- お役立ち記事
- Basics and points for development of SiC wafer manufacturing technology (crystal growth, processing, evaluation) for power semiconductors
Basics and points for development of SiC wafer manufacturing technology (crystal growth, processing, evaluation) for power semiconductors
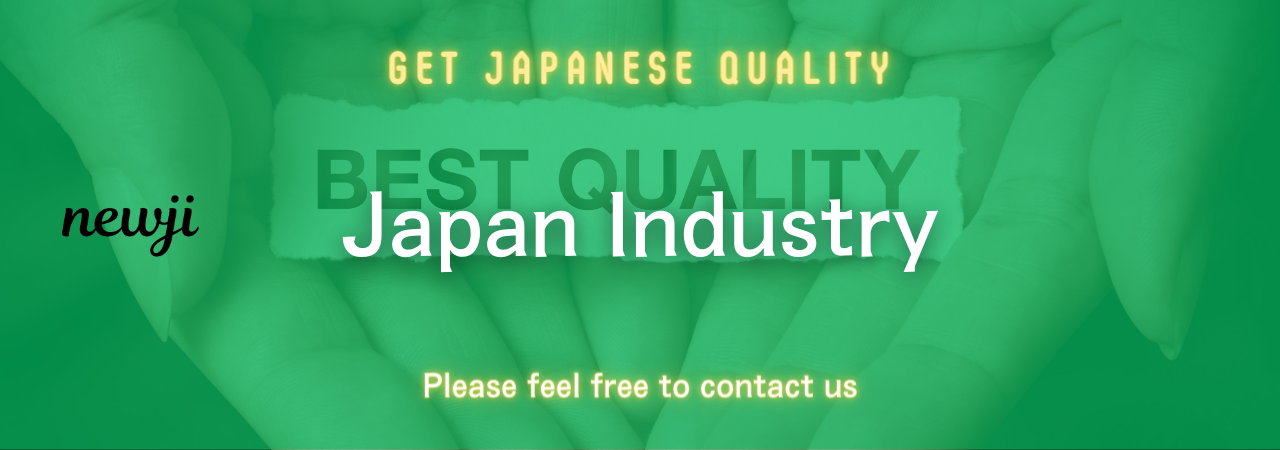
目次
Introduction to SiC Wafers
Silicon carbide (SiC) wafers are becoming increasingly significant in the field of power semiconductors.
These wafers are prized for their ability to handle high voltages and temperatures, making them ideal for power electronics.
As the demand for energy-efficient electronic devices rises, the development of SiC wafer manufacturing technology has become crucial.
In this article, we will explore the basics and essential points for the development of SiC wafer technology, focusing on crystal growth, processing, and evaluation.
Understanding SiC Crystal Growth
SiC wafers begin their journey as crystal formations.
Crystal growth is a pivotal step in producing high-quality SiC wafers for power semiconductors.
1. What is SiC Crystal Growth?
Crystal growth of SiC involves creating large wafers from smaller crystals.
Many semiconductor applications require SiC crystals with perfect structure and minimal defects.
The process typically uses methods such as Physical Vapor Transport (PVT) or Chemical Vapor Deposition (CVD).
2. PVT Method
The PVT method is one of the most widely used techniques for SiC crystal growth.
In this process, the SiC powder is sublimated in a high-temperature environment, transitioning from solid to vapor.
Subsequently, the vapor condenses on cooler surfaces, forming SiC crystals.
The PVT method is favored for its capability to produce large and high-quality crystals.
3. CVD Method
The Chemical Vapor Deposition method involves the chemical reaction of vapor-phase precursors.
These gaseous precursors decompose or react on the surface of a substrate, leading to a thin film or crystalline layer.
CVD allows for better control over the stoichiometry and composition of the SiC crystal.
Though effective, it is typically used for producing thin films rather than bulk crystals.
Processing of SiC Wafers
After successful growth, the SiC crystals undergo processing to convert them into wafers ready for semiconductor applications.
1. Wafer Cutting
Wafer cutting is the initial stage in processing.
The large SiC crystal, often in a cylindrical form, is sliced into thin circular wafers.
Diamond wire saws are commonly used in this stage due to SiC’s hardness.
Cutting requires precision to prevent cracking and ensure flatness.
2. Surface Grinding and Polishing
Once cut, the wafer surfaces need to be smoothed to remove imperfections.
Surface grinding and polishing are vital for achieving the planarity needed for semiconductor device fabrication.
The grinding process removes most of the surface irregularities, while polishing provides a mirror-like finish.
This step is crucial for minimizing light scattering, enhancing electronic performance.
3. Doping Process
The doping process involves intentionally introducing impurities into the SiC wafer to modify its electrical properties.
Doping is essential for creating p-type or n-type semiconductors, required in electronic devices.
Implantation or diffusion methods are typically used for doping, with precise control essential to ensure the desired characteristics.
Evaluation of SiC Wafers
The final aspect of SiC wafer technology is the evaluation, ensuring that the wafers meet the required standards.
1. Quality Inspection
Quality inspection involves testing wafers for defects and uniformity.
Non-destructive evaluation methods, such as X-ray topography or photoluminescence, are used to detect structural anomalies.
These inspections are vital to ensuring that the wafers can function effectively in their intended applications.
2. Electrical Testing
Electrical testing examines the wafer’s conductive properties and ensures proper doping levels.
Measurements such as carrier lifetime, mobility, and resistivity are evaluated.
These parameters are critical for the performance of the final semiconductor device.
3. Thermal Analysis
Given SiC’s use in high-temperature applications, thermal analysis is essential.
Techniques such as thermogravimetric analysis and differential scanning calorimetry are used to test heat resistance and thermal expansion.
These tests ensure that the wafers will perform under extreme conditions.
Challenges and Future Prospects
While SiC wafer technology has made tremendous strides, there are challenges yet to overcome.
One significant challenge is cost.
The production of SiC wafers remains expensive, partly due to the complexity of crystal growth and processing technologies.
Researchers and manufacturers are working on innovations to reduce costs and improve scalability.
Looking forward, the future of SiC wafer technology is promising.
Demand is expected to rise in industries such as automotive, energy, and telecommunications.
Advancements in manufacturing techniques could significantly enhance the performance and affordability of SiC-based power semiconductors, fueling a new generation of energy-efficient devices.
In conclusion, the development of SiC wafer manufacturing technology is integral to advancing power semiconductor applications.
Understanding the intricacies of crystal growth, processing, and evaluation is essential for producing high-quality wafers.
As technologies evolve, SiC wafers will play a critical role in meeting the demands of modern electronic devices.
資料ダウンロード
QCD調達購買管理クラウド「newji」は、調達購買部門で必要なQCD管理全てを備えた、現場特化型兼クラウド型の今世紀最高の購買管理システムとなります。
ユーザー登録
調達購買業務の効率化だけでなく、システムを導入することで、コスト削減や製品・資材のステータス可視化のほか、属人化していた購買情報の共有化による内部不正防止や統制にも役立ちます。
NEWJI DX
製造業に特化したデジタルトランスフォーメーション(DX)の実現を目指す請負開発型のコンサルティングサービスです。AI、iPaaS、および先端の技術を駆使して、製造プロセスの効率化、業務効率化、チームワーク強化、コスト削減、品質向上を実現します。このサービスは、製造業の課題を深く理解し、それに対する最適なデジタルソリューションを提供することで、企業が持続的な成長とイノベーションを達成できるようサポートします。
オンライン講座
製造業、主に購買・調達部門にお勤めの方々に向けた情報を配信しております。
新任の方やベテランの方、管理職を対象とした幅広いコンテンツをご用意しております。
お問い合わせ
コストダウンが利益に直結する術だと理解していても、なかなか前に進めることができない状況。そんな時は、newjiのコストダウン自動化機能で大きく利益貢献しよう!
(Β版非公開)