- お役立ち記事
- Basics and processing technology of aluminum alloys and application to automobiles for a decarbonized society
Basics and processing technology of aluminum alloys and application to automobiles for a decarbonized society
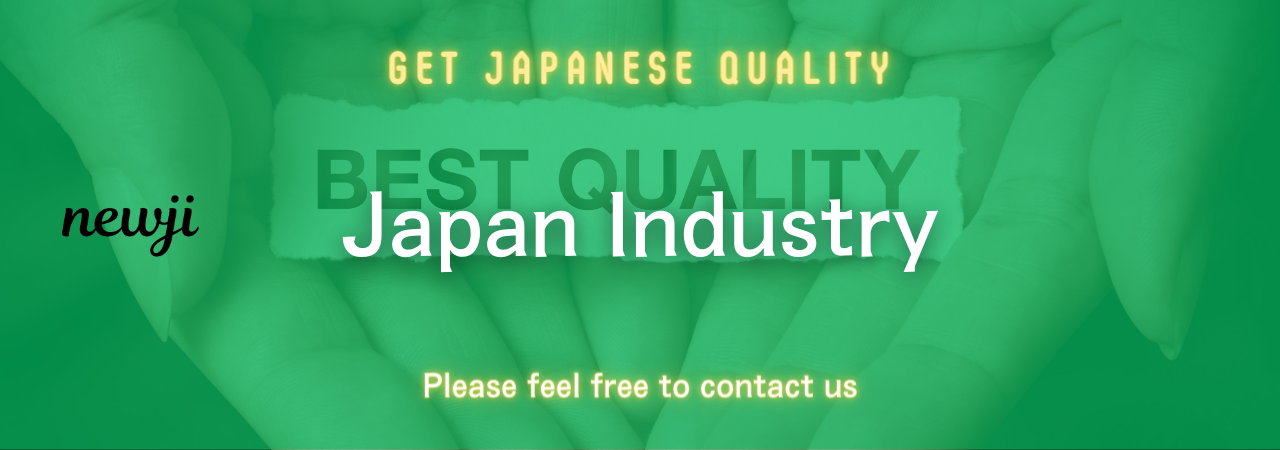
目次
Understanding Aluminum Alloys
Aluminum alloys are pivotal in a wide range of industries due to their remarkable properties.
These alloys are created by combining aluminum with other elements like copper, magnesium, silicon, and zinc.
This combination enhances aluminum’s natural properties, making it stronger, more durable, and resistant to corrosion.
In its pure form, aluminum is relatively soft.
However, when alloyed, it gains the strength necessary for industrial applications.
This versatility makes aluminum alloys a sought-after material for manufacturing lightweight and efficient components.
Types of Aluminum Alloys
Aluminum alloys are classified into two main categories: wrought and cast.
Each of these categories is divided further depending on the specific elements added and the processing techniques used.
1. **Wrought Aluminum Alloys**: These are mechanically worked into final shapes through rolling, extruding, or forging.
They are known for their excellent mechanical properties.
2. **Cast Aluminum Alloys**: As the name suggests, these alloys are shaped by pouring molten aluminum into a mold.
They are less expensive to produce and are frequently used in the production of complex shapes.
Within these categories, alloys are further classified by a four-digit numbering system.
The first digit indicates the principal alloying element, such as 1xxx for pure aluminum, 2xxx for copper, 3xxx for manganese, and so on.
Processing Technology of Aluminum Alloys
The processing of aluminum alloys involves several steps, each critical to achieving the desired material properties and characteristics.
Melting and Casting
The journey begins with melting raw aluminum and alloying elements.
This process requires precise temperature control to avoid contamination and ensure uniformity.
Once molten, the mixture is poured into molds to create ingots or billets suitable for further processing.
Forming Techniques
Forming techniques are utilized to shape aluminum alloys into their final forms.
Common forming processes include:
– **Rolling**: Used to produce sheets, plates, and foils.
– **Extrusion**: Forces the material through a die to create objects with a fixed cross-section.
– **Forging**: Involves shaping the metal through localized compressive forces.
Heat Treatment
Heat treatment is crucial in enhancing the mechanical properties of aluminum alloys.
This process involves heating and cooling the alloy in a controlled manner to adjust hardness, strength, and ductility.
Common heat treatment processes include:
– **Annealing**: Softens the material and improves workability.
– **Quenching**: Rapid cooling to increase hardness.
– **Aging**: A controlled natural or artificial process to maximize strength.
Machining
After forming and treating, machining operations are often required to achieve the precise specifications needed for the final product.
Techniques like milling, drilling, and turning are employed to refine the shape and finish of aluminum components.
Applications in the Automotive Industry
With the world striving for a decarbonized society, the automotive industry has increasingly turned to aluminum alloys as a solution for sustainable manufacturing.
These materials are lightweight yet strong, providing several advantages for car production.
Weight Reduction
One of the key benefits of using aluminum alloys in automobiles is weight reduction.
Reducing a vehicle’s weight leads to lower fuel consumption and emissions, aligning with global sustainability goals.
Cars made with aluminum components require less energy to operate, enhancing fuel efficiency and reducing the carbon footprint.
Improved Performance
Aluminum alloys offer excellent thermal conductivity, which helps in heat dissipation from engines and brake systems.
This property is crucial in ensuring the car’s performance and safety, especially under harsh conditions.
Moreover, the high strength-to-weight ratio of aluminum alloys improves the overall dynamics of the vehicle.
It contributes to better handling and acceleration, enhancing the driving experience.
Corrosion Resistance
Vehicles are constantly exposed to harsh environments, making corrosion resistance a vital factor in material selection.
Aluminum alloys naturally form a protective oxide layer, which shields them from moisture and environmental chemicals, ensuring longevity and reducing maintenance costs.
Versatility in Design
The versatility of aluminum alloys allows designers extensive freedom.
Complex shapes can be easily formed without compromising structural integrity, providing opportunities to innovate in both aesthetics and functionality.
This design flexibility is instrumental in meeting the diverse and evolving demands of automotive consumers.
Challenges and Future Outlook
Despite the advantages, there are challenges associated with aluminum alloy processing and application in the automotive industry.
Cost Considerations
Aluminum alloys are typically more expensive than traditional materials such as steel.
The cost of production and processing can pose a barrier, particularly for budget-intensive vehicle projects.
Technical Challenges
Working with aluminum requires specialized knowledge and equipment.
Ensuring uniformity and preventing defects during production can be technically challenging.
Future Prospects
Ongoing research and development are focused on making aluminum alloys more accessible and efficient.
Advancements in recycling can also play a significant role in reducing costs and environmental impact.
As the automotive industry continues to prioritize sustainability, the demand for lightweight, eco-friendly materials like aluminum alloys is expected to grow, fostering innovation and driving progress toward a greener future.
資料ダウンロード
QCD調達購買管理クラウド「newji」は、調達購買部門で必要なQCD管理全てを備えた、現場特化型兼クラウド型の今世紀最高の購買管理システムとなります。
ユーザー登録
調達購買業務の効率化だけでなく、システムを導入することで、コスト削減や製品・資材のステータス可視化のほか、属人化していた購買情報の共有化による内部不正防止や統制にも役立ちます。
NEWJI DX
製造業に特化したデジタルトランスフォーメーション(DX)の実現を目指す請負開発型のコンサルティングサービスです。AI、iPaaS、および先端の技術を駆使して、製造プロセスの効率化、業務効率化、チームワーク強化、コスト削減、品質向上を実現します。このサービスは、製造業の課題を深く理解し、それに対する最適なデジタルソリューションを提供することで、企業が持続的な成長とイノベーションを達成できるようサポートします。
オンライン講座
製造業、主に購買・調達部門にお勤めの方々に向けた情報を配信しております。
新任の方やベテランの方、管理職を対象とした幅広いコンテンツをご用意しております。
お問い合わせ
コストダウンが利益に直結する術だと理解していても、なかなか前に進めることができない状況。そんな時は、newjiのコストダウン自動化機能で大きく利益貢献しよう!
(Β版非公開)