- お役立ち記事
- Basics and practice of the PDCA cycle in purchasing operations for new employees
Basics and practice of the PDCA cycle in purchasing operations for new employees
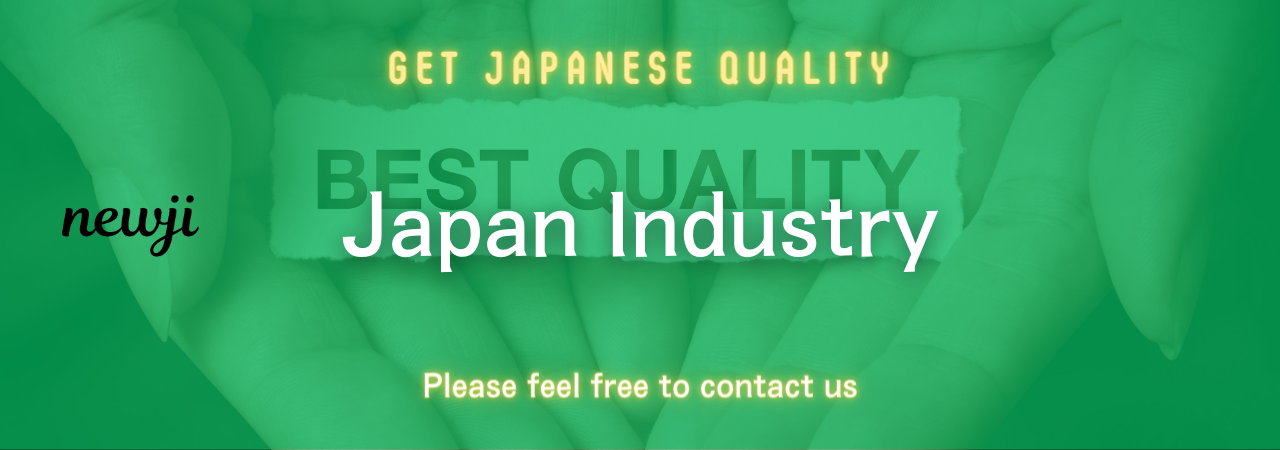
目次
Understanding the PDCA Cycle
The PDCA cycle, also known as the Deming Cycle or Plan-Do-Check-Act, is a continuous improvement model used in various industries to ensure effective management and process optimization.
For new employees in purchasing operations, understanding the PDCA cycle is crucial for managing tasks efficiently and driving improvements.
Let’s break down each component of the cycle to help you get a better grasp of its practical applications in purchasing.
Plan
The first step in the PDCA cycle is the Planning phase.
In purchasing operations, this involves identifying objectives, developing strategies, and outlining a detailed plan of action.
For new employees, it’s important to understand the needs and goals of your organization.
Start by assessing current procedures and identifying any potential areas for improvement.
Your plan should specify targets for cost reduction, efficiency enhancement, and improved supplier relationships.
Consider utilizing historical data to forecast demand and anticipate purchasing needs.
Clear objectives will serve as a guide for the rest of the process.
Do
The second step is the Doing phase, where the planned actions are implemented.
This is a critical stage where you’ll execute the developed strategies and begin making purchases based on your plan.
New employees should focus on adhering to the established procedures, but also be ready to respond to unexpected challenges.
During this phase, maintaining communication with suppliers and internal team members is vital.
Effective communication ensures everyone is aligned and any issues are addressed promptly.
Keep track of all actions taken during this phase.
This documentation will be useful for the next stages of the cycle.
Check
The Checking phase involves evaluating the results of the actions taken.
For new employees in purchasing, this means comparing what was achieved against the initial objectives.
Analyze the data collected to determine if targets were met, and examine any deviations from the plan.
Identify what worked well and what did not.
Look for trends in supplier performance, cost efficiency, and delivery times.
This analysis helps in understanding the root causes of any shortcomings.
Conducting a thorough review in this phase will inform necessary adjustments in the next step.
Act
The final stage is the Acting phase, where measures are taken to refine and improve the process based on insights gained during the Check phase.
For new employees, this might involve tweaking processes, adjusting strategies, or establishing new standards.
Addressing issues identified in the Check phase is essential for continuous improvement.
Implement modifications to your purchasing processes to enhance future performance.
Document these changes thoroughly to update the purchasing process guidelines.
This helps establish a baseline for the next PDCA cycle.
Continuous refinement ensures your purchasing operations remain efficient and effective.
The Importance of the PDCA Cycle in Purchasing Operations
For new employees in purchasing operations, the PDCA cycle offers a structured approach to managing tasks and facilitating improvements.
The cycle encourages proactive problem-solving and supports a culture of continuous improvement, which is crucial for any organization looking to stay competitive.
The PDCA cycle helps in identifying inefficiencies and waste in purchasing processes, leading to cost savings and better resource utilization.
Moreover, it promotes a more organized and systematic approach to managing supplier relationships, ensuring timely delivery and quality products.
By regularly applying the PDCA cycle, employees can also enhance their analytical skills, learning how to assess data and make informed decisions.
This not only benefits their professional development but also contributes to the overall success of the organization.
Practical Tips for New Employees
Here are a few practical suggestions for new employees applying the PDCA cycle in purchasing operations:
– **Start Small:** Begin with a small project or process that you can easily manage and track.
This will help you understand the cycle and build confidence before tackling larger tasks.
– **Be Organized:** Keep detailed records of your Plan, Do, Check, and Act stages.
Good documentation is essential for tracking progress and making informed adjustments.
– **Stay Informed:** Stay updated on industry trends and best practices in purchasing. This knowledge will be valuable in the planning and execution stages of the PDCA cycle.
– **Seek Feedback:** Don’t hesitate to ask for feedback from more experienced colleagues. Their insights can provide valuable perspectives and guidance.
– **Embrace Change:** Be open to change and innovation.
The PDCA cycle is all about continuous improvement, so always look for ways to enhance processes.
Conclusion
The PDCA cycle is an effective tool for driving improvements in purchasing operations.
By following the Plan-Do-Check-Act approach, new employees can systematically manage tasks and contribute to the overall efficiency and success of their organization.
Remember, applying the PDCA cycle is a continuous process.
Embrace it as a part of your routine, and you’ll be well-equipped to meet the challenges of purchasing operations head-on.
資料ダウンロード
QCD調達購買管理クラウド「newji」は、調達購買部門で必要なQCD管理全てを備えた、現場特化型兼クラウド型の今世紀最高の購買管理システムとなります。
ユーザー登録
調達購買業務の効率化だけでなく、システムを導入することで、コスト削減や製品・資材のステータス可視化のほか、属人化していた購買情報の共有化による内部不正防止や統制にも役立ちます。
NEWJI DX
製造業に特化したデジタルトランスフォーメーション(DX)の実現を目指す請負開発型のコンサルティングサービスです。AI、iPaaS、および先端の技術を駆使して、製造プロセスの効率化、業務効率化、チームワーク強化、コスト削減、品質向上を実現します。このサービスは、製造業の課題を深く理解し、それに対する最適なデジタルソリューションを提供することで、企業が持続的な成長とイノベーションを達成できるようサポートします。
オンライン講座
製造業、主に購買・調達部門にお勤めの方々に向けた情報を配信しております。
新任の方やベテランの方、管理職を対象とした幅広いコンテンツをご用意しております。
お問い合わせ
コストダウンが利益に直結する術だと理解していても、なかなか前に進めることができない状況。そんな時は、newjiのコストダウン自動化機能で大きく利益貢献しよう!
(Β版非公開)