- お役立ち記事
- Basics and mechanisms of sintering technology and how to utilize it for applications
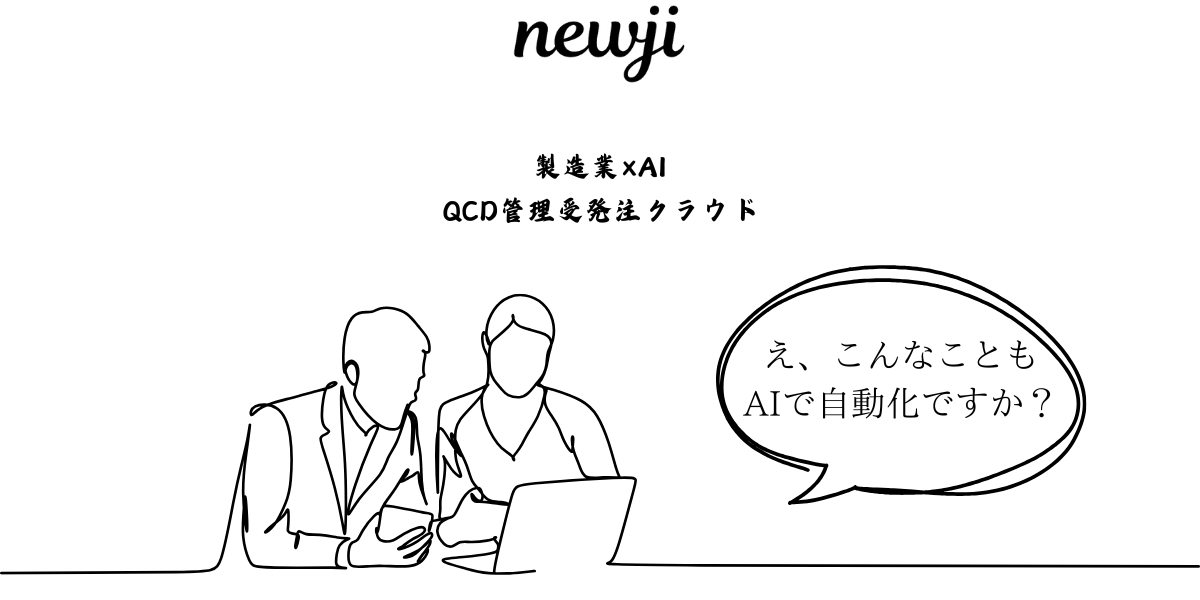
Basics and mechanisms of sintering technology and how to utilize it for applications
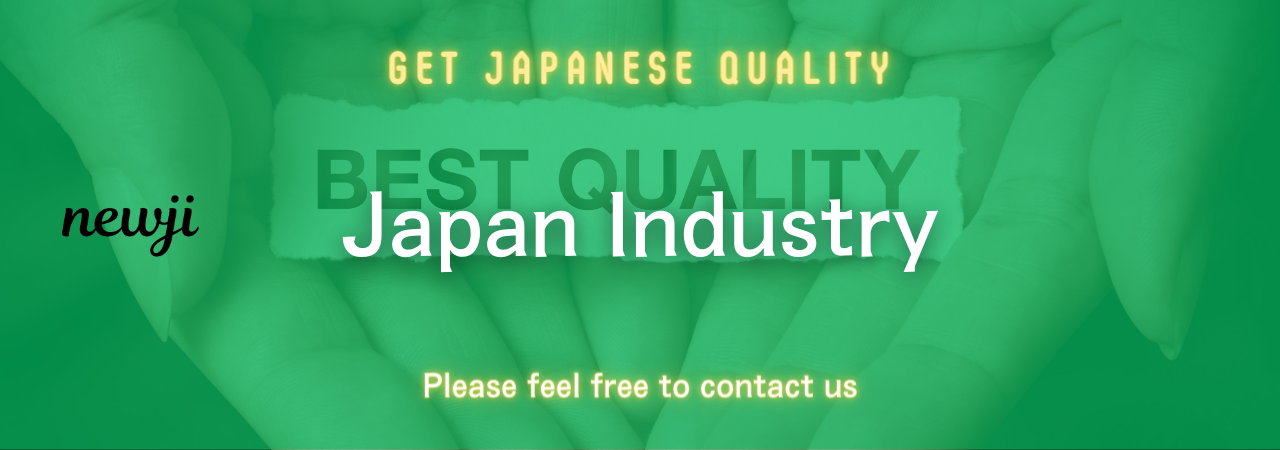
目次
Introduction to Sintering Technology
Sintering is a fascinating process that transforms powdered materials into solid structures without melting them completely.
It’s a key technology used in various industries, from manufacturing heavy machinery parts to delicate components in electronic devices.
So, what exactly is sintering, and why has it become such an indispensable part of modern industrial processes?
At its core, sintering involves the bonding of particles through heating.
During this process, particles in a powdered form are packed tightly together and then heated to a temperature below their melting point.
As a result, the particles bond at their points of contact, leading to a reduction in overall porosity and an increase in strength and density.
Interestingly, this process occurs in a carefully controlled environment to ensure optimal results.
The Basics of Sintering Mechanisms
The Driving Forces Behind Sintering
The main driving force behind sintering is the reduction of free energy on the surface of powder particles.
When powders are compacted and heated, the boundaries between particles diminish, and their overall surface area reduces.
This reduction in surface energy leads to the sintering phenomenon where particles bond to achieve a more stable configuration.
Several mechanisms contribute to this process, with diffusion being the most prominent one.
Diffusion occurs when atoms move at elevated temperatures, filling vacancies between them.
This atomic movement eventually leads to particle bonding during sintering.
Stages of Sintering
The sintering process can typically be broken down into three distinct stages:
1. **Initial Stage**: Initially, when the material is heated, the grain boundaries begin to form.
Necks, or bonding areas, start to develop between particles, which is an indication of early-stage sintering.
2. **Intermediate Stage**: As the temperature remains constant, neck growth continues.
The material begins to densify, and the porosity between the particles reduces significantly.
Pores present in the initial stage are slowly eliminated, strengthening the structure.
3. **Final Stage**: In the final stage, substantial dimensional changes occur.
Grain growth reduces the number of pores to a minimum, resulting in a dense and solid structure.
The mechanical properties also improve significantly during this stage.
Applications of Sintering Technology
Sintering technology offers a myriad of applications that cater to different industries.
Let’s explore some of these applications to understand the versatility and importance of sintering.
Powder Metallurgy
One of the most significant applications of sintering is in powder metallurgy.
This involves creating metal parts from powdered materials without melting them completely.
It’s especially useful for producing complex shapes that would be difficult or costly to achieve through traditional casting methods.
The automobile and aerospace industries greatly benefit from this technology.
By utilizing sintering in powder metallurgy, these industries can manufacture high-strength components that withstand extreme conditions.
Ceramic Manufacturing
Sintering is also essential in the production of ceramics.
Traditional ceramics like bricks and tiles, as well as advanced ceramics used in electronics and biomedical implants, rely heavily on this process.
In particular, sintering contributes to improving the mechanical properties of ceramics, making them ideal for challenging applications.
3D Printing
The advent of 3D printing technology has highlighted a modern application of sintering known as Selective Laser Sintering (SLS).
In SLS, a laser selectively fuses powdered material to create a solid object, layer by layer.
This technique allows for the creation of complex and intricate designs that are otherwise impossible through conventional manufacturing methods.
3D printing, powered by sintering, has revolutionized industries by offering rapid prototyping, customization, and reducing material waste.
Electronic Components
The electronics industry also takes advantage of sintering technology to produce miniaturized components with high precision.
For instance, sintered materials like ferrites and piezoelectric ceramics are used in a variety of electronic devices.
The use of sintering ensures these components are not only highly functional but also durable enough to withstand prolonged usage.
Optimizing Sintering for Better Results
While sintering offers numerous benefits, it requires careful control and optimization to achieve the best results.
Here are some key factors to consider when optimizing sintering processes:
Material Selection
Choosing the right material is crucial in sintering as it affects both the quality and efficiency of the process.
It’s important to select materials that have a similar melting point or thermal expansion rates to avoid discrepancies during heating.
Furthermore, additives, such as binders or lubricants, can enhance the sintering process by improving the packing density and reducing friction between particles.
Temperature Control
Precise temperature control is vital in any sintering process.
Overheating can lead to unwanted grain growth, while insufficient heating may result in inadequate bonding.
Thus, it is crucial to maintain an optimal temperature profile to ensure proper particle bonding and high-density structures.
Sintering Atmosphere
The atmosphere in which sintering occurs also plays a critical role, as various gases can interact with the material.
Inert gases like nitrogen or argon are often used to prevent oxidation or unwanted chemical reactions.
Future Prospects of Sintering Technology
Sintering technology is continually evolving, with research and development paving the way to new advancements and applications.
As manufacturing processes advance, sintering is expected to become even more integral, developing materials with superior properties and expanding its applications.
For instance, advances in nanoparticle sintering could enable the production of highly dense and strong nanostructured materials, opening new avenues in various fields, including medicine, electronics, and energy storage.
Moreover, combining sintering with other emerging technologies could revolutionize production methods, improving efficiency and reducing environmental impact.
In conclusion, sintering technology is an invaluable asset to the industrial landscape.
Understanding its mechanisms and applications can lead to innovation and efficiency in producing high-quality materials for a wide array of sectors.
As technology progresses, so will the fascinating field of sintering, transforming how we create and utilize materials in the future.
資料ダウンロード
QCD調達購買管理クラウド「newji」は、調達購買部門で必要なQCD管理全てを備えた、現場特化型兼クラウド型の今世紀最高の購買管理システムとなります。
ユーザー登録
調達購買業務の効率化だけでなく、システムを導入することで、コスト削減や製品・資材のステータス可視化のほか、属人化していた購買情報の共有化による内部不正防止や統制にも役立ちます。
NEWJI DX
製造業に特化したデジタルトランスフォーメーション(DX)の実現を目指す請負開発型のコンサルティングサービスです。AI、iPaaS、および先端の技術を駆使して、製造プロセスの効率化、業務効率化、チームワーク強化、コスト削減、品質向上を実現します。このサービスは、製造業の課題を深く理解し、それに対する最適なデジタルソリューションを提供することで、企業が持続的な成長とイノベーションを達成できるようサポートします。
オンライン講座
製造業、主に購買・調達部門にお勤めの方々に向けた情報を配信しております。
新任の方やベテランの方、管理職を対象とした幅広いコンテンツをご用意しております。
お問い合わせ
コストダウンが利益に直結する術だと理解していても、なかなか前に進めることができない状況。そんな時は、newjiのコストダウン自動化機能で大きく利益貢献しよう!
(Β版非公開)