- お役立ち記事
- Basics and key points of reliability design to improve productivity
Basics and key points of reliability design to improve productivity
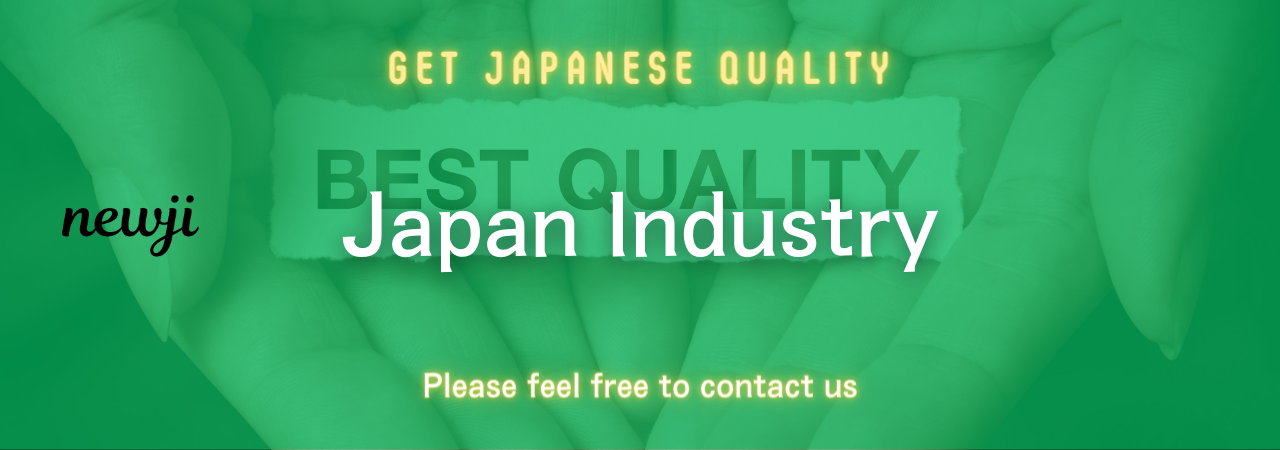
目次
Understanding Reliability Design
Reliability design is a crucial facet of product development that ensures a product performs its intended function consistently over its expected lifespan.
This concept is not just relevant for engineers and product designers; it also impacts business strategies and consumer satisfaction.
A product with high reliability can significantly boost a company’s reputation, reduce costs associated with warranty claims, and increase customer loyalty.
Reliability design involves a systematic approach to identifying potential failure modes and implementing measures to mitigate them.
The primary goal is to minimize the risk of product failure, thereby ensuring higher productivity and efficiency.
The Importance of Reliability Design in Product Development
In today’s competitive market, the reliability of a product can make or break a company’s success.
Consumers expect products to work seamlessly without frequent failures, and meeting these expectations requires careful planning and design.
When reliability is not prioritized, companies face various negative consequences, including increased maintenance costs, loss of consumer trust, and damage to brand reputation.
Furthermore, unreliable products can lead to safety hazards, which can have severe legal and financial implications.
Investing in reliability design during the early stages of development can provide significant long-term benefits.
Not only does it result in robust products, but it also allows companies to optimize production processes and reduce waste, ultimately leading to improved productivity.
Key Components of Reliability Design
Reliability design encompasses several key components that work together to ensure a product’s durability and functionality throughout its lifecycle.
Understanding these components can help companies formulate effective strategies for improving reliability.
Failure Mode and Effects Analysis (FMEA)
FMEA is a proactive tool used to identify potential failure modes of a product and assess their impact on overall functionality.
By understanding how and why a product might fail, designers and engineers can prioritize resource allocation to address the most critical issues.
FMEA is a critical step in reliability design, as it helps prevent costly and time-consuming failures after product launch.
Reliability Testing
Reliability testing involves subjecting a product to various stress conditions to evaluate its performance and durability.
This process helps determine the product’s limits and ensures it can withstand real-world usage scenarios.
Common reliability tests include thermal cycling, vibration testing, and accelerated life testing, which simulate long-term use in a short period.
Through rigorous reliability testing, companies can identify weaknesses in their products and make necessary improvements before reaching consumers.
Redundancy
Implementing redundancy involves designing systems or components that provide backup options in case of a failure.
This approach enhances reliability by ensuring that if one part fails, others can take over the function without disrupting the overall operation.
Redundancy is commonly used in crucial industries such as aerospace and healthcare, where system failures can have catastrophic consequences.
By incorporating redundancy in design, companies can improve the reliability and safety of their products.
Design for Maintainability
Designing products with maintainability in mind is another essential aspect of reliability design.
This involves creating products that are easy to service, repair, and upgrade.
By considering maintainability during the design phase, companies can reduce downtime, simplify repair processes, and extend the product’s lifespan.
Effective maintainability design leads to satisfied customers who experience fewer disruptions and lower total cost of ownership.
Strategies to Enhance Reliability Design
To reap the benefits of reliability design, companies must implement effective strategies throughout the product development process.
Cross-Functional Collaboration
Collaboration between different departments, such as design, engineering, quality assurance, and marketing, is essential to ensure comprehensive reliability design.
Each team brings a unique perspective and expertise, contributing to a well-rounded approach to preventing failures.
Engaging stakeholders from various functions early in the development process can facilitate better decision-making and minimize potential issues.
Continuous Improvement
Reliability design is not a one-time effort but an ongoing process.
After a product is launched, companies must continue to gather data on its performance and customer feedback.
Analyzing this information allows for iterative improvements, addressing any emerging problems and refining reliability.
By fostering a culture of continuous improvement, companies can ensure their products remain reliable and competitive in the market.
Leveraging Technology
Technological advancements play a key role in enhancing reliability design.
From computer-aided design (CAD) software to data analytics and machine learning, modern tools and platforms enable companies to simulate and analyze potential failure modes more efficiently.
Utilizing these technologies can streamline the reliability design process, providing valuable insights that lead to better decision-making and optimal product performance.
The Impact of Reliability Design on Productivity
Strong reliability design not only improves the quality and durability of products but also has a profound impact on overall productivity and efficiency.
Products designed with reliability in mind require fewer maintenance interventions, minimizing downtime and ensuring uninterrupted operations.
This increase in uptime leads to higher productivity levels and improved output.
On the manufacturing side, incorporating reliability design can optimize production processes and reduce waste.
When defects and failures are minimized, companies can operate more efficiently, achieving leaner production cycles.
Overall, reliability design manifests in improved customer satisfaction, reduced costs, and a distinct competitive advantage—critical factors contributing to enhanced productivity and business success.
In conclusion, incorporating reliability design into product development is vital for creating robust and durable products that meet consumer expectations.
By focusing on failure prevention, thorough testing, redundancy, and maintainability, companies can mitigate risks and optimize productivity.
Embracing strategies such as cross-functional collaboration, continuous improvement, and leveraging technology will further strengthen reliability design efforts.
Ultimately, investing in reliability design is a win-win for both companies and consumers, driving business growth and fostering long-term loyalty.
資料ダウンロード
QCD調達購買管理クラウド「newji」は、調達購買部門で必要なQCD管理全てを備えた、現場特化型兼クラウド型の今世紀最高の購買管理システムとなります。
ユーザー登録
調達購買業務の効率化だけでなく、システムを導入することで、コスト削減や製品・資材のステータス可視化のほか、属人化していた購買情報の共有化による内部不正防止や統制にも役立ちます。
NEWJI DX
製造業に特化したデジタルトランスフォーメーション(DX)の実現を目指す請負開発型のコンサルティングサービスです。AI、iPaaS、および先端の技術を駆使して、製造プロセスの効率化、業務効率化、チームワーク強化、コスト削減、品質向上を実現します。このサービスは、製造業の課題を深く理解し、それに対する最適なデジタルソリューションを提供することで、企業が持続的な成長とイノベーションを達成できるようサポートします。
オンライン講座
製造業、主に購買・調達部門にお勤めの方々に向けた情報を配信しております。
新任の方やベテランの方、管理職を対象とした幅広いコンテンツをご用意しております。
お問い合わせ
コストダウンが利益に直結する術だと理解していても、なかなか前に進めることができない状況。そんな時は、newjiのコストダウン自動化機能で大きく利益貢献しよう!
(Β版非公開)