- お役立ち記事
- Basics and principles of injection molding
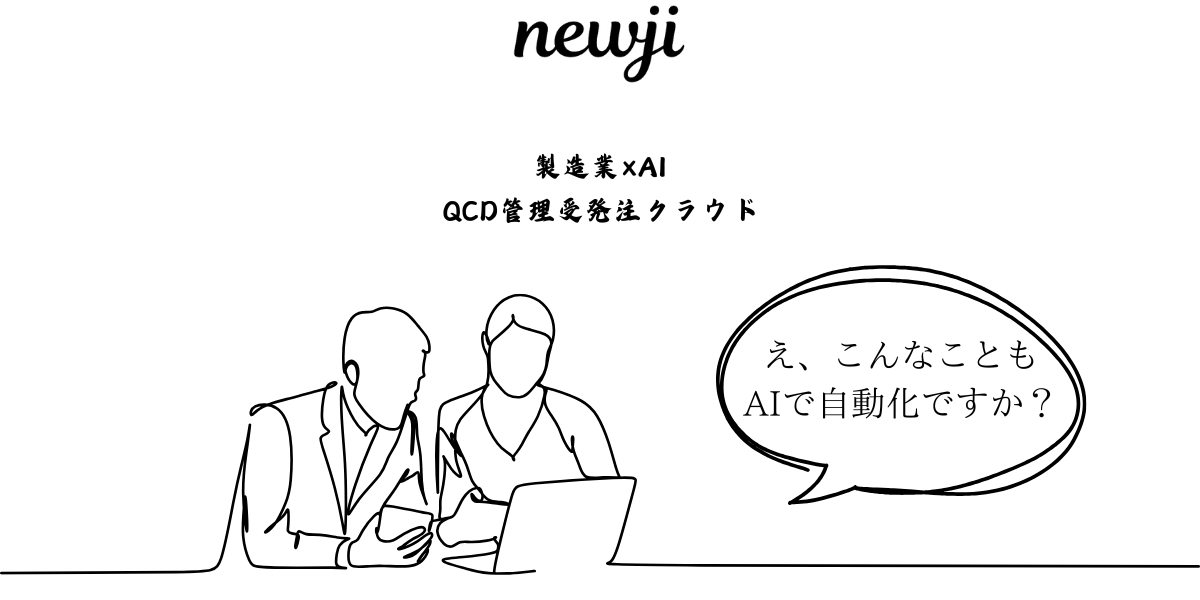
Basics and principles of injection molding
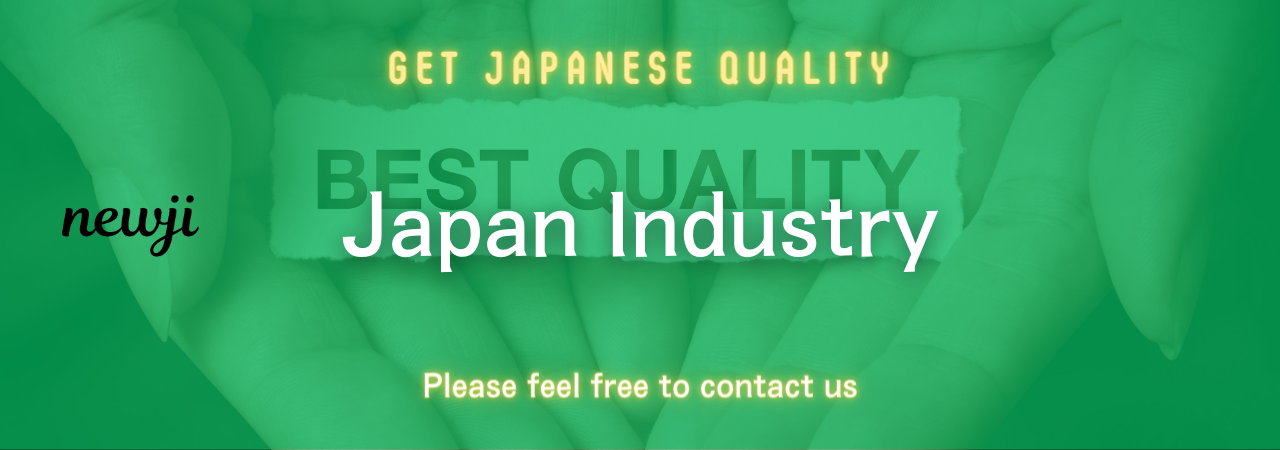
目次
Introduction to Injection Molding
Injection molding is a manufacturing process used to produce large volumes of identical items.
This method is popular in various industries because of its ability to create intricate shapes at high precision and low cost.
Understanding the basics and principles of injection molding can help you appreciate how everyday objects are made.
What is Injection Molding?
Injection molding involves injecting molten material into a mold to create a desired shape.
This process is used mainly for plastics but can also be applied to metals and glass.
The injected material cools and solidifies, taking the shape of the mold cavity.
The finished product is then ejected, ready for use or additional processing.
The History of Injection Molding
The concept of injection molding dates back to the late 19th century.
Its development accelerated in the 20th century with the creation of synthetic plastics.
The industrial revolution further advanced technology, allowing for mass production of plastic products.
Materials Used in Injection Molding
While thermoplastics are the most commonly used materials, thermosetting plastics and elastomers are also employed.
Polyethylene, polystyrene, and polyvinyl chloride are popular choices due to their versatility and durability.
Each material has unique properties that influence the end product’s characteristics.
Thermoplastics
Thermoplastics are widely used in injection molding.
They become pliable upon heating and return to their solid state when cooled.
The ability to be repeatedly melted and solidified makes these plastics perfect for recycling.
Thermosetting Plastics
Unlike thermoplastics, thermosetting plastics cannot be remelted once they are hardened.
They undergo a curing process that sets their shape permanently.
These materials offer higher resistance to heat and chemicals, making them suitable for demanding applications.
The Injection Molding Process
The injection molding process consists of several key steps:
Clamping
It begins with clamping, where the two halves of the mold are secured in place.
A powerful clamping unit holds them together under pressure, preventing material leakage during injection.
Injection
The molten material, usually plastic, is fed into a heated barrel.
A screw mechanism pushes the material forward, through the barrel, and into the mold cavity at high speed.
Cooling
Once inside the mold, the material begins to cool and solidify.
Cooling time is crucial, as insufficient cooling can lead to defects in the final product.
Ejection
After cooling, the mold opens, and the product is ejected using ejector pins.
This step must be precise to avoid causing damage to the part.
Finishing
The final stage often involves trimming excess material or performing additional processing to ensure high-quality standards.
Advantages of Injection Molding
Injection molding offers a host of advantages, making it a preferred choice for manufacturers.
Efficiency
Once the initial cost of designing and testing molds is covered, the process is exceptionally efficient for high-volume production.
A single mold can produce thousands, if not millions, of identical items.
Cost-Effectiveness
Despite the high upfront investment, the low per-unit cost makes it a cost-effective solution for large-scale manufacturing.
Materials are used efficiently, and labor costs are minimized.
Design Flexibility
Injection molding allows for complex designs and detailed features.
Multiple materials can be used simultaneously, and varying colors can easily be incorporated.
Challenges and Considerations
While injection molding is advantageous, it also presents some challenges.
Initial Costs
The creation of molds requires precision engineering and significant upfront investment.
Design changes during production can also be costly.
Production Lead Time
Designing and testing molds take time.
Delays in this phase can lead to longer lead times for new products.
Material Selection
Choosing the right material is crucial, as it affects the product’s strength, flexibility, and durability.
Consider environmental factors and the intended application of the end product.
Conclusion
Injection molding is a cornerstone of modern manufacturing, enabling the efficient and cost-effective production of complex designs.
Understanding its basics and principles is essential for anyone involved in product design or manufacturing.
As technology continues to advance, injection molding will likely find even wider applications, offering new opportunities for innovation and efficiency in product development.
資料ダウンロード
QCD調達購買管理クラウド「newji」は、調達購買部門で必要なQCD管理全てを備えた、現場特化型兼クラウド型の今世紀最高の購買管理システムとなります。
ユーザー登録
調達購買業務の効率化だけでなく、システムを導入することで、コスト削減や製品・資材のステータス可視化のほか、属人化していた購買情報の共有化による内部不正防止や統制にも役立ちます。
NEWJI DX
製造業に特化したデジタルトランスフォーメーション(DX)の実現を目指す請負開発型のコンサルティングサービスです。AI、iPaaS、および先端の技術を駆使して、製造プロセスの効率化、業務効率化、チームワーク強化、コスト削減、品質向上を実現します。このサービスは、製造業の課題を深く理解し、それに対する最適なデジタルソリューションを提供することで、企業が持続的な成長とイノベーションを達成できるようサポートします。
オンライン講座
製造業、主に購買・調達部門にお勤めの方々に向けた情報を配信しております。
新任の方やベテランの方、管理職を対象とした幅広いコンテンツをご用意しております。
お問い合わせ
コストダウンが利益に直結する術だと理解していても、なかなか前に進めることができない状況。そんな時は、newjiのコストダウン自動化機能で大きく利益貢献しよう!
(Β版非公開)