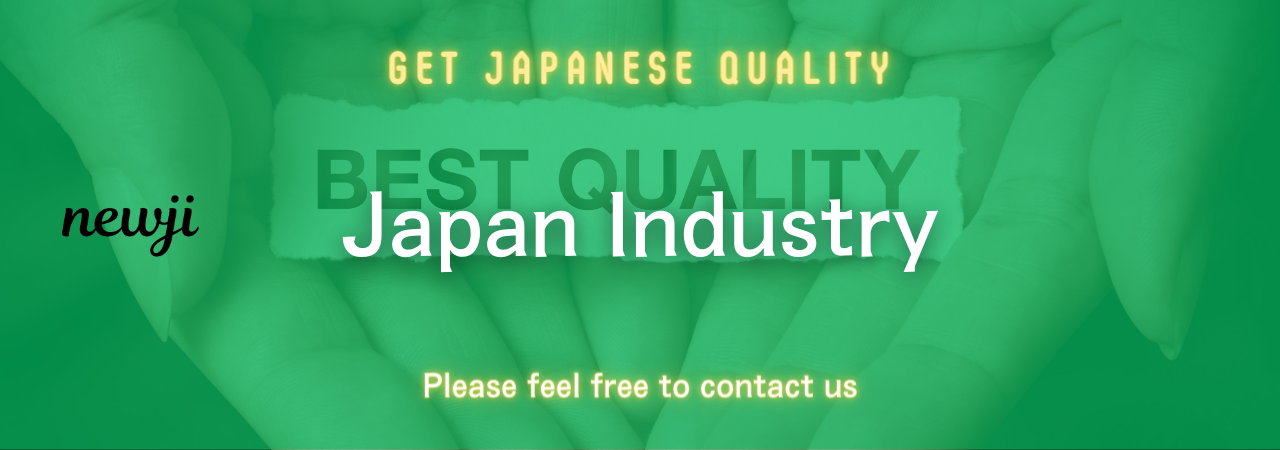
目次
Understanding Laser Marking
Laser marking is a prevalent technology used across various industries, especially in the manufacturing of electronic parts.
It involves using a laser beam to mark or engrave a surface with information such as logos, barcodes, serial numbers, or other identifiers.
This method is preferred for its high precision, durability, and ability to mark a wide range of materials.
Learning the basics of laser marking is essential for new employees in the production technology department.
How Laser Marking Works
Laser marking is achieved through a highly focused beam of light that interacts with the surface material.
The laser beam modifies the surface resulting in distinct marks.
The process can be classified into different types such as laser engraving, laser etching, and laser annealing depending on the material and the marking requirements.
The depth, texture, and permanence of the mark are controlled by the laser’s wavelength, output power, and speed.
Types of Laser Marking
**Laser Engraving**: This is one of the most durable methods where the laser beam physically removes a portion of the object’s surface to create a deep mark.
It is suitable for materials like metals and hard plastics.
**Laser Etching**: Similar to engraving, etching alters the object surface by melting the material.
It’s often used on metals and allows for a shallower depth than engraving.
**Laser Annealing**: This involves heating the metal surface to create oxide layers of varying colors.
This method is suitable for stainless steel and titanium.
Materials Suitable for Laser Marking
Laser marking is versatile and can be used on a variety of materials.
**Metals**: Steel, aluminum, gold, and silver are commonly laser marked for creating durable and resistant marks.
**Plastics**: Laser marking on plastics like ABS, polycarbonate, or acrylic is possible, and it is often used for creating barcodes and serial numbers.
**Ceramics and Glass**: These materials can be marked using lasers to ensure precision without damaging the structural integrity.
Importance of Laser Marking in Electronic Parts Manufacturing
In the electronic parts manufacturing industry, precision and clarity in labeling are paramount for tracking, quality control, and customer information.
**Traceability**: Laser marking ensures that each part is easily traceable throughout its lifecycle.
By marking critical information directly on the part, manufacturers can track the production batch, assembly configurations, and other details effectively.
**Quality Control**: The high precision of laser marking minimizes errors, guaranteeing that labels or markings are consistently clear and legible.
This is particularly important for components that need to adhere to strict industry standards.
**Durability**: Since electronic parts often undergo rigorous conditions, the permanence of laser marking ensures that necessary information remains intact and legible, even in harsh environments or after frequent handling.
Benefits of Laser Marking
Laser marking offers numerous advantages that make it a preferred choice in industrial applications.
**Non-Contact Process**: Since laser marking doesn’t require physical contact with the material, it results in minimal wear and tear on both the marking equipment and the material being marked.
**High Speed and Precision**: The process is incredibly fast and allows for intricate designs to be replicated with high precision, crucial for compact electronic components.
**Environmentally Friendly**: Laser marking is safe, emitting no harmful chemicals or emissions.
This makes it an environmentally friendly choice compared to other marking techniques.
Implementing Laser Marking in Production
For new employees working in production technology, understanding how to implement laser marking effectively is vital.
**Choosing the Right Equipment**: Depending on the materials and required precision, selecting the appropriate laser marking equipment is essential. Consider factors like laser type, power, and speed capability.
**Setting Parameters**: Tailoring the laser’s settings such as speed, frequency, and focus can significantly impact the quality of the marking.
Proper training in adjusting these parameters is crucial for achieving desired results.
**Safety Measures**: Laser systems require adherence to safety protocols to prevent hazards.
Employees should be trained on proper use, handling of equipment, and emergency procedures to ensure a safe work environment.
Future Trends in Laser Marking
Laser marking technology is continually evolving with advancements aimed at improving efficiency and precision.
**3D Laser Marking**: This emerging technology allows marking on complex surfaces without compromising quality.
It is set to revolutionize how components with irregular shapes are labeled.
**Integration with Automation**: Tying laser marking machines with automated production lines ensures seamless operation and improved productivity.
This is particularly beneficial for mass production environments.
**Enhanced Software Solutions**: Software advancements are enhancing the capabilities of laser marking machines, offering real-time monitoring, customization, and integration with other production technologies.
Conclusion
For new employees in the production technology department of an electronic parts manufacturing company, mastering laser marking basics is essential to maintaining efficient and reliable operations.
From understanding how the technology works to implementing it safely in production, laser marking plays a critical role in ensuring the high quality and traceability of electronic components.
Adopting best practices and staying informed about technological advancements can greatly enhance productivity and quality in your work environment.
資料ダウンロード
QCD調達購買管理クラウド「newji」は、調達購買部門で必要なQCD管理全てを備えた、現場特化型兼クラウド型の今世紀最高の購買管理システムとなります。
ユーザー登録
調達購買業務の効率化だけでなく、システムを導入することで、コスト削減や製品・資材のステータス可視化のほか、属人化していた購買情報の共有化による内部不正防止や統制にも役立ちます。
NEWJI DX
製造業に特化したデジタルトランスフォーメーション(DX)の実現を目指す請負開発型のコンサルティングサービスです。AI、iPaaS、および先端の技術を駆使して、製造プロセスの効率化、業務効率化、チームワーク強化、コスト削減、品質向上を実現します。このサービスは、製造業の課題を深く理解し、それに対する最適なデジタルソリューションを提供することで、企業が持続的な成長とイノベーションを達成できるようサポートします。
オンライン講座
製造業、主に購買・調達部門にお勤めの方々に向けた情報を配信しております。
新任の方やベテランの方、管理職を対象とした幅広いコンテンツをご用意しております。
お問い合わせ
コストダウンが利益に直結する術だと理解していても、なかなか前に進めることができない状況。そんな時は、newjiのコストダウン自動化機能で大きく利益貢献しよう!
(Β版非公開)