- お役立ち記事
- Basics and practices of SLP (facility layout planning) that new leaders of production technology departments should know
ユーザー企業増加中
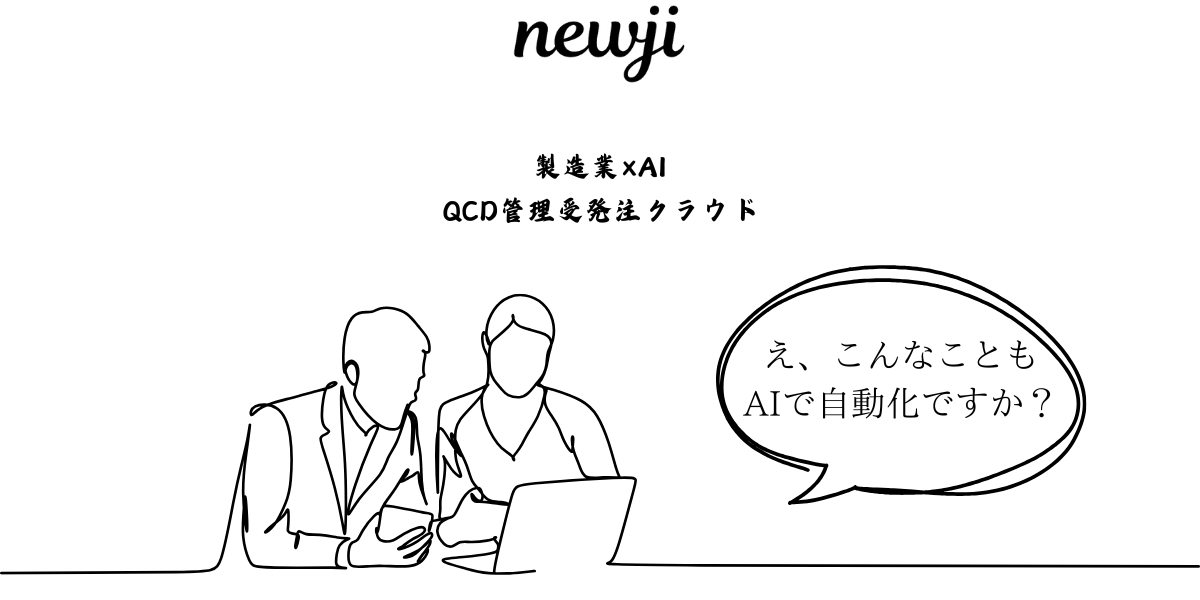
Basics and practices of SLP (facility layout planning) that new leaders of production technology departments should know
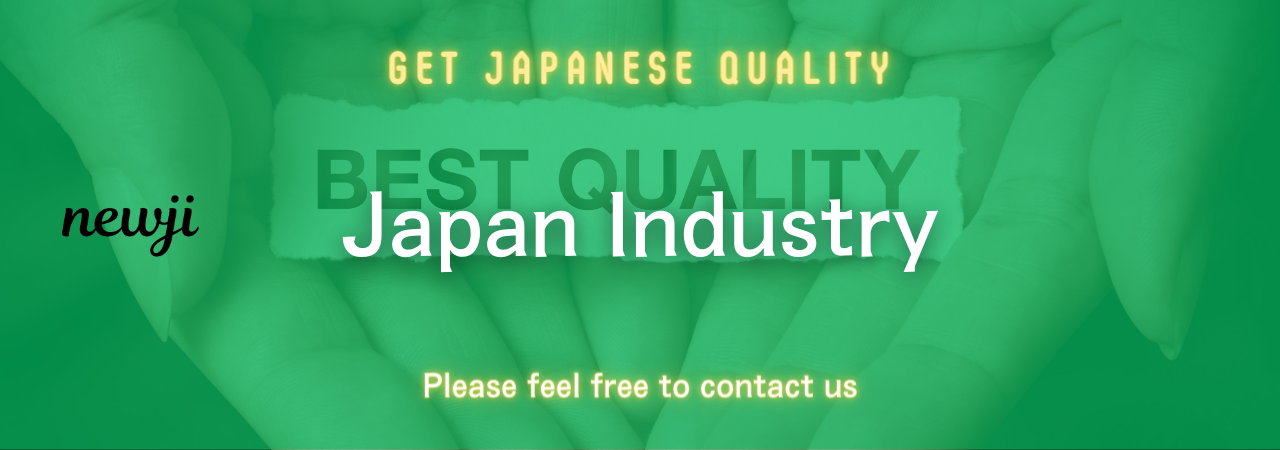
目次
Understanding Facility Layout Planning (SLP)
Facility layout planning, commonly referred to as Systematic Layout Planning (SLP), is a crucial element in the success of any manufacturing operation.
It involves arranging machinery, equipment, and other physical resources within a plant to optimize production efficiency and safety.
As a new leader in the production technology department, understanding the principles and applications of SLP can significantly enhance your team’s performance.
The core of SLP revolves around improving workflow and reducing waste, leading to increased productivity and reduced operational costs.
An efficient layout can make a world of difference in a plant’s functionality by minimizing material handling, improving work conditions, and ensuring safety standards.
Thus, grasping the basics of SLP will empower you to make informed decisions that drive your facility towards operational excellence.
The Importance of Facility Layout Planning
The role of facility layout planning in a manufacturing environment cannot be overstated.
A well-designed layout not only streamlines the production process but also enhances the overall work environment.
The benefits of SLP extend beyond just the technical aspects, affecting various facets of productivity and employee well-being.
One of the main objectives of SLP is to enhance productivity by reducing the distance materials and products travel within the facility.
When the layout is optimized, the movement of goods, as well as the flow of work, becomes more efficient.
This directly translates to time savings and cost reductions, which are vital components of a competitive manufacturing operation.
Additionally, safety is a pivotal concern in any production facility.
Proper facility layout planning includes designing safe pathways and workstations to minimize the risk of accidents.
When safety is integrated into the layout, it contributes to a healthier work environment and reduces potential liabilities for the company.
Steps to Implement Facility Layout Planning
Implementing SLP involves several stages, each designed to build upon the last.
Understanding these steps can help you to effectively oversee the layout planning process.
1. Define Objectives
The first step in SLP is to clearly define the objectives of the layout.
This includes understanding what the facility needs to achieve, such as increased production rates, improved safety, or better utilization of space.
By setting clear objectives, the planning team can focus on what needs to be achieved.
2. Analyze the Current Layout
Before making any changes, it is important to analyze the existing layout.
This involves studying the flow of materials, workers, and information within the facility.
Gathering data on current operations provides insights into workflow bottlenecks and areas for improvement.
3. Develop Layout Alternatives
Once the current layout has been thoroughly analyzed, it is time to develop alternative layouts.
These alternatives should consider different ways of arranging equipment, workstations, and pathways that align with the defined objectives.
Using computer simulations or models can facilitate the testing of these alternatives without disrupting ongoing operations.
4. Evaluate and Select the Best Layout
After developing several layout alternatives, the next step is to evaluate each one against set criteria such as cost, safety, and efficiency.
This evaluation helps to identify the most feasible and beneficial layout for the facility.
5. Implement the Layout
Once the best layout is selected, it is time for implementation.
This phase requires careful planning to minimize disruption to production.
It may involve phased implementation or scheduling changes during off-peak hours to ensure a smooth transition.
6. Review and Adjust
After implementation, it is crucial to review the performance of the new layout.
Gather feedback from employees and conduct performance analyses to identify any potential issues.
Continuous monitoring allows for adjustments to be made, ensuring the layout remains effective over time.
Challenges in Facility Layout Planning
While the benefits of an efficient layout are clear, several challenges can arise during the process.
Being aware of these potential hurdles can better prepare you to tackle them.
One major challenge is resistance to change.
Employees may be hesitant to adapt to a new layout, which can affect productivity and morale.
Effective communication about the benefits and rationale behind the changes can help alleviate these concerns.
Another challenge is balancing the various factors involved in layout planning, such as cost, space limitations, and workflow efficiency.
Achieving an optimal layout often requires trade-offs, and as a leader, it is important to weigh these carefully.
Finally, technological advancement continually changes the landscape of manufacturing operations.
Staying informed about new technologies and incorporating them into the layout plan can be challenging but is essential for maintaining a competitive edge.
Conclusion
Facility layout planning is a dynamic process that significantly impacts the effectiveness of a production facility.
By understanding the fundamentals and following a systematic approach, new leaders can design and implement layouts that enhance productivity, safety, and employee satisfaction.
Navigating the complexities of SLP with an informed perspective allows for creating environments that not only meet today’s demands but are also adaptable to future challenges.
資料ダウンロード
QCD調達購買管理クラウド「newji」は、調達購買部門で必要なQCD管理全てを備えた、現場特化型兼クラウド型の今世紀最高の購買管理システムとなります。
ユーザー登録
調達購買業務の効率化だけでなく、システムを導入することで、コスト削減や製品・資材のステータス可視化のほか、属人化していた購買情報の共有化による内部不正防止や統制にも役立ちます。
NEWJI DX
製造業に特化したデジタルトランスフォーメーション(DX)の実現を目指す請負開発型のコンサルティングサービスです。AI、iPaaS、および先端の技術を駆使して、製造プロセスの効率化、業務効率化、チームワーク強化、コスト削減、品質向上を実現します。このサービスは、製造業の課題を深く理解し、それに対する最適なデジタルソリューションを提供することで、企業が持続的な成長とイノベーションを達成できるようサポートします。
オンライン講座
製造業、主に購買・調達部門にお勤めの方々に向けた情報を配信しております。
新任の方やベテランの方、管理職を対象とした幅広いコンテンツをご用意しております。
お問い合わせ
コストダウンが利益に直結する術だと理解していても、なかなか前に進めることができない状況。そんな時は、newjiのコストダウン自動化機能で大きく利益貢献しよう!
(Β版非公開)