- お役立ち記事
- Basics and practical implementation guide of LEAN production method that new employees of production technology department should know
Basics and practical implementation guide of LEAN production method that new employees of production technology department should know
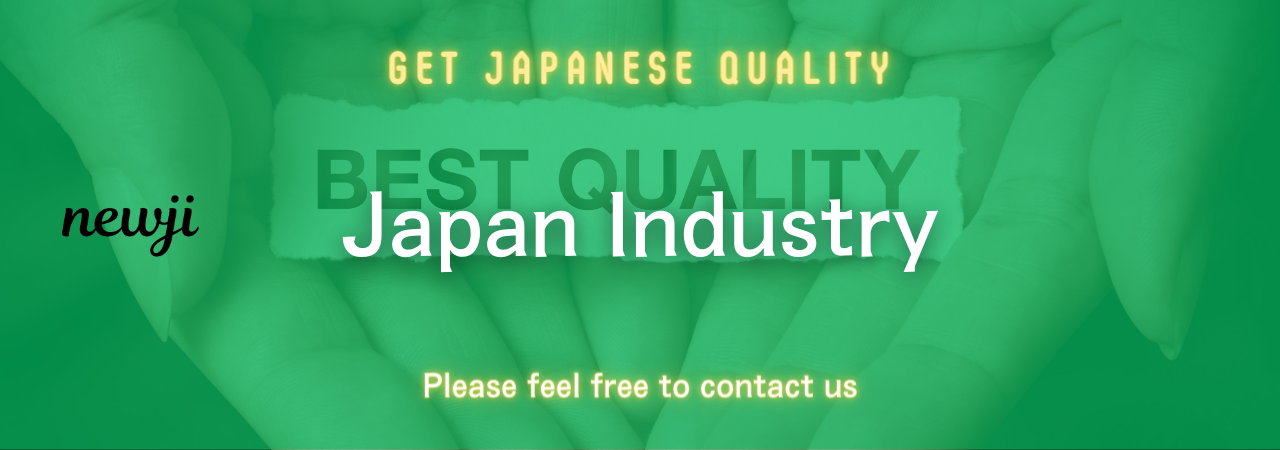
目次
Understanding the Basics of Lean Production
Lean production is a systematic method for waste minimization within a manufacturing system without sacrificing productivity.
It involves a focus on the customer by providing value-added products and services efficiently.
For new employees in the production technology department, understanding the fundamentals of lean production is crucial.
Lean production originated in Japan, predominantly with its development attributed to the Toyota Production System (TPS).
The methodology focuses on maximizing value for the customer while minimizing waste.
This process is about improving quality, enhancing productivity, and reducing costs.
The Five Lean Principles
To effectively implement lean production, it’s important to grasp its core principles.
These principles serve as a guiding framework that drives efficiency and productivity.
1. **Define Value**:
Value is determined from the customer’s perspective.
It is what the customer is willing to pay for, and it sets the foundation for all lean initiatives.
Anything that does not add value to the end product is considered waste and must be eliminated.
2. **Map the Value Stream**:
This involves analyzing the entire production process from start to finish.
Mapping helps identify activities that add value and those that do not.
By understanding each step, organizations can work to eliminate unnecessary processes.
3. **Create Flow**:
Once wasteful processes are removed, it’s crucial to ensure that value-added activities flow smoothly.
This involves removing any interruptions or bottlenecks in the production cycle.
Continuous flow indicates that processes run efficiently without delays or unnecessary steps.
4. **Establish Pull**:
Production should be based on actual customer demand rather than forecasts.
This reduces overproduction and excess inventory, which are forms of waste.
A pull-based system ensures that resources are only deployed when there is clear demand.
5. **Seek Perfection**:
Lean is a journey towards perfection.
Continuous improvement (Kaizen) is integral, where employees at all levels are encouraged to suggest improvements.
This culture of ongoing advancement fosters an environment of innovation and efficiency.
Implementing Lean Production
Implementing lean production in an organization requires a structured approach and commitment.
Here are steps to guide new employees on practical implementation:
Step 1: Obtain Leadership Support
Leadership must be committed to the lean philosophy for successful adoption.
This includes providing resources, training, and support systems for employees at all levels.
Management should lead by example, demonstrating the benefits of lean practices.
Step 2: Engage Employees
Lean relies heavily on employee participation.
Staff should be involved in the identification of waste and be a part of the solution.
Training and open communication are essential for fostering an empowered workforce.
Employees must feel valued and understand how their roles contribute to the lean goals.
Step 3: Start With Pilot Projects
It is advisable to implement lean in pilot projects before scaling up.
Select a specific area or process that can be improved.
Evaluate the outcomes to learn what works and what doesn’t.
Use the insights gained from pilot projects to refine processes and apply them more broadly.
Step 4: Standardize Successful Practices
Once improvements demonstrate positive results, standardize these practices.
Document the processes clearly and ensure that all team members understand and follow them.
Standardization helps maintain consistency and quality across the production line.
Step 5: Monitor and Adjust
Continuous monitoring is key to successful lean implementation.
Regular assessments of processes can help identify new areas for improvement.
Be ready to adjust strategies based on changing demands or new insights.
Ongoing evaluation ensures the lean process adapts to the evolving needs of the organization and its customers.
Tools and Techniques in Lean Production
Lean production employs various tools and techniques to streamline operations and eliminate waste.
Understanding these tools is essential for effective implementation.
5S Methodology
5S is a workplace organization method with five phases: Sort, Set in order, Shine, Standardize, and Sustain.
It focuses on maintaining an orderly workplace to improve productivity and safety.
Just-In-Time (JIT)
JIT is a production strategy aimed at reducing times within the production system as well as response times from suppliers and to customers.
Materials are produced or acquired only as required for use, reducing inventory costs.
Kanban
Kanban is a scheduling system that helps determine what to produce, when to produce it, and how much to produce.
It uses visual signals (cards or electronic boards) to communicate tasks and streamline production.
Value Stream Mapping (VSM)
VSM is a tool used for analyzing the flow of materials and information required to bring a product to a customer.
It helps identify waste and areas of improvement in the production process.
Total Productive Maintenance (TPM)
TPM focuses on maintaining and improving manufacturing equipment integrity.
It aims to increase productivity by reducing downtime and enhancing reliability and quality.
The Role of New Employees in Lean Production
As new employees, you play a critical role in the lean journey.
Your fresh perspective can bring valuable insights into identifying inefficiencies.
Engage actively in lean training and apply the concepts you learn to your daily tasks.
Always seek opportunities for improvement, and don’t hesitate to share your ideas with coworkers and management.
Lean production is not a one-time project but an ongoing process that requires dedication and teamwork.
By understanding and implementing lean principles, you can contribute significantly to the success of your organization, ensuring a culture of continuous improvement and high-quality production.
資料ダウンロード
QCD調達購買管理クラウド「newji」は、調達購買部門で必要なQCD管理全てを備えた、現場特化型兼クラウド型の今世紀最高の購買管理システムとなります。
ユーザー登録
調達購買業務の効率化だけでなく、システムを導入することで、コスト削減や製品・資材のステータス可視化のほか、属人化していた購買情報の共有化による内部不正防止や統制にも役立ちます。
NEWJI DX
製造業に特化したデジタルトランスフォーメーション(DX)の実現を目指す請負開発型のコンサルティングサービスです。AI、iPaaS、および先端の技術を駆使して、製造プロセスの効率化、業務効率化、チームワーク強化、コスト削減、品質向上を実現します。このサービスは、製造業の課題を深く理解し、それに対する最適なデジタルソリューションを提供することで、企業が持続的な成長とイノベーションを達成できるようサポートします。
オンライン講座
製造業、主に購買・調達部門にお勤めの方々に向けた情報を配信しております。
新任の方やベテランの方、管理職を対象とした幅広いコンテンツをご用意しております。
お問い合わせ
コストダウンが利益に直結する術だと理解していても、なかなか前に進めることができない状況。そんな時は、newjiのコストダウン自動化機能で大きく利益貢献しよう!
(Β版非公開)