- お役立ち記事
- Basics and practices of SLP (facility layout planning) that new leaders of production technology departments should know
ユーザー企業増加中
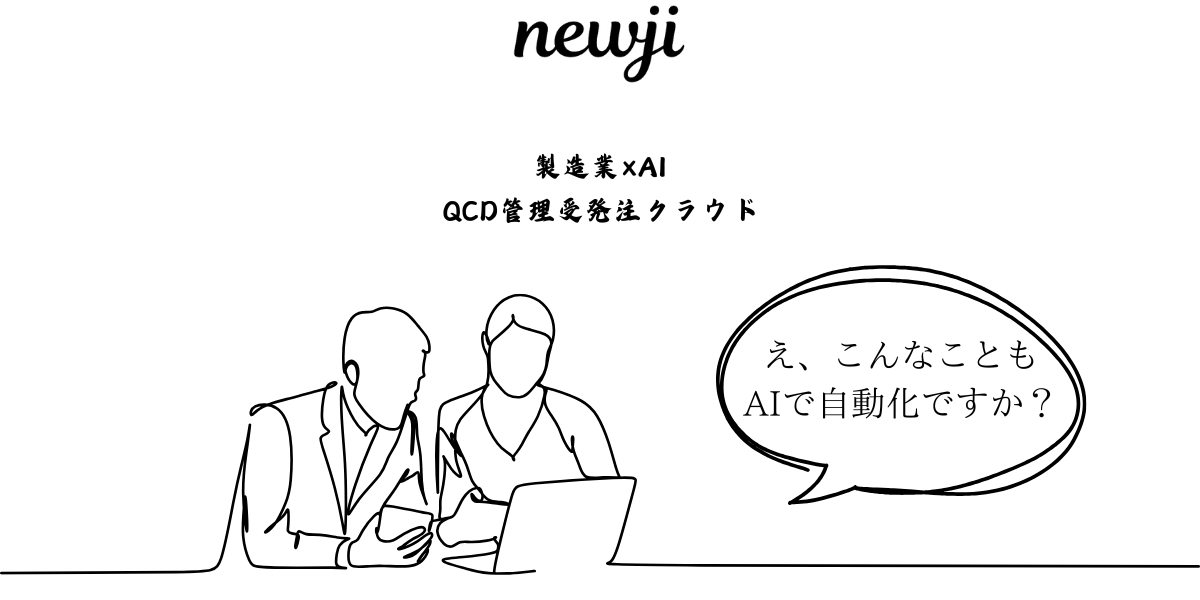
Basics and practices of SLP (facility layout planning) that new leaders of production technology departments should know
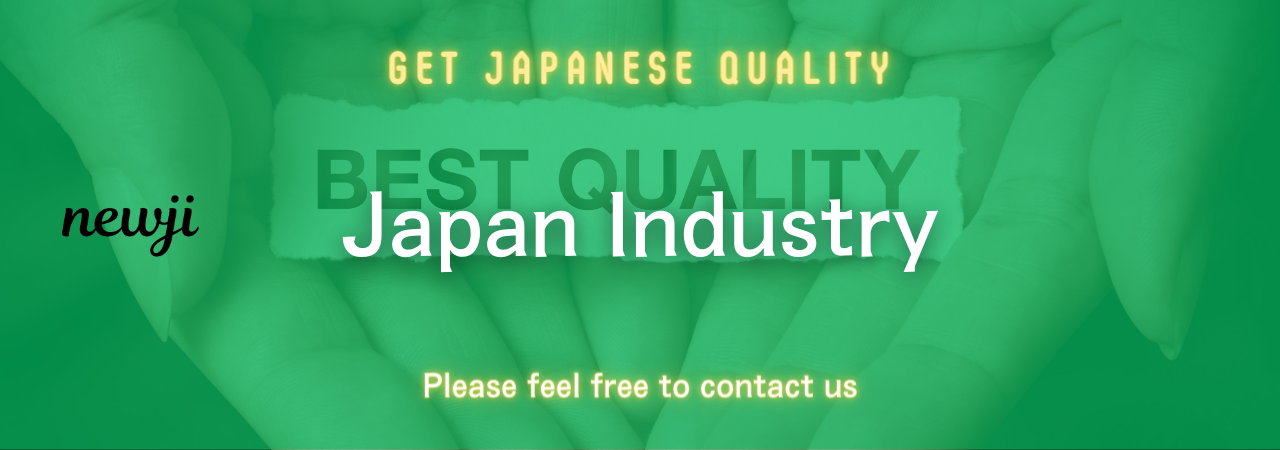
Understanding Facility Layout Planning
Facility Layout Planning (SLP) is a critical aspect of production technology, especially for new leaders stepping into the role.
In simple terms, SLP involves designing an optimal arrangement of physical facilities, such as machines, equipment, and work areas, to enhance productivity and efficiency.
The goal is to streamline operations, reduce waste, and improve workflow.
For anyone new to this field, mastering the basics and practices of SLP is essential for achieving operational success.
The Importance of Facility Layout Planning
Effective facility layout planning plays a significant role in the overall performance of a production unit.
A well-planned layout minimizes material handling costs, reduces production time, and maximizes space utilization.
This aligns with the strategic objectives of enhancing output while maintaining quality.
Moreover, a thoughtful layout can contribute to safer working conditions, enabling workers to perform their tasks with fewer interruptions and hazards.
Basic Principles of SLP
To get started with SLP, it’s important to understand some fundamental principles that guide the process.
These include:
1. **Systematic Arrangement:** Items must be organized systematically to facilitate a harmonious flow of materials, regardless of the type or size of the production facility.
2. **Flow Orientation:** The layout should ensure a smooth flow of materials and products from raw materials to finished goods.
3. **Space Utilization:** Efficient use of space is crucial.
This involves not only fitting everything within the physical constraints of the plant but also allowing room for movement and future expansion.
4. **Flexibility and Adaptability:** The layout must be flexible enough to handle changes in production volume, product design, or technology without significant disruptions.
5. **Safety and Comfort:** Prioritize the safety and comfort of workers.
A good layout minimizes risks and makes the work environment more pleasant and productive.
Process of Facility Layout Planning
The process of SLP involves several stages, each critical to developing a layout that supports the organization’s goals.
Initial Analysis
This initial phase requires a detailed analysis of the facility’s requirements.
Understanding the production process and the specific needs of each section is fundamental.
This includes examining material flow, machinery needs, and workforce requirements to identify key areas for improvement.
Flow Planning
Next, map out the flow of materials and the sequence of operations.
This stage is crucial for identifying bottlenecks and areas where processes can be optimized.
Analyzing the flow helps in visualizing how materials travel through the facility and can highlight inefficiencies.
Development of Layout Alternatives
Based on the analysis and flow planning, develop several layout alternatives.
These should cater to different aspects such as space, cost, and scalability.
Considering multiple layouts allows for comparison and helps identify the most efficient option.
Evaluation and Selection
Evaluate each layout alternative based on criteria like cost-effectiveness, ease of implementation, flexibility, and potential for future growth.
Using tools like simulations or modeling software can help predict the performance of each layout.
Implementation and Optimization
After selecting the best layout, proceed with implementation.
This involves restructuring the physical space and setting up equipment according to the new plan.
Once implemented, monitor the layout for performance and make necessary adjustments to optimize productivity continuously.
Common Challenges in SLP
Facility layout planning can present several challenges, especially for those new to the field.
These include constrained space, budget limitations, and evolving technology demands.
Balancing these factors while maintaining operational efficiency requires strategic thinking and flexibility.
An effective way to overcome these challenges is through continuous learning and adaptation.
Staying updated on industry trends and advancements can provide insights into innovative layout strategies.
Leveraging Technology in SLP
In today’s rapidly advancing technological landscape, leveraging technology can enhance SLP processes significantly.
Utilizing software tools for simulation and modeling can offer a virtual preview of layout designs, helping identify potential issues before physical implementation.
Moreover, data analytics can provide deep insights into production patterns, aiding in making informed decisions when planning facility layouts.
Collaboration and Communication
Effective SLP requires collaboration across various departments, including production, engineering, and management.
Open communication ensures that all stakeholders have input in the layout design, aligning with broader organizational goals.
Regular meetings and feedback sessions can enhance the layout planning process by incorporating diverse perspectives and expertise.
Conclusion
Facility Layout Planning (SLP) is an indispensable aspect of production technology that significantly impacts operational success.
For new leaders stepping into the role, understanding the basics and practices of SLP is crucial.
By adhering to fundamental principles, systematically planning the process, and leveraging technology, new leaders can effectively design layouts that enhance productivity and safety.
With strategic planning, collaboration, and continuous improvement, SLP can lay the foundation for efficient and successful production technology operations.
資料ダウンロード
QCD調達購買管理クラウド「newji」は、調達購買部門で必要なQCD管理全てを備えた、現場特化型兼クラウド型の今世紀最高の購買管理システムとなります。
ユーザー登録
調達購買業務の効率化だけでなく、システムを導入することで、コスト削減や製品・資材のステータス可視化のほか、属人化していた購買情報の共有化による内部不正防止や統制にも役立ちます。
NEWJI DX
製造業に特化したデジタルトランスフォーメーション(DX)の実現を目指す請負開発型のコンサルティングサービスです。AI、iPaaS、および先端の技術を駆使して、製造プロセスの効率化、業務効率化、チームワーク強化、コスト削減、品質向上を実現します。このサービスは、製造業の課題を深く理解し、それに対する最適なデジタルソリューションを提供することで、企業が持続的な成長とイノベーションを達成できるようサポートします。
オンライン講座
製造業、主に購買・調達部門にお勤めの方々に向けた情報を配信しております。
新任の方やベテランの方、管理職を対象とした幅広いコンテンツをご用意しております。
お問い合わせ
コストダウンが利益に直結する術だと理解していても、なかなか前に進めることができない状況。そんな時は、newjiのコストダウン自動化機能で大きく利益貢献しよう!
(Β版非公開)