- お役立ち記事
- Basics and points for development of SiC wafer manufacturing technology (crystal growth, processing, evaluation) for power semiconductors
月間76,176名の
製造業ご担当者様が閲覧しています*
*2025年3月31日現在のGoogle Analyticsのデータより
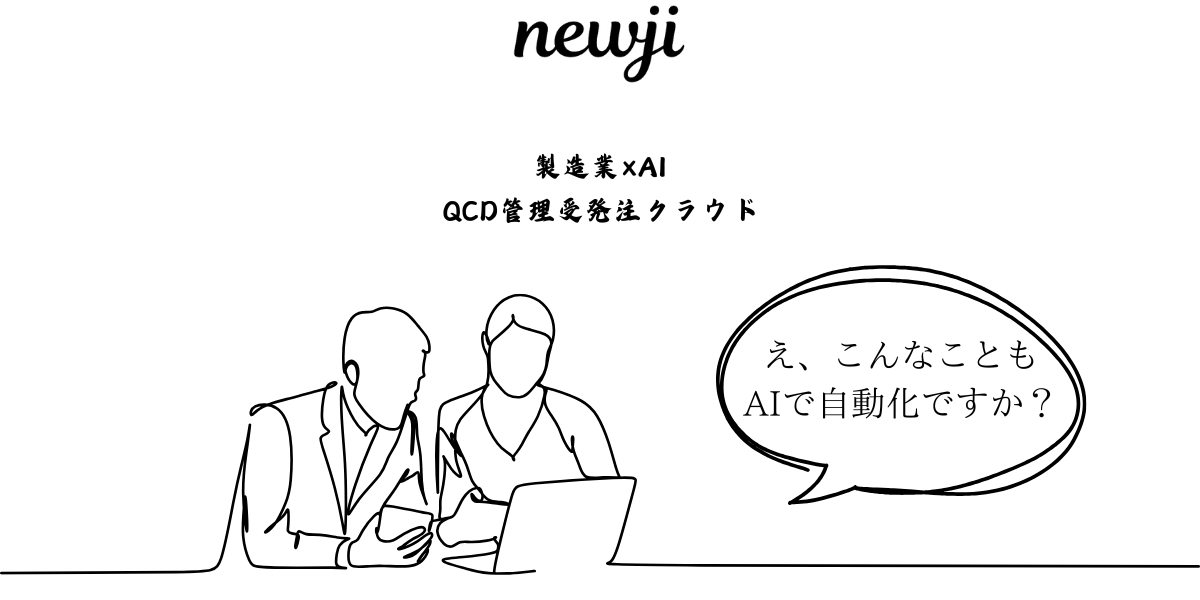
Basics and points for development of SiC wafer manufacturing technology (crystal growth, processing, evaluation) for power semiconductors
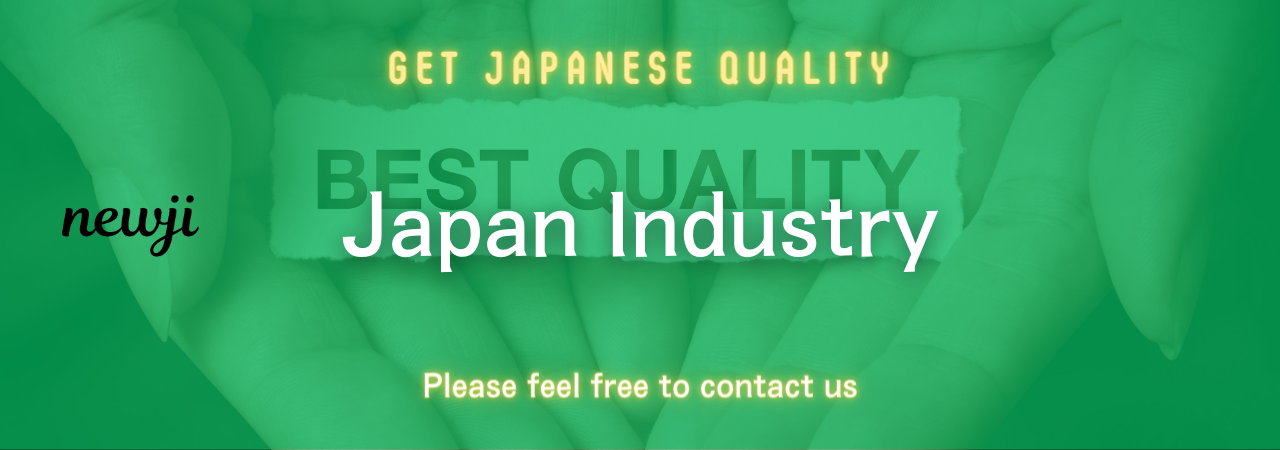
目次
Introduction to SiC Wafer Manufacturing Technology
Silicon carbide (SiC) wafers are increasingly becoming essential components in the realm of power semiconductors.
Utilized for their superior material properties, SiC wafers contribute to high efficiency and reduced size in electronic applications.
Their manufacturing processes are intricate, involving crystal growth, precision processing, and thorough evaluation to ensure the highest quality.
This article explores the fundamental methods and notable considerations in the development of SiC wafer manufacturing technology.
Crystal Growth in SiC Wafer Manufacturing
The Significance of Crystal Growth
At the heart of SiC wafer manufacturing lies the intricate process of crystal growth.
The quality and purity of the crystal directly impact the performance and efficiency of the final product.
Crystal growth method determines the lattice structure, defect rates, and material uniformity, all of which are critical for applications in power devices.
Methods of Crystal Growth
Several methods are employed in the crystal growth of SiC wafers, each with its benefits and complexities.
– **Physical Vapor Transport (PVT):** PVT is one of the most common methods used for SiC crystal growth.
In this process, a high-temperature environment is used to sublimate pure SiC powder, which is then transported in vapor form to a cooler area where it condenses and forms a crystal.
This method is favored for producing larger crystals with fewer defects.
– **Chemical Vapor Deposition (CVD):** CVD involves reacting gaseous precursors in a chamber to deposit crystalline SiC on a substrate.
This method allows for precise control over the film thickness and purity, making it ideal for producing thin films and epitaxial layers.
– **Solution Growth:** This method involves dissolving SiC in a solvent at high temperatures and allowing it to recrystallize slowly.
While this process can produce high-purity crystals, it is generally slower and less scalable than PVT.
Processing Techniques for SiC Wafers
The Importance of Processing
Once SiC crystals are grown, they undergo several processing steps to transform into functional wafers.
Precision in these steps is vital, as any imperfections can significantly impact the electrical and thermal performance of the resulting devices.
Cutting and Slicing
The first step in processing involves cutting the bulk crystal into thin wafers.
Wire sawing is commonly employed, using a wire with an abrasive slurry or bonded diamond particles to slice precise layers.
Minimizing kerf loss (material lost during cutting) is a key challenge in this stage.
Grinding and Polishing
Post-slicing, the surfaces of the wafers are ground and polished to achieve the desired thickness and surface finish.
Grinding removes surface damage from the cutting process, while polishing creates an ultra-smooth surface.
Attention to detail in these steps ensures low defect density and prepares the wafer for subsequent processes.
Etching and Surface Cleaning
Chemical etching is used to remove damaged layers and further reduce surface roughness.
This process may involve acids or other chemicals tailored to selectively remove material without compromising wafer integrity.
Thorough cleaning removes contaminants, ensuring the surface is pristine for device fabrication.
Evaluation and Quality Control
Ensuring Wafer Quality
Rigorous evaluation procedures are essential to confirm the quality and performance potential of SiC wafers.
Defect Identification
Advanced imaging techniques such as X-ray diffraction, electron microscopy, and optical characterization are employed to detect structural defects and imperfections.
These evaluations help in maintaining the high standards required for power semiconductor applications.
Electrical and Thermal Testing
To ensure the functionality of the wafers, various electrical tests are conducted to assess parameters such as conductivity, resistivity, and carrier mobility.
Thermal stability tests are equally important, as SiC is often used in high-temperature environments.
Environmental Considerations
Evaluation of SiC wafers also includes ensuring compliance with environmental regulations and industry standards.
This includes assessing the environmental impact of manufacturing processes and striving for sustainable practices.
Future Prospects in SiC Wafer Technology
As the demand for efficient and compact power semiconductor devices continues to rise, SiC wafer technology is poised for further advancements.
Research into novel crystal growth methods, improved processing techniques, and more comprehensive evaluation protocols promises to enhance the performance and reliability of SiC-based devices.
Furthermore, the integration of artificial intelligence and machine learning in manufacturing processes shows potential for optimizing production and improving yield rates.
Conclusion
The development of SiC wafer manufacturing technology is a multifaceted process that influences the future of power semiconductors.
From the initial stages of crystal growth to the final evaluation, each step requires precision and innovation.
By understanding and advancing these processes, the industry can continue to produce high-performance semiconductors that meet the evolving demands of modern technology.
資料ダウンロード
QCD管理受発注クラウド「newji」は、受発注部門で必要なQCD管理全てを備えた、現場特化型兼クラウド型の今世紀最高の受発注管理システムとなります。
ユーザー登録
受発注業務の効率化だけでなく、システムを導入することで、コスト削減や製品・資材のステータス可視化のほか、属人化していた受発注情報の共有化による内部不正防止や統制にも役立ちます。
NEWJI DX
製造業に特化したデジタルトランスフォーメーション(DX)の実現を目指す請負開発型のコンサルティングサービスです。AI、iPaaS、および先端の技術を駆使して、製造プロセスの効率化、業務効率化、チームワーク強化、コスト削減、品質向上を実現します。このサービスは、製造業の課題を深く理解し、それに対する最適なデジタルソリューションを提供することで、企業が持続的な成長とイノベーションを達成できるようサポートします。
製造業ニュース解説
製造業、主に購買・調達部門にお勤めの方々に向けた情報を配信しております。
新任の方やベテランの方、管理職を対象とした幅広いコンテンツをご用意しております。
お問い合わせ
コストダウンが利益に直結する術だと理解していても、なかなか前に進めることができない状況。そんな時は、newjiのコストダウン自動化機能で大きく利益貢献しよう!
(β版非公開)