- お役立ち記事
- Basics and utilization methods of joining dissimilar metals and materials and friction stir welding (FSW)
月間76,176名の
製造業ご担当者様が閲覧しています*
*2025年3月31日現在のGoogle Analyticsのデータより
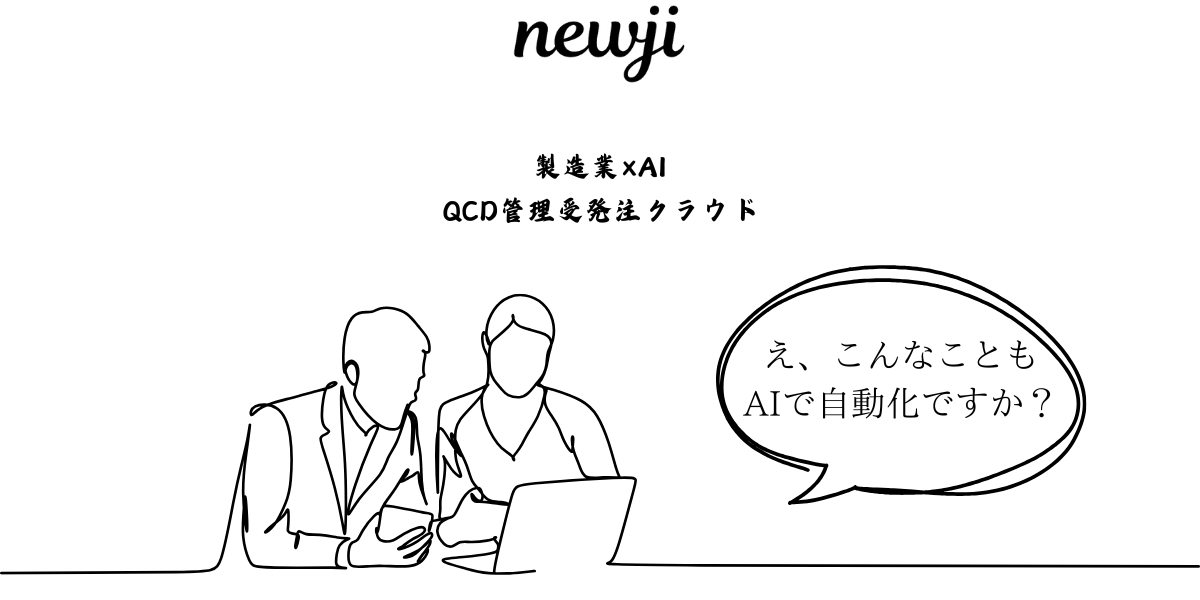
Basics and utilization methods of joining dissimilar metals and materials and friction stir welding (FSW)
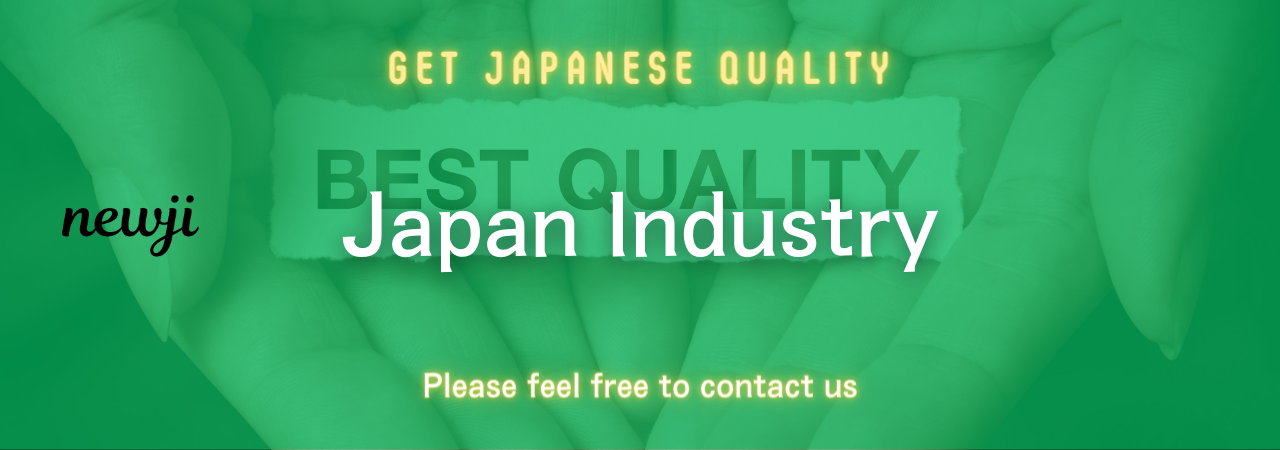
目次
Understanding the Basics of Joining Dissimilar Metals and Materials
Joining dissimilar metals and materials involves the challenging task of combining different types of metals, each with its own unique properties, into a cohesive unit.
This process is critical across various industries, as it allows manufacturers to leverage the advantages of different materials in a single product.
The primary challenge lies in the differences in melting points, thermal expansion, and metallurgical characteristics of the various metals or materials being joined.
Traditional methods, such as riveting or using adhesives, can be costly and may not provide the structural integrity required for certain applications.
Additionally, these methods often add extra weight to the final product, making them less efficient.
Modern technologies, however, offer advanced solutions to these challenges, enabling stronger bonds without compromising the benefits of the individual materials.
Why Join Dissimilar Metals?
The need to join dissimilar metals often arises from the desire to combine the beneficial properties of different materials.
For example, one metal might offer excellent tensile strength while another might provide superior corrosion resistance.
By joining these two metals, manufacturers can produce a component that maximizes both strength and durability.
In automotive and aerospace industries, the demand for lightweight yet strong materials is particularly high.
By joining dissimilar materials, manufacturers can reduce weight without compromising safety or performance.
This is also a common practice in electronics, where materials are chosen for their electrical conductivity or thermal management properties.
Introduction to Friction Stir Welding (FSW)
Friction Stir Welding (FSW) is an innovative solid-state joining process that has become a game-changer in the realm of material joining.
Unlike traditional welding methods that require melting the materials, FSW is performed below the melting point, thereby reducing the occurrence of defects such as porosity and cracking.
FSW involves a rotating tool that generates frictional heat at the interface of the materials being joined, softening them and enabling a strong bond upon cooling.
This method is particularly effective for joining aluminum alloys but is also used for other metals and dissimilar materials.
The FSW Process Explained
The FSW process begins with the positioning of the metals or materials to be joined on a supportive base.
A specially designed cylindrical tool with a probe and shoulder is then inserted into the materials.
As the tool rotates and moves along the joint, it generates heat through friction, softening the materials’ surface and allowing them to fuse together.
This process does not reach the melting point of the materials, which minimizes the likelihood of metallurgical defects.
The key advantages of FSW include reduced energy consumption, lower levels of distortion, and the capability to join metals that are difficult to weld using conventional techniques.
Applications of Friction Stir Welding
FSW has found applications in numerous industries due to its versatility and superior properties.
Automotive Industry
The automotive industry benefits significantly from FSW for joining aluminum and other lightweight materials.
The technique enhances the strength of automotive frames and components while ensuring that the vehicles remain lightweight, contributing to better fuel efficiency.
Aerospace Industry
In the aerospace sector, FSW is utilized for constructing lightweight yet strong aircraft components.
The reduction of weld-induced defects and the ability to join high-strength aluminum alloys make FSW an ideal choice for critical applications in aircraft manufacturing.
Shipbuilding
FSW is employed in the shipbuilding industry to join panels and sections of ships’ hulls, offering improved mechanical properties and reducing the risk of leaks.
The ability to join large metal sheets efficiently makes FSW particularly valuable in this field.
Electronics
The electronics industry uses FSW to join conductive materials, improving performance in heat-sensitive applications.
This method ensures high-quality joints with excellent thermal and electrical conductivity.
Benefits of Friction Stir Welding
FSW offers a host of benefits that make it an appealing choice for joining dissimilar metals and materials.
Enhanced Mechanical Properties
FSW produces joints with superior mechanical properties compared to those achieved using conventional welding.
The absence of melting ensures a uniform microstructure, providing greater strength and stability.
Cost-Effectiveness
By minimizing material waste, reducing the need for additional workpieces, and lowering energy consumption, FSW is a cost-effective method.
The streamlined process also reduces the need for post-weld treatments, further decreasing production costs.
Environmental Friendliness
FSW is environmentally friendly, as it reduces emissions and energy usage compared to traditional welding methods.
This further enhances its appeal in industries striving for sustainable manufacturing practices.
Challenges and Considerations
Despite its many advantages, FSW does come with challenges and considerations.
One of the primary challenges is the need for specialized equipment and expertise, which can increase initial setup costs.
Additionally, while FSW is highly effective for certain materials, it may not be suitable for every type of metal or application.
Thorough testing and material analysis are necessary to ensure proper implementation.
In summary, the joining of dissimilar metals and materials, particularly through Friction Stir Welding, offers substantial advantages across various industries.
The ability to combine different material properties into a single component can lead to innovations in product design and functionality.
With its myriad of benefits, FSW stands out as a cutting-edge solution, paving the way for advances in manufacturing technology.
資料ダウンロード
QCD管理受発注クラウド「newji」は、受発注部門で必要なQCD管理全てを備えた、現場特化型兼クラウド型の今世紀最高の受発注管理システムとなります。
ユーザー登録
受発注業務の効率化だけでなく、システムを導入することで、コスト削減や製品・資材のステータス可視化のほか、属人化していた受発注情報の共有化による内部不正防止や統制にも役立ちます。
NEWJI DX
製造業に特化したデジタルトランスフォーメーション(DX)の実現を目指す請負開発型のコンサルティングサービスです。AI、iPaaS、および先端の技術を駆使して、製造プロセスの効率化、業務効率化、チームワーク強化、コスト削減、品質向上を実現します。このサービスは、製造業の課題を深く理解し、それに対する最適なデジタルソリューションを提供することで、企業が持続的な成長とイノベーションを達成できるようサポートします。
製造業ニュース解説
製造業、主に購買・調達部門にお勤めの方々に向けた情報を配信しております。
新任の方やベテランの方、管理職を対象とした幅広いコンテンツをご用意しております。
お問い合わせ
コストダウンが利益に直結する術だと理解していても、なかなか前に進めることができない状況。そんな時は、newjiのコストダウン自動化機能で大きく利益貢献しよう!
(β版非公開)