- お役立ち記事
- Basics and practice of controller design using PID control
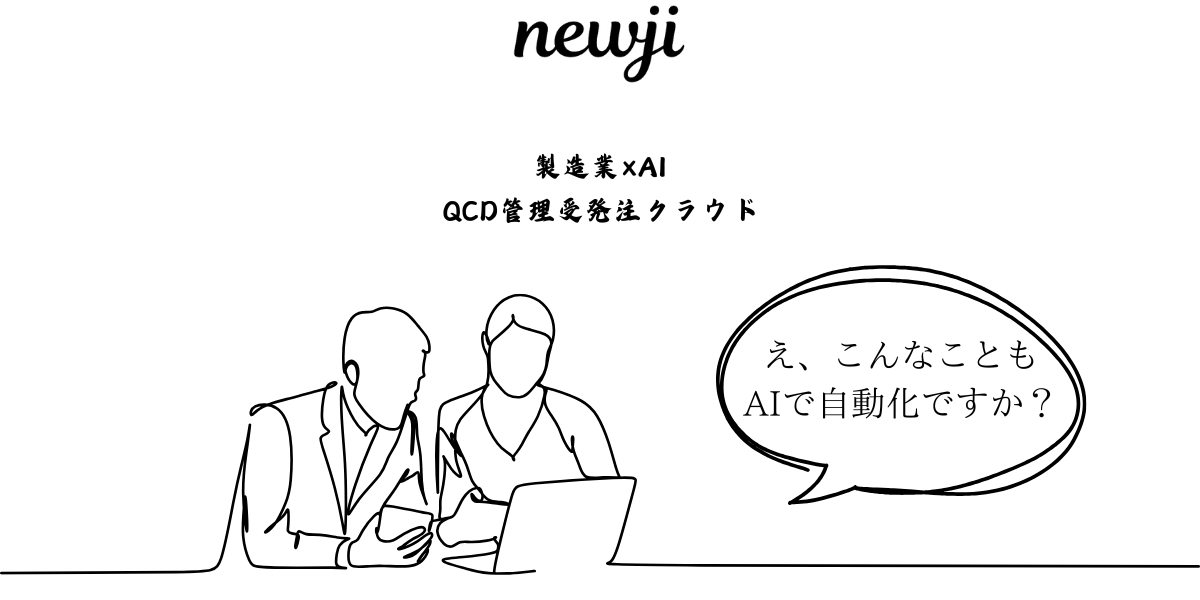
Basics and practice of controller design using PID control
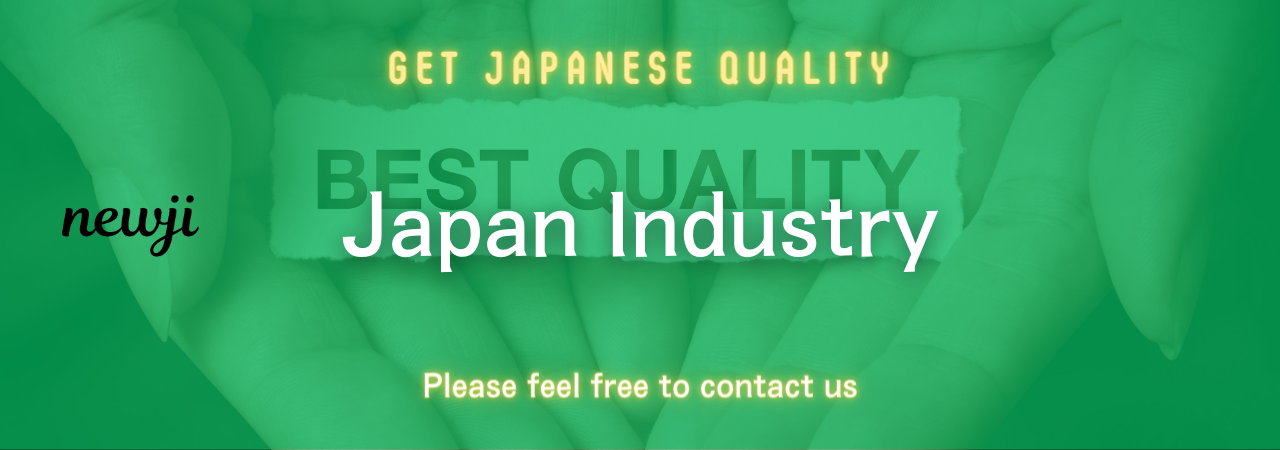
PID Control: The Basics and Practical Approaches
目次
What is PID Control?
PID control is a common feedback loop mechanism widely used in industrial control systems.
The term “PID” stands for Proportional, Integral, and Derivative, which are the three essential components of the controller.
Understanding the PID Components
A PID controller calculates an “error value” as the difference between a desired setpoint and a measured process variable.
The controller attempts to minimize this error by adjusting the process control inputs based on the following strategies:
Proportional Control (P)
The proportional component is based on the present error value.
The controller applies a correction proportional to the error, meaning if the error is large, the control effort is strong.
However, proportional control alone can lead to a steady-state error, where the system never settles exactly at the setpoint.
Integral Control (I)
The integral component sums the error over time.
If a steady-state error exists, the integral action will accumulate over time, increasing the control action to eliminate the error.
This component is essential for ensuring zero steady-state errors but may introduce overshoot and oscillations if not tuned properly.
Derivative Control (D)
The derivative component predicts system behavior.
By considering the rate of change of the error, the D-component helps mitigate excessive overshooting and oscillations by dampening the system response.
However, it is sensitive to noise in the error signal, and overuse can lead to undesirable performance.
How Does PID Control Work?
The magic of PID control lies in its ability to fine-tune performance by adjusting the three coefficients: Kp, Ki, and Kd.
These coefficients determine the strength of each component of the controller — proportional (P), integral (I), and derivative (D).
Kp: Proportional Coefficient
The proportional gain (Kp) scales the error to produce a corrective action proportional to the error.
A higher Kp means more aggressive response and reduces the rise time, but it can cause overshooting and instability if too high.
Ki: Integral Coefficient
The integral gain (Ki) influences the amount of cumulative error correction.
Higher Ki values can eliminate steady-state errors more effectively but can lead to excessive overshoot and oscillations.
Kd: Derivative Coefficient
The derivative gain (Kd) affects the system’s ability to dampen the rate of error change.
A higher Kd can improve stability and response, but excessive use can increase noise sensitivity.
Applications of PID Control
PID controllers are ubiquitous, finding applications across industries due to their simplicity and effectiveness.
Industrial Automation
In manufacturing, PID controllers are used to regulate temperature, pressure, speed, flow, and other process variables.
They ensure that machines and processes operate within optimal parameters.
Robotics
Robots utilize PID control for motion and trajectory control.
The precision of PID control allows robots to move smoothly and accurately to desired positions.
HVAC Systems
Heating, ventilation, and air conditioning (HVAC) systems often use PID controllers to maintain temperature and humidity at comfortable levels while optimizing energy efficiency.
Automotive Cruise Control
In vehicles, cruise control systems apply PID controllers to maintain a steady speed.
The proportional term responds to speed deviations, while the integral and derivative terms help achieve smooth acceleration and deceleration.
Practical Tips for Designing PID Controllers
Tuning a PID controller involves finding the right balance of the Kp, Ki, and Kd parameters to achieve desirable performance.
Manual Tuning
Start with Kp, increasing it until the system oscillates, then reduce it by half.
Next, increase Ki to decrease the steady-state error and finally adjust Kd to fine-tune response speed and stability.
Ziegler-Nichols Method
This empirical method involves setting Ki and Kd to zero, gradually increasing Kp until reaching the critical gain where the system oscillates, and using this data to calculate the PID values.
Use of Simulation Tools
Utilize simulation software to model your system and test different PID values.
Simulation avoids real-world risks and helps visualize the controller impact.
Gain Scheduling
For systems with varying dynamics, gain scheduling adjusts the PID parameters in real-time based on changing conditions.
This approach ensures optimal performance across different operating ranges.
Challenges and Considerations
While PID controllers are versatile, certain challenges can arise during implementation.
Noise Sensitivity
Derivative action can magnify noise, leading to erratic control output.
Using filters or reducing Kd can mitigate this issue.
Process Non-linearity
Non-linear processes require adaptive or model-based control strategies as traditional PID control may not provide satisfactory results.
Stability and Robustness
Finding a balance between responsiveness and stability is critical.
Poorly tuned controllers can lead to instability and system damage.
Conclusion
PID control remains a cornerstone in automation due to its simplicity and robustness.
By understanding the roles of the proportional, integral, and derivative components, and carefully tuning the PID parameters, engineers can optimize process performance.
Continued advances in control theory and technology promise to further enhance the capabilities and applications of PID control systems.
資料ダウンロード
QCD調達購買管理クラウド「newji」は、調達購買部門で必要なQCD管理全てを備えた、現場特化型兼クラウド型の今世紀最高の購買管理システムとなります。
ユーザー登録
調達購買業務の効率化だけでなく、システムを導入することで、コスト削減や製品・資材のステータス可視化のほか、属人化していた購買情報の共有化による内部不正防止や統制にも役立ちます。
NEWJI DX
製造業に特化したデジタルトランスフォーメーション(DX)の実現を目指す請負開発型のコンサルティングサービスです。AI、iPaaS、および先端の技術を駆使して、製造プロセスの効率化、業務効率化、チームワーク強化、コスト削減、品質向上を実現します。このサービスは、製造業の課題を深く理解し、それに対する最適なデジタルソリューションを提供することで、企業が持続的な成長とイノベーションを達成できるようサポートします。
オンライン講座
製造業、主に購買・調達部門にお勤めの方々に向けた情報を配信しております。
新任の方やベテランの方、管理職を対象とした幅広いコンテンツをご用意しております。
お問い合わせ
コストダウンが利益に直結する術だと理解していても、なかなか前に進めることができない状況。そんな時は、newjiのコストダウン自動化機能で大きく利益貢献しよう!
(Β版非公開)