- お役立ち記事
- Basics and practice of fluid analysis using open CAE
月間77,185名の
製造業ご担当者様が閲覧しています*
*2025年2月28日現在のGoogle Analyticsのデータより
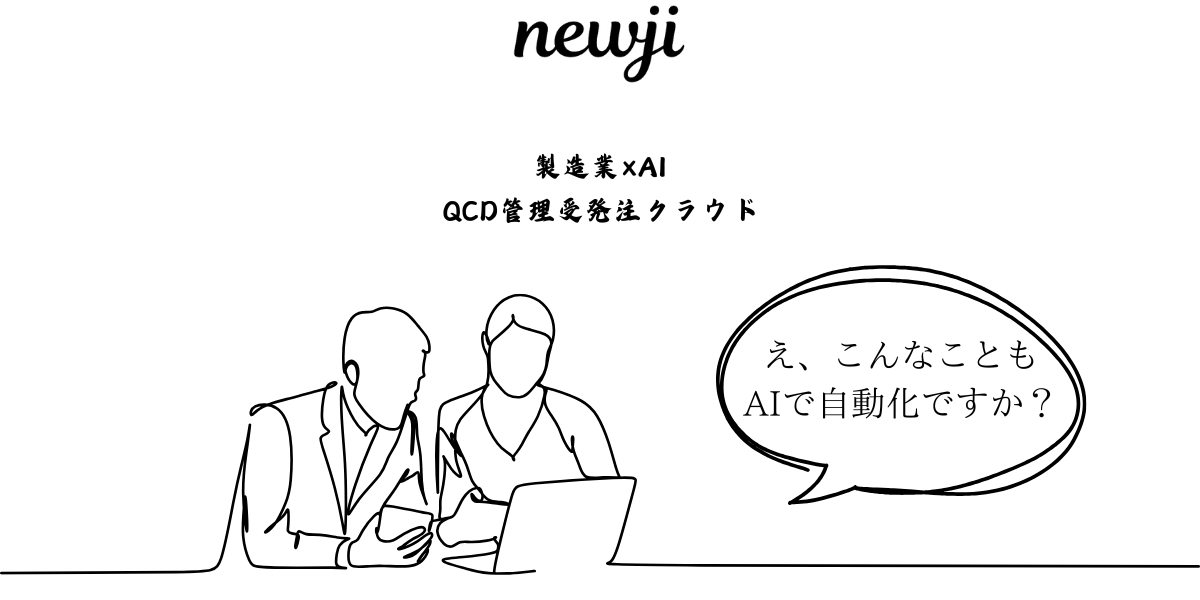
Basics and practice of fluid analysis using open CAE
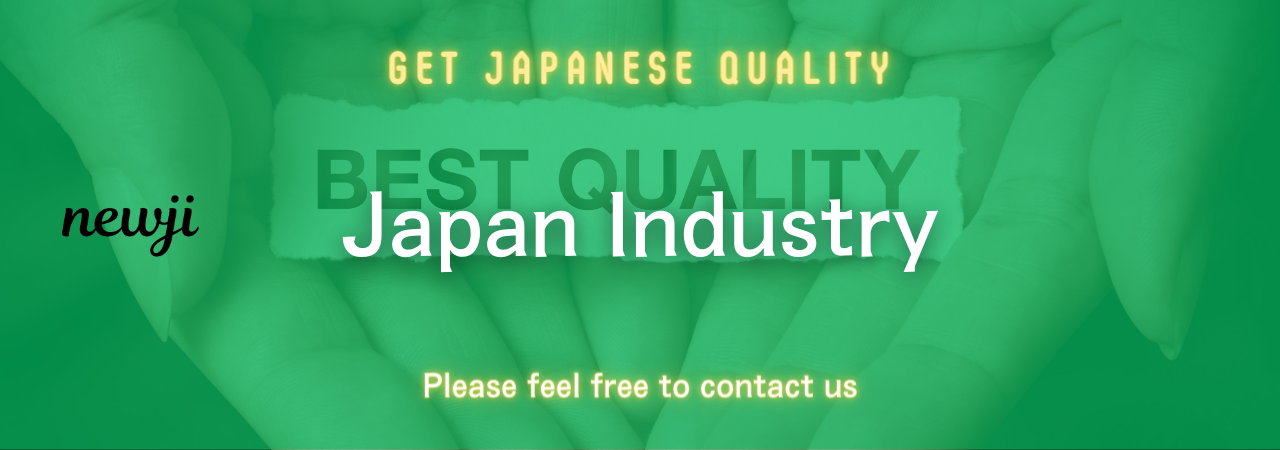
Fluid analysis, an essential part of engineering and science, involves the study of fluid flow behaviors in various situations. Open-source Computer-Aided Engineering (CAE) tools have become popular for conducting these analyses. They offer cost-effective and flexible solutions for engineers and researchers worldwide. This article delves into the basics and practices of fluid analysis using open CAE, aiming to guide beginners in understanding the foundational concepts and how to effectively utilize these tools.
目次
Understanding Fluid Analysis
Fluid analysis, also known as computational fluid dynamics (CFD), is the process of simulating fluid flow, heat transfer, and related phenomena. It plays a crucial role in many industrial applications like aerospace, automotive, and civil engineering. By analyzing the fluid behavior, engineers can optimize designs, improve performance, and ensure safety.
The fundamental equations governing fluid dynamics are the Navier-Stokes equations. These equations describe how the velocity field of a fluid evolves over time. Solving these equations for every point in the fluid domain can be computationally intensive, which is why CFD software is utilized.
Importance of Fluid Analysis
Fluid analysis helps engineers understand how fluids will behave under different conditions. This knowledge is vital for designing efficient systems and improving existing processes. For example, in the automotive industry, fluid analysis is used to enhance aerodynamics, leading to better fuel efficiency and performance.
Moreover, fluid analysis is crucial for environmental studies, such as modeling ocean currents or predicting weather patterns. It also aids in designing HVAC systems to ensure comfortable indoor environments.
Basic Principles
To effectively conduct fluid analysis, one must grasp several basic principles:
– **Continuity Equation:** This principle states that mass is conserved in a fluid flow, meaning the mass entering a system equals the mass leaving it.
– **Momentum Equation:** Derived from Newton’s second law, it explains the forces acting on the fluid.
– **Energy Equation:** This relates to the conservation of energy within the fluid system, considering factors such as heat transfer and fluid viscosity.
Understanding these principles helps in setting up realistic simulations and interpreting the results accurately.
Introduction to Open CAE for Fluid Analysis
Open-source CAE tools are incredibly beneficial for fluid analysis, particularly for those starting or working with limited budgets. These tools provide powerful capabilities comparable to commercial software, but without the cost. Additionally, the open-source nature allows for customization and innovation.
Popular Open CAE Tools
Several open-source CAE tools have gained popularity for fluid analysis:
– **OpenFOAM:** A widely-used open-source CFD toolbox. It supports a wide variety of solvers and is highly customizable.
– **Salome:** Often used in conjunction with OpenFOAM, Salome provides an interface for pre-processing, including mesh generation.
– **ParaView:** An open-source data analysis and visualization tool that supports large datasets, ideal for interpreting fluid dynamics results.
– **CFD-Post:** Often used for post-processing CFD simulations, providing visual representation and analysis of the flow data.
Advantages of Using Open CAE
Open-source CAE tools offer several advantages over their commercial counterparts:
– **Cost-Effectiveness:** There’s no licensing fee, making it accessible to students, researchers, and small businesses.
– **Flexibility and Customization:** Users can adapt the source code to meet specific needs or integrate new models and solvers.
– **Community Support:** A robust community provides forums, tutorials, and additional resources, facilitating learning and problem-solving.
Practicing Fluid Analysis Using Open CAE
For beginners looking to get started with fluid analysis using open CAE, understanding the workflow is crucial. The typical process involves several steps, including pre-processing, solving, and post-processing.
Pre-processing
In the pre-processing stage, users define the physical model, create a geometric representation, and generate the computational mesh. The mesh divides the domain into smaller cells, where calculations will be performed. Tools like Salome can be used for creating complex geometries and generating high-quality meshes.
Setting Up Simulations
Setting up a simulation involves defining boundary conditions, material properties, and solver parameters. It’s essential to configure these settings carefully, as they significantly impact the analysis results. OpenFOAM, for example, provides various solvers and turbulence models to cater to different flow characteristics.
Solving
Once the setup is complete, the solver is executed. This involves iteratively solving the governing equations over the mesh. Computational resources, such as CPU cores and memory, play a role in determining the speed and accuracy of the simulation. It’s crucial to monitor convergence to ensure the solution is stable and accurate.
Post-processing
After solving, the results need interpretation, which is where post-processing tools like ParaView come into play. They help visualize fluid flow characteristics, such as velocity fields, pressure distributions, and streamline patterns. This step is vital for validating results and identifying any design improvements.
Tips for Effective Fluid Analysis
While open CAE tools provide powerful capabilities, effective fluid analysis also requires a strategic approach:
– **Start Simple:** Begin with simpler models and progressively tackle more complex simulations. This approach helps build confidence and understanding.
– **Validate Models:** Compare simulation results with experimental data or analytical solutions to confirm accuracy.
– **Optimize Mesh:** A well-structured mesh can significantly affect the simulation’s accuracy and computational cost. Aim for a balance between resolution and performance.
– **Leverage Community Resources:** Engage with forums and discussion groups to solve problems and share insights.
Fluid analysis using open CAE presents an incredible opportunity for engineers and researchers to innovate and optimize designs without the hefty price of commercial tools. Through understanding the basics and adopting effective practices, users can unlock the full potential of these resources, driving advancements across various fields.
資料ダウンロード
QCD管理受発注クラウド「newji」は、受発注部門で必要なQCD管理全てを備えた、現場特化型兼クラウド型の今世紀最高の受発注管理システムとなります。
ユーザー登録
受発注業務の効率化だけでなく、システムを導入することで、コスト削減や製品・資材のステータス可視化のほか、属人化していた受発注情報の共有化による内部不正防止や統制にも役立ちます。
NEWJI DX
製造業に特化したデジタルトランスフォーメーション(DX)の実現を目指す請負開発型のコンサルティングサービスです。AI、iPaaS、および先端の技術を駆使して、製造プロセスの効率化、業務効率化、チームワーク強化、コスト削減、品質向上を実現します。このサービスは、製造業の課題を深く理解し、それに対する最適なデジタルソリューションを提供することで、企業が持続的な成長とイノベーションを達成できるようサポートします。
製造業ニュース解説
製造業、主に購買・調達部門にお勤めの方々に向けた情報を配信しております。
新任の方やベテランの方、管理職を対象とした幅広いコンテンツをご用意しております。
お問い合わせ
コストダウンが利益に直結する術だと理解していても、なかなか前に進めることができない状況。そんな時は、newjiのコストダウン自動化機能で大きく利益貢献しよう!
(β版非公開)